Isolator in pharmaceuticals has a significant place in the production of sterile products because of their decontaminated environment. They meet Grade A conditions and provide continuous isolation from its interior to the external environment.
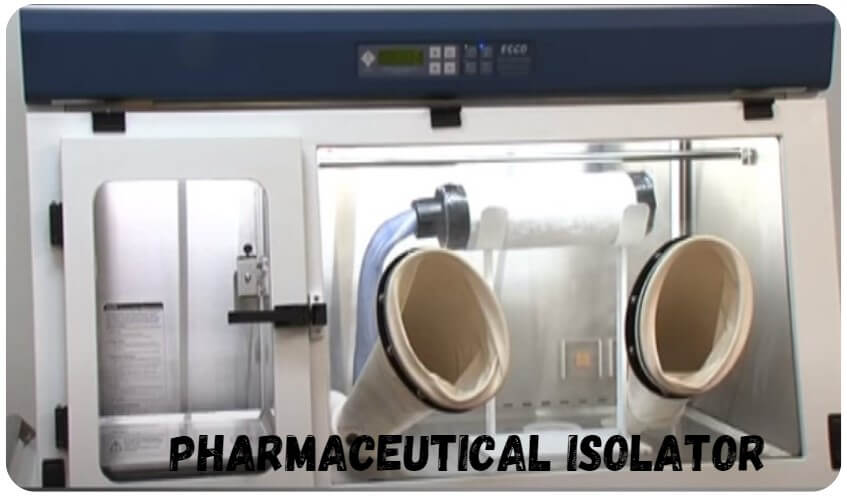
The Evolution of Aseptic Processing
If we talk about their Journey, aseptic processing has been quite interesting, taking us from traditional class 100 clean rooms to modern isolators. Traditional clean rooms were widely used from the 1950s to the 80s. However, due to their limitations, a new system comes into play named Restricted Access Barrier Systems (RABS) which is more significant than the old one.
Introduction of Isolator
The origin of isolators in the early 1980s was one more step for aseptic processing. They are starting primarily as sterility test chambers, their successful use in preventing false positives is shown by their introduction and acceptance into aseptic processing. Today, isolators are widely used to control areas and minimize the risk of contamination.
Restricted Access Barrier Systems (RABS)
However, isolators are more effective than RABS which helps to minimize contamination and cross-contamination in the manufacturing area. RABS is of two types, open and closed RABS. Read more about RABS by clicking here.
Comparing Isolators, Traditional Clean Rooms, and RABS
Comparing the three, isolators stand out due to several advantages. One of them is the process of sterile gowning, which is required in traditional clean rooms and RABS. Now it is simplified for isolator operators. Isolators also make sanitization more effective and reliable. In comparison to the 3-4 log reduction achieved with wet chemical sanitizers in clean rooms and RABS, isolators achieve greater than 6 log reduction due to their use of gaseous sanitizers.
Isolators Classification
Isolators can be classified based on their barrier type, size, and function. Their types include closed and open isolators, single-chamber isolators, multi-chamber isolators, and isolators integrated with other equipment like autoclaves and lyophilizers.
Sanitization and Disinfection in Isolators
Isolators can be sealed and sanitized using a gas or vapor, which leads to a high level of disinfection. Gaseous vapor sanitizers, such as hydrogen peroxide, ethylene oxide, nitrogen dioxide, and chlorine dioxide, are commonly used in isolators. Hydrogen peroxide is the most commonly used sanitizer in pharmaceutical isolators today.
How Sanitizers Work
All sanitizers work by oxidizing proteins, nucleic acids, nucleotides, and other biomolecules, leading to cell death. Gaseous vapor sanitizers have a significant advantage over traditional clean rooms with wet chemical sanitizers, as they provide a 6-log reduction in bioburden compared to a 3 to 4-log reduction in traditional clean rooms. The gaseous vapor phase affects all exposed surfaces and is not dependent on the cleaning operator’s performance.
The VHP Process
Vaporized hydrogen peroxide is produced from liquid hydrogen peroxide, which is heated to evaporate the hydrogen peroxide and water. In the isolator chamber, the hydrogen peroxide and water are in equilibrium between the gaseous and liquid phases. The temperature and humidity levels in the chamber affect the distribution of hydrogen peroxide. Visual condensation should be avoided, as it can affect the control of the VHP process.
VHP Cycle
The VHP cycle in isolators consists of a total of four phases: Dehumidification, conditioning, decontamination, and aeration. During the process of De-Humidification temperature and humidity levels shall be maintained. Next, Conditioning is done for rapid diffusion of hydrogen peroxide to achieve high levels of sanitization. Next, Decontamination maintains the high level of VHP for a fixed time period, and Last, aeration is done to remove the VHP to safe levels. The cycle should be carefully controlled to ensure effective sanitization and aeration.
Validation of VHP Cycles:
At BSM, we only use dry VHP and have discovered that 700 to 1000 PPMs of vapor hydrogen peroxide are needed for 30 to 50 minutes to get a 6-log reduction of geobacillus. It was also noted that the closer the relative humidity is to 100%, the faster the kill. Bi should be placed in warmer locations, which are usually near where the vaporized hydrogen peroxide enters the chamber.
