Drum dryer and roll dryer is widely used in industries because of their heat-drying property. In this article learn about principle, constructions, and workings, along with their advantages, disadvantages, and pharmaceutical applications.
Principle of Drum Dryer:
In the drum dryer principle, we use a heated hollow metal drum that rotates on its longitudinal axis. The drum is partially immersed in the solution to be dried. It is a simple and effective method that ensures proper drying of the material. The solution is carried as a film on the surface of the dryer and dries to form a layer that is collected.
Construction of Drum Dryer or Roll Dryer:
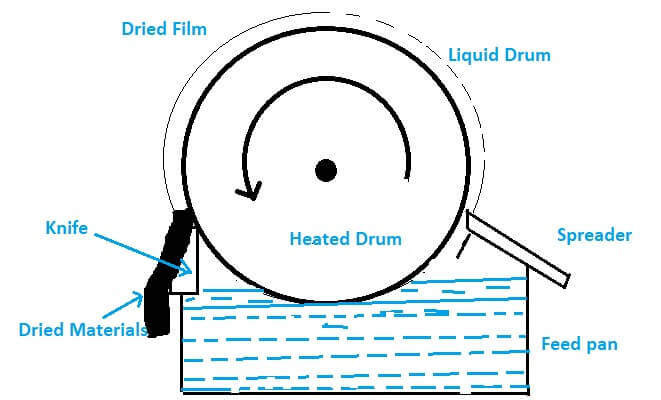
- The drum dryer, a moving bed dryer, is constructed using cast iron and stainless steel materials.
- The MOC of the drum dryer has durability, cleanliness, and resistance to chemical attacks.
- It consists of a hollow steel drum of about 0.75 to 1.5 m in diameter and 2.4 m in length.
- It is heated internally, usually by steam, and rotates in its longitudinal axis.
- The external surface of the drum is polished for long sustainability.
- For drying purposes, the materials are fed into the pan.
- The drum is partially dipped in the pan.
- Spreader is used in spreading liquid film eventually on a drum roller.
- The drum is rotated continuously and its speed is adjusted so that all the liquid is fully vaporized.
- Dried deposited or material can be scraped off with the help of a knife and collected in a storage bin.
a. Double Drum Dryer:
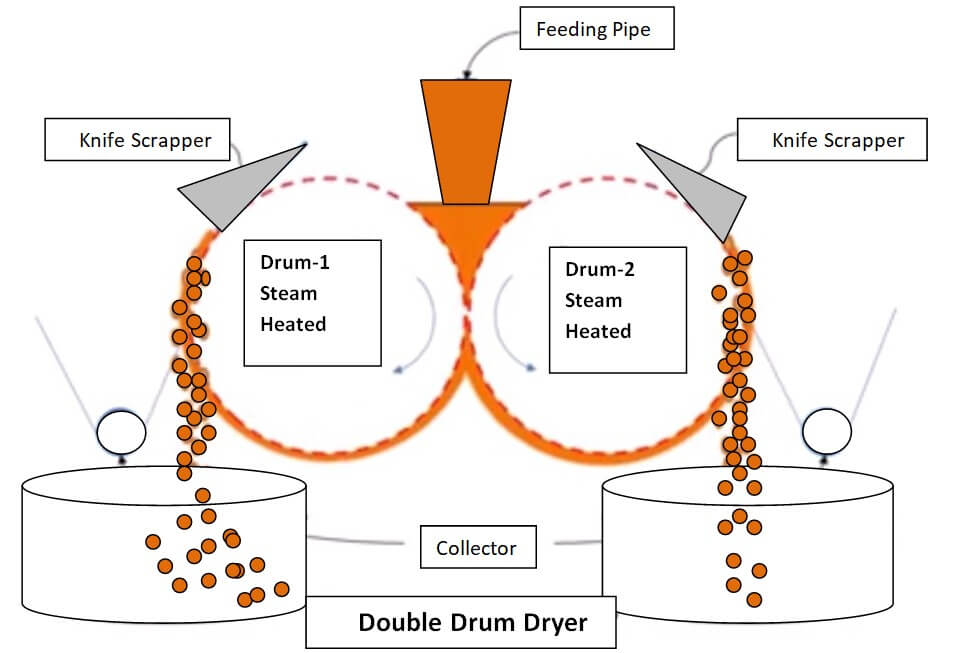
- It is utilized for low to medium-viscous materials.
