The audit is an important aspect of determining the growth and market existence of any organization, particularly in the pharmaceutical sector. The success rate of an audit relies on multiple factors, some of the Audit Check List for Quality Assurance are described below:
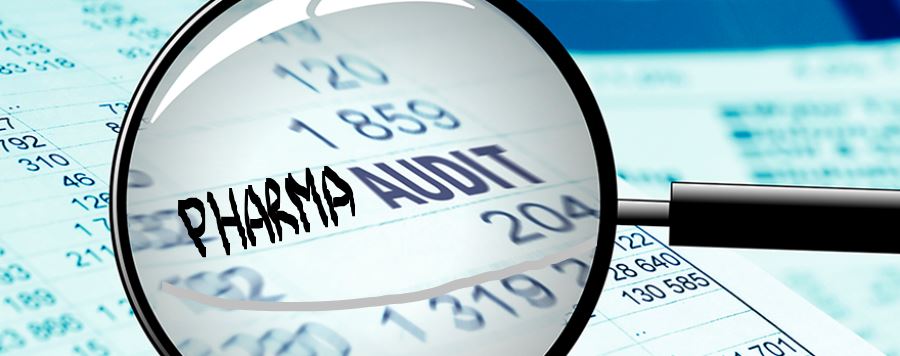
1.0 Quality Assurance Department
1.1 Does the company have a later quality policy statement?
1.2 Does the company have an updated organization chart?
1.3 Are the previously audited records maintained?
1.4 Are parenteral products designed and developed according to the requirement of cGMP & other associated codes such as good laboratory practice (GLP)and good clinical practice (GCP)?
1.5 Are production and control operations clearly specified in a written form and cGMP requirements are adopted?
1.6 Are responsibilities clearly specified in the job description?
1.7 Are all necessary controls on starting materials, intermediate products, and other in-process controls, calibrations, and validation carried out?
1.8 Are finished products correctly processed and checked (In-Process Checks) according to the written procedures?
2.0 Validation Related Audit Checklist
2.1 Is validation properly documented and includes Validation Master Plan, Cleaning Validation Master Plan Validation Protocols (HVAC, Purified Water, WFI, Process Validation, Cleaning Validation, etc.) Validation Reports and Equipment Qualification (IQ, OQ, and PQ)?
2.2 Are validation studies conducted in accordance with pre-defined protocols (VMP) and validation planners?
2.3 Have production procedures been validated (Process Validation)?
2.4 Does the process control (In- Process Checks) address an issue to ensure the identity, strength, quality, and purity of the product?
2.5 Are all weighing and measuring performed by a specialized & qualified person and observed by a second person and duly signed by both of them on the record sheet?
2.6 Validation of New Master Formula:
Are new master formulas or methods of preparation adopted and steps taken to demonstrate their suitability for routine processing, process-defined materials, and equipment specified?
2.7 Validation of Equipment & Materials:
Are significant amendments to the manufacturing process, including any change in equipment and materials affecting product quality or re-productivity of process validated?
2.8 Are validation records properly maintained and updated?
3.0 Documentation and Records
3.1 Are documentation meticulously maintained as per rules and regularly reviewed and kept up to date?
3.2 Is documentation maintained in properly segregated areas and easily available?
3.3 Is a master list of documentation maintained?
3.4 Is documentation accurate, clear & neat? Does it define specifications and procedures for all materials & methods of manufacture & control?
3.5 Are all the specifications, testing, procedures, master formulae, packing instructions, and standard operating procedures (SOPs) available, current & being followed?
3.6 Do the records provide the existence of documented evidence, traceability, and an audit trail that will permit investigation?
3.7 Does the record provide batch processing & packaging details including receiving the sample, processing equipment, analytical testing, and laboratory instrument records?
4.0 Labeling
4.1 Are labels to the containers, equipment or premises applied un-ambiguously according to the company’s agreed format?
4.2 Are labels of different colors indicating the status such as “Quarantined”, “Accepted”, “Rejected”, or “Cleaned” used?
