ISO CleanRoom Classification is done to define the limit of particles as per the standardized or predetermined criteria. A cleanroom is one where the viable count and particle count are kept within predetermined and standardized ranges. These rooms must always be kept at the specified level of cleanliness, as their name suggests, and cleaning is a strict requirement. Cleanrooms are crucial for the production of pharmaceutical products.
Based on the size of the particles and the quantity of the particles per cubic meter of air, clean rooms in the pharmaceutical industry are categorized. There are specific limits for particle count, microbial count, and air changes for each clean room.
Cleanroom Classes and Their Importance:
Cleanliness classes, for example, grade A grade B, and grades C and D can also link to the ISO classes and provide a direct link between the monitoring plan alternatives and the class for example in grade A which can be considered an ISO class 5.
The monitoring activities must be performed during the full duration of operation during the entire filling operation for example changing the batch setup or any machine setup these activities will directly impact the contamination of the clean room were preparing for the filling. so the monitoring may be with different other connection limits but also the preparation must be included in the continuous monitoring activity. grade B normally surrounding grade a must be monitored daily as well as the grade C which has to be monitored weekly and the great D is not mainly required.
4 Types of CleanRoom Classification in Pharmaceutical
- ISO 14644-1 Cleanroom
- FS (Federal standard) 209 E
- EU (Europian Union)
- BS (British Standard) 5295
Clarification of Different Cleanroom Classifications
|ISO Classes| |EU GMP| |F.S. Standred| |
ISO 5 Grade A Class 100 |
ISO 6 Grade B Class 1000 |
ISO 7 Grade C Class 10,000 |
ISO 8 Grade D Class 100,000 |
1. ISO 14644-1 Cleanroom classification
(International Organization for Standardization) ICH class starts from class 1 to class 9 as described in the Table below. Although class 5 to class 8 are widely used in pharmaceuticals. ISO Class 1 is the most cleaned, If talk about which class is the cleanest class in pharmaceuticals and class 9 is less cleaned.
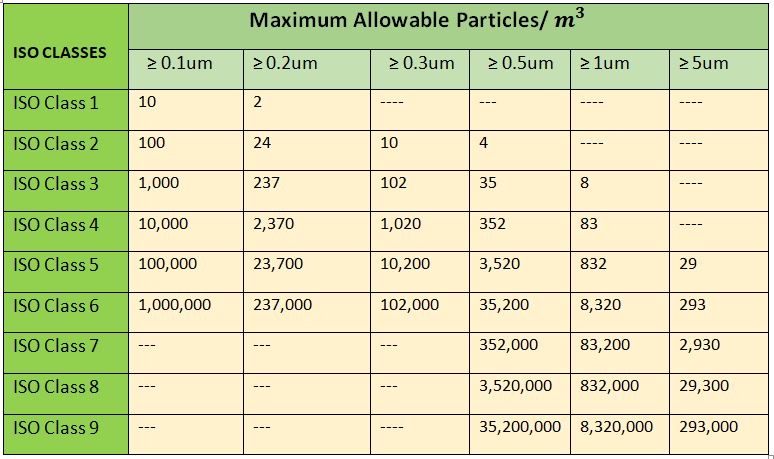
2. FS (Federal standard) 209 E Cleanroom classification
Federal standards described the cleanroom classification as follows:
- Class 100
- Class 1000
- Class 10,000
- Class 100,000
Related: Air Change Per Hour (ACPH) Calculation
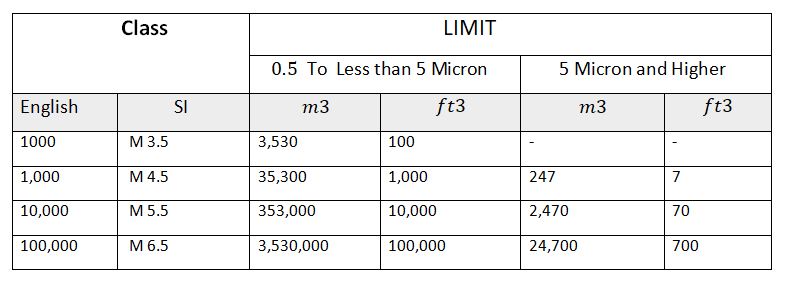
Note: New international standards legally replace Federal Standard 209E with ISO 14644-1, in November 2001, although some companies still use it.
3. EU (Europian Union) Cleanroom classification
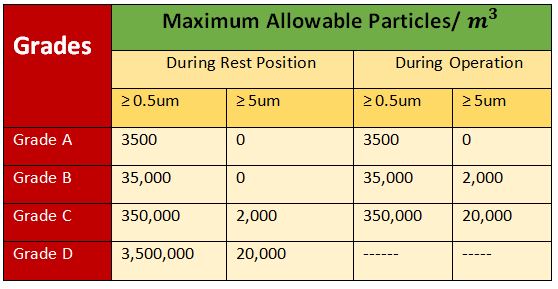
4. BS (British Standard) 5295
For the purpose of defining clean rooms and classifying them, the BSI provides the BS 5295 standard. They separated clean rooms into 10 categories in order to categorize them. However, BS 5295 has been replaced by ISO 14644-1, much like FED STD 209E.
Formula use for Cleanroom classifications
Cn= 10n x (0.1/d)2.08
where,
N – ISO Class number
D – Particle Diameter, or size of the particle
Cn – Maximum concentration (Particles per m3) 0.1- is constant
Risk Assessment for cleanrooms:
Risk assessment is an essential part of any clean room management and a clean room monitoring plan is essential for implementing a compliant monitoring plan for the goal of the risk assessment. When developing a risk assessment are needed to understand your process which is the critical areas and locations.
To correctly select the sample location which is the possible source of contamination not only from the human activities in the clean room but also other elements or even that may compromise the clean room performance compromising the clean room performance will affect the product quality and as well as the patient but will also negatively affect the operation cost for your company.
Important Documents for Cleanroom Risk Assessment:
ICH Q9 provides probably the best guidelines for a proper risk assessment. The development of another useful resource is represented by the PDA (parental drug association) which has technical report number 13 which is titled fundamental of the environmental monitoring program.
These also addressed the meaning of the means and the need for a meaningful manageable and defensible monitoring program, other resources also recommended by the ISO are represented by the HACCP which is normally applied to the food manufacturing side but also gives you a lot of interesting information about the correct way to set up to create a risk assessment as well as risk assessment development.

Naresh Bhakar is the Founder and Author at Pharmaguddu.com, bringing his extensive expertise in the field of pharmaceuticals to readers worldwide. He has experience in Pharma manufacturing and has worked with top Pharmaceuticals. He has rich knowledge and provides valuable insights and data through his articles and content on Pharmaguddu.com. For further inquiries or collaborations, please don’t hesitate to reach out via email at [email protected].