The purpose of the Auto Coater Performance Qualification protocol is to verify that the equipment produces the desired output. Once the equipment is installed and Operational qualification is done, we shall plan to check its performance. The equipment’s working capacity is challenged by charging the equipment with the maximum and minimum capacity of the equipment.
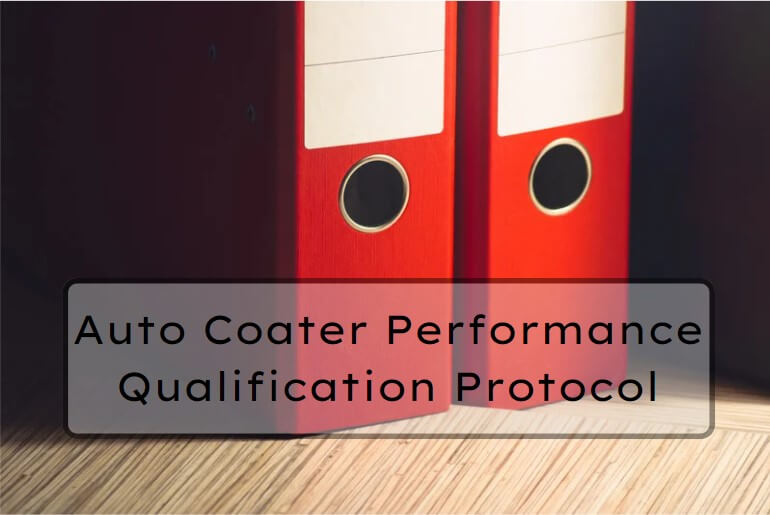
Read: Auto Coater Installation Qualification Protocol/ Annexures
Auto Coater Performance Qualification Protocol Contents:
SERIAL NO. | ITEM DESCRIPTION |
1.0 | PROTOCOLAPPROVAL |
2.0 | OVERVIEW: |
2.1 | Objective |
2.2 | Purpose |
2.3 | Scope |
2.4 | Responsibility |
2.5 | Execution Team |
3.0 | GENERAL CONSIDERATION/PREREQUISITE |
4.0 | REVALIDATION CRITERIA |
5.0 | PERFORMANCE QUALIFICATION PROCEDURE |
5.1 | Methodology |
6.0 | ACCEPTANCE CRITERIA |
7.0 | MATERIAL REQUIRED FOR COATING |
8.0 | PHYSICAL VERIFICATION OF COATED TABLETS |
9.0 | RESULTS |
10.0 | DEFICIENCY AND CORRECTIVE ACTIONS |
11.0 | Annexure (s) |
12.0 | PERFORMANCE QUALIFICATION FINAL REPORT |
12.1 | Summary |
12.2 | Conclusion |
12.3 | Final report approval |
1.0 | PROTOCOL APPROVAL: |
This performance qualification protocol of Auto Coater has been reviewed and approved by the following persons:
FUNCTION | NAME | DEPARTMENT | SIGNATURE | DATE |
PREPARED BY | QUALITY ASSURANCE | |||
REVIEWED BY | PRODUCTION | |||
REVIEWED BY | QUALITY CONTROL | |||
APPROVED BY | QUALITY ASSURANCE |
2.0 | OVERVIEW: |
2.1 | OBJECTIVE: |
The purpose of this protocol is to verify that the equipment produces the desired output. Once the equipment is installed and Operational qualification is done, we shall plan to check its performance. The equipment’s working capacity is challenged by charging the equipment with the maximum and minimum capacity of the equipment. | |
2.2 | PURPOSE: |
The purpose of this protocol is to verify that the equipment produces the desired output. Once the equipment is installed and Operational qualification is done, we shall plan to check its performance. The equipment’s working capacity is challenged by charging the equipment with the maximum and minimum capacity of the equipment. |
2.3 | SCOPE: |
The following shall be responsible; Quality assurance officer/Executive – For Preparation of Protocol /Execution Production Head – For execution support quality Control head – To analyze the Coated tablet quality Assurance Head – For adequacy and final approval | |
2.4 | RESPONSIBILITY: |
The following shall be responsible; Quality assurance officer/Executive – For Preparation of Protocol /Execution Production Head – For execution support quality Control head – To analyze the Coated tablet quality Assurance Head – For adequacy and final approval |
2.5 | EXECUTION TEAM: |
The execution team is responsible for the execution of the performance qualification of Auto Coater. The execution team comprises of: |
DEPARTMENT | DESIGNATION | NAME | SIGNATURE | DATE |
PRODUCTION | ||||
QUALITY CONTROL | ||||
QUALITY ASSURANCE |
3.0 | GENERAL CONSIDERATION/PREREQUISITE |
3.1 | Approved Standard operating procedure of the equipment shall be available |
3.2 | Approved analytical methods for testing the samples collected during the processing |
3.3 | The maximum and minimum capacity of the equipment shall be verified by taking the batch/lot to suit the requirement. |
3.4 | The installation and operational qualification of the equipment shall be completed before the execution of the performance qualification. |
