There are various Autoclave Qualification Tests that need to be done along with procedure and acceptance criteria. Autoclave works by using heat and pressure to kill the microorganisms such as bacteria and spores so it becomes very crucial or very important equipment for sterilization processes
In this article we will go through the few prerequisites for the operational qualification test and then operational qualification tests such as the Bowie-Dick test, air leakage test, Air detected test, sound power test, steam quality test, thermometric test, and microbiological tests.
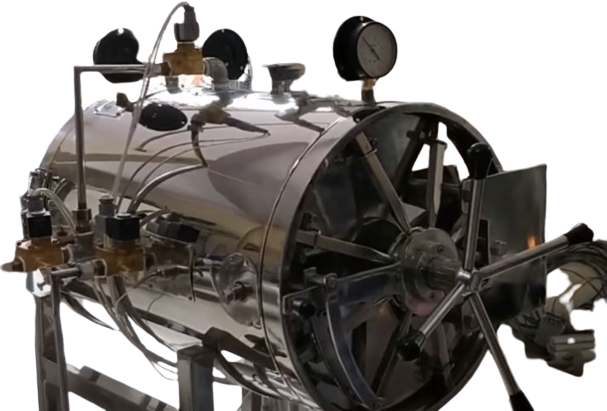
Prerequisites for Autoclave Qualification Tests
There are a few pre-checks on the prerequisites for the operational qualification test if the sterilizer has been provided and installed properly. is the sterilizer safe to work? is the sterilizer not interfere with adjacent equipment? and are all connected services suitable?
1. BOWIE-DICK TEST: Check our full article on the Bowie dick test
2. LEAKAGE TEST: An air leakage test for autoclave chambers is done to find out any leakage from the chamber. Air leakage test is used to establish that the quantity of air leakage into the sterilizer chamber during the period of vacuum does not exceed the level. air leakages will obstruct the penetration of steam into the sterilizer load and the presence of the air leakages will pose a potential risk of decontamination to the sterilizer.
Procedure: Tested pressure gauges shall be used to check pressure indicating a recording instrument. stabilize the temperature of the sterilizer chamber with sterilization cycle with the empty sterilized chamber. When the pressure in the sterilizer chamber is 70 millibars absolute or 7 kilopascals or below close all the walls connected to the sterilizer chamber and stop the vacuum pump. Observe and record the time and absolute pressure and wait for at least 300 ±10 seconds to allow evaporation of condensation in the chamber and then observe and record the absolute pressure in the sterilizer chamber and the time, after a further 600 ±10 seconds, again observe and record the absolute pressure and time.
Acceptance Criteria for a leakage test: if the chamber is leaked then the pressure inside will go on rising so the acceptance criteria for a leakage test is the rate of pressure rise shall be not greater than 1.5 millibars per minute or 0.13 kilopascal per minute.
3. AIR DETECTOR TEST: The purpose of the air detector test is to determine whether non-condensable gases contained in the steam delivered to the sterilizer and the remaining air after the air removal stage of the sterilization cycle are sufficient to cause the sterilization process.
Procedure for air detector test: To perform the air detector test connect the metering device to a Sterilizer chamber using a Valved port provided by the manufacturer prior to starting the air detector test. ensure that the Bowie Dick test and air leakage test are passed for the sterilizer. this test is needed to be carried out with the empty sterilizer chamber.
Acceptance criteria: Acceptance criteria for the air detector test is that the probe located in the center of the load must not be depressed by more than 2 °C once the drain achieves the sterilization conditions.
4. SOUND POWER TEST: A sound power test is done to ensure compliance with the requirement of peak sound produced by the sterilizer and to ensure that the level of weighted sound power is known and obtainable by national legislation that controls the supposed noise or the sound pressure in the working environment.
Test Procedure: To perform the sound power test, locate the microphones in the identified locations. then determine the environment correction factor k and the sterilizer containing the test load performs the test, ensuring that the pressure and the flow from the steam and the water services are set to the levels which cause the maximum noise and are within the range specified for the sterilizer.
