Learn the details contents and description of the Design Qualification Of FBD in Pharmaceuticals.
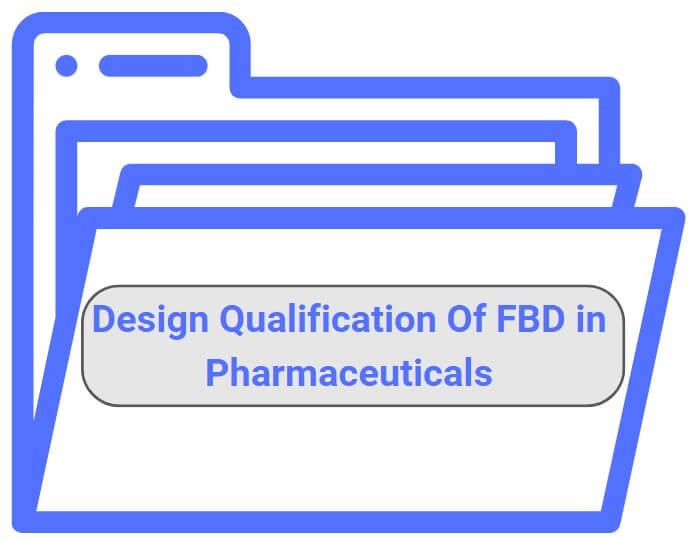
CUSTOMER: XYX Pharmaceutical Company.
LOCATION: XYZ
P.O. NO.:
DATE:
EQUIPMENT: FLUID BED DRYER
MODEL: FBD GM 250 HW
J.O. NO.:
SERIAL NO.:
CONTENTS | ||||
S. NO. | HEADING | REMARK | ||
1.0 | OBJECTIVE & SCOPE | |||
2.0 | ACCEPTANCE CRITERIA | |||
3.0 | RESPONSIBILITIES | |||
4.0 | SYSTEM DESCRIPTION | |||
5.0 | DESIGN BASE & ASSUMPTIONS | |||
6.0 | VARIATIONS | |||
7.0 | TECHNICAL SPECIFICATI0NS | |||
7.1 | PROCESS & PRODUCT REQUIREMENTS | |||
7.2 | EQUIPMENT SUB-ASSEMBLIES & PARTS | |||
7.3 | cGMP PRACTICES | |||
7.4 | SAFETY FEATURES | |||
7.5 | LIST OF ITEMS TO BE SUPPLIED BY CLIENT | |||
8.0 | MATERIAL OF CONSTRUCTION | |||
9.0 | DOCUMENTATION | |||
9.1 | DRAWINGS | |||
9.2 | DOCUMENTS | |||
10.0 | SUPPORTING UTILITIES |
11.0 | SPARE PARTS | ||
11.1 | SPARE PARTS | ||
11.2 | LUBRICATION CHART | ||
11.3 | FILTERS | ||
12.0 | LIMITATION FOR PERFORMANCE OF EQUIPMENT | ||
13.0 | VARIATIONS | ||
14.0 | PRE- QUALIFICATION CHECKLIST | ||
14.1 | FACTORY ACCEPTANCE TEST (FAT) | ||
14.2 | SPECIFIC CHECKPOINTS | ||
14.3 | SITE ACCEPTANCE TESTS (SAT) | ||
15.0 | FINAL REPORT | ||
15.1 | SUMMARY | ||
15.2 | CONCLUSION | ||
16.0 | DESIGN QUALIFICATION APPROVAL | ||
17.0 | APPENDIX | ||
17.1 | ABBREVIATIONS |
1.0 OBJECTIVE & SCOPE:
The purpose of this document is to provide Design Qualifications for Fluid Bed Dryer GM 250 HW. This document provides evidence that the machine is designed, manufactured, supplied, installed & commissioned as per the requirement of the user. This also confirms that this meets all the requirements of product, process, safety, regulatory bodies, and GMP obligations. This design qualification will provide information as a basic document for the validation.
Related: Installation Qualification Protocol for Automatic four head Vial Sealing Machine
PROTOCOL COMPLIED BY | PROTOCOL APPROVED BY | PROTOCOL AUTHORISED BY | |
PRODUCTION | Q.C. : | PLANT INCHARGE | |
QUALITY CONTROL | |||
ENGINEERING | |||
SAFETY | |||
MANUFACTURER | |||
DATE | DATE : | DATE : |
2.0 ACCEPTANCE CRITERIA:
01. The equipment shall conform to the specifications and requirements as specified in this design qualification
02. The physical verification of the subassemblies and parts shall be carried out in the manufacturer’s premises as per specifications and requirements.
03. The performance test shall be demonstrated after installation at the site i.e. at the user’s Premises.
3.0 RESPONSIBILITIES:
CLIENT ‘S
01) For providing complete technical specifications for design along with Purchase Order.
02) To qualify equipment along with the manufacturer.
MANUFACTURER ‘ S
01) To manufacture and supply the equipment incorporating all the specifications as per purchase order and requirement.
02) To assist the client with successful installation & commissioning at the site.
4.0 SYSTEM DESCRIPTION:
4.01 FLUID BED DRYER:
The Principle of a Fluid Bed Dryer is to create fluidal turbulence in a granulated or Powdery wet product by means of hot air ( or dehumidified air ) flowing in an upward Direction & to dry the same to the final required degree in a careful manner.
