The sugar coating of tablets process involves building up layers of coating materials on tablet cores by repetitively applying a coating solution or suspension and drying off the solvent. Sugar coating insulates and masks the color and texture of the core of the tablet. Here in this article, you will learn about the steps of sugar coating or types of sugar coating, examples of ingredients used, what are the benefit, advantages, disadvantages, tablet coating defects, and remedies.
Steps involved in sugar Coating of Tablets:
Sugar coating of tablets steps includes; waterproof or seal coating to sub-coating, smooth coating for coloring finishing, polishing, and last Printing as discussed below:
- Sealing (Seal Coat)
- Sub-Coating
- Smooth coating
- Color coating
- Polishing
- Printing
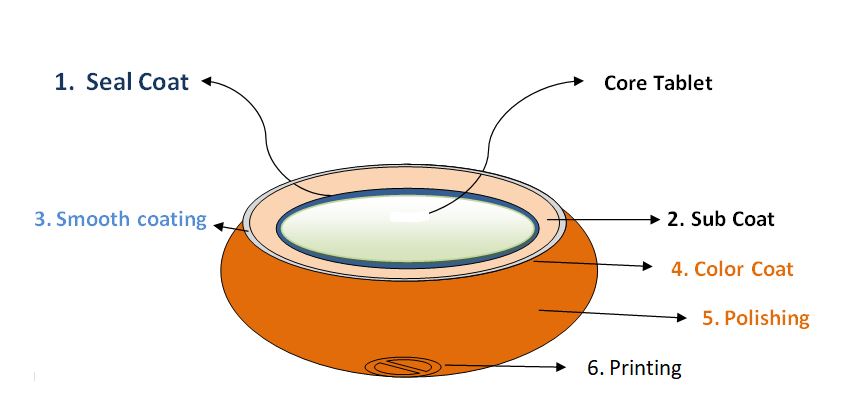
Step1: Sealing (Water Proofing)
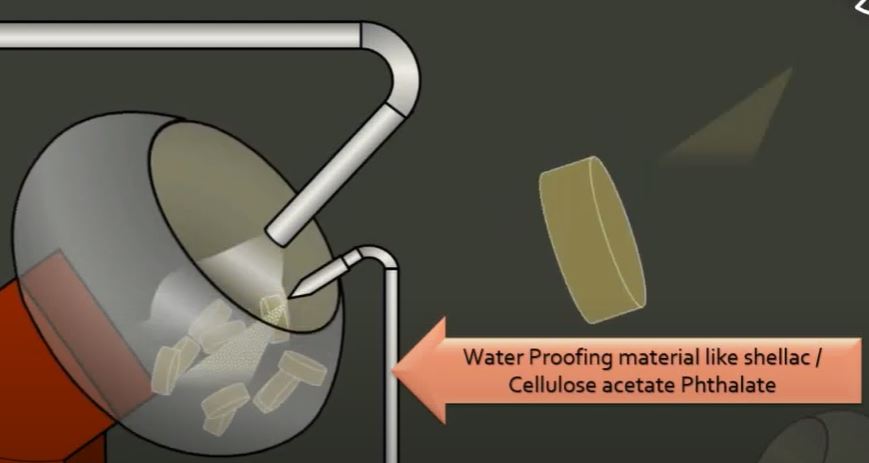
The seal coat delivers a moisture barrier and hardness to the tablet and prevents attritional effects on tablets during rotation in a tablet coating machine.
Polymers for seal coating are generally water-insoluble and applied from an organic solvent solution, Generally, two or three coating layers are applied and must be applied cautiously since excess materials may increase the disintegration time of the tablets.
Examples of seal coating materials:
- Shellac in Combination with PVP (it prevents hardening with age)
- Zein alcohol soluble protein derivative
- Ethylcellulose
- Cellulose acetate Phthalate
- Polyvinyl acetate Phthalate
- HPMC (hydroxypropyl methylcellulose)
- HPC (hydroxypropyl cellulose)
Step 2: Sub coating
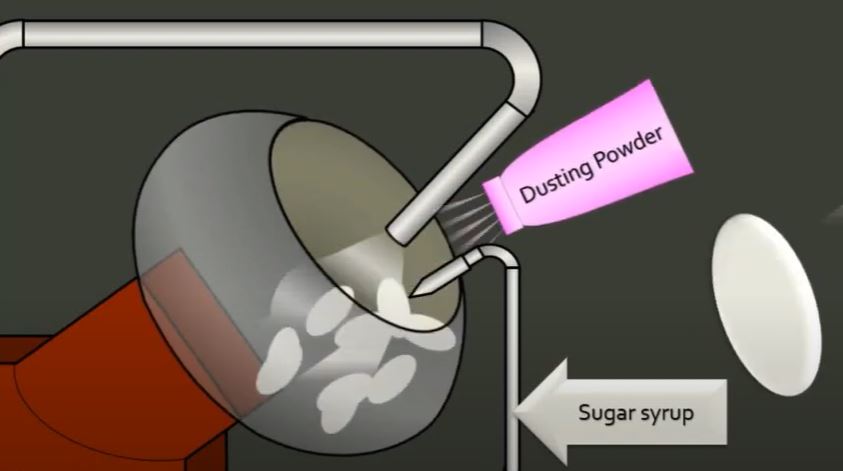
it is the actual start of the sugar coating process it provides the rapid build-up necessary to round up the tablet edge. it also acts as the foundation for smoothing and color coats.