4.3 Are all finished products labeled as per specifications?
5.0 Process Documents and Records
Ensure the following documents/records are available at the time of Audit:
- Are all master copies of documents available?
- Specifications for intermediate and bulk products
- Batch processing records
- Record for process operation.
- Batch packaging records.
- Record for packaging operation
- Record of Batch numbers.
- Analytical records of the batch.
- Record for finished product release procedures.
- Record of issuance and retrieval of documents (BPR and Data Recording Formats)
6.0 SOPs Related Audit Check List
6.1 Are SOPs and associated records of actions, and conclusions reached available for the following at the premises?
6.2 Equipment Assembly and Validation.
6.3 Analytical apparatus and calibration
6.4 Maintenance, cleaning, and sanitization,
6.5 Personnel matters including qualification, training, clothing, and hygiene
6.6 Environmental monitoring.
6.7 Pest Control
6.8 Complaints
6.9 Drug recalls
7.0 Vendor Qualifications
7.1 Do you have an updated list of approved vendors?
7.2 Are the vendors supplying raw material (both active & inactive ingredients), primary packaging & printed components audited & found to be satisfactory?
8.0 Change Control Programm
8.1 Is there a format change control program in place supported by an SOP to initiate, review & approve changes in material, sources, processes, product packaging, equipment, batch size changes, etc. is it properly followed?
9.0 Sample
9.1 Does the company retain a sample of a lot or batch of the packaged/labeled drug for a period of at least one year after the expiration date on the label of the drug?
9.2 Does the company retain a sample of each lot or batch of raw material (including both active and inactive ingredients)?
9.3 Does the retained samples properly labeled and records maintained as per SOP?
Related: Audit Checklist for Quality Control
10.0 Stability Studies
10.1 Does the company have a prospective and concurrent stability studies program based on SOP and utilizing proper equipment i.e. climatic chambers maintained at 30°C/ 65% RH for ambient and 40 °C / 75% RH for stress conditions and continuously monitored for temperature & RH.
10.2 Is the stability of finished products evaluated and documented prior to marketing?
10.3 Does the stability data support the shelf life assigned to the product?
10.4 Are any deviations in data reviewed and appropriate steps taken in case of stability issues?
11.0 Drug recalls
11.1 Do you have an SOP for drug recalls?
11.2 If answered yes to the above did you have any drug recall in the past 2 years?
12.0 Annual Product Review
12.1 Is there a process in place to review statistical data (i.e. trend analysis, reworks, rejects, customer complaints) of all the products manufactured during the year?
12.2 Provide the name of the products manufactured by you along with the price list.
12.3 Provide the source of raw material for individual products.
12.4 Do you export your products if so then to whom and mention the name of the products?
13.0 Equipments LogBooks
13.1 Are logbooks for major & critical equipment identified by the company kept?
13.2 Are the issuance of logbooks & archival properly documented?
14.0 Audit / Complaints
Below is some point that must be considered during internal GMP audits.
Internal GMP Audit:
14.1 Do you have an effective internal GMP inspection program to audit all the manufacturing areas, activities & QC lab at specifically defined periods?
14.2 Is there a process in place to fill the gaps/observations / non-conformance found during the internal GMP audits?
14.3 Is there an audit planner for all departments available?
14.4 Is the compliance of all discrepancies found during audits done?
Each point of the Audit Check List shall be filled as applicable and comments or remarks, in addition, shall be given under the remarks column in the checklist.
Note: The points mentioned in the Audit Check List for Quality Assurance list are not limited to these only

Naresh Bhakar is the Founder and Author at Pharmaguddu.com, bringing his extensive expertise in the field of pharmaceuticals to readers worldwide. He has experience in Pharma manufacturing and has worked with top Pharmaceuticals. He has rich knowledge and provides valuable insights and data through his articles and content on Pharmaguddu.com. For further inquiries or collaborations, please don’t hesitate to reach out via email at [email protected].