SUITABILITY:
In a Fluid Bed Dryer, the wet material is transposed to a fluidized state by a hot air stream that surrounds the material completely & therefore the heat transfer rate achieved is very high & the temperature distribution throughout the product is uniform. Due to this, drying time is considerably reduced & thus high production rates are achieved in comparison to other dryers. As the product is in close contact with hot Air at low temperatures & also for a short duration, the physical & chemical properties of the product are generally not affected & therefore the dryer can effectively be used for heat-sensitive products. Due to the movement of the product during drying, lump formation, case hardening, etc., are minimized. The Fluid Bed Dryers are not suitable for drying of liquids or pasty material.
For further Details Refer to Chapter “INTRODUCTION & GENERAL DESCRIPTION” given in operating manuals.
Fluid Bed Dryer is upgradable to top spray Fluid Bed Processor by modification in main body and provision of accessories viz.
a) Spray Nozzle
b) Peristaltic Pump
c) Silicon Tubes
d) Liquid storage tank
e) Software changes in PLC
4.02 LOADING & UNLOADING OF MATERIAL:
The material should be transferred to the product bowl either manually or mechanically. Material unloading can be done by tilting the bowl and by manual operation. The Unloading may be done by means of Pn. Conveying system or mechanical tippers.
5.0 DESIGN BASE & ASSUMPTIONS:
The Fluid Bed Dryer and its subassemblies design will be based on technical requirements, cGMP requirements, performance requirements & control logic mentioned by the client in their purchase order.
The manufacturer on the basis of the technical know-how will work out the complete specification of all the components required for the Fluid Bed Dryer.
6.0 VARIATIONS:
If there are any variations sought by the client after approval of Drawings, Documents, & Design qualifications, in the equipment from the original design then they shall be incorporated by the manufacturer in the equipment drawings after receiving written consent from the client.
This will form the basis for preparing the “As Built” drawings.
7.0 TECHNICAL SPECIFICATION
7.1 | PROCESS AND PRODUCT REQUIREMENTS | |||
S. No. | Description | Details | Acceptance Criteria | Remark |
01. | EQUIPMENT NAME | Fluid Bed Dryer | ||
02. | EQUIPMENT TYPE | Two Pc. Welded Const., & | ||
Pillar supported body | ||||
03. | WORKING CAPACITY | 250 KG Wet Product | ||
04. | PRODUCT CONTAINER VOLUME | 840 LTRS. | ||
05. | Material Of Construction & Thickness | |||
Contact Parts | S.S. 316 L – 4 mm, 3 mm | |||
Non Contact parts up to Blower | S.S. 316 L/ S.S. 304 | |||
assembly | 5 / 4/ 2 mm | |||
Non Contact parts others | S.S. 316 L/M.S. – 4 mm, 3 mm etc. | |||
Impeller | Aluminium – 5 mm, 3 mm | |||
06. | LOCATIONS OF ASSEMBLIES | |||
Main Body | Production Area | |||
Air Preparation Unit | Technical Area | |||
Blower Assembly | Technical Area | |||
Control Panel | Production Area, Near Equip. | |||
Power Panel | Technical Area | |||
Exhaust Filter unit | Technical area | |||
07. | AIR FILTRATION | |||
No of Stages | Four Stage | |||
Pre-filter 1st Stage | 20 Micron, < 90% Efficiency | |||
Fine filter 2nd Stage | 5 Micron, 95% Efficiency | |||
Hepa Filter 3rd Stage | 0.3 Micron, 99.97% Efficiency | |||
Exhaust Filter 4th Stage | 5 Micron, 95% Efficiency |
08. | AIR HEATING | Acceptance Criteria | Remark | |
Working temperature | 95°C ± 5°C | |||
Heater type | S.S. 304 Finned tube Heat Exchanger to suit Hot water. | |||
Heater Capacity | ≃ 1,35,000 Kcal / Hr. | |||
Heating Media | Hot water at 3.5 kg/cm² Pressure gauge & 125 ºC inlet temperature. | |||
Hot water Control Valve | 50 NB, Pn. Operated, 3 way on/off Valve | |||
Hot water inlet connections | 50 mm NB ASA 150 # Flanged | |||
Hot water outlet connection | 50 mm NB ASA 150 # Flanged | |||
09. | SEALING GASKETS | |||
For P. C. & Bottom body | Inflatable Tube, Food grade quality (FGN) | |||
For retarding chamber & PC | Inflatable Tube, Food grade quality (FGN) | |||
For Filter bag | Inflatable Tube, Food grade quality (FGN) | |||
For Ducting | Flat Gaskets, Food grade quality (FGN) | |||
10. | FILTER BAGS | |||
Type | Multiple Fingers Hooked up with S.S. Hanger | |||
Moc | P.C. Satin Cloth | |||
Air Permeability | 2.6 m³ /m²/ min at 10 mm WC | |||
Op. Temperature | 100 º C | |||
Particle Retention Capacity | 15 to 20 Microns | |||
11. | FILTER BAG SHAKING | |||
Type | Pn. Cylinder without wire rope | |||
Operation | Pneumatic, PLC Controlled | |||
Size | Tel. 125 Ø x 700 Stroke x 3 Stage |
