Installation Qualification Protocol of Automatic Injectable Powder Filling With Rubber Stoppering Machine is done to ensure that the system received matches the Design specification.
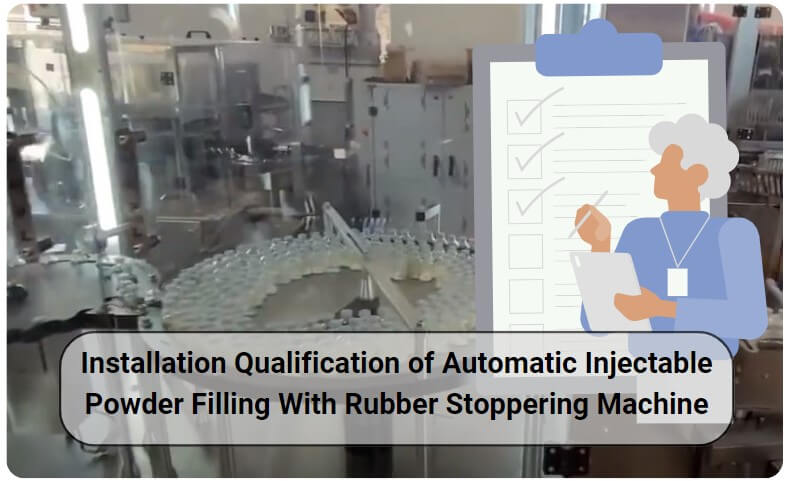
SERIAL NO. | ITEM DESCRIPTION |
1.0 | PROTOCOL APPROVAL |
2.0 | OVERVIEW: |
2.1 | Objective |
2.2 | Purpose |
2.3 | Scope |
2.4 | Responsibility |
2.5 | Execution Team |
3.0 | ACCEPTANCE CRITERIA |
4.0 | REVALIDATION |
5.0 | INSTALLATION QUALIFICATION PROCEDURE |
5.1 | System Description |
5.2 | Major Components |
5.3 | Instruction For Filling The Checklist |
5.4 | Installation Checklist |
5.5 | Identification of Major Components |
5.6 | Material of construction |
5.7 | Identification of Supporting Utilities |
5.8 | Identification of Safety And interlock system |
5.9 | Identification of standard operating procedure (SOP) |
5.10 | Identification of component to be calibrated |
5.11 | Verification of Drawing and Documents |
5.12 | Abbreviations |
5.13 | Deficiency And Corrective Action(s) report(s) |
5.14 | Annexure(s) |
6.0 | INSTALLATION QUALIFICATION FINAL REPORT |
6.1 | Summary |
6.2 | Conclusion |
6.3 | Final report approval |
Related: Operation Qualification of Sterilizing and Depyrogenation Tunnel
1.0 | PROTOCOL APPROVAL: |
The signing of this approval Protocol indicates agreement with the qualification approach described in this document. If a modification to the qualification approach becomes necessary, an addendum shall be prepared and approved. The protocol cannot be used for execution unless approved by the following authorities.
