The Area Qualification Protocol plays an important role in the pharmaceutical sector, serving as a vital process that ensures compliance and upholds quality standards across various sections within a pharmaceutical facility. This protocol entails a thorough assessment and examination of the important zone including cleanrooms, manufacturing areas, storage spaces, and laboratories to validate their appropriateness for specific pharmaceutical operations. Its comprehensive nature guarantees the suitability and reliability of these areas, contributing significantly to maintaining industry standards and regulatory requirements.
Area Qualification Protocol Content:
Serial No. | Item Description |
1.0 | Protocol Approval |
2.0 | Overview: |
2.1 | Objective |
2.2 | Purpose |
2.3 | Scope |
2.4 | Responsibility |
2.5 | Execution Team |
3.0 | Acceptance criteria |
3.1 | Construction features/layout |
3.2 | Re-qualification criteria |
4.0 | Area Qualification Procedure |
4.1 | Instruction for Filling the Checklist |
5.0 | Verification of Physical Parameters |
5.1 | Equipment Details. |
5.2 | Observation of Area. |
6. 0 | Deficiencies and Corrective Action Report |
7.0 | Area Qualifications Final Reports |
7.1 | Summary |
7.2 | Conclusion |
7.3 | Final report approval |
1.0 Protocol Approval:
This qualification protocol for the area has been reviewed and approved by the following persons:
FUNCTION | NAME | DEPARTMENT | SIGNATURE | DATE |
Prepared By | Quality Assurance | |||
Reviewed By | Projects / Engineering | |||
Reviewed By | Production | |||
Reviewed By | Quality Control | |||
Approved By | Quality Assurance |
2.0 Overview:
2.1 Objective:
The objective of developing and executing this protocol is to collect sufficient data pertaining to the area and define the qualification requirements as per the acceptance criteria in static conditions.
2.2 Purpose:
The purpose of this protocol is to establish documentary evidence to ensure that the area is controlled as per the requirement suitable for manufacturing.
2.3 Scope:
This protocol is applicable for the Qualification of PPM Staging area in the manufacturing facility.
2.4 Responsibility:
The following shall be responsible;
Projects / Engineering – For execution.
Production Head – For execution support.
Quality control head – For area monitoring and for execution.
Quality Assurance Head – For adequacy and final approval.
2.5 Execution Team:
The qualification of the area shall be verified by executing the qualification studies and test procedures as described in this protocol. The successfully executed protocol documents that the area is qualified as per the design. All executors involved with this protocol shall sign within the prescribed format given below.
DEPARTMENT | DESIGNATION | NAME | SIGNATURE | DATE |
Projects | ||||
Production | ||||
Quality Control | ||||
Quality Assurance |
3.0 Acceptance Criteria:
3.1 Construction Features/layout:
3.1.1 All criteria mentioned in the verification of physical parameters should be met.
3.2 Requalification criteria:
The area has to be qualified if-
- There are any major civil changes that affect the performance of the area
- After any changes in HVAC system components
- There are any changes in the operational layouts.
- There are any major changes in the utility point.
4.0 Area Qualification Procedure:
4.1 Instruction for Filling the Checklist
4.1.1 In case of compliance with the test use the word ‘Complies’ otherwise use’ Does not comply ‘ to indicate non-compliance.
4.1.2 For Verification of physical parameters use the word ’Complies’ if the parameter matches with the Design specification and use ‘Does not comply’ if the parameter is not matching with the specification.
4.1.3 Give detailed information in the summary and conclusion part of the
Area Qualification Report.
