Learn About SOP of SOP (How to Write SOP by implementing Different Fonts, Size, Title, Logo, Stamps, Formats, BMR/ BPR, Spec/STP, protocols, Worksheets, Reports, and Logbooks, and Annexures as per the Pharmaceutical Guidelines).
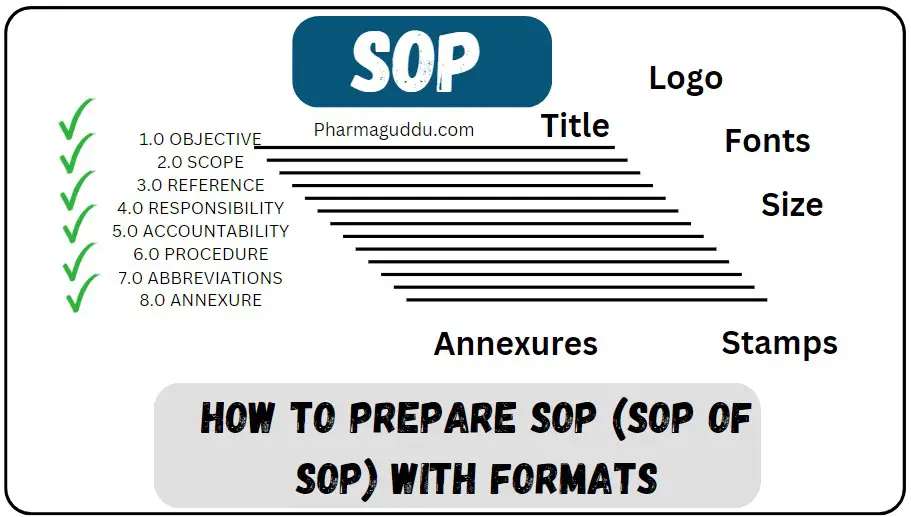
1.0 OBJECTIVE: 1.1 To lay down the procedure for the preparation of SOP (SOP on SOP), Format, Numbering, Review, Approval, Implementation, Distribution, Retrieval, and Control of Standard Operating Procedures.
1.2 This Standard Operating Procedure (SOP) describes how to prepare detailed written instructions that specify how an operation or administrative procedure is to be performed.
2.0 SCOPE: 2.1 This procedure applies to all related departments of XYZ Pharmaceuticals.
2.2 This SOP also describes the Issuance, Control, Distribution, Revision, Retrieval of SOP and Destruction of Obsolete / Cancelled SOPs.
2.3 This SOP also describes stamping details for SOPs, Formats, BMR/ BPR, Spec/STP, protocols, Worksheets, Reports, and Logbooks.
3.0 REFERENCE:
3.1 Inhouse.
4.0 RESPONSIBILITY:
4.1 All the Department Heads/Designees in-charges shall be responsible for the Preparation of SOPs for all operations, equipment, and activities related to their department.
4.2 All Heads/Designee of the departments and Head Quality Assurance shall hold overall responsibility for the implementation of the SOPs.
4.3 All the company personnel shall be familiar with this procedure & follow the SOPs about their area of work.
4.4 The head of the originating department/ approver shall ensure that all proposed SOPs are confirmed to this SOP while reviewing any SOP.
4.5 The approvers of the SOP Shall verify the conformity of the Contents with the cGMP and regulatory requirements wherever applicable.
5.0 ACCOUNTABILITY:
5.1 Head-QA/Designee: Approval, ensure Training and effective implementation of SOPs. Ensure the availability of hard copies of all Master copies.
6.0 PROCEDURE for SOP of SOP:
The following sections explain How to prepare SOP.
6.1 The person who performs the activity/ supervises the activity in consultation with the Department Head or after a group discussion on the matter shall prepare an SOP. All the SOPs are to be generated by computer with MS-WORD in the Format known as “Standard Operating Procedure” (Annexure – I below).
6.2 It is recommended (But not limited to) that all the characters of SOP text matter shall be in “Times New Roman” and with font size ‘12’. All the characters in the SOP Header shall be in “Times New Roman” uppercase letters and the Footer shall be in “Times New Roman” Title case with font size ‘12’. The title of SOP shall be in Font size ‘12’.
6.3 Every new SOP shall be prepared with the watermark “Draft copy” & reviewed by the concerned department Head/Designee along with QA & corrections should be made on the same. All such drafts shall be destroyed immediately after the final printing of the SOP & subsequent sign-off.