This Installation Qualification protocol of Automatic Injectable Powder Filling with Rubber Stoppering Machine Model (Modal Name) has been reviewed and approved by the following persons:
FUNCTION | NAME | DEPARTMENT | SIGNATURE | DATE |
PREPARED BY | QUALITY ASSURANCE | |||
REVIEWED BY | PROJECTS / ENGINEERING | |||
REVIEWED BY | PRODUCTION | |||
APPROVED BY | QUALITY ASSURANCE |
2.0 | OVERVIEW: |
2.1 | OBJECTIVE: |
The objective of developing and executing this protocol is to collect sufficient data pertaining to the Automatic Injectable Powder Filling with Rubber stoppering Machine Model (Modal Name) and define the qualification requirements and acceptance criteria for the Filling and Rubber stoppering. Successful completion of these qualification requirements will provide assurance that the Automatic Injectable Powder Filling with Rubber stoppering Machine Model (Modal Name) was installed as required in the sterile area. | |
2.2 | PURPOSE: |
The purpose of this protocol is to establish documentary evidence to ensure that the Automatic Injectable Powder Filling with Rubber stoppering Machine Model (Modal Name) system received matches the Design specification and also to ensure that it is properly and safely installed. The Automatic Injectable Powder Filling with Rubber stoppering Machine Model (Modal Name) is used for filling the powder and stoppering of free-standing vials. | |
2.3 | SCOPE: |
This Protocol is applicable to the installation of Automatic Injectable Powder Filling with Rubber stoppering Machine Model (Modal Name) at the sterile injectable manufacturing facility in XYZ Pharmaceutical & the subsequent documentation. |
2.4 | RESPONSIBILITY: |
The following shall be responsible; Head of Department: Their Responsibilities. |
2.5 | EXECUTION TEAM: |
The satisfactory installation of the Automatic Injectable Powder Filling with Rubber Stoppering Machine Model (Modal Name) shall be verified by executing the qualification studies described in this protocol. The successfully executed protocol documents that the Automatic Injectable Powder Filling with Rubber stoppering Machine Model (Modal Name) is installed and is satisfactorily integrated. The execution team is responsible for the execution and installation of Automatic Injectable Powder Filling with Rubber stoppering Machine Model (Modal Name). The execution team comprises of: |
DEPARTMENT | DESIGNATION | NAME | SIGNATURE | DATE | |
PROJECTS /ENGINEERING | |||||
PRODUCTION | |||||
QUALITY ASSURANCE | |||||
3.0 | ACCEPTANCE CRITERIA: | ||||
3.1 | The Automatic Injectable Powder Filling with Rubber Stoppering Machine Model (Modal Name) shall meet the system description given in the design qualification. | ||||
3.2 | The Automatic Injectable Powder Filling with Rubber Stoppering Machine Model (Modal Name) shall meet with the acceptance criteria mentioned under the topic “Identification of major components.” | ||||
3.3 | Manual/PLC shall operate the Automatic Injectable Powder Filling with Rubber stoppering Machine Model (Modal Name) system. |
4.0 | REVALIDATION CRITERIA: |
The Automatic Injectable Powder Filling with Rubber Stoppering Machine Model (Modal Name) has to be revalidated if | |
✔There are any major changes in system components, which affect the performance of the system. ✔Shifting of the equipment from one location to another. ✔As per revalidation date and schedule. |
5.0 | INSTALLATION QUALIFICATION PROCEDURE: |
5.1 | SYSTEM DESCRIPTION |
- Automatic Single Head Injectable Powder Filling with Rubber Stoppering Machine Model (Modal Name) is a compact versatile machine. The Machine can be used to fill the injectable Powder in a duly sterilized vial received from the sterilizing tunnel. Then vial will be transferred to the next operation of Rubber Stoppering. Duly Rubber stopper vial reaches to the Unscrambler. This Machine can handle vials ranging from 5 ml to 30 ml (Min. Dia 24mm to Max. Dia. Up to 53mm). Duly stoppered vial further moves to the sealing operation.
- RUBBER STOPPERING UNIT: It works on the basic principle of that when a duly powder-filled vial moves on the machine conveyor then it will be held by the timing belt of the rubber stoppering unit simultaneously vial pickup the stopper from the exit end of the chute. The two-pressing roller will press the rubber stopper during the vial movement with the timing belt. This shall be suitable for 20mm rubber stoppers.
- UNSCRAMBLER: Unscramble is located at the in-feed side of the machine. The main working principle of the turn table is to deliver the vials either to the filling machine by rotary movement of the round plate through a supportive nylon guide. The output of the turn table depends on the speed of the round plate and the diameter of the round plate.
- SCRAMBLER: The Scrambler is located at the infeed side of the machine. The main working principle of the turn table is to collect the filled & stoppered vials by rotary movement of the round plate through a supportive nylon guide. The output of the turn table depends on the speed of the round plate and the diameter of the round plate.
