1.0 OBJECTIVE: 1.1 To define SOP on Change Control to be made in the authorized documents, validated methods, process, procedures, facilities, and equipment.
2.0 RESPONSIBILITY
2.1 Assistant / Chemist / Executive – To initiate the Change Control Form.
2.2 Respective Department Head – To evaluate and justify the required change.
2.3 Other Departments Heads – To review and comment on the proposed changes and to ensure the respective changes.
2.4 Change Control Coordinator – To evaluate and conclusions for Change
(QA In-charge) Request Form against appropriate guidelines, industry practices, and cGMP compliance
2.5 Head QA &RA – To approve / Reject the changes.
3.0 PROCEDURE FOR SOP ON CHANGE CONTROL
3.1 The SOP on change control shall be followed if any of the following changes are required but not limited to:
- Changes requesting an additional or alternate source of raw materials and packaging materials
- Changes in manufacturing procedures.
- Change in product color, shape, and size.
- Change in packaging and labeling.
- Changes to process and or testing equipment.
- Changes to qualified facility or utilities.
- Changes to Master Production / Packaging Records
- Changes to approved procedures like SOP Specifications, STPs, and GTPs.
3.2 Whenever a change becomes necessary or desirable the concerned Assistant / Chemist / Executive prepares a “Change Control Form” (Annexure-1) outlining the proposed change and the reason for the change, attaches supporting documents, if any, and forwards it to the Department Head.
3.3 Respective Department Head shall thoroughly evaluate the “Change Control Form” against the established procedures and policies and forward it to the Change Control Coordinator.
3.4 Change Control Coordinator shall categorize the changes that require Regulatory Department Review required.
3.5 The categorization shall be done as follows:
- Category “A”- No Regulatory Impact
- Category “B” – Minor Changes that require notification to the Regulatory Affairs
- Category “C” – Major Changes that require approval from the Regulatory Affairs
3.6 Change Control Coordinator identifies and forwards the change control form to other departments whose comments are required against the proposed changes.
3.7 The other departments / Regulatory Affairs shall forward the filled change control form to the Change Control Coordinator.
3.8 Change Control Coordinator shall evaluate the proposals and give comments and conclusions on the “Change Control Form”.
3.9 If the evaluation is found satisfactory, the Change Control Coordinator shall forward the “Change Control Form” to Head QA & RA for final conclusions and recommendations.
3.10 Head QA & RA finally decide upon the acceptance or rejection of proposed changes.
3.11 If the proposed change is not acceptable to either Department Head/Change Control Coordinator or Head QA &RA, the reason for rejection shall be written in Change Control Form and shall be returned to DC.
3.12 Upon the acceptance by the Head – QA & RA, the Documentation Controller shall allot a unique, sequential Number to the Change Control Form.
3.13 Change Control Number shall consist of 11 characters.
3.14 The first two characters are department codes indicating the department from where the Change Control Form originated. The department codes are given in Annexure – 3.
Note: Only Engineering and Process Development & Technology Transfer shall have three characters as “ENG” & “PDT” respectively.
3.15 The third Character is a “/” (slash).
3.16 Fourth and fifth characters denote “DC” for document change and for “FC” for facility change.
3.17 Sixth, seventh, and eighth characters indicate the serial numbers starting from “001” on every new year (from 1st January).
3.18 The Ninth character is a “/” (slash).
3.19 The last two characters are numerical indicating the year.
Example: The first change control number raised in the Year 2022 by Production Department shall be numbered as:
- PR/DC001/22 (for Document Change)
- PR/FC001/22 (for facility Change)
3.20 After allocating the number of Change Control Forms, DC shall identify the documents affected by the accepted change, and the same details shall be entered into Change Control Form.
3.21 The Change Control Form shall be forwarded Change Control Coordinator for approval of the accepted change.
3.22 Change Control Coordinator shall identify the requirements of Training / Validation / Stability Studies based on the accepted changes.
3.23 Based on the requirements Documentation Controller shall coordinate with Validation / Stability Testing/training departments etc for completion.
3.24 After fulfilling the above requirement, the Change Control Coordinator shall review the completion of accepted changes and record the effective date and status of disposition of the raised change control form.
3.25 Documentation Controller shall fill out the Change Intimation Form (Annexure-5) and circulate it to all department In-Charges.
3.26 The details of the Change Control Form shall be recorded in a “Change Control Log ” as given in Annexure – 4 by Documentation Controller.
3.27 Documentation Controller shall file the approved and completed Change Control Form along with the supportive document.