6.4 Assignment of SOP numbers:
6.4.1 Each SOP shall be assigned with a unique number. This number shall consist of fourteen characters. E.g. PGDC/XX/001/00.
6.4.2 The first four characters are “PGDC” in the English alphabet denote the name of the Company For Example (Pharmaguddu Dot Com). These four alphabets will be common for all SOP numbers on the premises.
6.4.3 The next character is “/ ” Slash.
6.4.4 The next two Characters “XX” is an abbreviation for various departments. The abbreviations for each department are as follows:
6.4.4.1 SR: Store (Raw Material)
6.4.4.2 SP: Store (Packing Material)
6.4.4.3 PG: Production (Granulation)
6.4.4.4 PR: Production (Compression)
6.4.4.5 PC: Production (Coating)
6.4.4.6 CM: Capsule Manufacturing
6.4.4.7 OL: Oral Liquid Manufacturing
6.4.4.8 PP: Production (Packing)
6.4.4.9 QA: Quality Assurance
6.4.4.10 QC: Quality Control (Micro-QM, QC Packing material-PM)
6.4.4.11 FG: Finished Goods Store
6.4.4.12 EN: Engineering & Maintenance
6.4.4.13 HR: Human Resources
6.4.4.14 IT: Information Technology
6.4.4.15 PPIC: Production Planning and Inventory Control
6.4.5 The next Character is “/” Slash.
6.4.6 The next three characters are serial numbers of the SOP starting from 001 in sequential order within the department.
6.4.7 The next character is “/” Slash.
6.4.8 The last two characters denote the revision number of SOP. The first time any SOP is written, it shall be numbered as “00”. The first revision of SOP shall be numbered as “01” and so on. For Example, This First SOP prepared as per this procedure for the Quality Assurance Department shall be numbered as “PGDC/QA/001/00” and the same when revised for the first time shall be numbered as “PGDC/QA/001/01”.
Note: a) All the SOPs prepared, and reviewed as per this procedure shall be mentioned as the “00” version. The previous SOP and version number will be mentioned in the change details.
b) In case of change in any SOP, SOP change via change control & SOPs generated as per this procedure will mention only “The Changes” made from the “Existing Version” of the respective SOP.
c) While referring to the SOP No. in other related documents indicate only SOP No. and, do not mention version No.
d) Department Head & Head – QA shall ensure circulation of the current version of SOPs.
6.5 The following are the parameters of the A4 size paper setup.
Paper Size | A4 (8.4” X 11.88”) | |
Paper Margin | Top 0.5” | Bottom 0.5” |
Left 0.5” | Right 0.5” | |
Header & Footer Margin | Header 0.5” | |
Footer 0.5” |
6.6 The following information shall appear in the “Header” of the SOP format:
XYZ Company with Address | ||
SUBJECT: STANDARD OPERATING PROCEDURE | PAGE NO.: 1/1 | |
DEPARTMENT: | SOP. NO.: PGDC/XX/001/00 | SUPERSEDES EARLIER PROCEDURE DATE: DD/MM/YYYY |
EFFECTIVE DATE: | REVIEW DATE: | |
TITLE: |
6.6.1 Title:
6.6.1.1 Give the detailed heading specific to the operation of the SOP.
Example: Procedure for preparation of Format, Numbering, Review, Approval, Implementation, Distribution, Retrieval and Control of Standard Operating Procedure.
6.6.2 Department: All sections should be written in their department section as:
6.6.2.1 The department should be written as:
i) Production.
ii) Quality control.
iii) Quality Assurance.
iv) Human Resources.
v) Warehouse.
vi) Engineering.
vii) Information and technology.
viii) Production Planning and Inventory Control.
6.6.3 SOP No.:
6.6.3.1 As per 6.4.
6.6.4 Effective date
6.6.4.1 The effective date is when the contents of the SOP become operative, after training the concerned personnel on the SOP. The effective date shall be written in green ink pen by the Head-QA/ his designated representative.
Note: Sufficient time shall be allowed on the effective date to facilitate training of the concerned personnel and to procure any required material as the case may be. In practice, 7 days after sign-off except for special cases is considered a period for training.
Relevant SOP training shall be documented in the SOP training record & assessment given on the training assesses record.
QA Personnel will write The effective date with a green ink pen when the training is complete and the SOP comes into effect.
6.6.5 Review date.
6.6.5.1 All SOPs shall be reviewed in 3 years ± 15 days from the effective date. The review date shall be written in green ink pen by QA Personnel.