12. | BLOWER ASSEMBLY | Acceptance Criteria | Remark | |
Capacity | 7000 m³/Hr, 800 to 850 ±10% mm static Pr. | |||
Motor | 30 HP, FLP-H, Foot Mounted, 415 VAC, | |||
3 ph, 50 c/s, 2935 rpm | ||||
Impeller | Backward-curved, Centrifugal type | |||
Impeller made out of Aluminium | ||||
Casing | M.S. Base Mounted, Vertical Exhaust | |||
13. | EXHAUST FILTER UNIT | |||
Type | Self Supporting | |||
MOC | M.S. | |||
Numbers Of Filters | Four (Aluminium Box Type) | |||
Size Of Filters | 24″ x 24″ x 12″ | |||
Capacity | 5 Micron 95% Efficiency | |||
14. | AIR INLET SHUT OFF VALVE | |||
MOC | S.S. 316 L + Silicon Gasket | |||
Size | 450 Ø OD x 400 Ø ID x 35 Thk. | |||
Operation | Pneumatic Actuator PD 150, On/Off Type | |||
15. | BLOWER INLET SHUT OFF | |||
VALVE | ||||
MOC | S.S. 316 L + Silicon Gasket | |||
Size | 450 Ø OD x 400 Ø ID x 35 Thk. | |||
Operation | Pneumatic Actuator PD 150 +M10 | |||
PID type |
16. | CONTROL SYSTEM | Acceptance Criteria | Remark | |
Control Panel | S.S. 304, Top Pendent Machine mounted, | |||
For MMI | ||||
Operating Voltage | 24 VAC. | |||
Pn. Control Panel | M.S. Foot Mounted Single Cabinet | |||
Power Panel | M.S. Foot Mounted Single Cabinet | |||
Earth Fault Relay | 230 Vac., Alliance make | |||
Variable frequency drive | Mitsubishi, To suit motor | |||
Programmable Logic Controller | Mitsubishi, FX2N, 32 MRES (By Client) | |||
Analog Module | FX2N, 8AD, 4DA (By Client) | |||
MMI | E 615 (By Client) | |||
Pneumatic Instruments & Valves | Festo | |||
Pneumatic Actuators | EL-O-Matic, Double Acting Rotary Act. | |||
Temperature Sensors | PT 100, Flameproof with Built-in | |||
Temp. Transmitters. | ||||
Hot & Cold air damper control Actuator | El-O-Matic PD 60+M10, PID Type | |||
Bottom Drain Valve | S.S. 316 L, 40 NB, Pn. Op. On/Off Type | |||
Solid Flow Monitor | SFM 10 + 20 mtr. cable & 300 mm long | |||
(Provision on BI Duct & panel) | sensor | |||
17. | SURFACE FINISH | |||
Contact Parts | Smooth & Mirror Finish, ≃ 320 ± Grit | |||
Non-Contact Parts | Smooth & Mat Finish, ≃ 180 ± Grit | |||
C.S. Parts | Siemens Gray Epoxy Painted | |||
C.S. Power Panel | Siemens Gray Powder Coated |
7.2 EQUIPMENT SUBASSEMBLIES & PARTS:
7.2.1 MAIN BODY
M.O.C. – S.S. 316 L Thickness – 4 & 5 mm
It is a Cylindrical Retarding Chamber & Filter Bag Housing, Side Explosion Chamber, etc. supported by side pillars, and rear chamber, and a cylindrical bottom body resting on floor level.
The Accessories of the Main Body are:
01. PC sealing arrangement (IT)
02. PC Bottom & Top Sealing Gaskets.
03. Safety Device for PC.
04. L / S Glass Windows
05. Earthing Device
06. Air Inlet Nozzle
07. Blower Inlet Nozzle
08. Explosion Frame & Flap
09. Lifting Eyebolts & Lugs
10. Spray Window & Cover
11. Pn. Shaking Cylinder
12. Pn. Component for PC Sealing
13. Pn. component for bag sealing & shaking
14. Bottom Dish, Leg supports.
15. Bottom Drain Triclover union with blind cover
16. Charging Nozzle
17. CIP Nozzle & Manifold
7.2.2 AIR INLET SHUT-OFF VALVE:
M.O.C. – S.S. 316 L Thickness – 35 mm
It is an isolating valve between the main body and the air preparation unit. The type of valve is On/Off. The flap is operated through a double-acting pneumatic actuator. This remains closed when the equipment is not in use or during bag shaking.
7.2.3 BLOWER INLET SHUT-OFF VALVE:
M.O.C. – S.S. 316 L Thickness – 35 mm
This valve is provided between the blower suction nozzle & main body. The type of valve is PID. The flap is operated through a double-acting pneumatic actuator and this valve also remains closed when the equipment is not in use or during bag shaking.
7.2.4 AIR PREPARATION UNIT :
M.O.C. – S.S. 304 + S.S. 316 L Thickness – 3 mm
It is a Rectangular Housing to accommodate Air Filters (20 Mic.+5 Mic +0.3 Hepa) and air heater. The one end is provided with a filter mounting frame while the other with a transition duct for changing rectangular sections to circular ducts.
The Accessories Fitted are:
01. Steam Inlet & Outlet Nozzle
02. Air Guide Cone
03. S.S. Air Heater
04. Δ P Connection Ports
05. Access Door
06. Hot & Cold Air Damper.
07. Air Filter 20 Micron
08. Air Filter 5 Micron
09. Hepa Filters 0.3 Micron
10. Hepa test window with cover
11. Hepa Filter fixing Frames
12. Exhaust Filter 5 Micron
13. Temperature Sensor Socket
14. Lifting Lugs
7.2.5 PRODUCT CONTAINER & TROLLEY:
A. PRODUCT CONTAINER
M.O.C. – S.S. 316 L Thickness – 4 mm
This is a conical-shaped container having the formed end at the top and a welded flange at the bottom. The wet product is loaded in the container, as per its working capacity i.e. 250 kg.