- This procedure is only applicable to all planned changes and continuous deviations.
- This procedure is not applicable to routine breakdown, calibration, and planned preventive maintenance activities.
Related: SOP for acceptable quality level in Pharma
4.0 ABBREVIATIONS
QA – Quality Assurance
RA – Regulatory Affairs
DC – Document Change
FC – Facility Change
Appendix: GUIDELINES FOR SCOPE OF CHANGE
Change Code | Scope of Change | Ownership of Change | Consent to be taken from departments other than QA/RA |
C01 | Documented Procedure SOP/STP/Specification/MFR/BMR/BPRR/BPAR/BPCR/ GTP/Validation Protocol/Stability protocols/Site Master File/Validation Master Plan/Formats/Like to Like | Operating owner of the procedure | Related user departments |
C02 | Change in facility Change in Building of Manufacturing block/warehouse/utility/QC/Microbiology lab/other parts of the premises/ Like to Like | Operating owner of the building | Related user departments Project Engineering & Utility Safety & Environment |
C03 | Change in Process Change of site/stream/Change of batch size/ Batch formula/ manufacturing process sequence/process parameter/packing mode. * Change in cleaning and sanitation agent/Lubrication/Lab chemical / Change in approved Vendor/Change in Artwork/ ( *shall be not applicable if addressed under C01) / Like to Like | Manufacturing departments/QC department/Purchase/Packaging Development department( as applicable) | R & D ( Process development & analytical development)/all other related responsible user departments |
