Size Separation involves the separation of a mixture containing particles of various sizes into two or more portions. This can be done through the use of screening surfaces or by shifting the mixture. It is also commonly known as sieving, sifting, or screening. The technique of size separation is based on different physical properties of the substances in the mixture, such as their size, shape, and density.
At starting, crude drugs like Nuxvomica, Rauwolfia, Ephedra, Ashoka, and others are typically present in larger sizes. But with the help of these techniques, it becomes very easy to reduce and separate the size of any crude drugs. However, we can obtain granules and particles of the desired size, thereby enhancing their pharmaceutical and pharmacological activity.
Principle of Mechanical Size Separation:
When it comes to size separation, mechanical sieving machinery depends on various methods. These methods include agitation, brushing, and centrifugal techniques as given below:
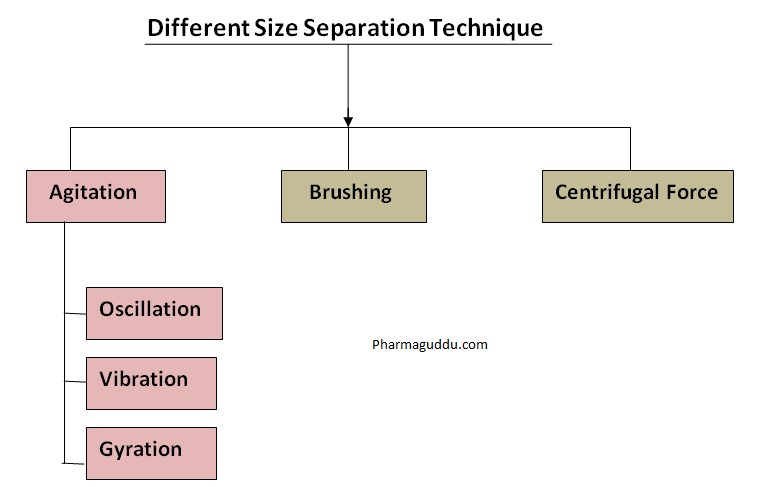
Agitation methods introduce movement to the sieves in different ways, such as:
a. Oscillation: Here, the sieve is mounted on a frame that oscillates back and forth. While simple, this method may cause the material to roll on the sieve’s surface.
b. Vibration: By using an electric device, the sieve is rapidly vibrated at high speed. This vibration help in the passage of powdered material through the sieve.
c. Gyration: Using a rubber-mounted sieve connected to an eccentric flywheel, this method imparts a rotary motion of small amplitude to the sieve.
Other mechanisms Include:
Brushing methods, on the other hand, involves using a brush to move the particles across the sieve’s surface and keep the meshes clear. A circular sieve utilizes a centrally rotated brush, while a horizontal cylindrical sieve employs a spiral brush rotated along the longitudinal axis.
Centrifugal methods, use a vertical cylindrical sieve with a fixed high-speed rotor. As the rotor rotates, centrifugal forces the particles outward. Additionally, the air current generated by the high-speed rotor helps in sieving the powder.
Official Guidelines for Powder Size:
The Indian Pharmacopoeia (ai.P.) provides rules for powders used in medicines. It says that the coarseness or fineness of a powder is determined by the size of the sieve holes it can go through. There are five grades of powder defined by the I.P. (See below Table), and each grade has a specific sieve number.
Table 1: Standards for Powders given by the Indian Pharmacopoeia (I.P.)
Grade of Powder | Sieve Number (All Particles Must Pass) |
Coarse | 10 |
Moderately Coarse | 22 |
Moderately Fine | 44 |
Fine | 85 |
Very Fine | 120 |
The I.P. suggests using a smaller sieve for rough powders, but not more than 40% should go through it. Table 2 below shows the different powder grades and their matching sieve numbers. So, when we say a powder is “coarse,” it means all particles go through a No. 10 sieve, but not more than 40% pass through a No. 44 sieve. People usually call this a 10/44 powder.
Table.2: Standards Classification for Powders given in I.P.
Grade of Powder | Sieve (All Particles Must Pass) | Sieve (Not More Than 40% Pass) |
Coarse | 10 | 44 |
Moderately Coarse | 22 | 60 |
Moderately Fine | 44 | 85 |
Fine | 85 | Not Specified |
Very Fine | 120 | Not Specified |
If a powder is described with a number, it means all particles must go through that sieve. And when we grind and sift a plant-based medicine, we must not throw any part away. This classification is important when comparing a plant-based medicine to a chemical substance.
Chemical materials are usually the same throughout. If we need a specific amount of powder, we can grind extra to get the right size by using a sieve. Then we can remove the bigger particles. But plant-based medicines are made up of different parts with different hardness levels.
So for this, We grind the soft parts first, and the leftover material contains more of the harder parts. Sometimes the constituents are not spread evenly within the plant. For example, digitalis has the most important parts concentrated in the middle and veins of the plant. So, if we throw away the extra material when grinding and sifting, we might lose a lot of the active parts.
Official Guidelines B.P.: Besides the regular grades, there is another grade called ultrafine powder in the British Pharmaceutical Codex. For this grade, at least 90% of the particles should not be bigger than 5 µm, and none of them should be larger than 50 µm. They check the size of the particles using a microscope.
The applications and objectives of size separation include:
- Determining the particle size required for the production of tablets, capsules, suspensions, emulsions, and similar formulations.
- Achieving the desired granule or particle size to ensure proper flowability and uniformity.
- Removing undesirable substances through the size separation process.
- Enhancing the mixing properties of powders by obtaining particles of the desired size.
- Improving the solubility and stability of particles during the production process.
- Optimizing feed rate, agitation, and screening parameters during production.
- Conducting quality control of raw materials to ensure their suitability for use.
Size Separation Methods:
Below are the different Methods used to separate powder as per their size:
Conclusion:
In conclusion, mechanical size separation uses different techniques such as agitation, brushing, and centrifugal methods, each designed to handle specific requirements and optimize the sieving process.