The ISO 14644‑1 standard (2015 edition) is the global benchmark for cleanroom air cleanliness, defining nine classes (ISO Class 1–9) based on airborne particle counts. Each class sets maximum concentrations of particles ≥0.1, 0.2, 0.3, 0.5, 1.0, or 5.0 μm in a cubic meter of air. In practice, lower class numbers mean cleaner environments. For example, ISO Class 5 (used in pharmaceutical Grade A/sterile areas) allows no more than 3,520 particles ≥0.5 μm per m³. ISO 14644‑1 applies across industries (including pharmaceuticals), providing a unified, science-based way to certify cleanrooms.
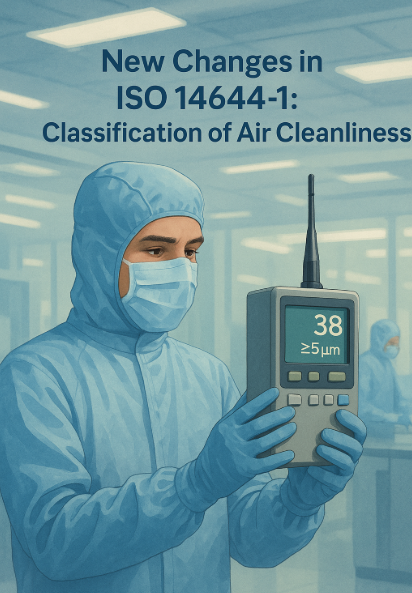
In late 2015, ISO released a major revision of Part 1 – its first update since 1999. This update refined the classification tables and testing methods, with an eye to modern cleanroom technology and regulatory needs (e.g., pharmaceutical GMP Annex 1). The core concept (class limits for particle sizes) remains intact, but the presentation and procedures have changed in key ways. In short, the 2015 revision is titled “Classification of air cleanliness by particle concentration” and keeps the same ISO classes, but simplifies sampling and reporting rules.
Key Changes in the ISO 14644‑1:2015 Revision:
The 2015 revision introduced several important updates affecting how cleanrooms are classified. These include:
Title change: The name became “Classification of air cleanliness by particle concentration,” stressing that the standard is based on measured particle counts rather than a subjective notion of “cleanliness.”
Explicit class tables: Instead of relying solely on a formula, the new ISO Table 1 explicitly lists the concentration limits for each ISO class and particle size. The familiar class thresholds are preserved (e.g. ISO 5 still allows 3,520 particles ≥0.5 μm per m³). However, some entries were removed. Notably, the ≥5.0 μm limit for ISO Class 5 was dropped. (In the 1999 standard, Class 5 had a 5 μm limit, but ISO 5 is so clean that collecting 5 μm particles is impractical.) Class 1 at 0.2 μm, Class 2 at 0.5 μm, and Class 3 at 1.0 μm were also removed. New notes in the table explain how to interpret blank entries.
Macro-particle (‘M’) descriptor: To handle large particles (≥5.0 μm), the revision defines them as macroparticles and introduces an “M” descriptor. Rather than altering the ISO class values, macro limits are written like “ISO M (20; ≥5.0 μm).” For example, Annex 1 Grade A (an ISO 5 environment) at rest is specified as ISO 5 (≥0.5 μm) and ISO M (20; ≥5.0 μm). In plain terms, this means: the Class 5 limit (3,520/m³ at 0.5 μm) still defines cleanliness, and separately, the large-particle limit (20/m³ at 5 μm) is tracked by the M descriptor. This reflects the view that ≥5 μm counts are important for monitoring events but not for determining the ISO class itself.
No more 95% UCL: Previously, when using 2–9 sample locations, a statistical “95% upper confidence limit (UCL)” on the count was calculated to ensure safety. The 2015 version eliminates the UCL calculation. Instead, each sample location is evaluated on its own: all points must meet the class limit for the room to pass. In simple terms, there is no longer any averaging or statistical fudge – every sampled spot must individually satisfy the limits.
Sampling locations by table: The new standard replaces the old √area rule with a lookup table (Annex A, Table A.1) for the number of sample locations (NL) needed for a given cleanroom area. This table is designed so that testing NL points gives ≥95% confidence that at least 90% of the room air meets the limits. In practice, this usually increases the number of sample points compared to the old method. (For very large rooms (>1000 m²), one can still use the area formula as a fallback.)
