Contamination and cross-contamination are terminologies used in the pharmaceutical industry when products undesirably come into contact with or mix with other products or their parts. Contamination can occur in starting materials or products due to contact with other related products. The risk of accidental contamination may arise from the uncontrolled release of dust, gases, particles, vapors, sprays, organisms, in-process products in the area, residues on equipment/operator clothing, and skin. The significance of contamination risk varies depending on the type of contaminants and the product being contaminated.
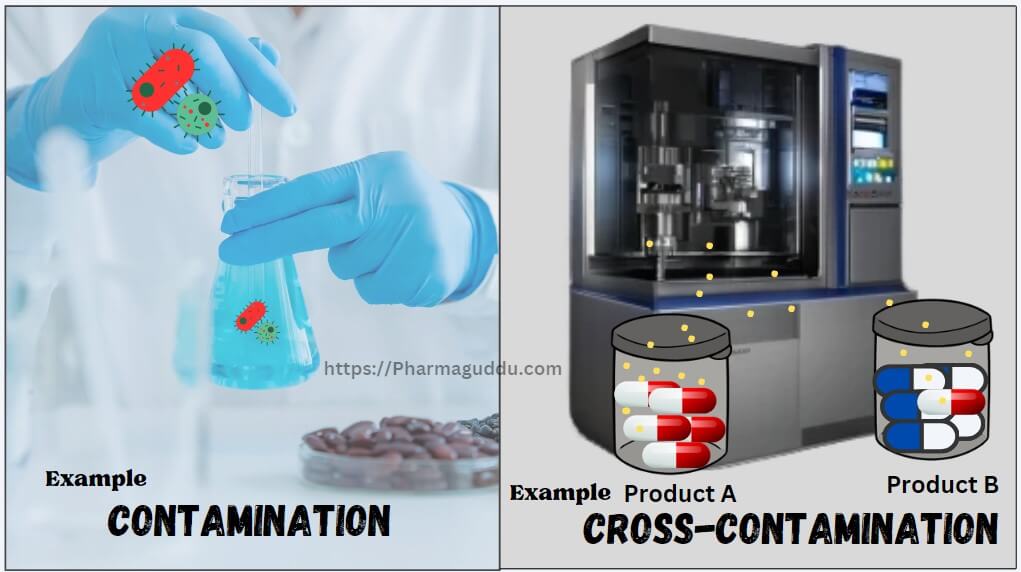
In this article, we will learn about contaminants, contamination types, and cross-contamination in pharmaceutical manufacturing sites. Let’s start with defining contaminants, contamination types, and cross-contamination.
What is Contaminants?
Contaminants: Contaminants can be impurities, products, or substances unrelated to the manufactured product, such as foreign products, particulate matter, microorganisms, and Endotoxin (which degrades microorganisms). Cross-contamination of products can also lead to contamination.
The People/machine-generated contaminant Examples:
- The human outer skin is completely shed every 24 hours.
- Particles of 0.3 microns and greater are liberated at a rate varying between 100000 to 10 million per minute.
- A person while walking will liberate thousands of bacteria per minute, and a single sneeze can produce up to 1 million bacteria.
- The manufacturing process itself can generate contaminants, for example, paint from equipment, dust from belt drives, etc.
What is Contamination?
Contamination: Contamination occurs when chemicals, microbial substances, or foreign matter are unintentionally introduced into or onto a starting material/intermediate during production, Sampling, Packaging/ Repackaging, storage, and Transport.
Types of contamination with Examples:
- Chemical contamination (leftover residue of the previous process).
- Microbiological contamination ( microbiological flora).
- Particulate contamination ( particles like dust, fibers, oil, or grease from the pieces of equipment. others like haires, and skin fragments).
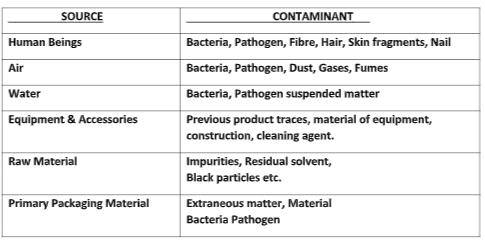
What is Coss-Contamination?
Cross-contamination contaminates the starting, intermediate, or finished products with other materials during production.
Source of cross-contamination generated?
- It may be due to poor design and operation of air handling systems and dust extraction systems.
- Inadequate procedure for personnel and equipment.
- Not proper cleaning of equipment.
How to minimize Cross-Contamination?
- cross-contamination may be minimized by using closed production systems.
- Applying a cleaning validation procedure.
- By maintaining the level of a product that is being manufactured.
- Adequate premises.
- Installing correct air pressure Airlock types systems like; Cascade airlock.
Way to control Dust in pharmaceuticals:
Dust control is important for controlling contamination and cross-contamination in pharmaceutical manufacturing areas. Whenever possible, promptly remove dust or vapor contaminants by identifying their source.
Design a dust extraction system with adequate transfer velocity to ensure effective dust removal. Carefully select the airflow direction to prevent production process contamination. Utilize well-validated HEPA filters in series for added protection. Consider installing a sophisticated computer-based data monitoring system.
Drawback of Contamination Hazards in Pharmaceuticals
Pharmaceutical manufacturers are required to the validated cleaning procedure, AHU system, air cascade, and personnel movements to ensure the production of good quality products throughout their life cycle. Failure to prevent contamination and cross-contamination can lead to a loss in customer faith or satisfaction from the investors, loss of market values, loss in money, and direct consequences from regulatory bodies.
Conclusion:
The system or equipment shall be validated to prevent the Product from contamination and cross-contamination. Cleaning validation of equipment and area with a well-defined procedure shall be maintained. Using the cleaning validation approach, we can easily identify any discrepancies or loops in a system.

Naresh Bhakar is the Founder and Author at Pharmaguddu.com, bringing his extensive expertise in the field of pharmaceuticals to readers worldwide. He has experience in Pharma manufacturing and has worked with top Pharmaceuticals. He has rich knowledge and provides valuable insights and data through his articles and content on Pharmaguddu.com. For further inquiries or collaborations, please don’t hesitate to reach out via email at [email protected].