The Bag filter works to enhance the air quality and prevent the loss of powder in pharmaceutical production. In pharmaceutical manufacturing, the processing of highly potent drugs like hormones, vitamins, antibiotics, etc., generates lots of powder, which can lead to hazards. Various processes, including screening, blending, mixing, drying, granulating, tableting, compression, and packaging, contribute to air pollution and chemical risks.
Removing these types of problems and maintaining clean air is highly required which is achieved by using filter bags. Antistatics(statin), nylon polymer, and cotton polymer filter bag act as dust collection mechanism that filters and captures powder within the process Air. When the filter cloth takes suspended on the machine it takes a cylindrical bag shape, This area is commonly known as the filter house.
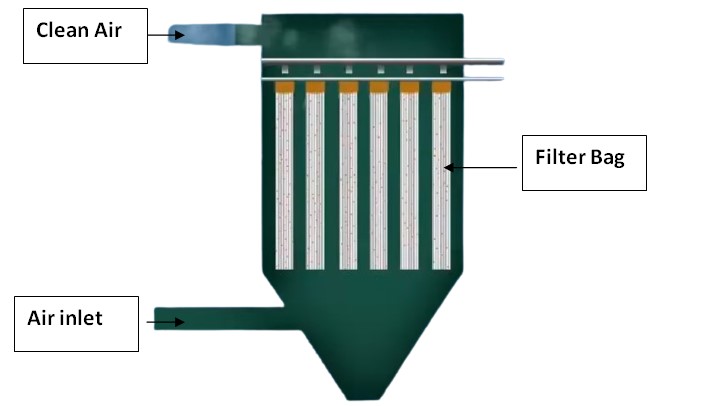
Principle of Bag Filter
The collection of poder by filter bags depends on the principle of filtration. The powder layer adheres to and deposits on the filter bag’s surface and the inner side of the filter cloth, to capture powder particles from the air. The fabric provides a surface for dust particles to accumulate. Accumulation or collection occurs through mechanisms such as inertial or electrostatic interaction, interception, and Brownian movement. These processes lead to the formation of a powder cake on the fabric surface.
Construction of Bag Filter
This equipment comprises a large metal vessel (bag house) divided into compartments, as shown in the above figure. The FBD bags are finger like structures made of Antistatics(statin), nylon polymer, and cotton polymer which helps withstand operating temperatures and pressures. These filter bags are attached to a round ring made of metals that help filter bags remain fixed.
The bags are suspended upside down within the vessel. Bag length ranges from 2 to 10 meters (Depending on the FBD size), with diameters up to 40 centimeters (Depending on the manufacturer’s requirements). The number of bags in a vessel can vary from 10 to 20 or more, depending on the size of the bag house. A hopper is provided at the bottom to collect the dust retained by the filter.
Working on filter Bag
The process gas enters through an inlet pipe, colliding with a baffle plate. Due to the impact, large particles slide down to the bottom hopper under the influence of gravity. The carrier gas then travels upwards and passes through the bags, leaving fine particulates to adhere to the inner surface.
Air moving through a filter cloth maintains a filtration velocity of 0.3-2 meters per minute and experiences a pressure loss of 1-2 kilopascals. As the particle layer on the filter cloth thickens, the pressure loss increases and the accumulated fine particle is removed by shacking periods. In most cases, fabric filter bags exhibit a dust collection efficiency of 99 percent or higher, resulting in a dust concentration at the outlet of less than 10 milligrams per cubic meter. To enhance efficiency, filter bags are periodically cleaned, maintained, and replaced.
Troubleshooting for Filter Bag
- Sometimes FBD filters may be choked during the process, so vagarious shaking is required from time to time.
- Filter bags may be damaged during the drying process so to prevent this SFM test is highly required.
Merits
- Filter bags offer the most effective method for removing fine particles from the air.
- They are very effective to retained Powder while the drying process in FBD.
- They consume low amounts of electricity.
- They contribute to maintaining and protecting a healthy environment.
- Their construction and operation are relatively simple.
- They possess versatility and an effective design.
- They aid in reducing housekeeping efforts and improving product quality.
- Filter bags adhere to the effective design standards of the American Ventilation System.
- High-quality filter bags ensure trouble-free operation.
Demerits
- Bag filters have limitations in operation due to high gas temperatures and high humidity.
- The maintenance cost can be high as the fabric used is expensive.
- The characteristics of the fabric can change under different operating parameters.
- Bag filters tend to be relatively large in size.
- Efficiency can be reduced by the condensation of vapors and the presence of hygroscopic materials.
Applications of bag filter
- They are commonly utilized in fluidized bed dryers to prevent powder loss.
- Bag filters are widely employed in industries to separate dust particles from the air.
- They are extensively used to clean the air in working areas.
- Bag filters find significant application in large industries that produce various types of powder/dust, including metals, cement, chalk and lime, ceramics, flour, and foundries.
Conclusion:
In summary, a bag filter is an important tool used in pharmaceutical production and other filed to ensure air quality and protect from the hazards of dust generated during various processes. By employing filter bags, can effectively collect and filters the dust present in the process gas.
FAQs (Frequently Asked Questions):
A bag filter is used to prevent powder loss from the FBD. Because in pharmaceuticals it is highly recommended to maintain the batch yield throughout the process.
The collection of poder by filter bags depends on the principle of filtration. The powder layer adheres to and deposits on the filter bag’s surface and the inner side of the filter cloth, to capture powder particles from the air. The fabric provides a surface for dust particles to accumulate. Accumulation or collection occurs through mechanisms such as inertial or electrostatic interaction, interception, and Brownian movement. These processes lead to the formation of a powder cake on the fabric surface.
Some advantages of bag filters include low electricity consumption, simplicity in construction and operation, effective powder collection efficiency, reduction in housekeeping efforts, and improvement in product quality.
Bag filters have limitations when it comes to operating under high Air, temperatures, and high humidity conditions. Additionally, the maintenance cost can be high due to the cost of the filter fabric. The characteristics of the fabric can also change under different operating parameters.
Bag filters are commonly used in industries that retain powder, such as pharmaceuticals, metals, cement, ceramics, flour, and foundries. They are also extensively utilized in fluidized bed dryers.