Propellers are mechanical devices that are used to mix liquid materials by using blades. A propeller normally contains a number of blades A three-bladed design is generally used The marine type propeller is similar to the blades of a table fan or ceiling fan. They may be either right or left-handed depending on the direction of slant of their blades Four bladed or toothed or similar design propellers are used for special purposes. In a deep tank, a push-pull propeller is used, in which two or more propellers may be attached to the same shaft These propellers work in opposite directions to create a zone of high turbulence The propeller produces axial movement of the liquid.
Principle:
The principle behind a propeller is the conversion of rotational motion into thrust, which allows it to transmit power. The blade’s airfoil shape creates a pressure difference between its forward and rear surfaces, resulting in the acceleration of fluid behind the blade. The propeller generates thrust, which is then transmitted through the main shaft and the propeller itself to move the liquid.
Construction of Propellers:
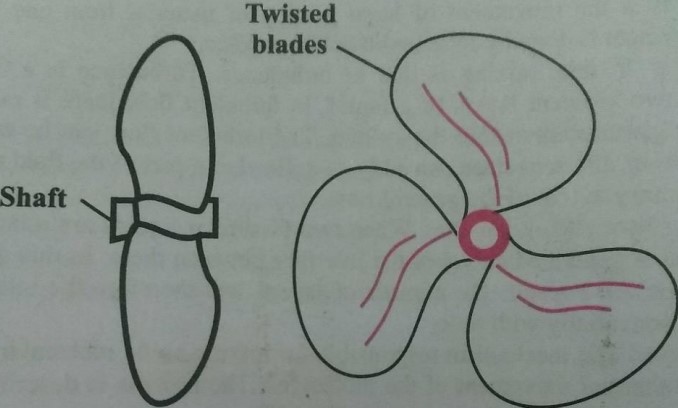
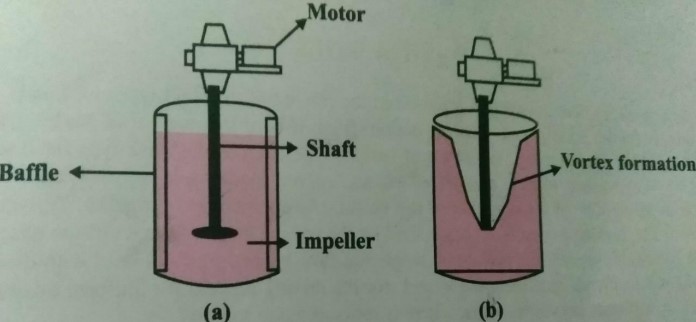
The construction of a propeller involves a vessel equipped with the propeller. The vessel is made of stainless steel grade 316L. It possesses a curved or flat bottom and maintains a height-to-width ratio of 1.5:1. A cooling jacket covers the vessel to provide improved temperature control. Propellers consist of multiple blades attached to the shaft, with a common design featuring 3 to 6 blades for liquid mixing. The blades can have a right or left-handed orientation. In large and deep tanks, two or more propellers may be used for proper mixing. The propeller size is generally small but can be increased up to 0.5 m, depending on the tank’s depth. Typically, the propeller diameter ranges from 0.13 to 0.67 times the tank diameter. Small propellers can rotate at speeds of up to 8000 r.p.m., producing longitudinal movement. Radial agitators, similar to marine propeller, consist of propeller with two to four blades that move in a screw-like motion, propelling the material parallel to the shaft for agitation. Propeller agitators are designed with blades tapering towards the shaft to minimize centrifugal force and maximize axial flow. They are commonly employed for simple mixing applications.
Related: Ribbon Blender
Working of Propellers:
When operating, the liquid to be mixed is pumped into the mixing vessel. Once the propeller starts rotating, the propeller blades’ centrifugal force creates a vortex, causing the liquid to back up around the vessel’s sides and creating a depression at the center around the shaft. The flow patterns induced by propellers are axial and can be directed towards the top or bottom of the vessel, depending on the direction of rotation (clockwise or anticlockwise). As the rotation speed increases, a vortex may suck air into the fluid. However, this vortex formation can be reduced by using baffles positioned vertically within the vessel. Vertical propeller mixers typically comprise three blades of suitable size based on the vessel’s diameter. Side-entry mixers can employ horizontal, inclined, or marine propeller. Inclining the propellers on the impeller shaft improves mixing and provides excellent blending capability for small batches of low to medium-viscosity liquids.
Advantages of Propeller:
- Effective for high mixing capability.
- Suitable for liquids with a maximum viscosity of 2 Pa.s.
- Effective for mixing gas-liquid dispersions at a laboratory scale.
- Increases material homogeneity.
- Can be used for drying and pressing processes.
Disadvantages of Propeller:
- Ineffective with liquids of viscosity greater than 5 Pa.s.
- Need high speed to avoid solid settlings in reactor vessels.
- Require low speeds if drying is an additional objective.
- Vortex formation can cause frothing and oxidation.
Application
Some common applications of propeller mixers include:
- Chemical industry
- Pharmaceutical industry
- Food and beverage industry
- Paint and coating industry
- Cosmetics industry
Conclusion
In conclusion, propellers play a vital role in mixing operations, particularly for liquids with low viscosity.
Related: Sigma Blade Mixer for Mixing
FAQs on Propellers
Propellers are mechanical devices that are used to mix liquid materials by using blades
Propeller mixers operate on the principle of shearing force, which facilitates the blending of liquids by inducing fluid circulation in both axial and radial directions.
A propeller mixer consists of a vessel and a propeller. The propeller has angled blades that cause fluid circulation within the vessel, ensuring effective mixing.
The size of the propeller depends on the dimensions of the tank. Propellers can range from small sizes to larger ones measuring up to 0.5 meters.
When the propeller blades impart centrifugal force to the liquid, a vortex is formed, circulating the fluid and creating a depression at the shaft. However, vortex formation can be reduced by installing vertical baffles in the vessel.
Propeller mixers are effective when a high mixing capacity is required. They offer efficient blending, a wide range of propeller sizes, and suitability for various tank sizes and applications.
Propellers are not effective for liquids with a viscosity greater than 5.0 Pascal second. Additionally, propeller mixers can be costlier compared to alternative mixing methods.
Propeller mixers are commonly used in industries such as chemicals, pharmaceuticals, food and beverages, paints and coatings, and cosmetics. They are suitable for mixing low-viscosity emulsions and suspensions with specific particle sizes.

Naresh Bhakar is the Founder and Author at Pharmaguddu.com, bringing his extensive expertise in the field of pharmaceuticals to readers worldwide. He has experience in Pharma manufacturing and has worked with top Pharmaceuticals. He has rich knowledge and provides valuable insights and data through his articles and content on Pharmaguddu.com. For further inquiries or collaborations, please don’t hesitate to reach out via email at [email protected].