An uncontaminated environment is essential in pharmaceutical manufacture. Clean rooms created with strict ISO guidelines are engineered with the intent of reducing particulate and microbial contamination in drug manufacturing processes. However, microbial contamination may still be present owing to inadequate cooling, cleaning regimens, or even both. These controlled environments must comply with regulations which means that sanitation must be met. Fumigation serves as a crucial decontamination technique. The article reviews the validation of fumigation processes in pharmaceutical cleanrooms and discusses in detail the fumigation process and its challenges as well as their compliance.
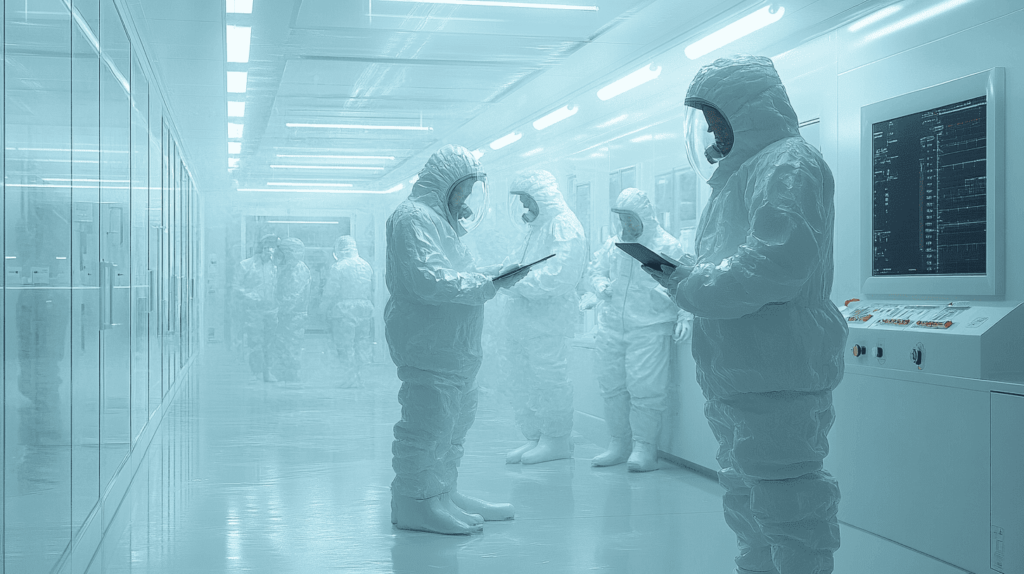
The Role of Clean Rooms in Pharma
Clean rooms are divided into categories ISO 1 through ISO 9 according to the number of allowable particles per cubic meter. These environments are crucial for the manufacture of all sterile products such as injectables, vaccines, and biologics. Contamination risks—either via airborne microbes, personnel, or equipment—can endanger products leading to recalls or patient injuries. Therefore, routine fumigation is required to destroy residual microorganisms.
Why Fumigation?
Despite air filtration and cleaning, microbes can persist. Fumigation eliminates resilient pathogens, including spores, fungi, and bacteria, using gaseous agents. It’s employed during routine maintenance, post-construction, or after contamination incidents.
Common Fumigation Methods
- Hydrogen Peroxide Vapor (H2O2):
- H2O2 is Non-carcinogenic and breaks down into water and oxygen.
- It is Effective against a broad spectrum of microorganisms.
- Formaldehyde Gas:
- Formaldehyde is Traditional but less favored due to toxicity, Carcinogenicity, and residue concerns.
- It Requires thorough aeration post-treatment.
- Chlorine Dioxide:
- It is used for rapid decontamination, especially in isolators.
Validation of Fumigation: A Step-by-Step Approach
Validation ensures the fumigation process consistently achieves a 6-log reduction in microbial load. Key phases include:
1. Development of the Protocol:
A validation master plan is used to have a systematic outline of objectives, methods, and acceptance criteria. It is done in accordance with GMP, FDA, and ISO regulations.
2. Development of the Cycle
Dosage Calculation: Fix concentration of fumigant and time of exposure.
Distribution Studies: Monitor the use of chemical indicators (CIs) to make sure that the gas is not only emitted but also evenly dispersed.
3. Microbial Testing
Biological Indicators: Place Bacillus atrophaeus or Geobacillus stearothermophilus for critical area (H2O2 or formaldehyde).
Fumigation Post Sampling: Perform swabbing on selective surfaces and the air sampling to check for sterility.
4. Equipment Qualification
- Installation Qualification (IQ): The installation of the fumigation apparatus must be checked accurately.
- Operational Qualification (OQ): Analytical calculation of equipment operational capacity is done while the piece of equipment is in operation.
- Performance Qualification (PQ): Confirmation of a process being performed during normal functioning activities.
5. Documentation & Reporting
All parameters (temperature, humidity, gas concentration), test results, deviations were recorded and are kept for audit purposes.
6. Requalification
Effective periodic requalification e.g. every annum or following any alterations to the facility.
Regulatory Compliance
Pharma companies must adhere to:
- FDA 21 CFR Part 211: Sterility of the drug product requirements.
- ISO 14698: Control of biocontamination.
- EU GMP Annex 1: Strategy for contamination control.
Challenges & Solutions
- Resistant Microbes: Employ sporicidal agents and ensure adequate contact time is achieved.
- Safety Risks: Put on fully encapsulating PPE when working with H2O2 and install gas detectors where appropriate.
- Environmental Impact: Use environmentally friendly agents like H2O2 and work in a ventilated environment.
Conclusion:
The evaluative process of clean room fumigation methods is very rigorous and scientific because it has to be certified that product safety is ensured. This can easily be achieved through adherence to set standard procedures, introduction of new fumigants, and general compliance, which are meant to be adopted by the pharmaceutical companies so as to reduce contamination. Periodic inspections and employee retraining create a strong quality culture for product and patient safety.
Final Thoughts:
Same as regulations, so do the strategies for fumigation. The adoption of new methods and constant adjustment of the old ones guarantee the cleanliness of clean rooms, which is essential for the pharmaceutical industry.

Naresh Bhakar is the Founder and Author at Pharmaguddu.com, bringing his extensive expertise in the field of pharmaceuticals to readers worldwide. He has experience in Pharma manufacturing and has worked with top Pharmaceuticals. He has rich knowledge and provides valuable insights and data through his articles and content on Pharmaguddu.com. For further inquiries or collaborations, please don’t hesitate to reach out via email at [email protected].