The purpose of the Auto Coater Operational Qualification protocol is to establish the documentary evidence to ensure that the installed Auto Coater shall operate reproducibly and consistently within its full dynamic range of operation according to the manufacturer’s specifications.
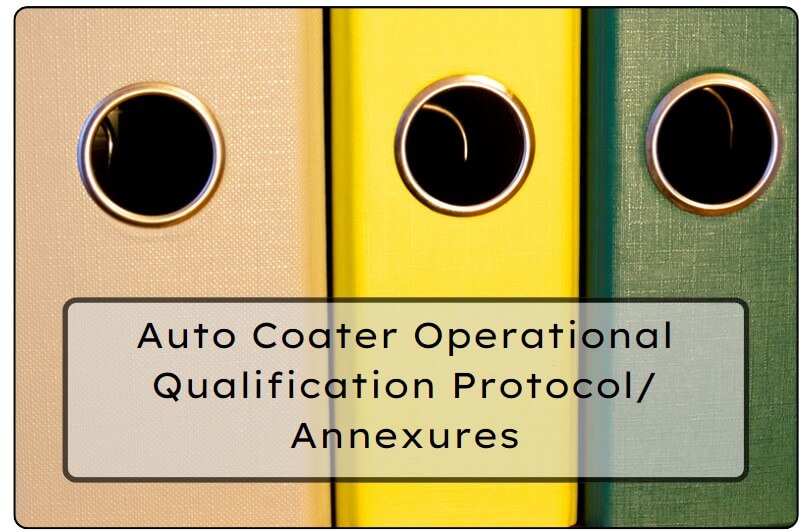
SERIAL NO. | ITEM DESCRIPTION |
1.0 | PROTOCOL APPROVAL |
2.0 | OVERVIEW: |
2.1 | Objective |
2.2 | Purpose |
2.3 | Scope |
2.4 | Responsibility |
2.5 | Execution Team |
3.0 | ACCEPTANCE CRITERIA |
4.0 | REQUALIFICATION Criteria |
5.0 | OPERATION QUALIFICATION PROCEDURE |
5.1 | Equipment Description |
5.2 | Instruction on filling out the checklist |
5.3 | Test instrument details |
5.4 | Verification of functional checks |
5.5 | Verification of key Functionality of the control panel |
5.6 | Verification of safety Feature(s) |
5.7 | Verification of Standard Operating Procedure |
5.8 | Training Record of Personnel(s) |
5.9 | Verification of Component (s) to be calibrated |
5.10 | Deficiency And Corrective Action(s) (Reports) |
6.0 | Operational Qualification Final Report |
6.1 | Summary |
6.2 | Conclusion |
6.3 | Final Report Approval |
Check Out Auto Coater Installation and Performance Qualification Protocol Also.
1.0 | PROTOCOL APPROVAL: |
The signing of this approval page of Protocol No. XYZ indicates agreement with the qualification approach described in this document. If a modification to the qualification approach becomes necessary, an addendum shall be prepared and approved. The procedure is only permissible for implementation upon receiving authorization from the designated authorities as below.