Accessories fitted are:–
01. Bottom perforated plate
02. Dutch Weave Mesh
03. L/S Glass window
04. Quick change Clamps
05. Sampling Device
06. Support bars
07. Temperature Sensor Socket
B. TROLLEY
M.O.C. – S.S. 304 Size – 40 NB Pipe
This is a tubular structure to support the product container, provided with S.S. 304 swivel castors and PU Wheels. There are four nos guide wheel brackets provided for easy locating with the main body. The product container can be transported from one place to another easily with the help of a trolley.
7.2.6 EXPLOSION FRAME & FLAP : (Flush Type)
M.O.C – S.S. 316 L Thickness – 3 & 4 mm
The S.S. 304 explosion frame is fitted with a 3 mm thick S.S. 316 L flush-type flap supported by a glazing rubber gasket on the body as a safety device. It suddenly releases the excess pressure developed inside, due to the explosion, and prevents the equipment & building from damage. It also provides Safety for personnel working around the equipment.
It is recommended that there should not be any obstruction in the vicinity of the explosion flap up to a reasonable distance of about 3 meters or more. The suitable extension ducts may be provided to suit site requirements. Additional extension ducts are provided for the explosion chamber to make it open to the atmosphere.
7.2.8 FILTER BAG SHAKING DEVICE:
M.O.C. – S.S. 304 / ALUMINIUM
This is an automatic type bag shaking arrangement. Where the bag Hanger & bag are Shaken through to double acting pneumatic cylinder shaft, The shaking frequency, and interval are variable parameters, which can be set through a Timer. The bag shaking is required to remove the adhered product particles on the bag contact surface to improve its permeability and avoid choking of the bags.
The accessories provided are :
01. Filter bag sealing gasket
02. FBT housing ring
03. Multiple-finger filter bag
04. Filter bag hooks
05. Filter bag hanger
06. Quick change coupling
07. Pn. Cylinder for shaking & lowering
7.2.9 DUCTING:
M.O.C. – S.S. 316 L/304 & M.S. Thickness – 2/ 2.5 / 3 mm
The ducting is provided between the air preparation unit, main body, product container, blower inlet, etc. made out of S.S. 316 L/304, This ducting conveys the air through filter bags to the blower suction. Then the air is exhausted through the blower outlet ducting made out of M.S. The size & length of ducting are designed to suit the site requirements. The duct flanges are provided with an FGN rubber gasket and C.S. /S.S. bolt & nuts.
7.2.10 BLOWER ASSEMBLY:
A) M.O.C. – M.S. Thickness – 4 / 5 mm
The blower is provided in the system to create an induced draft to pass the heated and conditioned air through the wet product and create the fluidization state of a material, which produces a uniformly dry product in a reasonably less time period.
The accessories of this assembly are:
01. Dynamically balanced backward curved Aluminium Impeller
02. Blower Casing
03. Supporting Structure
04. Anti-vibration pads
05. Blower suction nozzle
06. Air guide cone
07. Manually operated flow control damper
08. Blower Inlet Shut Off Valve PID type.
09. Blower outlet extension duct
10. Electric motor directly coupled with impeller
11. Silencer
The direction of rotation of the impeller is very critical & must be checked at the time of installation & trial run. Airflow is controlled through pn. operated blower inlet shut-off valve. This valve is located in the blower inlet duct and as near to the main body as possible. The valve remains closed during auto_pn. shaking and at the end of the process.
B) SILENCER:
M.O.C. – M.S. Thickness – 1.6 & 3 mm
The silencer is provided after the blower outlet damper & duct in order to reduce the sound level up to 5 – 10 dB.
The accessories/parts of silencer are:
01) Perforated shell
02) Jacket Shell
03) Sound absorbing material
04) End flanges
C) EXHAUST FILTER HOUSING:
M.O.C. – M.S. Thickness – 3 mm
The exhaust filter housing will be installed after the blower. This is provided with 5-micron air filters to arrest the fine particles escaping to the atmosphere and caters to the requirement of pollution control to some extent.
Related: Operational Qualification of Automatic High-Speed Linear Vial Washing Machine (Protocol)
7.2.11 SEALING GASKETS:
M.O.C. – Food Grade Quality Rubber FGN Rubber
For sealing the product container’s top and bottom face, as well as the filter bag’s bottom end, pneumatically operated inflatable sealing tubes are used. The tubes are inflated by compressed air at an operating pressure ranging from 2.0 to 2.5 kg/ cm². Low-pressure safety switches are provided for the safety of products. Filter bag ring is sealed by Holding it in s.s. ring.
The accessories of the assembly are :
01. Inflatable Sealing gaskets.
02. Pressure regulating valve with gauge.
03. Pressure switches etc.
04. Flow Control Valve.
7.2.12 CONTROL PANEL & POWER PANEL:
M.O.C. – Control Panel – S.S. 304 Thickness – 2 mm
M.O.C. – Pn. Panel – M.S Thickness – 1.6 mm
M.O.C. – Power Panel – M.S. Thickness – 1.6 mm
a) The SS 304 Control Panel is Top Pendent Machine mounted type located suitably near equipment & fitted with Electrical & pneumatic Instruments Viz.