6.6.6 Page No.
6.6.6.1 Each page of the SOP shall have a specific page number as well as the total number of pages. The Standard Operating Procedure comprises of Example:
X Of Y
Where X denotes Page No.
Y Denotes= Total no of pages.
6.7 The following information shall appear in the “Footer” of the SOP format:
Prepared By | Checked By | Approved By | Authorized By | |
Name | ||||
Design. / Dept. | ||||
Sign / Date |
6.7.1 Prepared by:
6.7.1.1 The personnel supervising the activity/operation, or who is directly involved in the procedure of the respective user department shall sign as “Prepared by” with date.
6.7.2 Checked by:
6.7.2.1 The department Head/functional head of the user department shall verify the adequacy of the procedure and shall sign in the first column as “Checked by” with a date.
6.7.3 Approved by:
6.7.3.1 The designated representative of Head-QA/Designee who ensures the GMP / regulatory compliance of the procedure, shall sign in as “Approved by” with the date.
6.7.4 Authorized by:
6.7.4.1 All The SOPs of the site should be authorized by the Plant Head and shall be signed as “Authorized by” with sign/date.
6.7.5 Format number:
6.7.5.1 Format number of SOP format shall be mentioned on the left bottom below the signatory, i.e. F/QA/001/A/XX.
6.7.5.2 XX indicates for revision number of the format.
6.8 Contents of the Standard Operating Procedure:
6.8.1 Each SOP shall have information under the following subtitles.
6.8.1.1 The title page of the final print of SOP will have the following information.
6.8.1.1.1 Change history details: It shall include the following information arranged as a table consisting of 3 columns and 3 rows.
6.8.1.1.1.1 SUPERSEDE SOP No.: The SOP No. of superseded SOP.
6.8.1.1.1.2 CCR No.: The updated CCR No. through which the procedure is changed.
6.8.1.1.1.3 REASON FOR REVISION: Summary of the ‘Reason’ for Revision.
Note: In case of a new SOP all the columns shall be defined as –. All the characters of the table shall be “Times New Roman bold” and with font size ‘12’. with supersede should be written as “NIL” then in CCR NO the change control number that is been taken and in the reason for revision column it should be mentioned as “New SOP”.
6.8.1.2 OBJECTIVE:
6.8.1.2.1 An overview of the SOP shall be briefly mentioned here.
6.8.1.2.2 This shall include the purpose of the procedure (Viz., Why the procedure is written)
6.8.1.3 SCOPE:
6.8.1.3.1 This Section defines the applicability of the SOP and also specifies Departments, areas, or sections to which this SOP shall be applicable.
6.8.1.3.2 This shall involve an area of application of the procedure (Viz., Where the procedure is required to be performed).
6.8.1.4 REFERENCE:
6.8.1.4.1 Shall specify the reference guidelines or in-house references for concern SOP.
6.8.1.5 RESPONSIBILITY:
6.8.1.5.1 Shall specify the personnel responsible for ensuring the implementation and compliance. (Viz., who performs the procedure, and who is responsible for seeing it is performed correctly.)
6.8.1.6 ACCOUNTABILITY:
6.8.1.6.1 Specify the person who is directly associated with the output.
6.8.1.7 PROCEDURE:
6.8.1.7.1 There should be specific instructions for each step in sequential order including the preparatory work, which must be done before starting the main procedure, as well as instructions for recording and reporting the results.
6.8.1.7.2 Clear concise, step-by-step instructions on how to perform the procedure. This should be written as instructions for the operator to follow, without a lot of theoretical background. A section on fundamental principles can be included if necessary, as below:
6.8.1.7.2.1 Preliminary steps that must be done before beginning the actual procedure.
6.8.1.7.2.2 Safety considerations: Precautions for work with physical, chemical, or biological hazards (containment facility, clothing, masks, hoods, goggles, gloves, cleanup of spills, etc.).
6.8.1.7.2.3 Each SOP shall follow sequenced chronological instructions. In case of repetition of the instruction(s) refer to the specific step no. (s) Of the related instruction (s).
6.8.1.7.2.4 Calculations: Explanations and samples of how to do any required calculations.
6.8.1.8 ABBREVIATION:
6.8.1.8.1 List out all the abbreviations used in the SOPs and their Elaboration.
6.8.1.9 ANNEXURE:
6.8.1.9.1 Documentation: Formats as per SOP.
6.8.1.9.1.1 Where appropriate, suitable documentation shall be developed to indicate either or all of the following Indicate the tolerance/ accuracy limits, as applicable.
