1.0 Purpose: To lay down the procedure for cleaning and preparation and packing of material for sterilization.
2.0 Applicable: This Standard Operating Procedure is applicable to the cleaning, preparation, and of packing of material for sterilization on the production floor.
3.0 Responsibility: 3.1 The operators who are trained in cleaning processes shall carry out the cleaning process of materials.
3.2 officers/executives shall supervise the process.
3.3 Production Manager shall be responsible for the implementation of SOP.
3.4 Head-Quality Assurance/designee shall be responsible for compliance with SOP.
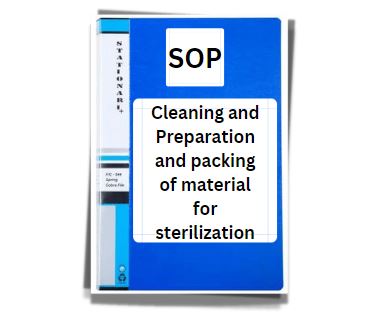
4.0 Procedure for Cleaning and Preparation and Packing of Material for Sterilization:
4.1 Cleaning, preparation, and packing of filling accessories:
4.1.1 Cleaning of filling accessories:
4.1.1.1 As per SOP “Cleaning accessories for sterilization“.
4.1.2 Preparation of filling accessories:
4.1.2.1 Place the material under LAF in Room.
4.1.2.2 Wrap the open ends of needles, and pistons manifold with the help of breathing paper.
4.1.2.3 Attach clamps to the product tank tightly.
4.1.2.4 Attach 0.2 µ air vent filter with the help of a silicone tube to open the ends of the product tank.
4.1.2.5 Prepare sampling bottles with siphon assemblies and ensure any kind of leakage.
4.1.3 Packing of filling accessories:
4.1.3.1 Pack each item individually in steri pack with the help of a pouch sealing machine as per SOP “Pouch sealing machine“.
4.1.3.2 Make sure that all material is sealed properly in steri pack.
4.1.3.3 If the material is not sterilized within 48 hours of its preparation then give rinsing a single time with hot WFI to the material before its sterilization.
4.1.3.4 After completion of material preparation, start the validated sterilization cycle.
4.1.3.5 If the accessory is not sterilized within 48 hours of the cleaning follow the washing procedure again with hot WFI.
4.1.3.6 Use the sterilized material within 48 hours (2 days) either the material should be sent back for repacking & resterilization.
4.2 Cleaning, preparation, and packing of formulation and solution preparation load:
4.2.1 Cleaning of formulation and solution preparation load:
4.2.1.1 As per the cleaning procedure
4.2.2 Preparation of formulation and solution preparation load:
4.2.2.1 Take the material under LAF in the room for the preparation.
4.2.2.2 Attach the cleaned siphon assemblies to the glass bottles. Along with 0.2-micron air vent filters.
4.2.2.3 Ensure the tubing is for any leakages.
4.2.3 Packing of formulation and solution preparation load:
4.2.3.1 Pack each item individually in a steri pack with the help of a pouch sealing machine.
4.2.3.2 Ensure that packing is sealed properly.
4.2.3.3 After completion of material preparation starts the validated sterilization cycle.
4.2.3.4 If the accessory is not sterilized within 48 hours of the cleaning follow the washing procedure again with hot WFI.
4.2.3.5 Use the sterilized material within 48 hours (2 days) either the material should be sent back for repacking & resterilization.
4.3 Cleaning and preparation of Rutten’s vessel:
4.3.1 Cleaning:
4.3.1.1 Clean as per cleaning procedure.
4.3.2 Preparation:
4.3.2.1 Provide connection to the addition and transfer port of vessel with Y connection.
4.3.2.2 Ensure the vessel is for any kind of leakage and put the vessel on pressure hold.
4.3.2.3 Ensure the proper O rings, and gaskets if leakages are observed.
4.3.2.4 Ensure the ambient temperature of the vessel before putting in pressure hold test.
4.3.2.5 Ensure that the gauge is calibrated.
4.3.2.6 Apply 1 kg pressure to the vessel and put it on hold for 30 minutes if the pressure withstands for the time period then it is ok the acceptance limit for the leakage is 0.1 bars.
4.3.2.7 If the vessel is not sterilized within 48 hours of the cleaning follow the washing procedure again with hot WFI.
4.3.2.8 After completion of material preparation starts the validated sterilization cycle.
4.3.2.9 Use the sterilized material within 48 hours (2 days) either the material should be sent back for repacking & resterilization.
4.4 Cleaning of disinfectant load for sterilization:
4.4.1 Take the disinfectant material to the wash area.
4.4.2 Paste status label “to be cleaned” as per SOP on “status labeling“.
4.4.3 Give first wash to the nalgen bottle & empty the S.S. bucket with high-pressure purified water.
4.4.4 Then give second washing with hot WFI.
4.4.5 Clean the filter housing of disinfectant filtration by passing 5-6 Ltr of hot WFI.
4.4.6 Wash other accessories such as tubing, forceps, and clamps first with purified water followed by final washing with hot WFI.
4.4.7 After completion of material preparation starts the validated sterilization cycle.
4.4.8 Use the sterilized material within 48 hours (2 days) either the material should be sent back repack & resterilization.
4.5 Packing of clean Room dress:
4.5.1 Packing of clean room dress done as per SOP “sterilization of clean room dress“.
4.5.2 After completion of material preparation starts the validated sterilization cycle.
4.5.3 Use the sterilized material within 48 hours (2 days) either the material should be sent back for repacking & resterilization.
5.0 Abbreviations:
ID No. : Identification number
No. : Number
QA: Quality Assurance
SOP: Standard Operating Procedure
TOC: Total Organic Carbon
LAF: Laminar Air Flow
WFI: Water For Injection
QC: Quality Control
DPB: Dynamic Pass Box

Naresh Bhakar is the Founder and Author at Pharmaguddu.com, bringing his extensive expertise in the field of pharmaceuticals to readers worldwide. He has experience in Pharma manufacturing and has worked with top Pharmaceuticals. He has rich knowledge and provides valuable insights and data through his articles and content on Pharmaguddu.com. For further inquiries or collaborations, please don’t hesitate to reach out via email at [email protected].