The Ribbon Blender is a mixing device that operates on the principle of shear and convective mixing.
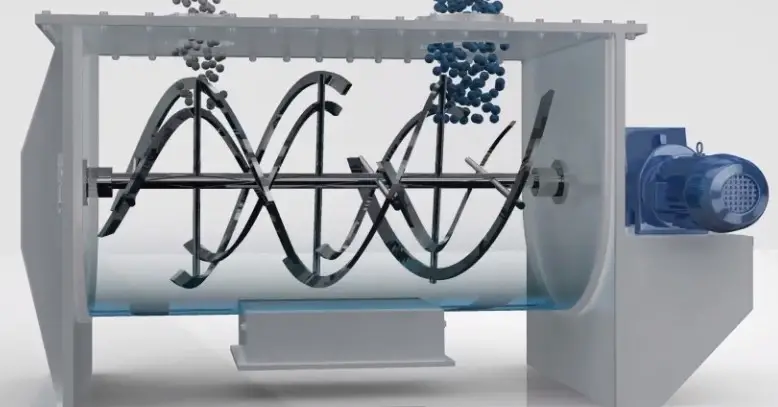
Principles of Ribbon Blenders:
- The mechanism of mixing in a ribbon blender relies on shear forces generated by the movement of blade-like ribbons within a stationary shell.
- This mixing process involves convective movements, which allow the redistribution of solids on a macro scale.
- Convective mixing occurs as the solids are continuously turned over along the horizontal axis of the agitator assembly.
- The effectiveness of ribbon blenders in breaking down lumps and aggregates stems from the application of high shear rates, ultimately achieving a state of equilibrium mixing.
Related: Size Reduction
Construction of Ribbon Blenders:
A ribbon blender consists of a U-shaped horizontal trough or shell that contains a helical double-ribbon agitator rotating inside it. The agitator’s shaft is positioned at the center of the trough, and the helical ribbons (also referred to as spirals) are welded onto it. This type of agitator is known as a “double” helical ribbon agitator because it consists of both internal and external helical ribbons. Counteracting blades are included to provide high shear and break lumps or aggregates.
The ribbon blenders are run by a system that consists of a motor, a gearbox, and couplings. Typically, a 10 HP to 15 HP motor powers them for blending about 800 kg of product mass. The specific power ranges from 3 to 12 kW/m² depending on the products being mixed. To prevent material from escaping the container, a sealing arrangement is implemented at the point where the shaft exits the container. The mixer is typically loaded with the material using feed hoppers and is also equipped with a bottom discharge spout.
Working of Ribbon Blenders:
To blend the materials, load the material into the blender, filling it between 40 and 70 percent of the total volume of the container. The drive system helps the ribbons to rotate. During the blending process, one blade slowly moves the solids in one direction, while the other blade rapidly moves them in the opposite direction. This motion ensures that the materials are thoroughly mixed in a short amount of time, resulting in a homogeneous blend. Typically, the blending operation takes around 15 to 20 minutes. Once the blending is complete, the material is discharged through a spout located at the bottom of the trough.
The efficiency of the ribbon mixer’s mixing process is influenced primarily by the particle size and bulk density of the ingredients. When the ingredients have similar particle sizes and bulk densities, they tend to mix more quickly compared to ingredients that vary in these attributes.
Related: Size Separation
Advantages of Ribbon Blenders:
- Ribbon mixers are a cost saving, and also reduce process time.
- It can blend a wide range of materials with minimal flaws.
- It is valuable for the industries where mixing of materials such as paint, concrete, and food products is required.
- It can also be used in food industries to mix food items.
- Required less space to install.
Disadvantages:
- The movement of particles in the Ribbon Blender is two-dimensional, making it less efficient for mixing compared to a planetary mixer.
- The shearing force is lower than in a planetary mixer.
- Attrition of particles can occur at the wall of the blender due to higher forces.
- Dead spots, especially near the discharge valve and along the central axis, lead to incomplete mixing.
Usage in Pharmaceuticals:
A Ribbon blender is used in the blending process for the large volume solid, semisolid mass.
Ribbon Blenders Varients
The paddle agitator is an alternative design to the ribbon agitator that is capable of handling delicate materials. Unlike the ribbon agitator, the paddle agitator consists of both forward and reverse paddles instead of a ribbon. These paddles are strategically positioned to facilitate movement of the material in lateral directions that oppose each other, as well as in a radial direction.
The paddle agitator is the best alternative to the ribbon agitator, The paddle agitator is used when mixing of friable materials is required, which are prone to breakage or damage. Its paddle arrangement allows for easy movement of the material, making it suitable for blending friable substances and smaller batch sizes, small as 15% of the blender’s total capacity.

Naresh Bhakar is the Founder and Author at Pharmaguddu.com, bringing his extensive expertise in the field of pharmaceuticals to readers worldwide. He has experience in Pharma manufacturing and has worked with top Pharmaceuticals. He has rich knowledge and provides valuable insights and data through his articles and content on Pharmaguddu.com. For further inquiries or collaborations, please don’t hesitate to reach out via email at [email protected].