6.8.1.9.1.1.1 The Person(s) responsible are doer and reviewer.
6.8.1.9.1.1.2 This form shall be a parallel summary document with a checklist, checkboxes, and blanks for all data to be recorded during the performance of the procedure.
6.8.1.9.1.1.3 It also shall have spaces for the signatures of the operator and other technicians who verify and countersign certain critical operations during the procedure.
6.8.1.9.1.1.4 Finally, there shall be spaces for the signature of the department supervisor who reviews the completed data record form.
6.8.1.9.1.1.5 Such blanks and checklists shall ensure that the required data are collected, that nothing is overlooked, and also provide evidence that the procedure was performed according to the SOP. This can be achieved by using counter-checking methods or by enclosing the printouts of equipment operations wherever applicable. When appropriate in all SOPs, wherever applicable, the format shall be attached as Annexure. In such case, the Annexure should have.
6.8.1.9.1.1.6 Title of the format.
6.8.1.9.1.1.7 The main subject points of format shall be typed in Capitals and boldface while the rest of the text is typed in regular font.
6.8.1.9.1.1.8 The formats attached to the master shall also be stamped as “Master Copy”. Stamp on each page of the format.
6.8.1.9.1.1.9 Distribute all such Annexures along with a controlled copy of SOP after ensuring the “Controlled Copy” stamp on each page of the format(s).
6.8.1.10 Format Numbering system:
6.8.1.10.1 Each format shall be identified with a number.
6.8.1.10.2 This number shall consist of 13 characters.
6.8.1.10.3 The first character “F” represents the Format. This alphabet shall be common for all formats.
6.8.1.10.4 The next character is “/” Slash.
6.8.1.10.5 The next two characters “XX” represent the dept. as mentioned in 6.4.4.
6.8.1.10.6 The fifth character is “/” Slash.
6.8.1.10.7 The next three characters “001” denotes the serial number of the SOP to which the format belongs.
6.8.1.10.8 The next character is “/” Slash.
6.8.1.10.9 The tenth character is “Y” represents the number of formats as A for the first format, B for the second format, C for the third format & so on for the respective SOP. If format no. exceed to 26 as “Z” then the 27th format indicated as “AA”, next BB & so on.
6.8.1.10.10 The eleventh character is “/” Slash.
6.8.1.10.11 The last two characters denote the revision number of the respective format.
6.8.1.10.12 For example F/QA/001/A/00 is the first format, made the first time, and relates to the first SOP of the QA department.
6.8.1.10.13 QA will assign the format number and make the department-wise list of formats with respective numbers.
6.8.1.10.14 Format number shall appear on the bottom left-hand side of each page of the format.
6.8.2 Distribution and Issue Control:
6.8.2.1 All original signed copies of SOPs in standard A4 size with stamped across as “Master Copy” (Ref annexure-VI) in Red ink at the top right-hand corners of all the pages of the SOP and shall be archived in the Quality Assurance department. For References Copy take a photo state copy of “Master SOP” and then first put the “Controlled copy’’ stamp in blue ink on the bottom left-hand side corner of all pages of SOP and then put “Copy no” “QA Sign” and “Date” stamp in blue ink at the bottom middle of all pages of SOPs and is issued to respective departments for reference copy.
6.8.2.2 For Display purposes Photostate of “Master Copy” shall be taken on plain A4 size paper, put the “Controlled Copy” stamp in blue ink on each page’s bottom left-hand corners and then put “SOP DISPLAY” “COPY NO” “Sign” and “Date” (Ref: Appendix) in blue ink at bottom right-hand corners of all the pages of SOP and distribute to the department heads.
6.8.2.3 The daily monitoring formats and other formats to the different user departments shall be distributed by taking without Annexure number of the Master copy format with., QA Sign and date shall be stamped with “Issued by QA”, “Sign” and “Date” in blue ink at the right side bottom corner on the first page and controlled copy stamp on each page on bottom left-hand corners.
6.8.2.4 In the case of BMR/BPR QA personnel shall put a stamp of “MASTER COPY” in red ink on the top right corner of each page and then take a photocopy of that master copy and put the “CONTROLLED COPY” stamp in blue ink on the bottom left-hand corner of each page and shall be executed for BPR and BMR.
6.8.2.5 In case of worksheets/Protocols/Reports put the “MASTER COPY” stamp on each page and take a photocopy and put the “CONTROLLED COPY” stamp on the left corner of each page and “Issued by QA” “sign….date…” in blue ink on the front of Right Side at the bottom of the first page. In the case of SPEC/STP put the “MASTER COPY” stamp on the top right corner of each page and then take a photocopy and put the “CONTROLLED COPY” stamp on the bottom left-hand corner of each page and “COPY NO SIGN…DATE….” in blue ink on the bottom center of each page.