4.1.4 Whichever column is blank or not used ‘NA’ shall be used.
5.0 Verification of Physical Parameters for Packing Hall.
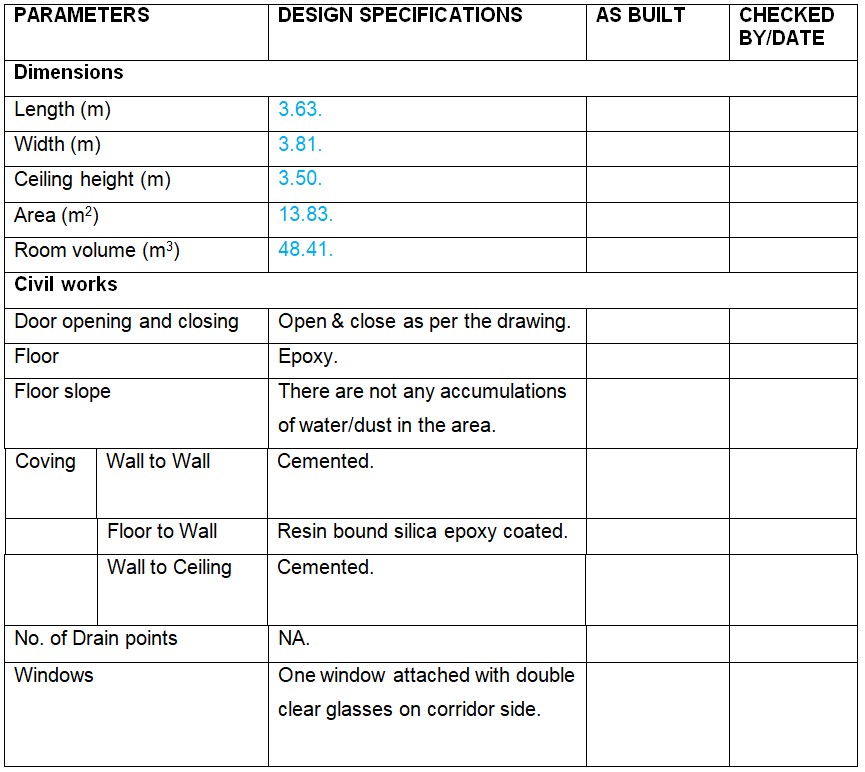
Electrical:
Wiring | Concealed type. | As Build | Checked By/Date |
Electrical fittings | Enclosed in SS Box and of industrial type. | ||
No. Of Lighting fixtures | 09. | ||
Flameproof fittings | NA. | ||
Luminance (Lux) | NLT 400 Lux. |
Related: Risk Assessment Protocol
Service/Utilities:
Purified water | NA. | As Build | Checked By/Date |
Compressed air | NA. | ||
Identification of different utilities | NA. |
Air handling system:
AHU no. | AHU- AHF-1B. | As Build | Checked By/Date | ||||
No. of supply air grills | 03. | ||||||
No. of return riser grills | 04. | ||||||
Dimension of supply air grill | 2×2 sq ft. | ||||||
Dimension of return air riser/grills. | |||||||
Position of filter | Terminal. | ||||||
Air Flow | 736 CFM. | ||||||
No. of air changes per hour | 20 | ||||||
Temperature range | 25 ± 2° C | ||||||
Relative Humidity range | 50 ± 5% | ||||||
Pressure differential with respect to adjacent area | Pressure differential with respect to the adjacent area |
Related: Protocol on Hold Time Study of Machine Parts
GMP Requirements:
Flow of Personal | Interlocking System | As Build | Checked By/Date |
Gowning facility | Required for operation and cleaning in the specified area. | ||
Area | Adequate space in the area is provided for the storage of materials. | ||
Noise level of the room | NMT 65 db. | ||
Status Board | NA. | ||
Room numbering and identification | Room is having proper identification and number i.e. RF-15. | ||
SOP stands | Provided. | ||
Status board | Provided |
5.1 Equipment Details:
Sr. No | Equipment Name | Equipment Id. | Utility Requirements. |
1. | |||
2. | |||
3. | |||
4. | |||
5. | |||
6. | |||
7. | |||
8. | |||
9. | |||
10. |
6.0 Deficiencies and Corrective Action Report
The following deficiencies were verified and corrective actions were taken in consultation with the Engineering Department.
Description of deficiency |
Corrective action(s) taken : |
Comments:
Reviewed By:
Date
7.0 Area Qualifications Final Reports:
All the data sheets and discrepancy reports shall be reviewed by the execution team to prepare a summary report. The summary of the qualification report shall be used to draw a conclusion for approval of the area qualification report.
7.1 | Summary : |
7.2 | Conclusion : |
7.3 Final report approval
It has been verified that all tests required by this protocol are completed, reconciled, and attached to this protocol or included in the qualification summary report. Verified that all amendments and discrepancies are documented, approved, and attached to this protocol.
The signature in the block below indicates that all items in this qualification report of the area have been reviewed and found to be acceptable and that all variations or discrepancies have been satisfactorily resolved.
NAME | DESIGNATION | DEPARTMENT | SIGNATURE | DATE |
Project/ Engineering | ||||
Production | ||||
Quality Assurance |

Naresh Bhakar is the Founder and Author at Pharmaguddu.com, bringing his extensive expertise in the field of pharmaceuticals to readers worldwide. He has experience in Pharma manufacturing and has worked with top Pharmaceuticals. He has rich knowledge and provides valuable insights and data through his articles and content on Pharmaguddu.com. For further inquiries or collaborations, please don’t hesitate to reach out via email at [email protected].