Pharma 4.0 and basically, it is a need for future pharmaceuticals. Then the question arises as to why Pharma Industry 4.0 is a need for future pharmaceuticals, there are so many reasons let me tell you one thing: data integrity.
Introduction: Pharma 4.0
You may be aware that so many companies are getting the observations and further new requirements are coming with respect to the regulatory expectations. so we need to now move to pharma 4.0. Already some people started working on that and today many companies are going for automation, software-based solutions.
So the point is now the business is increasing like anything. So we need to be aligned with that. Some guidelines such as ISPE and some other groups are being implemented. If you were to assess a pharmaceutical business five years from now, it would operate at a significantly higher level in terms of compliance, productivity, safety, and overall performance.
Pharma 4.0 plays an important role in the pharmaceutical industry. If you are not equipped with it, and if we fail to learn about it now, surviving in the pharmaceutical sector will become extremely challenging.
We will discuss elements of pharma 4.0 in collaboration with ISPE. What are the elements of Pharma 4.0, and how do they integrate with ISPE? You are already familiar with ISPE and its connection with Pharma; therefore, we will discuss how these elements collaborate.
What Pharma 4.0 Covers:
The aspects are driving towards Pharma 4.0. What exactly does 4.0 look like? We will explore its characteristics and its relationship with the ICH guidelines. The point here is how automation and other factors are linked with the ICH guidelines and other regulatory frameworks. We will discuss a holistic production control strategy.
Below we will also discuss some examples of pharma 4.0 which is followed or used currently in many companies.
Differentiating Pharma 1.0, 2.0, 3.0, and 4.0:
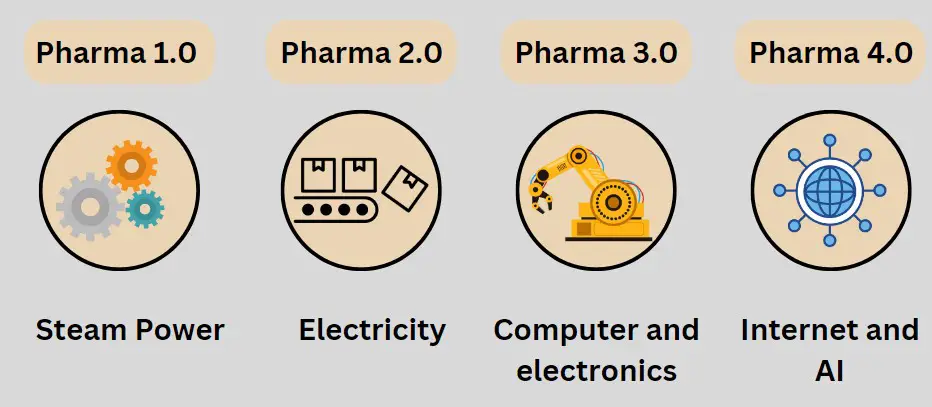
Here is a discussion on the What is pharma 4.0 and how it is different from Pharma 1.0, 2.0, 3.0 stages. so let’s start with Pharma 1.0 Stage.
Pharma Industry 1.0:
If look back in 1760, During the Pharma 1.0 stage, industries started to use steam power for their operation.
Pharma Industry 2.0:
At around 1890, the Industry 2.0 Phase started, where the use of electricity started for running the machines for mass production.
Pharma Industry 3.0:
Around 1960, Industries started using computers or HMI to run the machines or PLC to run the machines.
So, now, we are in the phase of implementing Industry 3.0. I mean, we are currently at the intersection of Industry 3.0 and Industry 4.0.
Pharma Industry 4.0:
Industry 4.0 entails the use of the Internet, as well as the Internet of Things. This means we no longer need to go to the workplace. For example, in your company, machines are everywhere, operated by PLC and SCADA. So, you give commands through PLC and all, and the machines run. This is the current scenario.
Pharma 4.0: Challenges and Opportunities:
The future scenario will be that you won’t need to approach the machine, including the HPLC. You can remain at home, process the chromatogram, and print it. Your only necessity will be to enter the laboratory to prepare the solutions and input them into the system. This concept is referred to as Industry 4.0, wherein running the machine doesn’t require physical presence at the machine level; you can operate it from a remote location.