5.2 MAJOR COMPONENTS.
5.2.1 Machine Frame Structure.
The machine frame is made of M.S. and fully covered with the S.S. 304 Sheet. Suitable SS covers cover the entire body from the sides. The Main Drive Gear Motor, Transmission Assembly, Lateral Belt Assembly, Conveyor Assembly, Filling Head Assembly, Vial Separator Assembly, Media Filling arrangement, Rubber Stoppering Unit, etc driving assembly are inside the stand frame.
5.2.2 Main Drive Mechanism.
The Main Drive gearbox assembly is mounted on the bottom side of the machine frame and it contains the main gear motor. The main drive gear motor is coupled with the Transmission Assembly, which drives the Powder filling unit. It drives the lateral belt unit conveyor belt through the chain drive.
5.2.3. Conveyor Belt.
The conveyor is mounted on the top plate of the machine and the main purpose of the conveyor is to feed the vial to the Powder filling unit. The conveyor is a 3.25” width Delrin material. Moving on an SS.”C” Type channel and its drive are taken from the Bottom of the machine from the lateral belt assembly. A nylon chain sprocket is fitted at the two ends of the conveyor for driving the conveyor “C” channel. S.S. guides are provided on the conveyor to adjust according to the vial diameter and height. The pressing Belt assembly is fitted on the conveyor for holding the vial during the stoppering operation.
5.2.4. Filling Head Assembly:
It is the main part of the machine, where the actual Powder Filling Operation is going to be done. It is located after the Unscrambler. It is mounted on S.S. Pipe. The Aluminium plate from the front and backside of the head will cover the filling head. It consists of a Powder Wheel, powder Hopper, and Geneva cam mechanism. It consists of one powder wheel having 8 filling ports. This machine will give an output of 120 vials/minute depending on the vial size.
5.2.5. Vial Separator Assembly: Two vial separator assemblies are assembled on the machine, just below the powder-filling wheel. The vial separator has to be changed for changes in each vial diameter or multiple dosing systems.
5.2.6. Vibrator Assembly: The Vibrator assembly is located at the right-hand position of the filling head on a separate S.S.pipe, it has having vibrator unit with a magnetic coil with spring steel vibrator strips to transfer the vibration to the Rubber Stopper bowl. The vibrator bowl will be made of S.S. 316 material. The vibrator unit will be covered with the S.S. 304 sheet. The vibrator bowl delivers the Rubber Stopper to the chute, which delivers the Rubber Stopper to the exit end of the chute.
Then vial will pick up the Rubber Stopper during the linear movement of the vial with the timing belt assembly. The vibratory bowl has the facility to make a movement of the rubber stopper on a smooth buffer track and during the movement wrong directional stopper will fall down in the bowl and not move towards the exit side of the bowl. The vibrator speed can be increased or decreased by the % speed pot given on the switch box.
5.2.7. Rubber Stopper pressing Device assembly: The Rubber stopper pressing device is mounted below the vibrator mounting plate. A rubber stopper pressing device is used to press the rubber stopper which is placed on the vial by means of two pressing rollers. Pressing roller pressure can be adjusted as per the requirement. The rubber stopper pressing device drive is taken from the direct gear motor provided on the backside of the pressing device. Its speed will increase or decrease by the main drive speed pot.
5.2.8. Vial Holding Pressing Device Assembly.:Vial Holding rubber stopper pressing device is mounted on the conveyor. It is used to hold the vial during rubber stopper pressing.
We can run different sizes of vials without any changing parts by rotating the adjustable screw knob. The vial will be held firmly by the pair of timing belts and during the linear movement of the vial with the timing belt vial pick up the rubber stopper from the exit end of the chute and it will get pressed in the rubber stopper pressing device. Then the vial further moves to the turn table for the next sealing operation.
5.2.9.Electrical Connection: All Electrical wires and pneumatics hose is located inside of the machine. All wires are appropriately numbered & identified.
5.2.10.Control Panel: A Control panel is provided on the machine. Different switches are provided like Emergency Stop & Speed Pot etc.
