1.0 Aim: Procedure for Analysis and Release of Packaging Materials
2.0 Purpose: This standard operating procedure outlines the procedure for analyzing and releasing packaging materials at [company name].
3.0 Scope: This procedure applies to the quality control laboratory and covers the analysis and release of packaging materials.
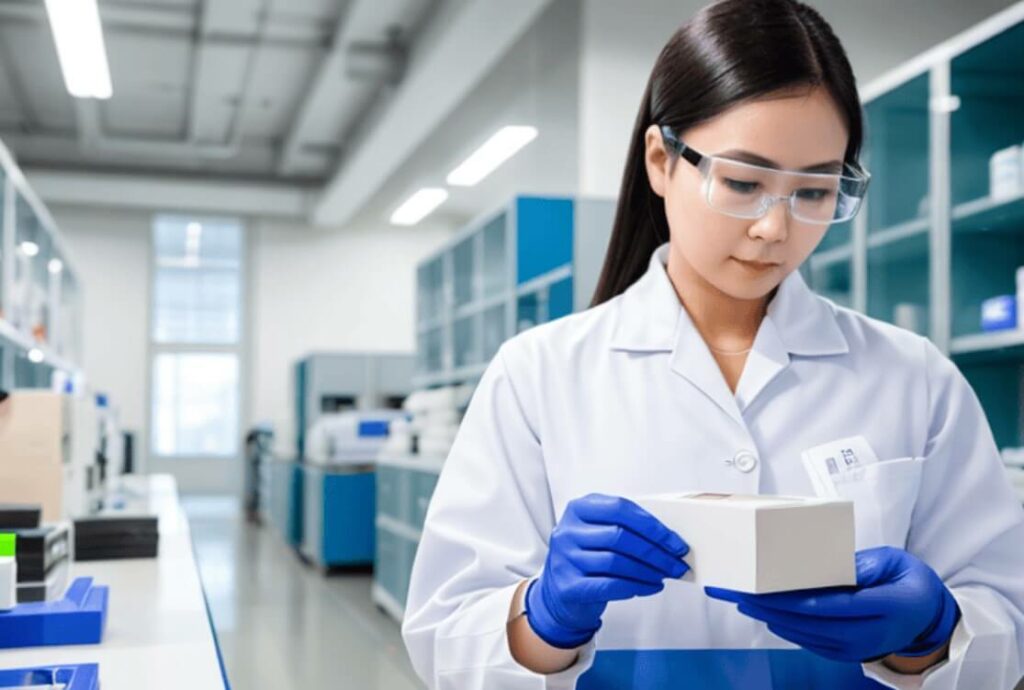
4.0 Responsibility:
QC Analyst: Responsible for analyzing packaging materials.
QC Supervisor: Allocates packaging material samples and submits them to the analyst for analysis.
QA Reviewer: Reviews the data.
QC Head: Approves raw materials and ensures compliance with this SOP.
5.0 Procedure for Analysis and Release of Packing Materials:
- All incoming packing materials must be examined according to the applicable standard.
- If reproducing an under-test or approved label or Certificate of Analysis is necessary, a re-print request must be submitted and approved by the Quality Assurance department.
- The QC Analyst will analyze the materials and record the data in the LIMS. After the analysis, the QC analyst must print the Approved/Rejected label from the LIMS.
- For packaging materials supplied in roll form (labels, foils, films), physical tests like breadth and grammage must be performed.
- Pack received Width and grammage as follows:
- Up to 3- All Rolls
- 4 to 8- 3 Rolls
- More than 8- 5 Rolls
- All received samples must undergo a description test.
- An identification test shall be performed on any one of the samples.
- For materials other than those received in roll form, dimension, grammage, and weight tests must be performed on 5 samples or as specified in the corresponding method of analysis.
- The production packing officer will assign the samples to the Q.C. analyst in LIMS for analysis. Any leftover samples must be stored in the Sample Storage Cabinet.
- The QC analyst will verify the sample allocation in the LIMS.
- Once the sample is received, the QC analyst must conduct the analysis following the specifications and method of analysis.
- After completing the analysis and recording the results in the LIMS, the reviewer must evaluate the test data in the LIMS and the corresponding instruments and conduct an audit trail review.