Methods of sub-coating:
Generally, 2 methods are used for sub-coating:
Method 1: Application of gum(acacia/gelatin) based solution followed by dusting with powder (Talc/CaCO3) and then drying. this step is repeated until the desired shape is achieved.
Binder Solution involved in Method 1:
Ingredients | %w/w |
Gelatin | 2 to 10 |
Gum acacia | 5 to 10 |
Sucrose powder | 40 to 50 |
Distilled water | upto 100 |
An example of Ingredients involved in Method 1 is:
Ingredients | %w/w |
Calcium carbonate | 30 to 50 |
Titanium dioxide | 2 to 10 |
Talc, asbestos-free | 20 to 30 |
Sucrose (Powdered) | 25 to 35 |
Gum acacia (Powdered) | 1 to 5 |
Method 2: Application of a suspension of dry powder and gum/sucrose solution followed by drying.
Examples of ingredients used for Method 2:
Ingredients | %w/w |
Sucrose | 30 to 50 |
Calcium carbonate | 15 to 25 |
Talc (Asbestos free) | 10 to 15 |
Gum acacia (Powdered) | 1 to 5 |
Titanium dioxide | 1 to 5 |
Distilled water | 20 to 30 |
Step 3: Smoothing
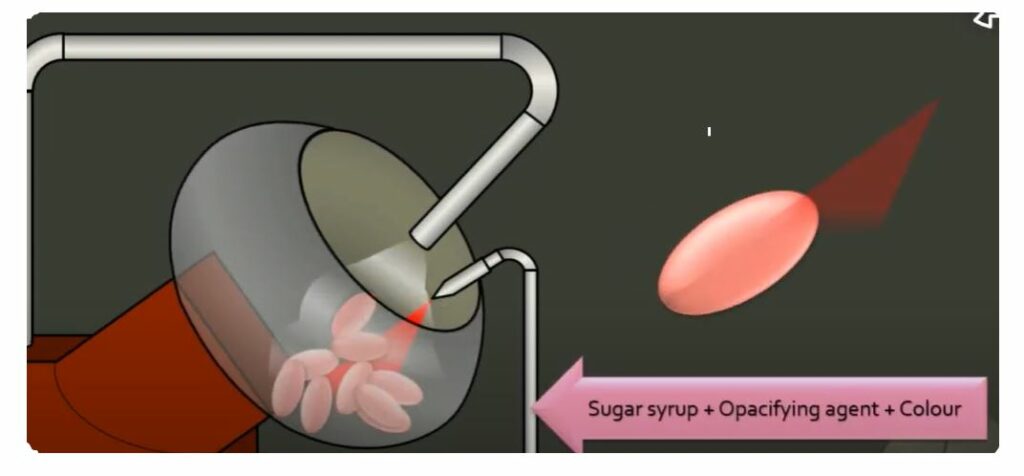
This process is specifically for smoothing and filing the irregularity/Roughness on the surface generated during sub-coating. it also increases the tablet dimension to a predetermined level. Smoothing usually can be accomplished by the application of a simple syrup solution of approximately 60 to 70% sugar solid. This syrup solution generally contains pigments starch gelatin acacia or opacifier (TiO2) if required.
Step 4: Coloring (Color Coating)
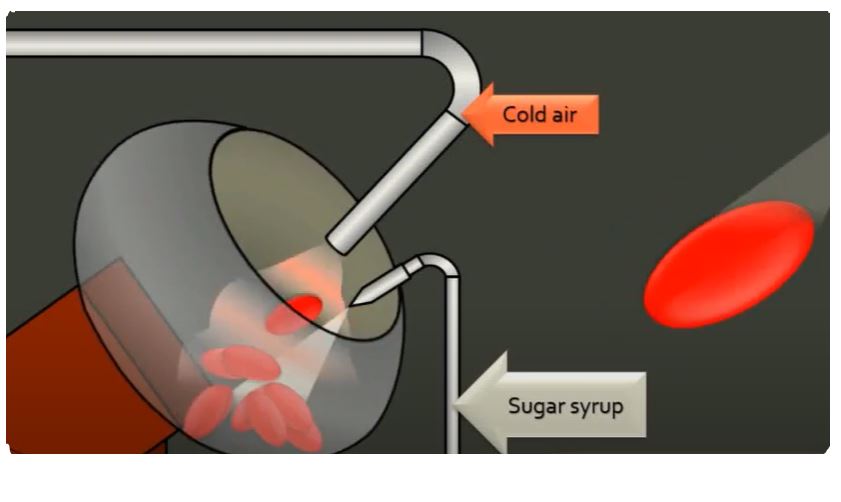
It involves the multiple application of syrup solution containing the requisite coloring matter.