Equipment Details:
Equipment Name: Automatic Injectable powder filling with rubber stoppering machine
Make: Make Name
Model No.: XYZ
Capacity: 120 vials/Minute
Related: Installation Qualification of Sterilizing and Depyrogenation Tunnel
5.3 | INSTRUCTION FOR FILLING THE CHECKLIST |
5.3.1 | In case of compliance of the test use the word ‘Complies’ otherwise use ‘Does not comply‘ to indicate non-compliance. |
5.3.2 | For identification of the components of the equipment and utilities use the word ‘’yes’’ to show its presence and use ‘No’ to indicate the absence of the identity. |
5.3.3 | Give detailed information in the summary and conclusion part of the Installation Qualification report. |
5.3.4 | Whichever column is blank or not used ‘NA’ shall be used. |
5.4 | INSTALLATION CHECKLIST: |
The installation checklist is as follows: |
Sr. NO. | Name of the component / Accessory | PresentYES / NO | CHECKED BY(SIGN) | DATE |
01. | Verify that the “As Built” drawing is complete and represents the design concept. | |||
02. | Verify that major components are securely anchored and shockproof. | |||
03. | Verify that there is no observable physical damage. | |||
04. | Verify that there is sufficient room provided for servicing. | |||
05. | All access ports are examined and cleared of any debris. | |||
06. | Equipment identification nameplate visible. | |||
07. | Verify that all piping and electrical connections are done according to the drawings. | |||
08. | Safe electrical connections. | |||
09. | A wiring diagram affixed to the inside section of the control panel. | |||
10. | Units installed on the foundation are secure in place as per the manufacturer’s recommendations. | |||
11. | Check the dimensions: ——mm (L) X ——-mm (W) X ——–mm (H) |
5.5 | IDENTIFICATION OF MAJOR COMPONENTS: |
Describe each critical component and check them and fill out the inspection checklist. |
System Components | Design Specification | Complies / Does Not Comply | Checked By(Sign) | Date | |||
Equipment description | Name: Automatic Injectable powder filling with rubber stoppering machine Make: Maker Name Model No. : XYZ Output: 120 vials/Minute | ||||||
Main Gear Box with Motor | Make: Make Name Model: XYZ Sr. No: XYZ, 0HP, 3Phase, 415V, 50HZ & RPM: 1400 | ||||||
Unscrambler gearbox with motor | Make: Make Name Model: XYZ.5HP, RPM: 1400 Gearbox ratio: 10:1 | ||||||
A.C. Frequency Drive for main drive, Unscrambler & Scrambler | Make: Make Name Model: XYZ, H.P: 1.0 | ||||||
No Vial No Filling Sensor | Make: Make Name Model: XYZ, Type: PNP, Volt: 10 to 30 | ||||||
No Rubber stopper in chute machine stop sensor No Filling Sensor | Make: Make Name Model: XYZ, Type: PNP, Volt: 10 to 30 | ||||||
Pressing Roller Assembly | Make: -Make Name Gear Box No: XYZ Ratio: 30:1 Motor No: XYZ R.P.M.: -1375. PHASE: -3 Phase. | ||||||
Vacuum Pump. | Make: Make Name, Ltrs. 300H.P.: 1H.P. | ||||||
Vacuum Pump Motor. | Make; Make Name, R.P.M.: 1400H.P.: 1H.P. 3 Phase. | ||||||
Vibrator Contactor | Make: Make Name: -LC1 D09A.M.P.: -9A | ||||||
Vibrator Relay | Make: Make Name: – LRD 10A.M.P.: – 7 To 10A | ||||||
Main Contactor | Make: Make Name: – LC1D18.A.M.P.: -18A. | ||||||
M.C.B. Main Supply | Make: Make Name No of Pole: -2 Pole.A.M.P.:-16A | ||||||
M.C.B. Main A.C. Drive | Make: Make Name No of Pole: -2 Pole.A.M.P.: -10A | ||||||
M.C.B. Unscrambler & Scrambler | Make: Make Name No of Pole: -2Pole.A.M.P.: -6A | ||||||
