1.0 Purpose: To lay down the procedure for packing vials.
2.0 Aim: This Standard Operating Procedure is applicable for packing vaccine vials in the Packing Section.
3.0 Responsibility: 3.1 Trained operators and casual workers shall be responsible for packing activity.
3.2 Officer/ Senior officer of Production shall be responsible for checking the activity.
3.3 IPQA person shall be responsible for compliance as per SOP.
3.4 Head Quality Assurance/designee shall be responsible for the authorization of the SOP.
4.0 Equipment:
4.1 Manual visual inspection table
4.2 Label printing and rewinding machine
4.3 Label pasting machine for vials
4.4 Cold room
4.5 Weighing balance
4.6 Carton coding machine
4.7 Deep Freezer
5.0 Materials and reagents:
5.1 Approved mono cartons
5.2 Approved packing inserts
5.3 Approved shippers (3-ply / 5-ply)
5.4 Approved outer cartons
5.5 Tape roll 12 mm
5.6 48 mm printed BOPP tapes (With company Logo if Applicable)
5.7 Approved Self-adhesive labels for vials/ carton labels
5.8 Approved VVM Dot labels (if required)
5.9 Packer slip
6.0 Procedure Procedure for Packing Vials:
Note: Packing activity shall be done for R&D and commercial Batches of vaccine vials
as per the below detail:
7.1 Visual inspection of vials:
7.1.1 Receive the required quantity as per packing plan on the requisition of semi-finished goods receive a note from Warehouse through a pass box and store it in a cold Room.
7.1.2 Take out the required quantity of filled vials from cold Room and carry out the manual visual inspection.
7.1.3 Record the detail of visual inspection in the logbook and BPR.
7.2 Labeling of vials:
7.2.1 Take the required quantity of labels from the label store cabinet (secondary packing material store) which are already printed on label printing and rewinding machine.
7.2.2 Carry out the labeling of visually inspected and accepted vials after cleaning and taking the line clearance from IPQA person.
7.2.3 Carry out the VVM Dot labeling (If required) on vials.
7.2.4 Record the detail of label printing and labeling of vials in respective logbooks and BPR.
7.3 Packing of vials in mono cartons and outer carton/ jali carton / E-flute carton packing and printing as follow:
7.3.1 Take approved package insert (if required) and mono cartons from the secondary packing material store and transfer them to carton packing workstation and note the quantity in BPR.
7.3.2 Fold and close one end of the mono-carton flap manually.
7.3.3 Pack the vials in a carton.
7.3.4 Place the packing insert in the carton (if required).
7.3.5 Close the open flap to form completely closed mono cartons.
7.3.6 If printed cartons are used carry out the coding of mono cartons/outer cartons (if required) or paste/ apply the carton labels which are already printed on label printing m/c.
7.3.7 Collect the printed mono cartons /outer cartons.
7.3.8 Transfer these mono cartons to the outer carton or outer carton in the shipper.
7.3.9 Carry out the batch coding of outer cartons (if required).
7.4 Packing of outer cartons in 5-ply shipper:
7.4.1 Pack the outer cartons in a 5-ply shipper on which the detail of batch is already mentioned or if not mentioned, a label should be pasted with the below-mentioned detail:
(a) Name of product
(b) Batch No.
(C) Mfg. Date
(d) Exp. Date
(e) Quantity of vials per box
(f) Box No.
7.4.2 Weigh each shipper on weighing balance, check the maximum-minimum weight limit, and fill in the detail of weight on the shipper weighting record as per Annexure-2
7.4.3 Cheek the number of packed vials in shipper and fill the Annexure -2 for transfer of packed vaccines to the Warehouse with cross-checking and signed by an IPQA person.
7.4.4 Transfer the material through the pass box to WH with FGTN as per Annexure-2.
7.4.5 After the receiving and confirmation of the quantity of material and FGTN by the store in charge of WH attach its duplicate copy in BPR.