Other technical updates: Particle counters must be calibrated to ISO 21501‑4 (light scattering standard). The sampling probe tubing is now limited to <1 m in length to minimize particle loss. Intermediate-class tables were added for optional decimal classes, but these rarely apply in pharma. Importantly, the actual class limits (number of particles) and required sample volumes remain unchanged from ISO 1999 (e.g., ISO 5 still uses 1 m³ total sample volume).
Each of the above changes is carefully explained in ISO 14644‑1:2015, but here is a concise summary of a couple of points:
Sampling plan example: ISO 14644‑1:2015 includes a table mapping room area (m²) to the minimum number of particle-count locations (NL). For instance, a 100 m² room now requires NL=16 sample sites. This ensures rigorous coverage; even a 2,000 m² cleanroom must be tested at 54 locations instead of the 45 required under the old formula.
Macro-particle example: The standard explicitly treats particles ≥5 μm as “macroparticles.” A Grade A clean area (ISO 5 at-rest) typically has an Annex 1 limit of 20 macroparticles/m³ /m³. In ISO 14644‑1:2015, this is written as ISO M (20; ≥5.0 μm). The ISO Class 5 count (3,520 at ≥0.5 μm) is unaffected by these macros.
Related: Microbial testing of non-sterile products
Minimum Number of Sample Locations Based on Cleanroom Area:
(As per ISO 14644-1:2015 Classification Guidelines)
Area of Cleanroom (m²) Less than or equal to | Minimum Number of Sample Locations (NL) |
---|---|
2 | 1 |
4 | 2 |
6 | 3 |
8 | 4 |
10 | 5 |
24 | 6 |
28 | 7 |
32 | 8 |
36 | 9 |
52 | 10 |
56 | 11 |
64 | 12 |
68 | 13 |
72 | 14 |
76 | 15 |
104 | 16 |
108 | 17 |
116 | 18 |
148 | 19 |
156 | 20 |
192 | 21 |
232 | 22 |
276 | 23 |
352 | 24 |
436 | 25 |
500 | 26 |
1000 | 27 |
>1000 | Use Equation A |
Equation A (for Cleanrooms Larger than 1000 m²):
N = 27 × (Area / 1000)
(Round up to the nearest whole number)
What the Changes Mean for Pharmaceutical Cleanrooms:
For pharmaceutical cleanrooms (EU Grade A/B/C/D), the core ISO classes haven’t changed – Grade A is still classified by ISO Class 5, Grade B by ISO Class 7 (operational), etc. In practice, the numeric limits for 0.5 μm particles remain the same as before. For example, a Grade A (ISO 5) area is still allowed up to 3,520 particles ≥0.5 μm per m³. The key difference is how we interpret and report the larger particles:
Macro vs Micro: Under the new ISO, ISO 5 has no specified limit for ≥5 μm particles; instead, the Annex 1 Grade A limit of 20/m³ is expressed via the M descriptor. In other words, ISO classification focuses on submicron (≥0.5 μm) counts, and ≥5 μm counts are logged separately. This matches the updated regulatory view: ISO 14644 states that low 5 μm values are statistically irrelevant and therefore cannot be the basis for a cleanroom classification. EU GMP Annex 1 (2022) explicitly accepts this and separates classification from monitoring. It requires that ≥5 μm counts be continuously monitored (and investigated if frequent), but they no longer define the nominal class.
Regulatory alignment: The PIC/S/EU GMP guidance expects ISO classes to be used for grading. Under the revised ISO, firms will classify rooms by the ISO‑table limits (e.g. “ISO 5 at-rest”). Macro counts (Grade A: 20/m³) become part of the environmental monitoring records, not the pass/fail of a periodic classification. In practice, this means a cleanroom qualification protocol will state “Classify the room as ISO 5 (0.5 μm counts)” and separately check that any ≥5 μm counts meet the Grade A macro limit.