- Following the review, the Head QC will approve or reject the packaging material.
- The Certificate of Analysis (CoA) shall include details such as Material Name, Material Code, Inspection Lot No., Specification Id., Specification Rev. No., Quantity Received, A.R. No., Manufacturer, Batch No., Received Date, Manufactured By, Date of Release, Retest Date, and results as per the specified tests.
- The QC analyst shall print the Approved or Rejected label from LIMS based on the number of containers. For materials that come in bulk, labeling can be rationalized based on risk scenarios.
- The Approved label shall contain Material Name, Material Code, A.R. No., Manufacturer, Mfr. Batch No., Mfg. Date, Exp. Date, Quantity, Retest Due On, Sign, Date, and number of packs.
- The Rejected label shall contain Material Name, Material Code, A.R. No., Manufacturer, Mfr. Batch No., Mfg. Date, Exp. Date, Quantity, Reason for rejection, Sign, Date, and number of Packages.
- In the case of Rolls for example; (Aluminum Foils roll, Blister Films roll, Roll Labels), Approved or Rejected labels should be affixed on the roll (inner side of the core).
- In case of material rejection due to a quality concern, a Rejection Report must be filled, and the rejection must be verified by QA. Once the material is rejected, the warehouse head must be informed to locate the material in the rejected area.
- the QC supervisor shall discard the remaining samples after completing the analysis and review activity, as per the given sample destruction SOP.
5.1 Sample preparation for Autoclave and TOC test:
- Microbiologists will prepare the samples.
- Purified water or Millipore water should be used for sample preparation. Ensure the beaker used to catch the water is clean and dry.
- Use freshly obtained filtered water for sample processing.
- When filling the sampling bottle, make sure to fill it completely up to the neck. Let it overflow a little to get rid of any trapped air inside.
- Use aluminum foil rinsed with pure water for bottle wrapping.
- Check the autoclave sample for leakage and unwrap the aluminum foil.
- After autoclaving, evaluate the produced sample for TOC and other specified tests.
5.2 Handling and using printed packaging material Shade Cards and Standard Specimens:
- Shade cards and standard specimen samples shall be designed and approved by the Artwork department.
- The validity period for shade cards and standard specimens is defined as 2 years from the date of preparation or in case of artwork revision. The validity shall be mentioned on the shade card.
- QA Department shall have two copies of approved shade cards and standard specimens from the Artwork department.
- On receipt of shade cards and standard specimens, the QA department shall verify the samples before they are used by QC for analysis. Inward and outward artwork records shall be maintained by the Quality Assurance department.
- They will make sure to have a record of it. Also, the QC department will receive a copy of the shade card and a standard specimen sample for reference. They will keep a record of this information in the appropriate format.
- For printed packaging material, tests for color and printing of the text matters shall be performed based on the approved shade card and standard specimens within their validity period.
- If there is a change in artwork, change in packing material, expiry of the validity period, discontinuation of packing material, or any other reason, shade cards and standard specimens shall be considered obsolete by the QA department. QA shall maintain the obsolete copy for future reference.
- QA shall destroy retrieved QC copies of shade cards and standard specimen samples by shredding, as per the respective SOP for destruction.
- For standard shade cards and standard specimen samples nearing their validity period, they shall be identified and intimated to the artwork department to receive new shade cards and standard specimens.
- New shade cards and standard specimen samples shall be made available by the artwork department before delivery of new consignments.
6.0 The Acceptable Quality Level (AQL) Inspection for Packing Materials:
- The Acceptable Quality Level (AQL) inspection is a statistical method used for checking the quality of packaging materials. The sample size for this inspection will be determined based on the “Sampling Plan of Acceptance Quality Level for Packaging Materials” as Annex below.
- During the AQL inspection, samples will be collected from a certain number of boxes or containers, depending on the sample size and the total number of boxes. For example, if there are 125 samples to be collected from 6 containers, 21 samples will be taken from each of the first 5 containers and 20 samples from the last 6th container.
- The collected samples will be examined by the QC personnel according to the “Acceptance Quality Level (Packaging Material)” guidelines in Annex as below.
- Defects found during the AQL inspection will be classified into three categories: Critical Defects, Major Defects, and Minor Defects.