01. Man Machine Interface (MMI)
02. Audio Signal Hooter, Emergency off Push Button
03. Push Buttons, Rotary Switches etc.
04. Printer for data recording with s.s. trolley
05. Pressure gauges
06. Pressure regulating valves
07. Diff. Pressure gauges.
An operator can control the equipment operation & process through these control panels.
b) The M.S. Foot Mounted single cabinet pneumatic panel is located in the technical area & fitted with pneumatic instruments viz.
01. PC Sealing Gasket Hand Valve + Pressure Gauge + Pressure Regulator
02. Filter Bag Lowering Hand Valve
c) The M.S. power panel is foot mounted single cabinet self-supporting type, located away from the production area consisting of:-
01. PLC Controller
02. Analog Modules
03. Motor Contactors
04. MCB’S
05. Ammeter
06. Voltmeter
07. Indication Lamps
08. Δ P Transmitters
09. Cooling Fan & Air Filters
10. Panel Door Switch
11. Connector terminals
12. Earth safety relay
13. Emergency Push Button
14. Misc. Electrical:
Due to high voltage switch gears, which are hazardous for flameproof areas, This panel is located away from the equipment. In the non-production area, same-time maintenance becomes easier due to its remote location.
7.2.14 CONTROL SYSTEM, FIELD INSTRUMENTS ETC:
The equipment is provided with a control system & field instruments as listed below.
S.No. | PARTICULARS | MAKE | FUNCTION |
01. | Differential Pressure Transmitter for Filter bag. | Make Name | Monitor Δ P Across filter bag |
02. | Differential Pressure Transmitter for Hepa | Make Name | Monitor Δ P Across HEPA |
03. | Programmable Logic Controller | Make Name | Programming of process Logic |
04. | Variable Frequency Drive (Provision only) | Make Name | Mitsubishi to suit motor |
05. | Operator Interface Terminal | Make Name | Process Monitoring |
06. | Printer | Make Name | Process Records |
07. | Temperature Sensor For | Make Name | Temp. Measurement & control |
Inlet Air | Make Name | For Air Inlet | |
Outlet Air | Make Name | For Air Outlet | |
Product Bed | Make Name | For Product Bed | |
08. | Heating Control Valve (On/Off Type) | Make Name | Steam Flow Control |
09. | Pr. Gauges and Regulators For PC Bottom, PCT Top & F.B.Tube Gaskets | Make Name | Air Pr. Regulation |
10. | Pr. Gauge For Air Filter, Regulation Unit | Make Name | Air Pr. Regulation |
11. | Pn. Cylinder | Make Name | Operating bag shaking |
12. | Pn. Actuator | Make Name | Operating Air Inlet Shut Off Valves |
13. | Pn. Actuator with Positioner | Make Name | Operating Blower Inlet Shut Off Valves |
14. | Pn. Actuator with Positioner | Make Name | For By-Pass Damper |
15. | Earth Relay & Sensor | Make Name | Ensure Earth Contact Off Product Container |
16. | Ammeter & Voltmeter | Make Name | Measuring Current & Voltage |
17. | Indication Lamps | Make Name | Ensure The Elec. Supply |
18. | Solenoid Valves | Make Name | Operating Sealing Gasket |
19. | Safety Pressure Switch | Make Name | For Sealing Gaskets |
20. | Air Filters | Make Name | Air Filtration & Pollution Control |
21. | Explosion Flap | Make Name | Safety of equipment & personnel |
22. | Silencer | Make Name | To reduce the noise level of the blower |
23. | Solid Flow Monitor (Provision on BI Duct) | Make Name | To Detect Bag Damage |
24. | WIP nozzle | Make Name | Inside washing of the body |
25. | Charging nozzle | S.S. 316 | Online material charging in the Product container |
26. | Flameproof Lamp | Make Name | For better visualization in R.C. |
7.3 cGMP PRACTICES:
The equipment will be designed and manufactured generally according to the cGMP practices listed below.
01. Provide smooth & rounded corners & edges and eliminate the sharp corners & edges as far as possible.
02. Facilitate for easy washing and cleaning of equipment
03. Provide drain points at bottom most locations where required
04. Avoid obstructions in the air path provide a guided air path for smooth air flow.
05. Provide the essential and adequate safety features to equipment, plant building & personnel.
06. Provide smooth surface finish on internal & external surfaces for easy cleaning.
07. Segregate the production Area & technical area for easy maintenance and to suit site conditions.
08. Provide insulation over ducts carrying Hot Air.
09. Properly concealed cabling should be provided so that equipment looks aesthetically better.
7.4 SAFETY FEATURES
The equipment shall be provided with safety features as listed below.