Today, many companies automate all their operations. Batch recording, meaning everything is paperless, captures data directly from the machine. Finally, the batch record is stored or updated on the server. Approvals and in-process checks ensure everything is accurately powered into the system. This reflects the way companies are now moving forward.
So, I was telling you about the close collaboration between ISPE (International Society for Pharmaceutical Engineering). ISPE provides a lot of guidance for qualifications regarding pharmaceuticals, utilities, and support systems in the pharmaceutical industry.
Firstly, when discussing ISPE and 4.0, there are two key aspects. One is data integrity by design, which is a very important concept nowadays. Many people are discussing data integrity by design. The point is, whatever software or automation you’re using for any operation, testing, storage, or monitoring purpose, it should comply with data integrity requirements from the outset.
Now, you might wonder why we’re discussing this. The reason is, that many companies have received warning letters despite already implementing available software. So, if you’re from a pharmaceutical company, chances are your laboratory is also using one of these chromatography software. However, despite using such software, many companies are facing data integrity issues because they lack proper data integrity controls from the start. When implementing the software, they merely follow the qualification and validation protocols, sign off on reports, and implement it without evaluating data integrity from a design perspective.
So, that is the reason this is the first right arm about the collaboration of ISPE with Pharma 4.0, and the second is digital maturity. So, when you are following or using computerized systems or digital solutions, at what maturity level is that digital solution provided? At what level is it developed? At what level are the controls being put? At what level is the qualification done, and whether the system is complying with Part 11 compliance? How is it evaluated? Those are the two major wings of the relationship with ISPE.
When discussing these two wings, there are basically four aspects: resources, culture, organization, process, and information systems. These four aspects play a very important role when you want to implement them in your organization.
So the question is why do we need to go with Pharma 4.0?
It takes a lot of effort, and many people may wonder why. The reason is the continuous increase in the complexity of activities. But what does increasing complexity mean? Let’s take an example. If you ask me about 10 to 15 years ago, everybody was discussing only basic quality systems: documentation, good documentation, deviations, and CAPA training. Was anyone focusing on training effectiveness? No. Was anyone concerned about the effectiveness of CAPA?
Now, it is very important. Earlier, there were no human error investigations. Now, we need to focus on human error investigations. So, the point is, that there is always a continuous emergence of complex systems in the picture, and there are a lot of expectations by the regulators. For example, earlier there was no focus on data integrity. Now, all companies and regulators are focusing on data integrity. Previously, there were some observations considered as non-conformities related to Good documentation practices.
Now, if the same observations are noted by the authorities, they are considered as issues related to data integrity. Therefore, the point is, that there is a continuous increase in expectations by the regulators and complexity in the processes. Additionally, there is an increasing push for continuous product monitoring.
The point is, earlier, some in-process samples were taken and given to QC for analysis or testing. This occurred at the in-process laboratory. However, now the expectations involve continuous product monitoring regarding quality, safety, efficacy, and purity. This is why Pharma 4.0 will play a very important role.
Example of continued process verification: So, the continuous process verification that previously occurred through annual quality reviews was perfectly prepared annually. Data was collected and gathered annually. Now, the expectation is not for annual evaluations but for routine or more frequent evaluations of data from all batches to ensure intra and inter-batch variability. Do you understand what I’m asking? Intra and inter-batch variability need to be evaluated more frequently. Therefore, there should be more frequent reviews rather than annual ones.
Today, Many requirements are coming into the picture. You know, the computerized batch records all the machines are automated and connected to the common computerized system. Then, continued process verification will be very easy. You can just collect the data, and your work is over. Then, you can evaluate the data very easily. But if it is all manual, as a traditional approach, then it will be very tough. You have to open all the bad records, you have to open all the radical records, you have to open all the QMS, and prepare the continuous process verification. So, this way, it is driving to the pharma 4.0.