This Operational Qualification Report of Auto coater has been reviewed and approved by the following persons:
FUNCTION | NAME | DEPARTMENT | SIGNATURE | DATE |
PREPARED BY | QUALITY ASSURANCE | |||
REVIEWED BY | PROJECTS / ENGINEERING | |||
REVIEWED BY | PRODUCTION | |||
APPROVED BY | QUALITY ASSURANCE |
2.0 | OVERVIEW: |
2.1 | OBJECTIVE: |
The objective of the operational qualification is to prove that each operation proceeds as per design specification and the tolerances prescribed there in the document are the same at utmost transparency. | |
2.2 | PURPOSE: |
The purpose of this protocol is to establish the documentary evidence to ensure that the installed Auto coater shall operate reproducibly and consistently within its full dynamic range of operation according to manufacturer’s specification. | |
2.3 | SCOPE: |
This protocol shall define the test procedures, documentation, references, and acceptance criteria to establish that the Auto coater operates and performs as intended in accordance with the design qualification. The equipment shall be preceded by the performance qualification procedure. The Scope of this protocol is limited to the operational Qualification of Auto Coater in Pharmaceutical (Company Name) | |
2.4 | RESPONSIBILITY: |
The following shall be responsible; Quality assurance officer/Executive – For Preparation of Protocol /ExecutionProjects / Engineering Head – For execution, Production Head – For execution support Quality Assurance Head – For adequacy and final approval |
2.5 | EXECUTION TEAM: |
The satisfactory operation of the Auto coater shall be verified by executing the qualification studies described in this protocol. The successfully executed protocol documents that the Auto coater is operational and is satisfactorily working. The execution team is responsible for the execution of the operation of Auto Coater. All executors involved with this protocol shall sign within the prescribed format given below. |
DEPARTMENT | DESIGNATION | NAME | SIGNATURE | DATE |
PROJECTS/ ENGINEERING | ||||
PRODUCTION | ||||
QUALITY ASSURANCE |
3.0 | ACCEPTANCE CRITERIA: |
3.1 | Ensure that the equipment functions in accordance with its defined operational Procedure |
3.2 | All SOPs for the related equipment are to be Checked and Varified by the concerned Departments |
3.3 | Training shall be given to all the concerned personnel |
3.4 | All materials of construction of the contact parts are to be checked as per the specifications. |
3.5 | All the functionality of equipment components is to be checked. |
4.0 | REQUALIFICATION CRITERIA: |
The machine shall be requalified if | |
Any major changes in system components affect the performance of the system· After a major breakdown maintenance is carried out.· As per revalidation date and schedule |
5.0 | OPERATIONAL QUALIFICATION PROCEDURE: |
5.1 | ||
Equipment Name | Auto coater | |
Manufacturer | XYZ Company Name | |
Model | Specify Modal Name | |
Location | Coating Area | |
Equipment Serial No | XYZ | |
Working Capacity | 129~215 kg (Working Capacity Range) | |
Service it offers | Film Coating of tablets and Caplets |
Mechanism
Under the supplied electric power the main driving motor produces the turning movement. While the Coating pan turns, the spray gun sprays the coating pan.
The spray gun sprays the coating solution into tablets in the coating pan. The Baffles attached on perforated plates help coated tablets move up for efficient spraying and drying. After spraying the coating solution to the tablets, high-temperature air is being supplied into the coating pan. The damper plates are worked by the compressed air which is supplied into the cylinder. The heat exchanger produces the high-temperature heated air and supplies the air to the coating pan.
Auto Coater comprises of following components: –
- Air Flowing System.
- Coater.
- Solution tank.
- Manual damper.
- Dust collector.
- Heat exchanger.
- Touch screen.
Air Flowing System
The compressed air pressure can be adjusted by the regulator, which is located at the rear side of the coating machine. Compressed air is supplied to the following area.
a. Solution tank.
b. Coater.
c. Manual damper.
d. Dust collector.
e. Integrated electric electric control panel.
COATER
The coater is the main part, where coating is performed through the mechanical functioning with other parts Viz. Solution tank, Heat exchanger, Dust collector, and Damper. Coater is constituted of the following areas.
a. Driving area
b. Working area
c. Operating control part.
a. Driving area:
The driving area consists of:
- Main power driving motor
- Worm reducer
- Chain
- RPM, WIP sensor
- Pneumatic Chamber
- Pumps for solution
b. Working area :
The working area of the coater is constituted:
a. Coating pan.
b. Baffle and discharging guide.
c. Heated air supply dust pipe.
d. Spray gun.
e. Heated air discharging duck and other auxiliary parts
Coating pan:
The coating pan consists of a round pan and 8 air ducts. The air-exhausting punching plates are located at the side between the duct and the pan. It has a heated air flowing system to supply heated air from the air duct pipe which is located at the rear side of the pan and exhausts the air after drying at the coating pan through the 8 air duct flange of the pan. 8 baffles are installed at the in the side of the pan for helping the mixing and drying the products as making easy air passing through among the products when they are falling to the bottom of the pan.
Discharging chute:
For discharging the products to the outside of the pan. It will be turned in the reverse direction and the discharging guide helps easy outcoming.
Heated air supply duct :
Heated air is supplied through 8 positions of jackets and the perforated holes on the surface of the coating pan.
Spray gun :
The spray gun sprays the coating solution into tablets during coating. On the spray gun coating solution supplying line, the Compressed air supplying line and nozzle withdraw line are attached to the atomizing air, the spray gun can supply coating solution equally to tablets.