S. NO. | FEATURE | SPECIFIED |
01. | Pillar Supported Equipment | For cGMP Site Layout |
02. | Motor overload relay, if overload the switch gear trip | For Motor Safety |
03. | Earth safety relay, if improper earthing halts the process | For Equipment & Operator Safety |
04. | Emergency off, if activated stops the process | For Equipment & Operator Safety |
05. | Pressure Switches For – 1) P.C. Sealing Gasket | For Product Safety & Gasket Safety |
2) F.B. Tube Gasket | ||
3) Main Air Pressure | ||
If air pressure is lower than required then stop the process | ||
06. | Temp. sensor air inlet, if inlet temp. Increases than set | For Product Safety |
Value, the steam control valve closes. | ||
07. | Password protection to operate PLC, and recipe features via | For Product Safety & Batch |
Operator interface terminal | Integrity | |
08. | Explosion flap, if relieves the excess pressure | For Plant Building, Equipment |
Developed during explosion | & Human Safety | |
09. | Safety clamps (manual) for holding product containers & | For Equipment & Product Safety |
Acting as a jumper for earth continuity of PC & RC | ||
10. | Solid flow monitor, if activated stops the blower | For Preventing Product Loss |
(Provision on BI Duct & Panel) |
7.5 LIST OF ITEMS TO BE SUPPLIED BY CLIENT:
Items listed below shall be supplied by the client:
01. Hot Water inlet & outlet manifold piping, Check valves, pressure reducing valve, etc.
02. Necessary conduits, cable trays, cables for connecting utilities & instruments.
03. Structural support for Blower Assembly, Exhaust filter unit, Air preparation unit, etc.
04. All civil work related to the Fluid Bed Dryer.
05. Hot Insulation for air inlet duct pipes & bends.
CAUTION NOTE :
THE FLOOR LEVEL OF FBD ROOM MUST BE PERFECT TO 0-0 WATER LEVEL WITHOUT SLOPE FOR BETTER PERFORMANCE, SEALING OF PRODUCT CONTAINER & REDUCED POSSIBILITY OF INFLATABLE SEALING GASKETS FAILURE. MANUFACTURER WILL NO WAY RESPONSIBLE IF THE FLOOR IS UNLEVELLED.
8.0 MATERIAL OF CONSTRUCTION
S.NO. | PART NAME / COMPONENT | MOC / SEPCIFICATION | THK. / SIZE |
01. | AIR FILTER & HEATER HOUSING | S.S. 316 L | 3 mm |
02. | AIR HEATER | S.S. 304+ S.S. 304 | 3/4″OD/ 0.4 Thk. |
03. | DUCTING UP TO BLOWER SUCTION | S.S. 316 L / 304 | 2 / 3 mm |
04. | INLET SHUT-OFF VALVE (AIR & BLOWER) | S.S. 316 L | 35 mm |
05. | MAIN BODY | S.S. 316 L | 4 / 5 mm |
06. | BOTTOM BODY | S.S. 316 L | 4 mm |
07. | PRODUCT CONTAINER | S.S. 316 L | 4 mm |
08. | TROLLEY | S.S. 304 | 40 NB |
09. | TROLLEY WHEEL with Brakes | S.S. 304 + P.U. | 150 Ø |
10. | RETARDING CHAMBER | S.S. 316 L | 4 mm |
11. | FILTER BAG HOUSING | S.S. 316 L | 4 mm |
12. | EXPLOSION CHAMBER | S.S. 316 L | 4 mm |
13. | EXPLOSION FLAP | S.S. 316 L | 3 / 4 mm |
14. | BLOWER CASING & SUPPORT | M.S. | 4 mm |
15. | IMPELLER | Aluminium | 5 & 3 mm |
16. | BLOWER OUTLET DUCT PIPE & BENDS | M.S. | 3 mm |
17. | EXHAUST FILTER HOUSING | M.S. | 3 mm |
18. | SILENCER | M.S. | 1.6 / 3 mm |
19. | CONTROL PANEL | S.S. 304 | 2 mm |
20. | PNEUMATIC PANEL | M.S. | 1.6 mm |
21. | POWER PANEL | M.S. | 1.6 mm |
22. | HARDWARE | S.S. 304 / M.S. | |
23. | SEALING GASKETS ( INFLATABLE ) | Food Grade FGN Rubber | GM 250 S |
24. | SEALING GASKETS ( MISC. ) | Food Grade FGN Rubber | GM 250 S |
25. | FILTER BAG | P.C. Satin Cloth | GM 250 S |
26. | PRINTER TROLLEY | S.S. 304 | 25 NB & 16 G |
27. | CHARGING NOZZLE | S.S. 316 | 100 NB |
28. | WIP NOZZLE | S.S. 316 | 1″ BSP |
9.0 DOCUMENTATION
9.1 DRAWING:
M/S.XYZ company will provide the following drawings along with the documentation for equipment.
Categorize the Drawings as follows:
A General Arrangement / Schematic Line Diagram.
B Piping and Instrumentation Diagram ( P & ID ).
C Utility.
D Isometric.
E Electricals
F. Pneumatic
9.1.1 LIST OF DRAWINGS:
S. No. | Title | Category | Rev No. | Date | Drawings No. | Remark |
01. | G.A. Drawing F.B.D. | |||||
02. | G.A. Drawing Power Panel | |||||
03. | G.A. Dwg. Control Panel | |||||
04. | Earth Relay Circuit | |||||
05. | Hot water Manifolds | |||||
06. | P & I Diagram of FBD |
Comments ( if any ) :
__________________________________________________________________________
__________________________________________________________________________
__________________________________________________________________________
9.1.2 LIST OF DRAWINGS ( PNEUMATIC CIRCUITS )
S.No. | Title | Category | Drawings No. |
01. | Pneumatic Flow Circuit | ||
02. | Compressed Air Main Pneumatic Line | ||
03. | IT Sealing for product Container | ||
04. | Filter Bag Sealing Tube | ||
05. | Hot Water Control Valve | ||
06. | Filter Bag Δ P Port Cleaning | ||
07. | Filter Bag Shaking & Lowering (Telescopic Cylinder) | ||
08. | Air Inlet Shut off Valve / Actuator | ||
09. | PID Butterfly Valve Cylinder | ||
10. | PID Air Inlet By-Pass Damper Actuator | ||
11. | Condensate Drain Valve | ||
12. | Bottom Drain Valve | ||
13. | MISCELLANEOUS FITTINGS | ||
14. | PN. SYMBOL & LOGIC |
Comments ( if any ) :
__________________________________________________________________________ __________________________________________________________________________
9.1.3 LIST OF DRAWINGS ( ELECTRICAL )
S. No. | Title | Category | Rev No. | Date | Drawings No. | Remark |
01. | Cable Schedule | |||||
02. | Electrical Circuit Diagram |
Comments ( if any ) :
__________________________________________________________________________
__________________________________________________________________________
__________________________________________________________________________
The Alliance Engineering Company will provide the following documents along with the equipment at the time of delivery.
