An audit is a main element in determining the growth and market presence of any organization. The success of an audit is dependent on various factors, that need to be reduced. some of the Audit Checklist for Human Resources and Administration that can be used are described below:
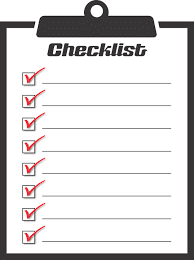
1.0 Personnel Audit Checklist
A. Key Personnel
- Are there sufficient key personnel to supervise assigned functions for the following Departments:
- Production
- Filling
- Labeling / Packaging
- Quality Control
- Engineering
- Maintenance
- Quality Assurance
- Marketing & Supply
- General Administration & Account
- Procurement & Stores
- Are they skilled / trained in fields such as biology, microbiology, chemistry veterinary medicines, chemical or industrial engineering, etc.?
- Engineering
- Production Department (s)
- Filling
- Quality Control
- Quality Assurance
B. Training
- Are there on-the-job training procedures for new employees?
- Are training and education records available?
- Is all records are current?
- Are they filed with the supervisor?
- Engineering / Maintenance
- Production Department(s)
- Filling
- Quality Control
- Quality Assurance
- Does a GMP training program exist?
- For a new employee?
- Annual update for all staff?
- Are records maintained?
- Is there training in containment procedures?
- By written procedures?
- Are records maintained?
C. Personal Hygiene
- Is appropriate protective apparel required?
- Is there a gowning SOP for production staff?
- For other staff entering production areas? (Engineering / Maintenance; cleaners; QC sampler; QA auditors)
- For staff in Quality Control Lab?
- Are staff instructed to report health or medical problems that may have an adverse effect on the product?
- Is there a medical monitoring program to ensure the protection of staff and products? Covid-19 Vaccination where applicable? For all employees?
- Do control entry requirements exist for :
- Production areas?
- Testing areas?
- Do procedures exist for preventing unauthorized entry into:
- Production areas?
- Storage areas?
- Quality Control areas?
- Are the procedures in writing?
2.0 Premises
- Is the building used for manufacturing of product suitably located and constructed, and of adequate size to facilitate cleaning, maintenance, and proper operation?
- Are areas clearly defined and appropriately controlled:
- For quarantine and storage of starting materials?
- For storage of in-process material?
- For manufacturing and processing operations?
- For control and laboratory operations?
- For quarantine and storage of finished products?
- For holding of rejected material?
- For ancillary usage, e.g. Restrooms, maintenance workshops?
- Does the building design prevent the entry of insects, vermin, and other animals?
- Plumbing:
- Do adequate drains exist? Are they designed with an atmospheric break to prevent back-siphonage from the sewer?
- Are traps being maintained to ensure adequate performance?
- Does the design of the facility achieve a unidirectional flow of materials, personnel, product, and waste so as to avoid cross-over of clean and dirty (infectious) materials?
- Is the lighting provided adequate for the conditions necessary for the work being conducted in the area?
- Are facility layout drawings including mechanical, electrical, and architectural kept up-to-date following changes? Is revalidation of facilities performed following refurbishment?
- Campaign production:
- Is the facility designed and constructed to permit production in campaigns?
- Is there a documented procedure for changeover that described decontamination, removal of equipment, etc.? Is the procedure followed?
- is there a campaigning schedule available?
- Do washing facilities include:
- Hot and cold water?
- Soap and detergent?
- Clean toilet facilities that are easily accessible to the working area?
- Clean hand drying facilities?
- Are the premises satisfactory with respect to:
- Neatness and cleanliness?
- State of repair, e.g. Paintwork, cracks in floors, ceilings or walls, door seals, etc.?
- Exposed piping or electrical wiring?
- Blocking of air ducts?
- Equipment blocking corridors or exists?
Each point of the Audit checklist shall be filled as applicable and comments or remarks, in addition, shall be given under the remarks column in the checklist.
Note: The points mentioned in this list are not limited to these only

Naresh Bhakar is the Founder and Author at Pharmaguddu.com, bringing his extensive expertise in the field of pharmaceuticals to readers worldwide. He has experience in Pharma manufacturing and has worked with top Pharmaceuticals. He has rich knowledge and provides valuable insights and data through his articles and content on Pharmaguddu.com. For further inquiries or collaborations, please don’t hesitate to reach out via email at [email protected].