The airlocks is a transition space that typically has two doors in series to separate controlled environments such as a cleanroom, lab, operating room, or isolation room from the corridor.
What is an airlock?
Airlocks are commonly used in the pharmaceutical industry to maintain cleanliness and prevent contamination of the manufacturing environment. In a pharmaceutical manufacturing facility, an airlock is a small, enclosed space that is used to transition between clean and non-clean areas. It typically consists of two or more doors that can be opened and closed to allow personnel or material to pass through while maintaining a separation between the two areas.
Purpose of airlocks in a pharmaceutical:
The purpose of an airlock in a pharmaceutical facility is to prevent contaminants from entering the clean areas, where drugs are manufactured and packaged. It also helps to prevent the spread of contaminants from one area to another within the manufacturing facility. This is important because even small amounts of contamination can have serious consequences, including the production of low-quality or unsafe products.
Working operation of airlocks in pharmaceutical manufacturing facilities:
Airlocks are often equipped with features such as air showers, which use high-pressure jets of air to remove dust and other particles from clothing and equipment before entering the clean area. They may also include HEPA (high-efficiency particulate air) filters, which remove particles from the air to maintain a sterile environment.
In addition to airlocks, pharmaceutical facilities may also use other types of barriers and controls, such as gowning rooms and negative pressure rooms, to maintain the cleanliness and safety of their manufacturing environments.
Types of airlocks system
The airlock is generally called PAL (personnel airlock) when used for personnel and MAL (Material airlock) when used for transferring materials.
In pharmaceuticals there are basically three types of the airlock used as described below:
- Cascade
- Bubble
- Sink
1. Cascade Airlock
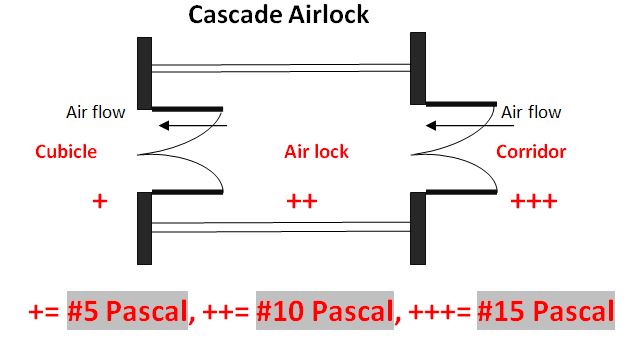
These cascade types are very common having higher differential pressure on one side (Corridor) and lower differential pressure on another side (Cubicle). in a cascade system positive air pressure flow from the higher pressure internal zone to the airlock and from the air lock to the lesser lower pressure grade area. this prevents to entry of dust and contaminated particles from outside to the airlock and from air lock to the inner side.
Application:
Any manufacturing facility where the product requires protection from particulate but the people outside the clean room does not need protection from the product in the clean room for example tablets manufacturing areas in facilities.
2. Bubbles Airlock
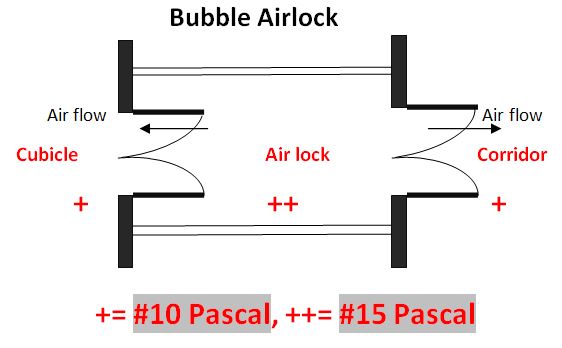
Bubble types have higher differential pressure inside the airlock as compared to outside. it creates barriers where contaminates within either area are pushed back into their own respective area.
Application:
A bubble type of airlock system is used in an area where the product needs protection and the person external to the cleanroom required protection from the product to reduce the possibility of viable particulate from entering the lesser pressure cleanroom. Area such as higher potency, compounding area terminal sterilization is not an option. These types of airlocks are used in injectable manufacturing areas.
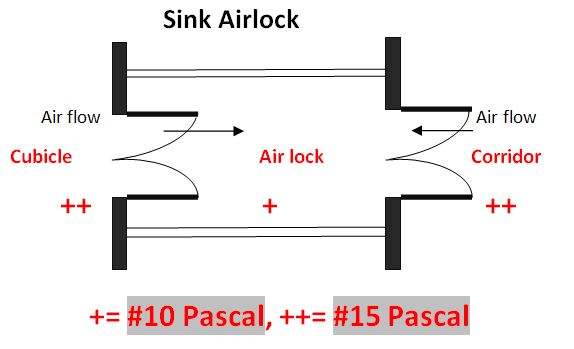
3. Sink Airlock
The sink airlock has lower pressure inside the airlock and higher pressure on both sides of the air lock. sink types pull air from both adjacent areas creating a low-pressure barrier and reducing the opportunity for contamination to pass to the internal zone.
Applications:
These types of airlock system are used inside research facilities, a substance that is experimented on are highly dangerous, and it is essential to keep them from being exposed during a few types of the production process in a clean room, air from a contaminated area has to be contained in one place for example; poisonous manufacturing area.
Potent compound Airlock
The Potent compound airlock is a combination of the pressure bubble and sinks air lock.
Related: Door Interlock System
Precautions while operating airlock system
- The air lock door should be open to higher differential pressure side which helps to close the door.
- An interlocking system should be there to prevent both doors from opening once at a time.
- An alarm system should be there to indicate one door is open at once.
- A Higher ACPH rate should be maintained in the airlock. it should be a minimum of 20 ACPH. it helps to remove the contamination entered from the outside easily.
- The air lock should be kept empty, and materials such that garments, shoe covers, etc. should not be kept in the air lock.
Frequently Asked Questions (FAQs):
Three types of airlocks systems are incorporated in pharmaceuticals for example Cascade Air lock, Bubble airlock, and Sink airlock
Cascade types air lock is majorly used in pharmaceutical tablet manufacturing
Air lock helps to prevent contamination and cross-contamination.

Naresh Bhakar is the Founder and Author at Pharmaguddu.com, bringing his extensive expertise in the field of pharmaceuticals to readers worldwide. He has experience in Pharma manufacturing and has worked with top Pharmaceuticals. He has rich knowledge and provides valuable insights and data through his articles and content on Pharmaguddu.com. For further inquiries or collaborations, please don’t hesitate to reach out via email at [email protected].