Pharma 4.0 technology enables continuous real-time monitoring of the manufacturing process, allowing for the prediction of any deviation from specified parameters. This predictive capability is crucial for ensuring product quality and reliability. For example, if the pH level of a product is supposed to be 4.5, but consecutive batches show an increase from 4.5 to 5.1, this indicates a trend of rising pH levels. Before the product is filled, predictive analysis can identify this trend and prompt action to address the underlying issue with the formulation or materials. By leveraging online data evaluation, proactive measures can be taken today to prevent potential failures tomorrow. This proactive approach minimizes downtime and ensures consistent product quality, ultimately benefiting both manufacturers and consumers alike.
But now, you may be thinking about the cost. Yes, the cost will increase, but it has more benefits, like controlling failures before they happen, ultimately enhancing productivity.
They were manufacturing the batches for the regulated market. So validation was completed for three batches. Then, initially, 01 batch and 8 to 10 batches were also completed. They cleared, they passed, they complied, and the batches were released to the market. But then, what happened? Suddenly, one batch failed.
There was no root cause identified for why the batch failed. So, the batch was kept separate, and they started investigating. The next batch was taken for manufacturing. The next batch passed. After a couple of batches passing, again, one batch failed. Again, they kept that batch separate or isolated, and the next batch started manufacturing. As they were not able to determine the root cause of the failure, they could not replace the batch. So, they didn’t release the batch but continued manufacturing the next batches.
Now, here, during the inspection, it was found that such a failed batch was among 60 or more batches that were kept on hold for a decision. The FDA issued a warning letter with observations and converted it into a warning letter stating that their process is not robust, and their manufacturing process is not robust. As a result, all batches of the products that were released to the market were recalled.
Now, the point here is, if you think about the benefit of Pharma 4.0 in this scenario, the point is, in traditional investigations and data evaluation, you have limited data recorded on the batch record. So, on the batch record, you have limited data, and you will not be able to evaluate all the product data.
But if you implement Pharma 4.0 in your facility where these types of products are being manufactured, all the batch data will be evaluated. You will have data analysis based on that, and you will come to know the factors leading to the failure of a particular batch because data is continuously generated and evaluated simultaneously. However, if you consider the traditional approach, only the displayed data is recorded, so there are significant limitations again.
You are familiar with traditional data and the traditional approach. With limited data, the investigation does not meet the required standards. Consequently, you won’t achieve a proper analysis of the data, potentially leading to the filling of batches without valid reasons. Without sufficient data, it’s impossible to identify the root cause accurately. This underscores the importance of Pharma 4.0.
So, it will provide predictive analysis. Secondly, it will assist you in properly investigating the possibility of errors or failures, and you can take action today so that these types of failures do not occur. Currently, the company is facing many problems, with more than 60 batches kept separately, and the FDA has taken significant action against the company.
Today, you might be thinking that automating all these processes could be costly. However, in two or three years, or maybe four years, it will likely become mandatory. By then, you will need to implement automation regardless. Therefore, it’s essential to start considering this now. It is highly suggested to bring up this matter with your management so that they can begin contemplating it. Alternatively, you could include this point in your management review meeting agenda to initiate the thought process within your organization.
Predictive analysis
Pharma 4.0 offers predictive analysis. Now, consider this: You have all the data. let’s suppose you have a Programmable Logic Controller (PLC). If you connect the printer, you can access all the data. But, are all the data evaluated? There is currently no solution for this. At this moment, there is no automation. What we’re doing is taking a printout of the PLC, attaching it with the battery cord, or perhaps integrating it into a computerized system. It may be uploaded into the system, and that’s it.
However, the data generated, for example, during the drying process, is not continuously evaluated. Let’s consider a simple example: What is the drying pattern in batch number one? What about the drying factor in batch number two? And so on. Each batch is considered separately nowadays.
But with Pharma 4.0, if you connect all the instruments and machines, the data will be analyzed and evaluated. It will provide predictions on whether the equipment will undergo wear and tear, whether there will be adverse observations in the equipment or process, or whether the data is trending towards failing results or borderline results. This way, predictive analysis of the data will be conducted through Pharma 4.0.
It plays an important role in protecting our processes and products from failure and equipment damage in the future. Currently, we’re discussing this concept, but it’s important to understand how it will benefit us. Do you understand its potential for reducing downtime and saving costs?