Relay Card | Make: – Make Name No of Relay: 6 Relay, For Sensor On/Off. | ||||||
Two SSR Card | Make:-Make Name, For Dosing | ||||||
Transformer | Make; – Make Name Voltage-18 To 220V. | ||||||
Vibrator controller | Make: – Make Name A.M.P.: -5A | ||||||
Pressure Gauge | Make: – Make Name, 7Kg/cm2 | ||||||
Vacuum Gauge | Make: – Make Name, 25Hg/mm760Lpm. | ||||||
Air Regulator | Make: – Make Name. Filter-1/4” Connection & 1/8” Connection. | ||||||
Rota Meter. | Make: – Make Name. 30 Flowtran LPMCO2 +N2 | ||||||
Vacuum Filter | Filter Housing: Make: -Polypropylene. Filter Element: Make: -PPSPUN (Kanisha) 0.2 Micron. Fitting 3/4” Connection. Inlet/Outlet. 8×6 Tube. | ||||||
Air Filter | Filter Housing: Make: -S.S. 10” DOE & S.S.316L. Filter Element: Make: -PLEATED (KANISHA) 0.2Micron. Fitting 3/4” Connection. Inlet/Outlet 8 x 6 Tube. | ||||||
SMPS | Make:- Make Name, Supply I/P: 230V, Single Phase, O/P: 24V, 2.1 A.M.P | ||||||
Inductor (Chock) | Make: -Make Name,Phase:- 3 Phase 415V, A.M.P : 30 A.M.P. | ||||||
Solenoid ValveDosing, Pre & post Gassing | Make: Make Name, Model: – G-50, ¼” Inlet. | ||||||
Dosing Sensor.No Vial No Filling Sensor. | Make: Make Name, No: -QS18VP6LP, Type:-PNPVolt:-10 To 30 | ||||||
No Stopper M/C. Stop Sensor (Mount on Chute) | Make: Make Name, No:-QS18VP6FP, Type:-PNPVolt:-10 To 30 | ||||||
Vial Separator Clutch Proxy. | Make: Make Name. 4mm Range.Type: PNP.Volt:-10 To 30 | ||||||
Dosing Cam Proxy | Make: Make Name. Range. 4mm, Type: PNPVolt: -10 To 30. | ||||||
No Stopper on the Vial Sensor. | Make: Make Name. No: -QS18VP6FP, Type: PNPVolt:-10 To 30. | ||||||
All Push Button | Make: Make Name | ||||||
Main On/Off Actuator | Make: Make Name | ||||||
% Speed Pot | Make: Make Name.10W/5W. |
5.6 | MATERIAL OF CONSTRUCTION: |
S. No. | Component | Material of construction | Method of verification | Checked By/Date |
1. | Powder Wheel | SS-316L | Visually with test certificate | |
2. | Powder Hopper | SS-316L | Visually with test certificate | |
3. | Vibrator Bowl | SS-316L | Visually with test certificate | |
4. | Vibrator Bowl Chute | SS-316L | Visually with test certificate | |
5. | Powder Wheel Piston | SS-316L | Visually with test certificate | |
6. | Piston Tips | Nylon 6. (Food Grade) | Visually with test certificate | |
7. | Piston “O” ring & Washer | Neo print Rubber. | Visually with test certificate | |
8. | Top Seal For Hopper | Teflon | Visually with test certificate | |
9. | Doctor Blade for hopper | Teflon/S.S. | Visually with test certificate | |
10. | Media Filling syringe | SS-316L | Visually with test certificate | |
11. | Nozzle for media Filling | SS-316L | Visually with test certificate |
5.7 | IDENTIFICATION OF SUPPORTING UTILITIES: |
Sr. No. | UTILITY | PROPERLY IDENTIFIED & CONNECTED (YES/NO) | CHECKED BY (SIGN) | DATE |
1. | Electrical supply: 415 V, A.C., 3 Phase, 50 Hz. | |||
2. | Air Supply (Nitrogen Gas for Dosing): 1Kg/cm2 (15Kg/40,000 Vials) | |||
3. | Vacuum supply 15” Hg. |
5.8 | IDENTIFICATION OF SAFETY AND INTERLOCK SYSTEM: |
Identify and record the safety and interlock features (if any) and their function in the following tables: |
Name of the safety feature/interlock | Specified Function | Identified by (Sign) | Date |
No vial No Filling Sensor | No vial no filling system is provided to avoid the wastage of costly powder, while the machine is running in ideal condition and the vial is not present below the powder wheel. | ||