S.NO. | TITLE OF DOCUMENTS |
01. | OPERATING MANUALS |
02. | SPARE PART LIST |
03. | LUBRICATION CHART |
04. | MATERIAL LIST WITH MATERIAL TEST CERTIFICATE |
05. | IMPELLER BALANCING CERTIFICATE |
06. | MANUFACTURERS CERTIFICATES FOR MAJOR BOUGHT OUT ITEMS |
07. | LIST OF BOUGHT-OUT ITEMS |
08. | DOCUMENT FILE WITH INSTRUMENT MANUALS, PREVENTIVE MAINTENANCE, OTHER |
TECHNICAL DETAILS | |
09. | CALIBRATION CERTIFICATES FOR INSTRUMENTS WHERE CALIBRATION IS REQUIRED |
10. | ELECTRICAL DATA & COMPONENT LIST |
11. | PLC DATA SHEET ( REFER ANNEXURE 4) |
12. | PLC OPERATING MANUAL |
13. | PLC LADDER LOGIC HARD COPY |
14. | PROGRAMME PRINT FORMAT |
15. | AS BUILT DRAWINGS |
10.0 SUPPORTING UTILITIES
A) The following utilities shall be provided by client at the site for satisfactory operation of equipment.
S.NO. | UTILITY NAME | OPERATING RANGE | SCOPE | REMARK |
01. | ELECTRIC POWER SUPPLY | 415 Volts ± 5% 3 phase, | ||
50 Hz + 5%, 4 wire | ||||
02. | POWER REQUIREMENT | ≃ 22.5 KW / 30 HP | ||
03. | HOT WATER SUPPLY, CLEAN | 3.5 to 4.5 kg/cm² (g) Pressure | ||
& FILTERED | Minimum, 125 ºc inlet temp. | |||
35 or 70 PSIG | ||||
04. | HOT WATER CONSUMPTION | ≃ 6000 to 7000 kg per hour | ||
05. | COMPRESSED AIR SUPPLY DRY, | 5 to 6 kg/ cm² (g) | ||
CLEAN, MOISTURE-FREE | 70 or 84 PSIG | |||
06. | COMPRESSED AIR CONSUMPTION | ≃ 10 m³ / hr or 6 CFM when | ||
Used as FBD | ||||
07. | DRAIN PITS & PIPES & VALVES | As Reqd. |
B) Accessories, as mentioned below, shall be provided by client at site.
S.NO. | DESCRIPTION | SPECIFICATION | SCOPE | REMARK |
01. | MAIN POWER SUPPLY CABLE | 4 Core, copper, | ||
16 mm² Armoured | ||||
02. | MOTOR SUPPLY CABLE | 3 Core, copper, | ||
6 mm² Armoured, 2 Nos | ||||
03. | MISC. INSTRUMENT CABLE & | As per details | ||
CABLE GLANDS | ||||
04. | HOT WATER INLET & OUTLET PIPING | As per Layout | ||
80 mm NB main reduced | ||||
to 50 NB near the Heater inlet | ||||
20 mm NB at the heater outlet | ||||
06. | AIR SUPPLY LINE | ≃ 15 mm NB with | ||
necessary moisture traps, | ||||
valves, strainers, etc. |
11.0 SPARE PARTS:
11.1 SPARE PARTS:
Incorporated in the document file, M/S.XYZ company will provide a list of spare parts that may be required to keep equipment in good working condition.
11.2 LUBRICATION CHART:
Incorporated in the document file, M/S.XYZ company will provide a list of lubricants that may be required to keep machine in good working condition.
11.3 FILTERS & FILTER BAGS:
Along with the document file, M/S.XYZ company will provide the details of filters & filter bags that may be required to keep machine in good working condition.
In house certificates should be provided.
12.0 LIMITATION FOR PERFORMANCE OF EQUIPMENT:
12.1 POWER FAILURE:
In the event of power failure, the process will stop, but through a battery backup facility PLC shall remain ‘ON’ & save the data recorded for retrieval.
12.2 CONTROL PANEL FAILURE:
Failure in the control panel will result in interruption of the process. However data till the fault occurred shall get saved in the memory of PLC.
12.3 UTILITIES FAILURE
Failure of utilities like electric power and compressed air will halt the process and failure of steam supply will stop the air heating.
However, the data till the stoppage occurred shall be saved in the memory of PLC.