So, how will it be helpful? How will it help to protect the equipment and the machine from possible future damages? Or will it predict the lifespan of specific spare parts? Will it also protect the product from defects or prevent it from following an outward trend? This predictive capability will aid in optimizing the process. Sometimes, there can be a lot of variability in the process, and it’s not always possible to monitor it continuously. However, with automation and solutions like Pharma 4.0, you’ll be able to optimize the process and all operations, thereby reducing variability.
As mentioned earlier, there is a significant amount of data that needs to be generated so that we can evaluate various aspects. If you refer to the process validation guidelines provided by the FDA, you will find that it also highlights the importance of collecting and evaluating data. The definition of process validation entails the comprehensive collection and assessment of data. Therefore, it is essential to collect and evaluate as much data as possible.
To illustrate, let’s consider an example that demonstrates the quantity of data we can obtain through automation. For example, tablet inspection machines are utilized for this purpose. These machines inspect each tablet’s defects for any foreign matter, foreign tablets, black specs, and numerous other physical defects such as embossing and demossing. They examine various parameters in each tablet.
Data Analysis:
The single online tablet inspection system generates a vast volume of data because it contains all aspects of one tablet. So, if you consider a batch size of one million tablets, then just imagine, that up to 24 terabytes of data are generated per year by just one tablet inspection machine. At the same time, if we take United Airlines as an example, which generates 9 terabytes of data, one can only imagine the sheer volume of data generated. Having more data to evaluate is the key benefit and novelty of this system.
If we have more and more data, we will have more and more information, and we will be able to evaluate properly. So, don’t worry that 24 terabytes of data will be evaluated automatically by the system. You need not go through each and every data manually; you will get all the statistics and information from the product. This way, you will come to know which type of physical defect is increasing from batch to batch, and accordingly, you can focus on the particular product. This will help significantly.
Role of Artificial Intelligence and Machine Learning in Pharma 4.0:
Now you are already aware that artificial intelligence is a new wing in engineering. It has started and, coupled with artificial diligence, the chat deputy has already come into the picture. The deputy is also playing a significant role in data evaluation and analysis.
Now we have lots of data but are worried about how to analyze it, Don’t worry nowadays artificial intelligence can do this work very efficiently in no time.
Goal of Pharma 4.0
The primary goal of Pharma 4.0 is to make pharmaceutical production safer and more efficient along the entire value chain. Here, the main point is cooperation. You need cooperation for the digitalization of processes and systems. This cooperation extends to all parts of the supply chain, not just one department or case.
It involves cooperation with academia, industry associations, and learning institutions. Additionally, exchanging best practices with players from various industries is essential. Some automation may work well for one company or industry but not for others. Therefore, exchanging best practices helps in generating better ideas for Pharma 4.0 implementation.
Shifting from Industry 4.0 to Pharma 4.0
Basically, Industry 4.0 is the broad terminology, while Pharma 4.0 is implementing the automation used in Industry 4.0 for pharmaceutical purposes. It focuses specifically on real-time monitoring, simulation, and control of manufacturing operations. So, when discussing Industry 4.0 and Pharma 4.0, our main focus should be on continuous real-time monitoring, simulation, and control of the manufacturing process.
The goal is to enable processes to self-adjust based on the data within the interconnected system throughout the operation. So, the point here is, if some variability or variations are occurring, the machine should automatically adjust as per the requirements. This means that there’s no need for a new operator or supervisor to manually change any parameters. Just like an automatic gear vehicle, where previously manual gear shifting was required, now, as the speed increases, the gear of the vehicle changes automatically. This is the standard scenario for drivers.
Similarly, in the case of the machine, it monitors and analyzes the changes in parameters and adjusts accordingly, ensuring consistent product quality. This process should be based on two main factors: Product quality by design and process analytical technology.
Guidelines and Regulations:
We have been discussing this approach for a while now. Though there are guidelines available, not many companies have implemented them yet. However, gradually, companies are starting to implement some controls. It’s not completely comprehensive, but they are exerting a considerable amount of control. Additionally, quality by design remains a requirement according to ICH Q8.