Water-soluble dyes were used previously in the sugar coating as water-soluble dye migrates to the surface during drying they are now replaced by water-insoluble pigment forms, for example, TiO2, Iron oxide, and Certified Lakes.
Step 5: Polishing
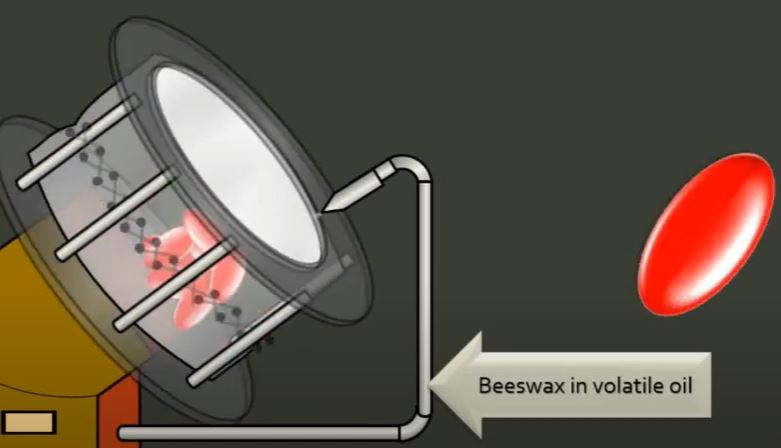
Sugar-coated tablets are polished to achieve a final elegance. it is the application of a thin layer of glossy wax. The wax may be dissolved in warm naphtha or petroleum benzene.
The solution is sprayed onto the tablets which are allowed to rotate until the solvent is evaporated.
The typical polishing mixture used is:
- Beeswax: 80 to 95% weight by weight
- Carnauba wax: 5 to 15% weight by weight
They melt together, strain, and cool.
Dissolve 5 to 10 grams of the mixture in 100 milliliters of Naphtha with the application of moderate heat.
Step 6: Printing
In addition to color, shape, and size, Printing is done on sugar-coated tablets for identification. Printing is done after or before polishing with pharmaceutical branded ink.
If sugar-coated tablets are to be further identified with a product name, dosage strength, company name, or logo, this has to be accomplished by means of a printing process.
Printing earlier to polishing allows the ink to adhere more firmly to the tablet surface, but any legend may later be removed by either friction or with the help of organic solvents during the polishing process.
Printing after polishing avoids the problem of print rub-off during polishing, but branding inks do not always adhere well to the waxed tablet surface. Adhesion of printing inks can be improved by applying (prior to printing) a modified shellac, preprint base solution.
Example of Sugar Coated Tablets:
Example of sugar-coated tablets includes Vitamins, conjugated oestrogen, and mebeverine hydrochloride.
Benefits of Sugar-Coated Tablets:
- The process requires low capital cost, and simple equipment, and is relatively easy to perform.
- It is cheap in terms of operating costs as the most typical ingredients used are water and sugar.
- It provides an attractive and glossy finish look and has wide consumer acceptability.
- Sugar-coated tablets are easy to take as orally because sugar coating masks the teste.
Disadvantages of Sugar Coating
- The achievement of high glossy quality often requires well-trained coating operators.
- The process is Labour intensive and requires a long processing time.
- Sugar-coated tablets are not cooperative with embossing, and the use of print for identification or labeling (the final gloss is achieved by a polishing step which can make imprinting difficult).
- Sugar coating increases the weight and size of the tablet (Increasing packaging and shipping costs)
- The Brittleness of the coatings causes the sugar-coated tablets exposed to potential damage if mishandled.
Coating Machine:
The following machine is generally used for sugar coating:
- Accela-Cota/Hi-coater Systems
- Driacoater
- Glatt coater
FAQs
The sugar-coating process involves a multi-stage process, where repetitively applying a coating solution or suspension and drying off the solvent.
For sugar coating, a Total 6 steps are involved
Source: Images credit to Tips & Tricks by AMB

Naresh Bhakar is the Founder and Author at Pharmaguddu.com, bringing his extensive expertise in the field of pharmaceuticals to readers worldwide. He has experience in Pharma manufacturing and has worked with top Pharmaceuticals. He has rich knowledge and provides valuable insights and data through his articles and content on Pharmaguddu.com. For further inquiries or collaborations, please don’t hesitate to reach out via email at [email protected].