Vial Separator Clutch Proximity Switch | If during production any vial comes with an over diameter or over height then any of the three clutches will get operated and through that signal machine will get OFF. | ||
No Stopper in Chute Machine Stop Sensor | This sensor is used to sense the presence of a rubber stopper in the chute. In case during the production time if there is no rubber stopper present in the chute then it will stop the machine. |
5.9 | IDENTIFICATION OF STANDARD OPERATING PROCEDURE (SOP) | |
The following Standard Operating Procedures were identified as important for the effective performance of Automatic Injectable powder filling With a Rubber Stoppering Machine. | ||
1. | Operation and cleaning of Automatic Injectable powder Filling With Rubber Stoppering Machine | |
2. | Preventive maintenance of Automatic Injectable powder Filling With Rubber Stoppering Machine | |
5.10 | IDENTIFICATION OF COMPONENT TO BE CALIBRATED: |
Sr.No. | Name of the Instrument | Location | Specification | Identified By(Sign | Date | ||
5.11 | VERIFICATION OF DRAWING AND DOCUMENTS: |
The following documents are reviewed and attached as listed below: |
Sr. No. | DRAWING AND DOCUMENT DETAIL | CHECKED BY (SIGN) | DATE |
5.12 | ABBREVIATIONS |
The following Abbreviations are used in the installation qualification protocol of the Air handling unit: QA – Quality Assurance M.O.C – Material of construction SS – Stainless Steel RPM – Revolutions per minute SOP – Standard Operating Processor HOD – Head Of Department PLC – Programmable Logic Controller MMI – Man Machine InterfaceNo-Number RA-Regulatory Affairs HP-Horse power UHMW – Ultra high molecular weight polyethylene OHNS – Oil-hardened non shrinkable |
5.13 | DEFICIENCY AND CORRECTIVE ACTION (S) REPORT (S) |
The following deficiency was identified and corrective actions were taken in consultation with the validation team. | |
Description of deficiency: | |
Corrective action(s) taken: | |
5.14 Annexure(s):
Sr.No. | Annexure No. | Title of Annexure |
6.0 | INSTALLATION QUALIFICATION FINAL REPORT: |
All the IQ data sheets and discrepancy reports shall be reviewed by the validation team to prepare a summary report. The summary of IQ shall be used to draw conclusion for approval of the installation qualification report. |
6.1 | SUMMARY |
6.2 | CONCLUSION |
6.3 FINAL REPORT APPROVAL
It has been verified that all tests required by this protocol are completed, reconciled, and attached to this protocol or included in the qualification summary report. Verified that all amendments and discrepancies are documented, approved, and attached to this protocol.
The signature in the block below indicates that all items in this qualification report of Automatic Single Head Injectable Powder Filling with Rubber stoppering Machine Model (Modal Name) have been reviewed and found to be acceptable and that all variations or discrepancies have been satisfactorily resolved.
NAME | DESIGNATION | DEPARTMENT | SIGNATURE | DATE |
PROJECTS / ENGINEERING | ||||
PRODUCTION | ||||
QUALITY ASSURANCE |

Naresh Bhakar is the Founder and Author at Pharmaguddu.com, bringing his extensive expertise in the field of pharmaceuticals to readers worldwide. He has experience in Pharma manufacturing and has worked with top Pharmaceuticals. He has rich knowledge and provides valuable insights and data through his articles and content on Pharmaguddu.com. For further inquiries or collaborations, please don’t hesitate to reach out via email at [email protected].