- Two drums are provided to rotate in opposite directions.
- The product is fed in between these two drums and the distance is adjusted as per to get desired material.
b. Vacuum Drum Dryer:
- A vacuum dryer allows for drying at lower temperatures by operating under vacuum conditions.
- In a Vacuum drum dryer, two steam-heated drums rotate within an airtight casing under a high vacuum.
- The liquid is introduced between the drums from the top, dried, and then scraped off before the drums complete a full rotation.
- There is no accumulation of product residues, and no material recirculation occurs.
- It is very easy to inspect and maintain.
- It is useful for heat-sensitive products and the low-temperature evaporation of solvents. Vacuum dryers provide careful treatment for feed materials, preserving thermolabile substances like enzymes and proteins and preventing protein denaturation.
Working of Drum Dryer:
Single Drum Dryer:
- In a single drum dryer, the drum body is heated internally by steam.
- The heat due to steam is transferred by conduction to the materials.
- As we rotate the drum, the liquid materials in the feed pan stick to the drum’s outer surface, forming a thin layer.
- Then materials get dried which is scrapped by the knife which then fall into a storage bin.
Double Drum Dryer:
- In a double-drum dryer, the liquid to be dried is fed into the space between the two drums.
- Then the drum starts to rotate in the opposite direction.
- The contact time between the material and the hot metal surfaces is typically only 6 to 15 seconds
- After that, a knife on each drum removes the dry product.
Advantages of Drum Dryer or Roll Dryer:
- Drying takes place in less time
- Suitable for thermosensitive drugs.
- Occupies less space.
- A vacuum chamber can enclose the drum to lower drying temperatures.
- Rapid drying takes place due to fast heat and mass transfer.
Related: Mixing – Pharmaceutical Engineering a Complete Guidance
Disadvantages of Drum Dryer or Roll Dryer:
- High maintenance costs.
- Requires skilled operators to control film thickness, rotation speed, and temperature.
- Not ideal for products with low solubility.
Pharmaceutical Uses of Drum Dryer or Roll Dryer:
- It is used for viscous liquids, slurries, suspensions, and pastes, to turn them into powders or flakes.
- This drying equipment is widely used in Food & Dairy industry, as well as the Chemical & Pharmaceutical industries, for drying various types of pastes and slurries.
Variants:
- Vacuum drum dryers integrate both the drum and feed line into a vacuum chamber, which helps in the drying of heat-sensitive materials.
- On a large-scale, two drums can be arranged in parallel, rotating in opposite directions with a shared feed inlet.
Conclusion:
In conclusion, drum dryers and roll dryers provide an easy solution for drying various materials, including viscous liquids, slurries, and pastes in various industries.
FAQs (Frequently Asked Questions):
Ans: Both drum and roll dryers can easily handle heat-sensitive materials.
Ans: Drum dryers have lots of advantages including reduced drying time, suitability for thermosensitive drugs, compact size, and rapid heat and mass transfer, leading to proper drying processes.
Ans: No. it is not suitable for products with low solubility.
Ans: This equipment is widely used in Food & Dairy industry, as well as the Chemical & Pharmaceutical industries, for drying various types of pastes and slurries.
Ans: Yes, on large-scale production, it is possible to use multiple drums arranged in parallel, rotating in opposite directions.

Naresh Bhakar is the Founder and Author at Pharmaguddu.com, bringing his extensive expertise in the field of pharmaceuticals to readers worldwide. He has experience in Pharma manufacturing and has worked with top Pharmaceuticals. He has rich knowledge and provides valuable insights and data through his articles and content on Pharmaguddu.com. For further inquiries or collaborations, please don’t hesitate to reach out via email at [email protected].