- The observations from the AQL inspection will be reported using the “Acceptance Quality Level Observation” format in Annex No. 03.
- If the number of defects found in the sample is equal to or less than the acceptance number, the entire lot or consignment will be considered acceptable.
- If the number of defects is equal to or greater than the rejection number, this will be communicated to the QC Head. In such cases where the lot fails to meet the acceptance quality level criteria, a deviation report will be initiated, and the lot will be re-inspected. For instance, if the lot size is 1300 and the designated sample size is 125 units if 6 minor defects are found and the acceptance number is 5, the lot will be rejected.
- In case of re-inspection, the same sampling plan will be used, and if the number of defects is equal to or greater than the rejection number, the final decision on the batch will be based on deviation closure.
- Observations from the AQL re-inspection will be recorded in the “Acceptance Quality Level Observation” format in Annex No. 01, with remarks manually noted in the bottom left corner.
- After completing the AQL Inspection observation, samples will be collected for testing from the same samples used during the AQL Inspection, following the “Sample Quantity for Packaging Material Testing” table.
6.1 Packaging Materials and Sample Quantity for Packaging Material testing as follow:
Aluminum Foil- 10 meters
Poly-laminated paper- 10 meters
PVC and PVdC coated PVC film- 5 meters
Carton (Inner / Outer)- 15 Nos.
Leaflet- 15 Nos.
Catch cover- 15 Nos.
Shrink Bag- 10 Nos.
HDPE container- 05 Nos.
Glass bottle- 05 Nos.
Corrugated box- 01 No.
BOPP Tape- 01 No.
Strapping roll- 05 meters
Silica gel bag- 05 Nos.
Annex. Sampling AQL plan for Packing materials:
Lot or Batch Size | Sample Size | Minor – AC | Minor – RE | Major – AC | Major – RE | Critical – AC | Critical – RE |
2 to 8 | 2 | 0 | 1 | 0 | 1 | 0 | 1 |
8 to 15 | 3 | 0 | 1 | 0 | 1 | 0 | 1 |
16 to 25 | 5 | 0 | 1 | 0 | 1 | 0 | 1 |
26 to 50 | 8 | 0 | 1 | 0 | 1 | 0 | 1 |
51 to 90 | 13 | 0 | 1 | 0 | 1 | 0 | 1 |
91 to 150 | 20 | 0 | 1 | 0 | 1 | 0 | 1 |
151 to 280 | 32 | 1 | 2 | 0 | 1 | 0 | 1 |
281 to 500 | 50 | 2 | 3 | 1 | 2 | 0 | 1 |
501 to 1200 | 80 | 3 | 4 | 1 | 2 | 0 | 1 |
1201 to 3200 | 125 | 5 | 6 | 2 | 3 | 0 | 1 |
3201 to 10000 | 200 | 8 | 9 | 3 | 4 | 0 | 1 |
10001 to 35000 | 315 | 12 | 13 | 6 | 7 | 0 | 1 |
35001 to 150000 | 500 | 20 | 21 | 8 | 9 | 0 | 1 |
150001 to 500000 | 800 | 32 | 33 | 16 | 17 | 0 | 1 |
500001 and over | 1250 | 50 | 51 | 25 | 26 | 0 | 1 |
Note: AC stands for “Acceptance Number,” and RE stands for “Rejection Number.” These values determine whether a lot or batch is acceptable or should be rejected based on the number of defects found in the sample.
Related: Quality Control Test for Secondary Packing Materials
7.0 Formats:
7.1 Specimen for Approved Label
- Material Name
- Material Code
- A.R. No.,
- Manufacturer
- Mfr. Batch No.
- Mfg. Date
- Exp. Date
- Quantity
- Retest Due On
- Sign, Date
- Number of packs
7.2 Specimen for Rejected Label.
- Material Name
- Material Code
- A.R. No.
- Manufacturer
- Mfr. Batch No.
- Mfg. Date
- Exp. Date
- Quantity
- Reason for rejection
- Sign
- Date
- Number of packs
7.3 Handling of Shade Cards and Standard Specimen Samples.
- Sr.No.
- Date of Receipt
- Material Code
- Material Name
- Manufacturer Name
- No. of Copies Received By QA (Sign/Date)
- Valid Upto