3.5 | All the deficiencies and discrepancies related to the equipment that affect the product quality and corrective action taken shall be recorded in the appropriate section of the protocol. |
3.6 | The analytical test results and other reports related to the equipment shall be attached with the performance qualification of the equipment and finally verified. |
3.7 | After completion of PQ activities, equipment shall be cleaned as per respective cleaning SOPs and released for manufacturing. |
3.8 | The analytical test results and other reports related to the equipment shall be attached to the performance qualification of the equipment and finally verified. |
Read: Design Qualification Protocol for Vertical Laminar Reverse Flow
4.0 | REVALIDATION CRITERIA: |
The machine shall be revalidated if: | |
Whenever there are significant changes, they can impact how well the equipment works. If the batch or lot size goes beyond the usual range for testing performance, it can cause issues. As per the revalidation date and schedule. |
5.0 | PERFORMANCE QUALIFICATION PROCEDURE |
5.1 | METHODOLOGY: |
Pan Capacity Determination:
Compressed tablets should be charged into the coating pan, and start rotating the coating pan. None of the tablets should be coming out from the coating pan.
Verification of Coating Process:
- Visual Inspection
- Verify the weight gain of the Tablet after the coating process.
- Set up a system with the necessary tools and programs to work smoothly without any stops or problems.
Auto Coater Performance Qualification Protocol:- Purpose
The purpose of the coating system is to uniformly coat Tablets with a coating solution (as per PQ BMR) Critical process characteristics are monitored throughout the trials to ensure that coated products are produced to have uniform coating & appearance. Tablets do not loose their characteristics during the coating process.
Processing Steps: The coating process is divided into the following process steps:
Preparation of the coating solution:
The coating solution needed for one batch of coating is prepared in a vessel used for solution preparation. The Solution will be transferred into the SS tank manually and is moved and connected to the Coating System.
Coating Process:
The uncoated Tablets are charged in the Coater. The coating solution is sprayed to coat the Tablets. Inlet AHU and outlet blower are provided to supply conditioned air and exhaust the solvent rich air.
After completion of the coating process, the coated tablets are sent for packing in the Blister/ Strip Packing Machines.
Test Method – Set process parameters for the Coating System as determined in PQ BMR Parameters defined shall be appropriate to have airflow for uniform atomization
Charge uncoated Tablets & prepare coating solution as per PQ BMR recipe and set process parameters, which include a heating, spraying, and cooling phase sequence.
Start the Coating System with the specified recipe.
Check the coating of the product bed visually every 15 minutes through sight glass and record the airflow and differential pressure of the product across the pass.
On completion of the coating process discharge the coater into Plastic Containers with polyliners.
Record the test data and any observations throughout the process in the PQ BMR as well as the PQ report
Samples of tablets are taken and tested as follows:
20 tablets each from six sampling locations to identify potential areas of poor coating.
Samples are analyzed, according to applicable Standard Operating Procedures, for appearance and weight gain.
Test for Weight Variation and thickness.
One PQ batch must be tested as described before, in order to demonstrate consistent performance.
