1.0 OBJECTIVE: To lay down a procedure for online inspection of washed empty / filled/labeled bottles during Liquid Orals filling and packing operation.
2.0 SCOPE: This procedure is applicable for online inspection of washed empty / filled/labeled bottles of all the Liquid dosage forms in Pharmaceuticals.
3.0 RESPONSIBILITY: Operator, Officer, Executive – Production Department
Manager – Production Department
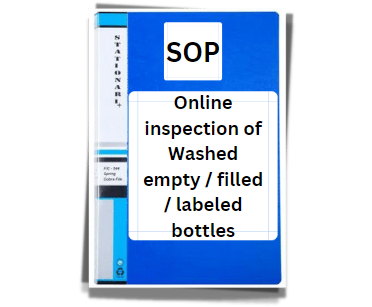
4.0 PROCEDURE:
4.1 Washed Empty Bottles:
4.1.1 Switch ‘ON’ the tube light of the empty bottle inspection unit.
4.1.2 Receive the washed empty bottles on the empty bottle inspection unit from bottle washing machine through turn table and attached conveyor.
4.1.3 Ensure that there is no water remaining in the bottles.
4.1.4 Check the bottles against the white tube light background for the following defects:
- Cracked bottles
- Deformed bottles
- Foreign particles
- Air bubble
- Embedded particles
4.1.5 Record the inspection time and rejection details in respective BPR.
4.1.6 Destroy the rejected bottles.
4.2 Filled Bottles:
4.2.1 Operate the filled bottle inspection unit as per the “inspection unit for empty and filled bottle” SOP.
4.2.2 Receive the filled bottles on visual inspection unit from bottle filling & sealing machine through attached conveyor.
4.2.3 Check the bottles against the black & white background for the following defects:
- Low and high fill volume.
- Defected cap sealing of filled bottles.
- Foreign particles in filled volume.
4.2.4 Record the inspection time and rejection details in respective BPR.
4.2.5 Destroy the rejected bottles and reprocess the bottles.
4.3 Labeled bottles:
4.3.1 Receive the labeled bottles from sticker labeling machine on attached conveyor.
4.3.2 Check the following details, during the online inspection of labeled bottles:
- Correct and legible coding
- Cross labeling
- Coding details on bottle label i.e. B.No. Mfg. Date, Exp. Date, Retail Price.
- A problem in printed matter
4.3.3 Record the observation and accountability in BPR
4.3.4 Reprocess the Defective bottles online inspection of labeled bottles
5.0 ABBREVIATION:
SOP: Standard operating procedure
No. : Number
BPR: Batch packing Record
6.0 DISTRIBUTION:
Master copy: Quality Assurance
Controlled copy ( s): Production department
Reference copy (s): Production department

Naresh Bhakar is the Founder and Author at Pharmaguddu.com, bringing his extensive expertise in the field of pharmaceuticals to readers worldwide. He has experience in Pharma manufacturing and has worked with top Pharmaceuticals. He has rich knowledge and provides valuable insights and data through his articles and content on Pharmaguddu.com. For further inquiries or collaborations, please don’t hesitate to reach out via email at [email protected].