C04 | Change in Equipment/Critical Utility Manufacturing equipment/change in accessories of equipment/ QC instruments/Weighing equipment/changes in capacity /operating principle/Like to Like Critical utilities like HVAC, water system, Compressed air, Vacuum, Nitrogen, dust extraction/Like to Like | Manufacturing/Quality Control/Engineering & Utility ( as applicable) | Projects Engineering & Utility All related user departments |
C05 | Software of manufacturing equipment/material inventory/other critical utility/testing equipment/BMS/any other monitoring, data processing, and recording system/Like to Like | Operating owner of the system /equipment | Projects Engineering & Utility All related user departments |
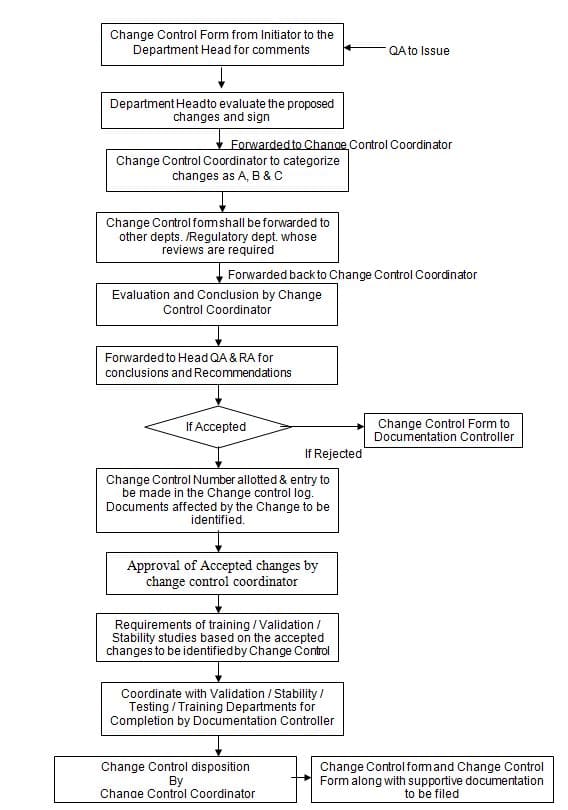
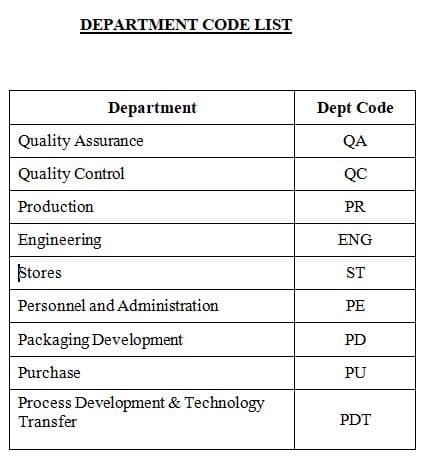
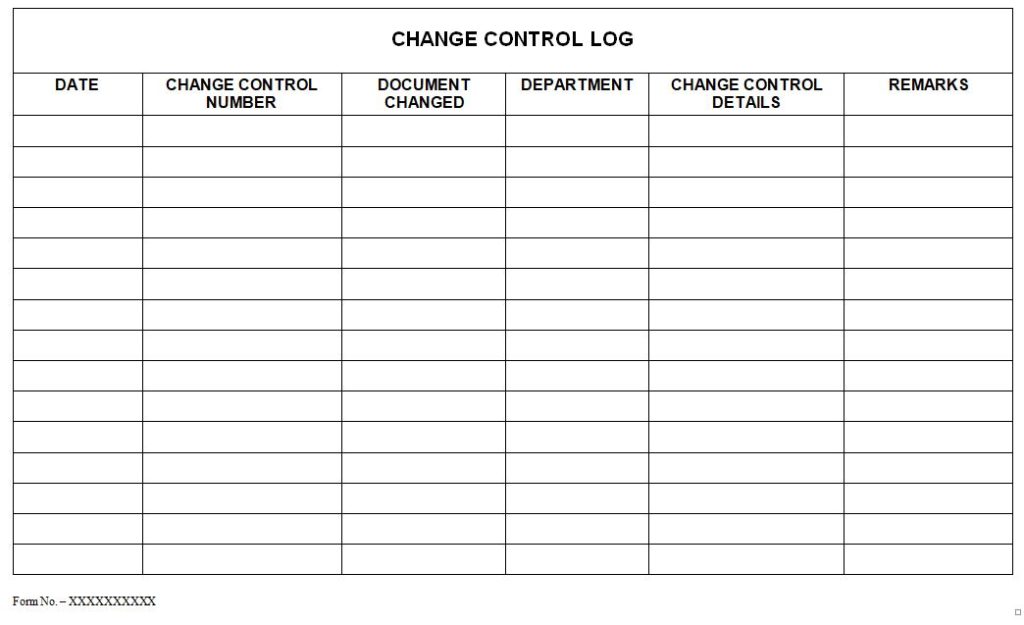
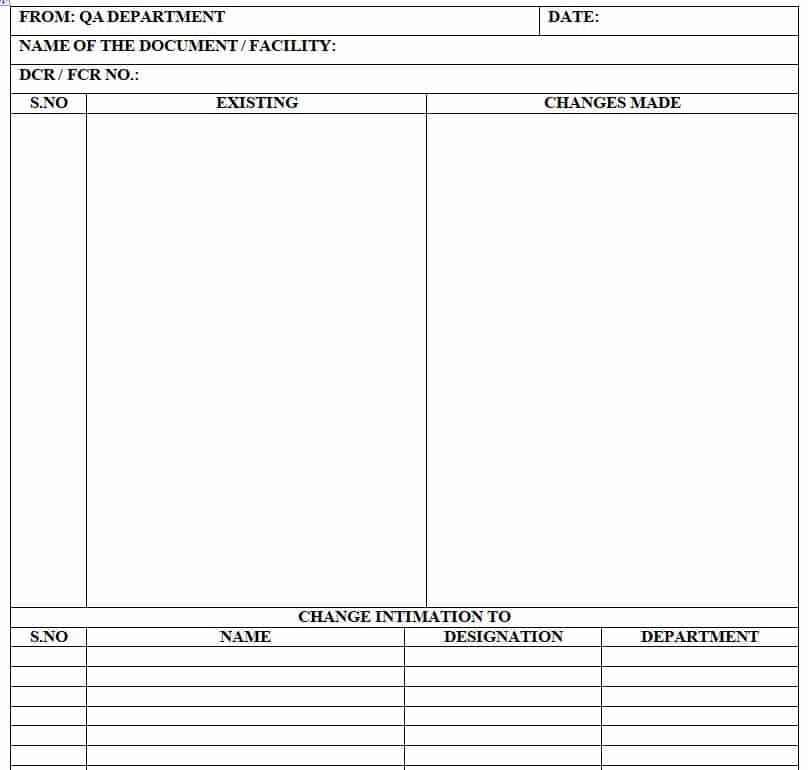

Naresh Bhakar is the Founder and Author at Pharmaguddu.com, bringing his extensive expertise in the field of pharmaceuticals to readers worldwide. He has experience in Pharma manufacturing and has worked with top Pharmaceuticals. He has rich knowledge and provides valuable insights and data through his articles and content on Pharmaguddu.com. For further inquiries or collaborations, please don’t hesitate to reach out via email at [email protected].