There are 3 spray guns on the setting bar for cleaning or maintenance, operator can take out the spray gun by pressing ‘OUT’ of the GUN SLIDING SYSTEM on the operation screen.
Heated air discharging duct :
This duct is installed at the left side of the coating pan and has the function of exhausting heated air that was used for drying the tablets.
SOLUTION TANK:
The solution tank has the function of containing and supplying the coating solution
MANUAL DAMPER:
The opening and shutting of the damper is done by compressed air to the damper cylinder
Dust collector
dust collector has the function of filling the exhausting air that is supplied for the coater. As passing through the dust collector air will be cleaned by the filter.
HEAT EXCHANGER
The heating coil which is installed at the inside of the heat exchanger will be heated by the supplied high-temperature system. Heat exchanger constituted by following parts:
1. Driving area.
2. Air heating area.
3. Filter.
TOUCH SCREEN
The operating control panel consists of the operation switches part and the operation screen part.
Operation switches are:
- Control power ON/OFF select switch.
- Pan ON/OFF select switch.
- Discharge ON/OFF select switch.
- Spray ON/OFF push button switch.
- Emergency switch.
- RPM meter.
- Supplying /Exhaust air temperature.
- Solution Temperature.
- Buzzer reset push button switch.
- Tower lamp switch.
Operation Screen:
All the functions of the system can be controlled by the operation screen. The functional description of the operation screen is as follows.
- Main control start/stop switch.
- Exhaust fan start/stop switch.
- Supply fan start/stop switch.
- Agitator start/stop switch.
- Agitator start/stop switch.
- Gun sliding system OUT/IN.
- Alarm screen.
- Running time.
- Spray screen.
- Intermittent drive.
- Supply velocity.
- Tab bed temperature.
5.2 | INSTRUCTION FOR FILLING THE CHECKLIST |
5.2.1 | In case of compliance of the test use the word ‘Complies’ otherwise use‘ Does not comply ‘ to indicate non-compliance. |
5.2.2 | For identification of the components of the equipment and utilities use the word ‘’yes’’ to show its presence and use ‘No’ to indicate the absence of the identity |
5.2.3 | Give detailed information in the summary and conclusion part of the Operational Qualification report. |
5.2.4 | Whichever column is blank or not used ‘NA’ shall be used. |
5.3 | TEST INSTRUMENT DETAILS |
This test is intended to describe the equipment/instruments and their complete details to have a traceability to the national standard which is to be used for the verification of the operation of the Auto coaterInstrument/Equipment required. 1. Tachometer, 2. Ammeter, 3. Photometer, 4. Anemometer |
Sr. No. | Name of Instrument | Inst. ID. Number | Calibration valid up to | Checked by/Date |
5.4 | VERIFICATION OF FUNCTIONAL CHECKS: |
NAME OF SYSTEM COMPONENT | SPECIFIED FUNCTION | MATCHES WITH THE SPECIFIED FUNCTION(YES / NO) | VERIFIED BY(SIGN) | DATE |
Machine Emergency Stop | To Stop the machine, PLC, | |||
Exhaust Air Pressure Manometer. | To monitor the air pressure of exhausting top duct | |||
Programmable logic controller | To control the process | |||
Operator Interface Terminal | To monitor the process | |||
Temperature sensor for inlet and outlet air | To measure the temperature | |||
Main Air Gauge | To monitor the total compressed air pressure | |||
Pump Air Gauge | To monitor the compressed air pressure of the diaphragm pump | |||
Atom Air Pressure Gauges | To monitor atomizing air pressure supplying to spray gun | |||
Air Flow Meter | Delicate adjusting of atomizing air pressure to spray gun | |||
Lamp ON/OFF Switch | Observation of coating operation | |||
Pan RPM | To show speed of Pan | |||
RPM Sensor | Checking the rotating speed of the Coating Pan |
NAME OF SYSTEM COMPONENT | SPECIFIED FUNCTION | MATCHES WITH THE SPECIFIED FUNCTION(YES / NO) | VERIFIED BY(SIGN) | DATE |