7.5 Record all packing activity hourly as per Annexure -1
7.5.1 Packing activity status should be recorded hourly on the in-process checklist as per Annexure -1.
8.0 Distribution:
Master copy -Archived with Quality Assurance Department
Controlled Copy 1 -Production Department
Subsequent controlled copies -Department (s) making the requisition
Related: Receiving and Transfer the FGTN to Warehouse
9.0 Abbreviations:
HOD: Head of the Department
ID No. : Identification number
No. : Number
SOP: Standard Operating Procedure
VFP: Vaccine Formulation Plant
BPR: Batch Processing Record
SFGRN: Semi-Finished Goods Receiving Note
WH: Warehouse
Annexures:
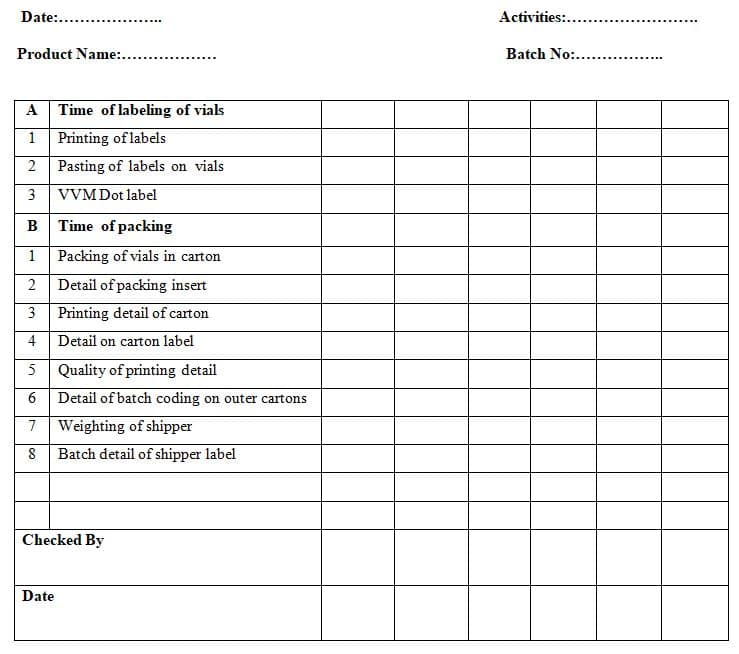
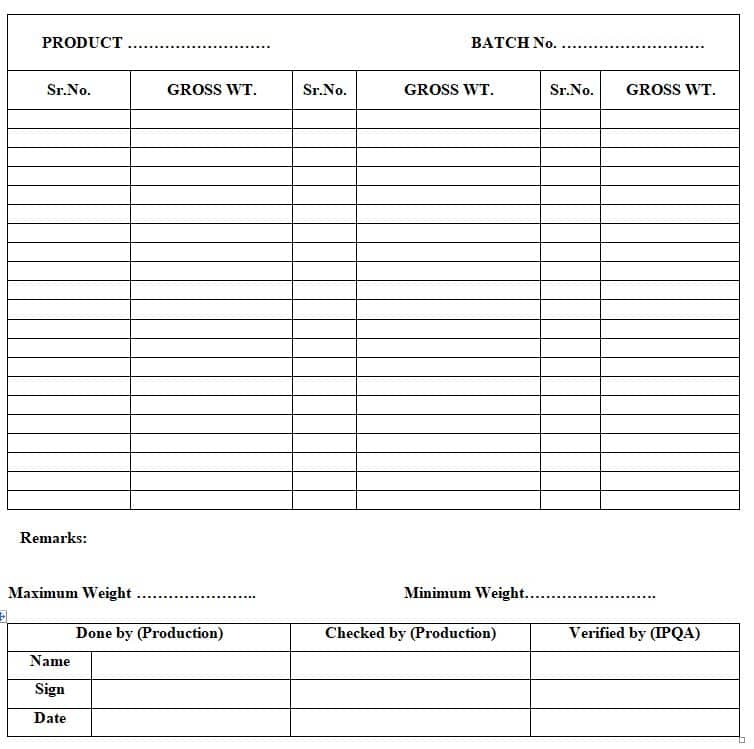

Naresh Bhakar is the Founder and Author at Pharmaguddu.com, bringing his extensive expertise in the field of pharmaceuticals to readers worldwide. He has experience in Pharma manufacturing and has worked with top Pharmaceuticals. He has rich knowledge and provides valuable insights and data through his articles and content on Pharmaguddu.com. For further inquiries or collaborations, please don’t hesitate to reach out via email at [email protected].