Advantages of Vapor Hydrogen Peroxide
Vapor hydrogen peroxide is used as a sanitizer in isolators due to its availability, use, and compatibility with many materials. It breaks down into water and oxygen, leaving no residues after sanitization and aeration. Hydrogen peroxide is also less toxic than many other sanitizing agents.
Isolator Guidelines
Isolator chambers should be compatible with and non-absorptive to hydrogen peroxide. They should be appropriately sized for the equipment and materials, operation, and easy to clean and pre-sanitize. The majority of pharma isolators are made of stainless steel (316 and 316L) and glass. Pharmaceutical industry Isolators must comply with the class A Standards as outlined in the EU GMP Classification of 07/01/97 (Source1).
Different Parts of Pharmaceutical Isolators:
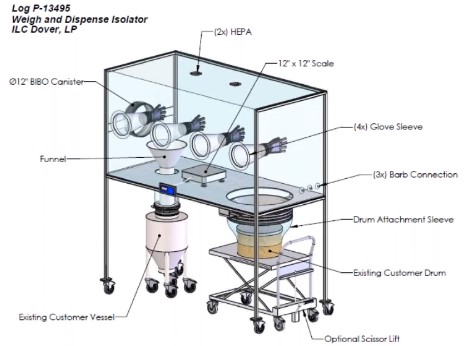
Gloves and Glove Ports
Gloves and glove ports in isolators are important parts of maintaining aseptic conditions inside the chamber. Gloves and glove ports should be installed to prevent glove integrity failures, chemical incompatibility, and long aeration times. Glove integrity tests should be performed before and after every activity in a filling isolator. Gloves should be compatible with the glove ports and fully extended without folds. Sterile gloves must be used inside the isolator gloves port.
Openings (Mouse Holes)
Openings, also known as mouse holes, are necessary for the ingress and egress of components and products in isolators. They should be sealed during sanitization and aeration processes. Active and passive mouse holes are used, and additional measures should be taken to protect the mouse holes from external contamination.
Airflow system
Isolators require a laminar flow or unidirectional airflow from the top to the bottom of the chamber. Turbulent flow can be accepted in closed isolators that are compact and do not house processing lines. Air can be recirculated through a plenum or have 100% exhaust and make-up air. The airflow should be carefully controlled to maintain pressure and temperature levels.
Vaporizers
Vaporizers are used to produce vaporized hydrogen peroxide in isolators. They heat liquid hydrogen peroxide to evaporate the hydrogen peroxide and water.
HVAC System
Fans direct air through HEPA filters: Recirculate air through a plenum with some exhaust and makeup air Or 100% exhaust, 100% makeup air
Unidirectional vs turbulent flow: Turbulent airflow is acceptable in some cases by some regulatory authorities.
ex. FDA “Turbulent flow can be acceptable within closed isolators, which are normally compact in size and do not house processing lines” — ex. sterility isolators.
Surface Monitoring and Glove Integrity Tests
Surface monitoring must be done at the end of an operation and before opening the isolator while making sure to check gloves, and critical surfaces such as fill needles, inside stoppers, and other critical areas. Glove integrity tests also have an important role in this process.
Understanding Environmental Monitoring
Environmental monitoring is very important to perform at various locations during operation. The plates that you use should be validated for exposure to VHP. Our suggestion to effectively use these plates involves hanging them inside your isolator to ensure the outside of the wrappings is decontaminated before you open them to use.
However, to ensure the effectiveness of the plates, a validation process is mandatory to verify that they didn’t absorb excessive vapor hydrogen peroxide which might lead to false negative results. After digging deeper into the issue, it was found that plates should be placed in sterile containers before taking them out of the isolator to avoid contamination.
A disturbing period witnessed positive hits inside the isolator, and two potential sources were identified. The problem seemed to vanish once we placed the plates in sterile containers before they were passed out of the isolator.
Application of Isolators:
- It helps to prevent contaminants.
- Easy for product transfer by using an exit port without interfering with the external environment.
- It is useful for handling, filling, sampling, and transferring solid, liquid, semi-solid, and powder materials.
Advantage:
- It provides a sterile environment.
- Positive and Negative pressure inside the chamber prevents contamination from external environments and working persons.
- It allows to control the of various parameters like temperature, RH, and Pressure.
- Lower cost, easy to operate, and maintenance.
- Isolator Requires less space to install.
Conclusion
To conclude, For example, if you were to buy a Phone, you wouldn’t opt for 10-year-old technology, but instead, go for the most advanced features the present day has to offer. Similarly, when it comes to choosing an isolator supplier, opt for the most modern technologies.
In essence, much like you wouldn’t buy an outdated clean room or RABs to produce your sterile product, you shouldn’t when a much more technologically advanced option exists.
Frequently Asked Questions
Ans. Isolators vary based on their barrier type, size, and function. They can be closed or open, single-chamber or multi-chamber, and can also be integrated with other equipment such as autoclaves and lyophilizers.
Ans. Open RABS have doors that can be opened for operators to lean in and work on the system inside. However, closed RABS, the doors remain largely closed throughout the entire process.
Ans. VHP or Vapor Hydrogen Peroxide is used in BSM for sterilization purposes. The validation process involves the use of this chemical to clean and validate the plates used in the isolator.