Acceptance criteria: Acceptance criteria for the sound power test the peak volume or the sound level generated by the autoclave is should not be more than 70 dB. No maximum value of a weighted sound power level shall exceed a mean weighted sound power level by more than us 15 dB.
5. STEAM QUALITY TEST: The steam quality test is performed to ensure the quality of steam that is provided to the sterilizer is as per the acceptance criteria. in this test, we check the non-condensable gases superheat and dryness must pass to support sterility.
Acceptance criteria: Acceptance criteria for the steam quality test are that non-condensable gases shall not be more than 3.5% and dryness shall be greater than or equal to 0.90 or greater than or equal to 0.95 for metal loads. superheat test passes if the superheat measured in the expansion tube does not exceed 25 °C.
6. THERMOMETRIC TESTS: The purpose of the thermometric test is to demonstrate that after the air removal stage of the sterilization cycle, the sterilizing environment is obtained within the sterilizer chamber and the standard test pack.
Procedure: for the thermometric test as per the PDA’s technical report number 1 minimum of 10 thermocouples or 5 thermocouples per 100 cubic feet shall be used, whereas as per the HTM 2010 (now known as EN285) 12 thermocouples and more than one pressure sensor shall be used during validation cycle. Introduce the temperature sensors into the sterilizer chamber through the temperature sensor entry connection and fitting. place one of the temperature sensors either in the active drain to a depth of at least 10 mm or at a reference measurement point. carry out the sterilization cycle with the empty sterilizer chamber.
Acceptance criteria: For the thermometric test, it is essential to achieve 121°C for each thermocouple for a predefined time period of 15 minutes. the difference between the temperature and thermocouple should not be more than 3°C that are all the thermocouples must have a temperature between 121°C to 124°C during the entire sterilization cycle.
7. MICROBIOLOGICAL TEST: Microbiological test is done to get the stability assurance for sterilization processes done by the autoclaves. spore testing provides a reliable method for sterility assurance. so for this bacillus stearothermophilus spores are most commonly used due to their resistance to heat, for testing purposes it measures the biological performance of the autoclave processes.
Procedure: For microbiological tests, it is recommended that at least two spore ampules of bacillus stearothermophilus are used per cycle. Place the spore ampules in a horizontal position inside the biohazardous bag with the representative materials to be sterilized. Select the appropriate cycle to process the load. Once the cycle is completed allow the autoclave to decompress and cool down and remove the load from the autoclave and allow it to further cool down for 10 to 15 minutes.
Retrieve the spore test ampules from the load and incubate them in an adjacent microbiological incubator at a temperature of 131 Fahrenheit to 140 Fahrenheit (55 to 60°C) for incubation, take both ampoules from the load that was autoclaved. Gently squeeze the plastic crusher to break the samples and place those in the incubator. Take a third spore Labeled as a “control ampule” which is not placed in the autoclave chamber. Proceed to break the glass ampoules and also incubate this in the same incubator allow the incubation and verify all three spore ampules after 24 hours.
Acceptance criteria: Examine the indicator ampules for any color change after 8, 12, 18, and 24 hours. the presence of a yellow color change indicates a failed test and positive bacterial growth, no color change indicates passing the test and proper sterilization of the sample the control ampule should produce a yellow color change.
Conclusion:
In summary, these are the key Autoclave Qualification Tests that are done to check the working efficiency.
Reference: GMPua BRITISH STANDARD BS EN 285:1997

Naresh Bhakar is the Founder and Author at Pharmaguddu.com, bringing his extensive expertise in the field of pharmaceuticals to readers worldwide. He has experience in Pharma manufacturing and has worked with top Pharmaceuticals. He has rich knowledge and provides valuable insights and data through his articles and content on Pharmaguddu.com. For further inquiries or collaborations, please don’t hesitate to reach out via email at [email protected].