Sampling rigor: With more sampling points required, pharmaceutical sites will likely revise their qualification plans. The elimination of the 95% UCL means each sample location must individually meet the ISO class limit. Previously, one failing location might have been masked by the UCL calculation; now, any high count immediately fails the classification and must be addressed. In effect, cleanroom rooms could be held to a stricter standard of uniformity.
Continuous monitoring: The new ISO text also acknowledges modern monitoring. It allows extending the interval between full classifications if continuous monitoring systems are in place (a clause moved from ISO 14644‑2 into 14644‑1). This complements pharmaceutical trends toward permanent real‑time counters in Grade A/B. Continuous systems will now play double duty: showing ISO class stability (so you can certify less often) and flagging any transient 5 μm events for investigation, per Annex 1.
In summary, the ISO 14644‑1:2015 revision does not change the cleanliness targets for pharma, but it changes how we get there. Facilities must update SOPs and protocols to: use the new sampling tables, apply the one‑point‑one‑sample rule, document macro‑particle counts via the M descriptor, and calibrate equipment accordingly. In practice, a pharmaceutical cleanroom will still aim for “ISO 5 (≥0.5 μm) with Grade A macro limit 20 (≥5.0 μm),” but the paperwork and procedures reflect the new ISO format.
Practical Implications for Operations
The revised ISO 14644‑1 changes the day‑to‑day approach to cleanroom testing and monitoring in several ways:
More sample points: Qualification runs will take longer. Almost all rooms (except the very smallest) will need more sampling locations than under ISO 1999. For example, moving from 45 to 54 sample points in a large hall. Operations staff should plan tests accordingly.
Even point distribution: Sampling must cover the space more evenly. The new guidance says points should avoid direct HEPA flow (as such spots might not represent overall conditions). In practice, this means adjusting our sampling maps – e.g. spacing points across the work area instead of clustering under filters.
No averaging: With no UCL allowance, every sampled location must pass its limit. Training and checklists should emphasize that finding any out‑of‑spec reading triggers investigation (and cleanroom actions), even if adjacent points are clean.
Simplified reporting: On the plus side, reporting is conceptually simpler: a location either meets the ISO limit or it fails; no statistical formula to compute. This can make qualification reports easier to interpret (but also more unforgiving).
Equipment setup: Confirm all particle counters meet ISO 21501‑4 calibration and use short sampling lines. Longer tubing (>1 m) can undercount large particles, so labs must reconfigure sampling racks if needed. Also, verify that counters can handle the two size channels (≥0.5 μm and ≥5.0 μm) separately.
5 μm monitoring: Although 5 μm counts no longer set the ISO class, they remain important. Continuous EM counters in Grade A/B should still record 5 μm particles (often using a cubic‑foot sample for practical speed). Under Annex 1, even a single large particle in 1 ft³ can trigger an alarm – so many sites now use rolling averages or extended sampling to avoid nuisance alarms. Processes should review these alarm settings and trending criteria in light of the new guidance.
Long‑term strategy: Because ISO 14644‑2 (the companion part) now allows less frequent re-classification when monitoring is in place, pharma plants might consolidate audits. If continuous monitors show consistently good control, one might classify (e.g., each room) less often than annually, saving qualification resources. Of course, any facility change (new equipment, major repairs) will still prompt re-classification under the new rules.
Conclusion:
In conclusion, ISO 14644‑1:2015 represents a modernization of cleanroom classification. Pharmaceutical manufacturers should update their GMP procedures to align with these changes: revise sampling plans, retrain staff on the new “all points must pass” criterion, and incorporate the macro-particle descriptor into documentation. By doing so, they will both comply with current ISO rules and support the stringent particulate control required by sterile drug production. In practical terms, this means more thorough sampling and clear separation of classification (ISO class by 0.5 μm counts) from monitoring (including ≥5 μm events), ensuring that high-quality, contaminant-free environments are maintained in production.

Naresh Bhakar is the Founder and Author at Pharmaguddu.com, bringing his extensive expertise in the field of pharmaceuticals to readers worldwide. He has experience in Pharma manufacturing and has worked with top Pharmaceuticals. He has rich knowledge and provides valuable insights and data through his articles and content on Pharmaguddu.com. For further inquiries or collaborations, please don’t hesitate to reach out via email at [email protected].