Read: Design Qualification of Electric Stacker
6.0 | ACCEPTANCE CRITERIA |
6.1 | Tablets shall have uniform appearance as seen visibly. |
62 | Weight Gain Three samples shall be weighed for each location. Samples should meet the following criteria. |
6.3 | All hardware and software components shall perform without problems and interruptions while processing the complete batch for capacities as agreed with the equipment supplier |
6.4 | Appearance, Weight Variation, and Thickness are to be limited as specified in PQ BMR. |
7.0 MATERIAL REQUIRED FOR COATING:
- Raw Materials (Tablets) in sufficient quantity
- Coating liquid in sufficient quantity
- Sample containers or sample bags.
- IPQC
8.0 PHYSICAL VERIFICATION OF COATED TABLETS:
S. No | Parameter | Specification | Actual Observation | Checked by Sign& Date |
1. | Appearance | |||
2. | The average Weight of 20 tablets | ——–mg ± 2% | ||
3. | Thickness | |||
4. | Pan load (60“) | 129 Kg / 215 Kg | ||
5. | Inlet Temperature | 50°C to 60°C | ||
6. | Exhaust Temperature | 40°C to 50°C | ||
7. | Pan RPM | 1-6 | ||
8. | Spray rate | 100 ± 20 gm/minute / gun | ||
9. | Bed temperature | 35°C to 45°C | ||
10. | No of spray guns | 3 | ||
11. | Diameter of the nozzle of a spray gun | 1.5 mm |
Time | Sapling location | Sample qty | Average Wt build-up % | Average weight in mg | Checked by Sign& Date | |||||||||||||||
10 | 20 tablets at each location | |||||||||||||||||||
Uniformity of weight-coated tablets (± 5% of Average Weight) | |||||||||
Location: 1 Time: | Location: 2 Time: | ||||||||
Tablet weight in mg | Tablet weight in mg | ||||||||
Location: 3 Time: | Location: 4 Time: | ||||||||
Tablet weight in mg | Tablet weight in mg | ||||||||
Location: 5 Time: | Location: 6 Time: | ||||||||
Tablet weight in mg | Tablet weight in mg | ||||||||
Location: 7 Time: | Location: 8 Time: | ||||||||
Tablet weight in mg | Tablet weight in mg | ||||||||
Location: 9 Time: | Location: 10 Time: | ||||||||
Tablet weight in mg | Tablet weight in mg | ||||||||
INFERENCE:
———————————————————————————————————————————
Checked by:
Date:
9.0 Results:
Tests | Acceptance criteria | Accepted(Yes/No) | Sign & Date |
Pan capacity Determination | According to the capacity as specified by the supplier | ||
Visual InspectionSample locations 6, 20 tablets at each location, Three time testing | Uniform in appearance | ||
Verify the weight gain of the Tablet after the coating process. Sample locations 6, 20 tablets at each location, Three-time testing | All individual results are within 10 percent (absolute) of the mean value of the results. | ||
Establish coater capacity with Hardware and software to perform without any interruptions and trouble. | Hardware and software to perform without any interruptions and trouble. | ||
Physical & chemical characteristics | Weight Variation, Thickness, Friability, Hardness, and Disintegration to be within limits specified in PQ BMR. |
INFERENCE:
———————————————————————————————————————————
——————————————————————————————————————————–
Checked by:
Date:
10.0 | DESCRIPTION AND CORRECTIVE ACTIONS |
The following deficiency was verified and corrective actions were taken in consultation with the validation team. |
Description of deficiency: |
Corrective action(s) taken: |
Reviewed By:
Date
11.0 Annexure (s):
Sr.No. | Annexure No. | Title of Annexure |
12.0 | PERFORMANCE QUALIFICATION FINAL REPORT: |
12.1 | SUMMARY: |
12.2 | CONCLUSION: |
13.3 Final Report Approval:
It has been verified that all tests required by this report are completed, reconciled, and attached to the Auto Coater Performance Qualification Protocol or included in the qualification summary report. Verified that all amendments and discrepancies are documented, approved, and attached to this protocol.
The signature in the block below indicates that all items in this qualification report of Auto Coater have been reviewed and found to be acceptable and that all variations or discrepancies have been satisfactorily resolved. The equipment can be taken for production trial.
NAME | DESIGNATION | DEPARTMENT | SIGNATURE | DATE |
PRODUCTION | ||||
QUALITY CONTROL | ||||
QUALITY ASSURANCE |