6.8.2.6 For issuing of bounded log book use blue ink stamp on the back side of overleaf/First page/ Before First page. (Ensure that each page must be available with numbering in the logbook.
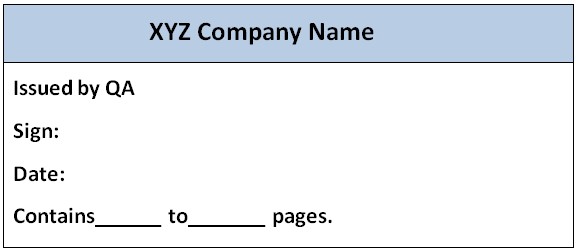
6.8.2.7 Department head to indent the number of copies/ requirement for department reference, user point display, and other file copies, as applicable.
6.8.2.8 Document the controlled copy issue as per “SOP Issue and Reconciliation Format” (Ref: Annexure-II Below)
6.8.2.9 If the need arises for an additional copy of SOP, the concerned Head of the Department shall request the Head of the Quality Assurance Department. Any SOP issued for non-operational use shall be Xerox of “Master Copy” and stamped as “Uncontrolled Copy” (Ref: Appendix) in Red ink on the bottom left corner of every page.
6.8.1.10 Maintain a current index of SOPs of all the departments as per the “SOP Master Index” (Ref: Annexure-III Below) with the current version number. Changes in SOP version No. shall be addressed and the master index shall be maintained when required.
6.8.1.11 In case of technology transfer (manufactured at another location) if any document is demanded, the document is stamped as “MASTER COPY” and then put as a controlled copy stamp if it is required in the company premises and put uncontrolled copy if it is sent outside the company premises for data entry & execution purpose.
6.9 Initiation of new SOP:
6.9.1 Equipment-related SOPs:
6.9.1.1 Equipment-related SOPs should be identified during the Installation Qualification stage.
6.9.1.2 Before the Operation Qualification stage the SOPs shall be prepared, reviewed, and the related operating and supervising personnel shall be trained.
6.9.1.3 The equipment-related SOPs should be inclusive as applicable, of the following:
6.9.1.3.1 Operating Procedure of the Equipment.
6.9.1.3.2 Cleaning Procedure of the Equipment.
6.9.1.3.3 Preventive Maintenance Procedure of the equipment and Calibration procedure.
6.10 Review Procedure for SOP:
6.10.1 The concerned personnel and the head of the department shall review all SOPs once every three years. If any change in the existing SOP during the review follow SOP no. (Title: Change control).
6.10.2 Whenever the SOP is reviewed, the changes made shall be entered on the “SOP Change History”.
6.10.3 The reviewed and approved SOP shall be effective after the training of concerned personnel.
6.10.4 In case if there are no changes required in the existing SOP during the review, the same shall be mentioned in the SOP change history as “Reviewed, No changes are required” and shall be valid for the next three years.
6.10.5 However in such cases the revision number shall be incremented and shall take a new “Review date” and “Effective date” (SOP training may not be applicable to such cases).
6.10.6 Retrieve the copies of old user copies of SOP in circulation, and destroy them after reconciliation. The Quality Assurance officer/Executive shall ensure the reconciliation & destruction and document the same in “SOP Issue and Reconciliation Format” (Ref: Annexure–II Below).
6.10.7 Destroy such retrieved user copies by shredding or by incineration.
6.10.8 The superseded Master Copy shall be stamped as “Obsolete – for Reference only” (Ref: Appendix Below) in Red ink at the bottom center of each page of the SOP and archived along with the Change control form in Quality Assurance.
6.10.9 In case of cancellation of any SOP, withdraw the controlled copies from the individual departments, retrieve & destroy them. “Master copy” shall be stamped with “Obsolete – for Reference only” in Red color at the bottom center of each page of the SOP along with Change control.
6.10.10 The canceled SOP number is not to be assigned to another SOP, & index shall be updated as obsolete for the same.
6.11 Training
6.11.1 Give / in training to the person(s) directly involved in the activity and to the concerned supervisor in charge.
6.11.2 The department head is to conduct the training and forward it to the Quality Assurance for evaluation by Quality Assurance. Head-Quality Assurance / designated representative shall evaluate training and after satisfaction to indicate the effective date in green ink on the master copy of the SOP.
