Drying is a process that involves the removal of water or other solvents through evaporation from solid, semi-solid, or liquid substances by applying heat to get dry solid mass or powders. Below is a detailed discussion on Drying, its application, Objective, mechanism, Theory, Rate of drying curve, formula, and equipment used.
Objectives of Drying
In the Pharmaceutical and Food industries, drying is carried out for one or more of the following reasons.
- To avoid or eliminates moisture that may lead to corrosion and decrease the product stability.
- To improve or keep the good properties of a material, for example, Flowability, Compressibility.
- To reduce the cost of transportation of large volume materials (Liquids).
- To make the materials easy or more stable for handling.
- Drying process also acts as a preservative, because water is the main content in a solution that allows micro bacterial growth.
Applications
“Drying is an important process in various applications:
- Granules used for making tablets or filling capsules need to be dried.
- Tablets, granules, and particles are dried during coating procedures.
- Nanoparticles, microspheres, and microcapsules are dried after preparation.
- Materials are dried to aid the grinding process.
- Freeze-drying (lyophilization) is a specific drying technique.
- It is also applied in preparing sterile injection powders.
- When obtaining plant-derived medicines, the plants must be dried before extraction, and the resulting extracts also need to be dried.
- Inorganic salts like sodium chloride and calcium carbonate require purification and drying.
- It is necessary to obtain drugs and excipients in dry powder form.”
Way to Remove Water by Drying:
There are two ways to remove water by drying:
A. Thermal process– By using heat
B. Non- Thermal– 1. It involves squeezing wet substances for example Spongy material.
2. By Adsorption- Water is adsorbed by all desiccant particles.
3. By Extraction- It is done by extracting water from wet solids.
Mechanism of the Drying
Mechanism of drying involving 2 processes.
1. Heat Transfer- Heat transfer is the process of heat flow to the exterior surface while generated within a solid.
2. Mass transfer- It involves the momentum of the flow of heat or vapor from the liquid solution.
Theory of Drying:
1. Diffusion Theory: The movement is from higher to lower concentration. So when we apply heat to a substance the liquid particles at the bottom get heated and they transfer heat to the next particle and so on it gets to the last particle and gets evaporated.
2. Capillary Theory: There are some capillary like voids present in wet solids. So when heat is provided on a solid, The water (liquid) gets removed through voids, and a dry solid is obtained.
Equilibrium moisture content (EMC) When the moisture content of a solid is in equilibrium with the given partial pressure of vapor in the gas phase is called Equilibrium moisture content. The EMC of a hygroscopic material, partially surrounded by air, indicates the moisture content at which the material neither gains nor loses moisture, varying with the material, relative humidity, and temperature of the surrounding air
Measurement and Application of Equilibrium moisture content:
It has two processes:
1. Desorption: Desorption solids contain more moisture than equilibrium moisture content. Then it will continuously lose water until EMC is reached.
2. Adsorption: If a solid substance with moisture is put into an environment where humidity and temperature are constant. it will take moisture until it reaches EMC.
Measurement of EMC:
Measure the equilibrium moisture content by putting the sample in a desiccator which is maintained at known relative humidity. Sample from each desiccator is collected and weighed at particular intervals until a constant weight is achieved. The final weight will be EMC.
Application:
- Analysis of drying operation and particularly in predicting final moisture content.
- Prevent the sample from over-drying
In the Drying Process, several terms are commonly used as below:
Bound water: Bound water refers to the moisture content of a substance with an equilibrium vapor pressure lower than that of pure liquid at the same temperature.
Unbound water: Unbound water, on the other hand, refers to the moisture content of a solid with an equilibrium vapor pressure equal to that of pure liquid at a given temperature.
Free moisture content (FMC): represents the excess moisture content of a solid beyond the equilibrium moisture content, and only free moisture can be evaporated during drying.
Critical moisture content (CMC): It represents the moisture content at which the constant-rate drying period transitions into the falling-rate drying period.
The constant-rate drying period: It is characterized by a constant amount of moisture evaporated per unit time per unit area of the drying surface, while the falling-rate drying period involves a continuous decrease in the amount of moisture evaporated per unit time per unit area of the drying surface.
Rate of Drying curve:
The rate of the drying curve provides valuable information about the drying process. It shows the drying rate in relation to drying time or moisture content. Their curve shows three main stages:
- Phase-1 Transient early stage: This stage involves the heating up of the product, known as the transient period.
- Phase-2 Constant rate period: In this stage, moisture removal is relatively easy as it occurs at a constant rate.
- Phase-3 Falling rate period: As the name suggests, the moisture within the solid matrix becomes bound or held, resulting in a continuous decrease in the rate of moisture removal.
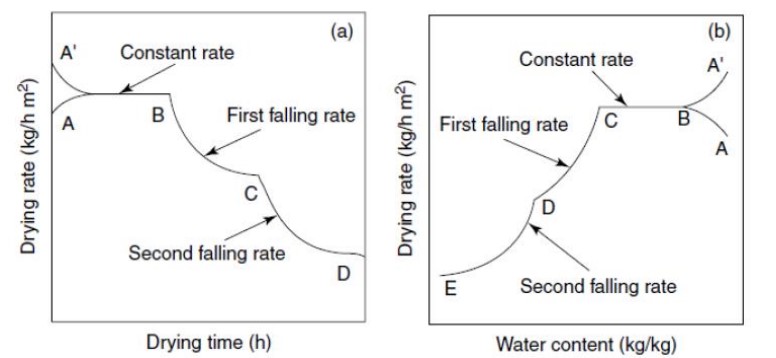
- Point B represents the temperature condition of surface product Curve BC [constant rate]- removal of unbound water from the product.
- Curve CD [1st falling rate]- occurs when wetted spots in the surface decline continuously until the surface is dried.
- Curve DE [2nd falling rate]- begins when the surface is completely dry Point C —decrease in drying rate start is referred to as CMC
The critical moisture content marks the point at which the drying period shifts from a constant rate to a falling rate. The behavior of food materials during drying depends on factors such as porosity, homogeneity, and hygroscopic properties. Hygroscopic materials tend to enter the falling rate period faster compared to non-hygroscopic materials.
Formula used for the Drying process Measurement:
Below is the following Formula that is used while drying process measurement:

Dryers Classification
Classification of Dryers as Follow:
Static Bed Dryers:(Ex. Tray Dryers, Freeze Dryer)
Moving Bed Dryer (Ex. Drum Dryer)
Fluidized Bed Dryer, Vacuum Dryer, Pneumatic Dryer
(EX. Spray Dryer)
Conclusion:
By using these drying techniques and controlling their mechanism, the drying process can easily remove moisture and achieve the desired property of final products.
REFERENCES
Subrahmanyam CVS, Setty JT, Sarasija S. Laboratory manual of pharmaceutical engineering (Unit operations) C.V.S., Delhi Vallabh Publications.
Pharmaceutical Engineering by K.Sanbamurty (New Age International, New Delhi)Cooper and Gunn’s Tutorial Pharmacy Edited by S.J.Carter (CBS Publishers, Delhi).