While discussing Pharma Industry 4.0, we need to consider that it should meet the GMP regulations. Now, what does it mean? It means that it should comply with the basic GMP requirements, 21 CFR. If it does not comply with these GMP requirements, then it is of no use. This point is very clear. I am putting it here because now many companies are implementing automation. Many companies claim that they are part 11 compliant.
Basically, when we are discussing Pharma 4.0, it will become a reality, or actually, you know, based on the implementation phase, when we will have the necessary base platform. This means it will have some integrated tools and devices where humans or operators have usability and awareness. It should not be that complex; it should be simple to use.
Correct machines and equipment should be fitted with sensors that can continuously collect data. This data should be evaluated to specific expectations using software. So, that is what is required. In case of any failure or prediction, the predictive information or predictive failure information should be communicated to the supervisor through different means or through pop-ups.
Relation to ICH Guidelines
You know, the ICH Q10 quality system is the design, creation, and execution of the shop floor production process so that it ensures repeatability, robustness, and getting it right the first time. You know, writing the first execution of the commercial production process is based on that. If you want to comply with these standards, you will require clear automation because you cannot manually record everything. That is the point. The parameter space must be adopted throughout the product lifecycle. I already told you that the lifecycle approach is the expectation of ICH Q10. The design space is, again, part of the Q8 design space requirement and submission-based control strategy.
Holistic Production Control Strategy:
It requires an educated workforce to manage integrated processes. So, the people who are going to use these system software, computerized systems, and all related tools should be educated or trained on how data flows from the system to the local server, from the local server to the main server, and how data will be analyzed. All of this is required for modern platform machines or facilities to support business processes with integrated GxP, IT systems, along with the supply chain. Moreover, the business processes should also support this integration. If there is a lot of automation but they are not integrated with the GxP systems, then they are of no use. For example, if machines have automation but deviations are handled manually, then they are of no use.
So, you should have a system in such a way that during manufacturing, if any parameter goes out of trend, it should automatically give an alert. It should pop up automatically, indicating the deviation or incident, or whatever notification is necessary. This way, it should be connected. Nowadays, many companies have chromatographic systems connected with Part 11 compliance software. They claim it as Part 11 compliance software, but still, they receive observations. The problem lies in the second part, such as raising the OOS, investigating the lab incident, or laboratory errors, which are done manually. If there is an error, it is not directly prompting to raise the incident or OOS, and because of that, people are facing a lot of problems.
New Technology Transformation:
- Continuous manufacturing ICH Q13
- Paperless manufacturing: paperless manufacturing means everything is automated and computer-based
- Additive manufacturing and 3d printing
- big data and analytics: Big data analytics lets us understand with an example of the tablet inspection machine. So, you will get big data, and it will analyze all the data. This will help you come to know about the predictions and understand what type of tablet defects are being generated more and more, allowing you to gain insights.
- Simulation: So you can simulate different products or manufacturing processes.
- Robotics: You can use robotics in manufacturing highly sensitive, highly toxic, or sterile products.
What are additive manufacturing and 3d Printing?
Many companies are now not very involved in the process of additive manufacturing or 3D printing, but I will give an example. Suppose there is a situation where mixing is very critical, especially in a specific product. By using additive manufacturing, you can add material in very thin layers, one layer at a time. First, you add one layer of material, then a second uniform layer, followed by a third, and so on. All the layers are uniformly added to the material in this way.
This is how additive manufacturing, or 3D printing, works. Many companies use this technology to produce products. Let me give you an example of surgical gloves. If you have specific size or other requirements for the gloves, you can design them and then command the printer to produce them automatically. Just like when we print a document from a word processor or PDF file, the printer produces the document. Similarly, when you give the command, the 3D printer manufactures the desired gloves or other materials automatically.
Roadmap for Pharma 4.0
You know, the roadmap is very clear on how to proceed with Pharma 4.0. The first step involves management, then connecting all the computers, followed by collecting data. After that, you analyze the data based on the parameters you’re interested in. When discussing this, you must consider two points: digital maturity and data integrity. This allows you to create a roadmap for Pharma 4.0, which varies from company to company. Your company may have already implemented automation in the PLC, but others may not even have PLC or other automation. Therefore, they need different roadmaps.