6.11.3 In case if SOP has been changed for updation and there are no changes in annexures then there is no need to revise the annexures.
6.12 End of document:
6.12.1 Type “END OF DOCUMENT” in bold capitals with a font size of 12 at the end of the procedure.
7.0 ABBREVIATIONS:
SOP | Standard Operating Procedure |
cGMP | Current Good Manufacturing Practice |
QA | Quality Assurance |
8.0 ANNEXURE:
Annexure-I | Standard Format for Standard Operating Procedure. |
Annexure-II | SOP Issue and Reconciliation Format. |
Annexure-III | SOP Master Index. |
Annexure-IV | SOP Review Comment Report Obsolete. |
Annexure-V | SOP TRAINING RECORD Obsolete. |
Annexure-VI | Training access record Obsolete. |
Annexure-VII | Stamp Specimen. |
Appendix -VIII | Specimen Stamps. |
…………..END OF DOCUMENT…………..

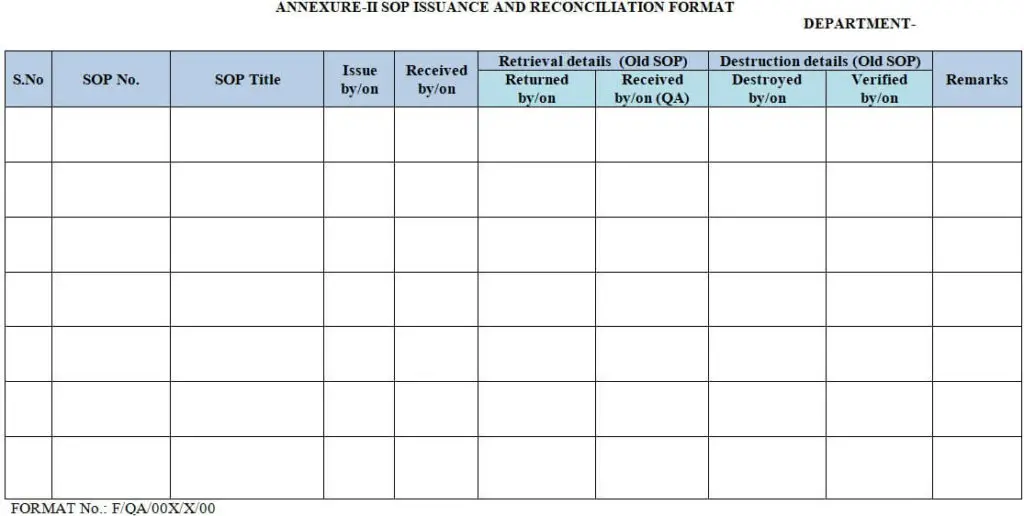
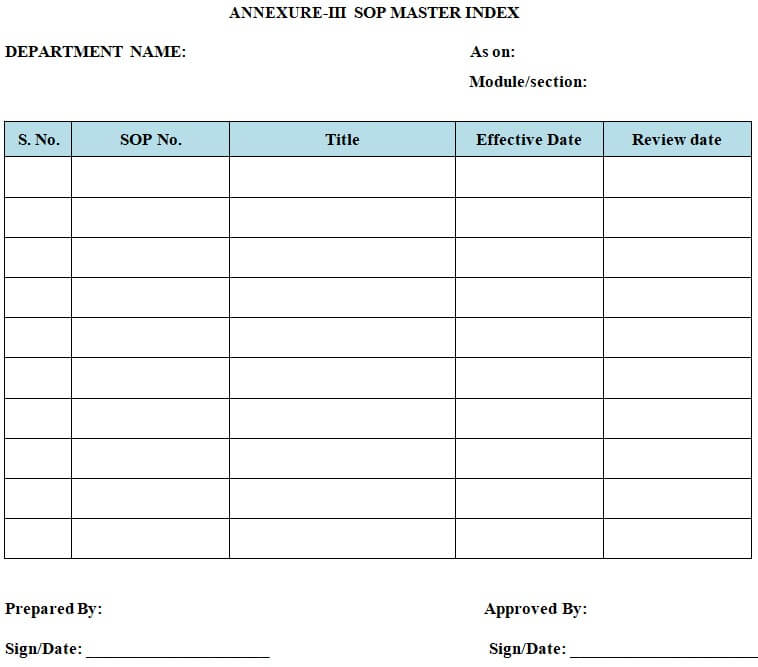
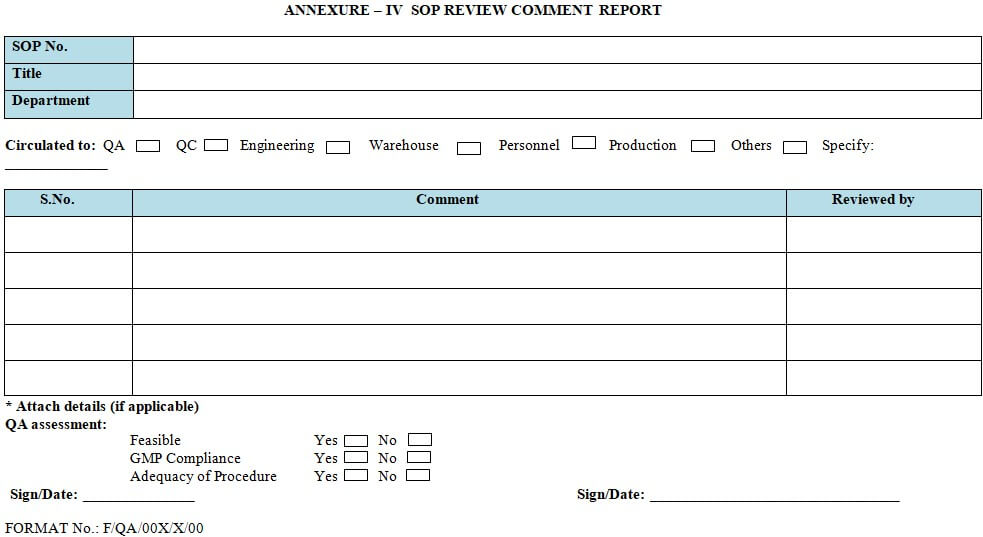
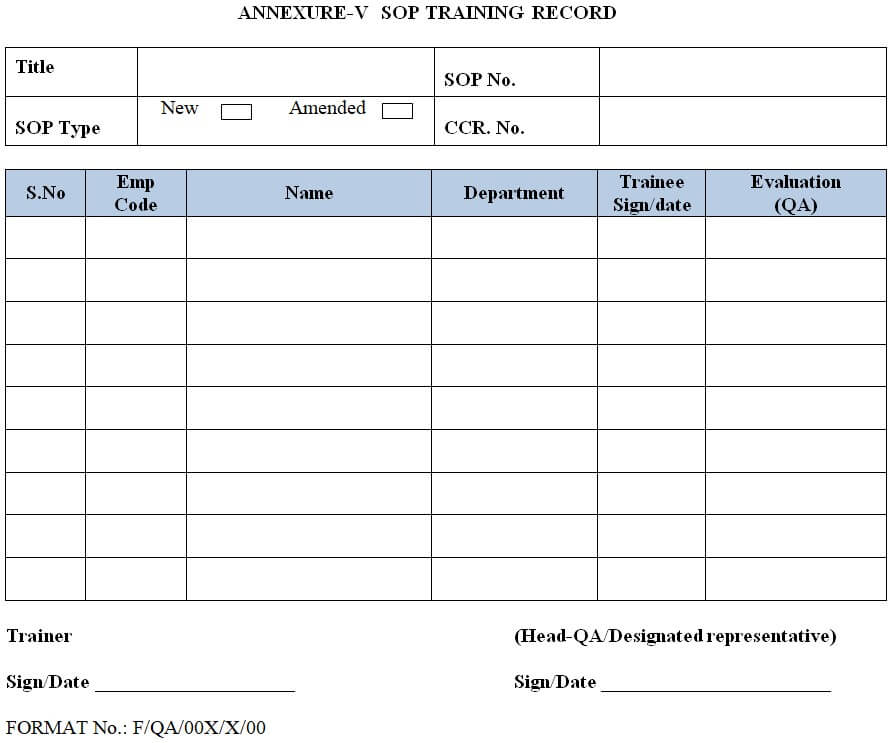
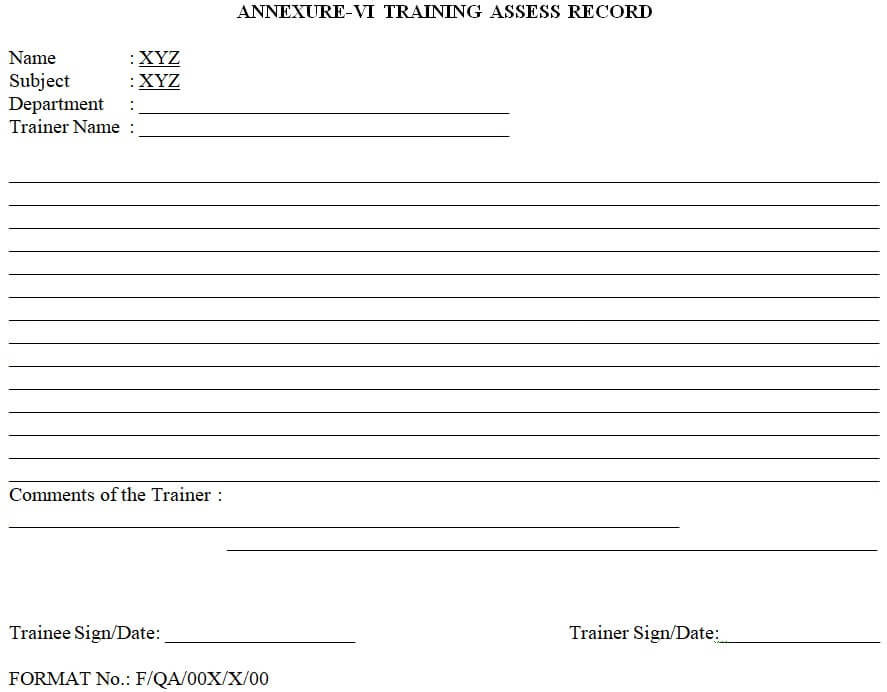
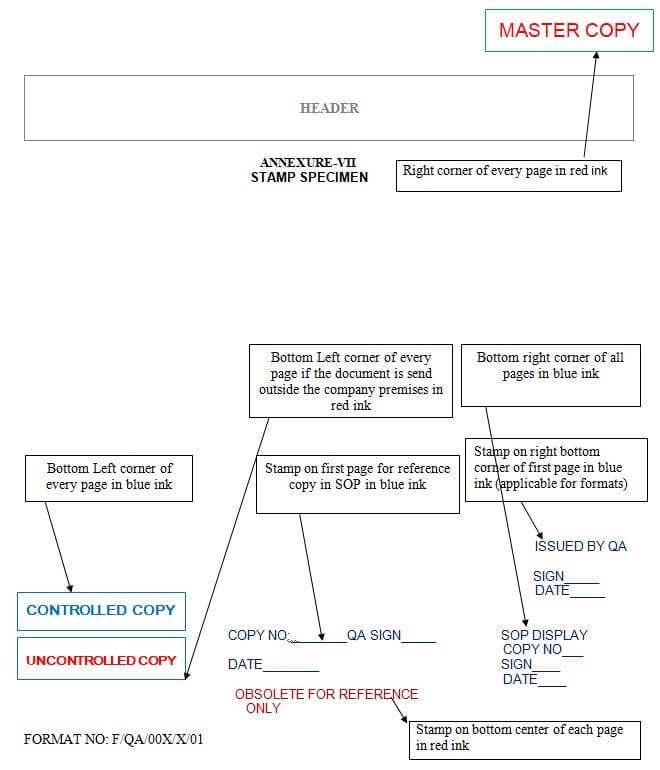
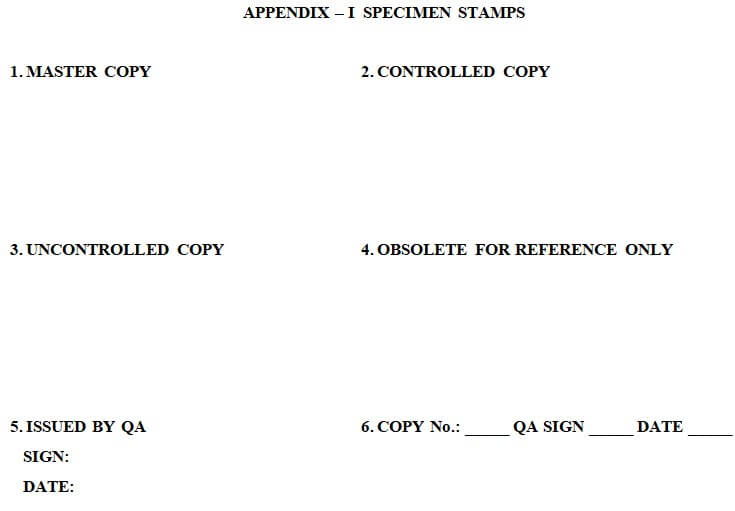