13.0 VARIATIONS & CORRECTIVE ACTION:
VARIATION (IF ANY ):
CORRECTIVE ACTION TAKEN:
14.0 PRE-QUALIFICATION CHECKLIST:
14.2 SPECIFIC CHECKPOINTS:
Following is a list of specific points of Fluid Bed Dryer:
S. No. | Test particulars | Specifications | Observation | Acceptance |
01. | Level of the main body | Perfectly Leveled | ||
02. | Gap Between Sealing Gasket & Product Container Faces | 5 to 8 mm | ||
03. | PC Sealing Tubes Air Pressure | 2.0 to 2.5 kg/cm² Gauge Pressure | ||
04. | F.B. Tube Sealing Air Pressure | 2.0 to 2.5 kg/cm² Gauge Pressure | ||
05. | Main Compressed Air Supply Pressure | 6 to 8 kg/cm² Gauge Pressure | ||
06. | Hot Water Supply Pressure near the Air Heater | 3.5 to 4.5 kg/cm² Gauge Pressure 125 ºC minimum | ||
07. | Earth Sensor | Visual Exam. for contact | ||
08. | Inflatable Sealing Gaskets | Visual Exam. for Leakproof ness | ||
09. | Impeller Direction of rotation | Clockwise from the Motor end | ||
10. | Exhaust BFV Sealing Gasket | Visual Exam. for Wear / Damage | ||
11. | Explosion Flap | Visual Exam. For Damage | ||
12. | Filter Bag | Visual Exam. For Damage | ||
13. | Bag Shaking Time | Piston up time 1.2 to 1.8 Sec. Piston downtime 1.2 to 1.8 Sec. | ||
14. | Motor Current | 30 HP Motor Full Load 39 Amp |
15.0 Final Respot:
15.1 Summary:
15.2 Conclusion:
16.0 DESIGN QUALIFICATION APPROVAL:
APPROVED / NOT APPROVED
FOR XYZ Pharmaceutical company. – Place Name.
NAME | DESIGNATION | SIGNATURE | DATE |
FOR M/S. XYZ company,- Place Name.
NAME | DESIGNATION | SIGNATURE | DATE |
Manager Engineering | |||
Instrumentation Engineer | |||
Planning Engineer | |||
Electrical Engineer | |||
17.0 APPENDIX:
17.1 Abbreviations and Definitions Reference Document:
SR.NO. | ABBREVIATIONS | PARTICULARS |
01. | ∆ PG | Differential Pressure Gauge |
02. | A | Ammeter |
03. | AI | Analog Input |
04. | AO | Analog Output |
05. | AFS | Air Flow Sensor |
06. | ASS | Ammeter Selector Switch |
07. | AISOV | Air Inlet Shut-Off Valve |
08. | BISOV | Blower Inlet Shut-Off Valve |
09. | C | Contactor |
10. | CF | Cooling Fan |
11. | CGMP | Current Good Manufacturing Practice |
12. | CT | Current Transformer |
13. | CDV | Condensate Drain Valve |
14. | DI | Digital Input |
15. | DO | Digital Output |
16. | DS | Panel Door Switch |
17. | DH | Dehumidifier |
18. | EPB | Emergency Push Button |
19. | ER | Earth Relay |
20. | ES / ED | Earth Senor / Earthing Device |
21. | F | Fuse |
22. | FB | Filter Bag |
23. | FBD / FBP | Fluid Bed Dryer / Fluid Bed Processor |
24. | For Pn. Fitting and Accessories | Pn. Accessories, Ref. Pn. Data list & Circuit |
25. | FBT | Filter Bag Tube |
26. | FCD | Flow Control Damper |
27. | H | Hooter |
28. | HCV | Heating Control Valve |
29. | HMI or MMI | Man Machine Interface |
30. | HTW | Hepa Test Window |
31. | HP | Horse Power |
32. | HV | Hand valve |
33. | I/P | I to P Converter |
34. | LR | Pressure Regulating Valve |
35. | M | Motor |
36. | M 1 | Proportional Pn. Actuator |
37. | MCB | Miniature Circuit Breaker |
38. | ME | MIST. Eliminator |
39. | MOC | Material of Construction |
40. | OIT | Operator Interface Terminal |
41. | O/L | Overload Relay |
42. | PB | Push Button |
43. | PC | Product Container |
44. | PID | Proportional (P), integral (I), Derivative (D) |
45. | PCB | Product Container Bottom |
46. | PCT | Product Container Top |
47. | PG | Pressure Gauge |
48. | PLC | Programmable Logic Controller |
49. | PO | Purchase Order |
50. | PS | Pressure Switch |
51. | RH | Relative Humidity |
52. | RPM | Rotations Per Minute |
53. | RS | Rotary Selector Actuator |
54. | S | Solenoid Valve |
55. | SS | Stainless Steel |
56. | SFM | Solid Flow Monitor |
57. | TR | Temp. Transmitter |
58. | TC & B | Triclover & Blind |
59. | V | Voltmeter |
60. | VSS | Voltmeter Selector Switch |
61. | VFD | Variable Frequency Drive |

Naresh Bhakar is the Founder and Author at Pharmaguddu.com, bringing his extensive expertise in the field of pharmaceuticals to readers worldwide. He has experience in Pharma manufacturing and has worked with top Pharmaceuticals. He has rich knowledge and provides valuable insights and data through his articles and content on Pharmaguddu.com. For further inquiries or collaborations, please don’t hesitate to reach out via email at [email protected].