WIP Sensor | It makes the coating pan stop one by one for washing each duct. | |||
Peristaltic pump | To control the supplying volume of the coating solution. | |||
Peristaltic pump RPM | 0-220 RPM Maximum | |||
Sight Glass Window | To view the coating function. | |||
Discharge Chute | To discharge the complete coated tablets. | |||
Tablet Temperature sensor | To measure the tablet bed temperature. | |||
Spray Gun | Spray the coating solution to tablets on the coating pan. | |||
Ball valve lever | To control the opening/closing of the ball valve for material discharge. | |||
Tower Lamp | For Indication of machine status. | |||
Power failure Recovery | The processing time elapsed should be in the PLC memory and the process shall continue from where the power interruption has occurred Switch off the mains for 5 minutes and observe the operation after resumption of power. | |||
NAME OF SYSTEM COMPONENT | SPECIFIED FUNCTION | MATCHES WITH THE SPECIFIED FUNCTION(YES / NO) | VERIFIED BY(SIGN) | DATE |
DOP Test | DOP penetration shown by the photometer should be less than 0.03% through the filter media and should be ‘zero’ through mounting joints |
5.5 | VERIFICATION OF KEY FUNCTIONALITY OF CONTROL PANEL: |
OPERATING PANEL | : | Programmable logic controller |
Make | : |
COMPONENT OF CONTROL PANEL | SPECIFIED FUNCTION | MATCHES WITH THE SPECIFIED FUNCTION(YES / NO) | VERIFIED BY(SIGN) | DATE |
2. Pan ON/OFF | To screen display | |||
2.Pan ON/OFF | To control coating pan operation | |||
3. Discharge pan ON/OFF | To turn the coating pan count clockwise | |||
4. Spray on | To spray of a spray gun. | |||
5. Spray off | To Stop Spray. | |||
6. RPM Meter | To Indicate pan RPM. | |||
7. Suppling Air Temperature Meter | For Measurement of inlet air temperature. | |||
8. Exhausting Air Temperature Meter | For Measurement of outlet air temperature. | |||
9. Buzzer Reset Push Button | To stop the buzzer sound. |
5.6 | VERIFICATION OF SAFETY FEATURES: |
SAFETY FEATURES DESCRIPTION | FUNCTION | VERIFIED BY(SIGN) | DATE |
1. Earthing | To avoid the electrical shock due to leakage current. | ||
2. Hooter | To give an audio signal in case of any deficiency. | ||
3. Emergency Stop Button | To stop the machine if the problem appears in running condition. |
5.7 | VERIFICATION OF STANDARD OPERATING PROCEDURE (SOP) |
The following Standard Operating Procedures were verified as important for the effective performance of Auto Coater operation.
Sr.No. | SOP TITLE | SOP NUMBER | VERIFIED BY | DATE |
5.8 | TRAINING RECORD OF PERSONNEL (S) : |
Sr. No. | Name of Personnel | Designation | Sign. & Date | Trained By | Remark |
1. | |||||
2. | |||||
3. | |||||
4. |
5.9 | VERIFICATION OF COMPONENT (S) TO BE CALIBRATED |
Verify that the drafted calibration procedures for different identified components in Auto Coater are adequate and appropriate covering the operating range(s). e.g. Pressure gauge, temperature gauge, temperature indicator cum controller, etc (As applicable).
COMPONENT / PART TO BE CALIBRATED | IDENTIFICATION NO. | EXTERNAL CALIBRATION(Attach Certificate) | VERIFIED BY(SIGN) | DATE |
1. Pump air pressure gauge | ||||
2. Main air gauge | ||||
3. Pump air pressure gauge | ||||
4. Cil air pressure gauge | ||||
5. Atom air pressure gauge | ||||
7. RPM meter | ||||
8. In/Outlet temperature sensor | ||||
9. Solution tank air pressure gauge. | ||||
10. Inlet/Outlet temperature controller |
5.10 | DEFICIENCY AND CORRECTIVE ACTION(S) REPORT(S) |
The following deficiency was verified and corrective actions were taken in consultation with the Engineering Department. |
Description of deficiency: |
Corrective action(s) taken: |
Reviewed by
Date
6.0 | OPERATIONAL QUALIFICATION FINAL REPORT: |
6.1 | SUMMARY: |
6.2 | CONCLUSION: |
6.3 FINAL REPORT APPROVAL
It has been verified that all tests required by the Auto Coater Operational Qualification protocol are completed, reconciled, and attached to this protocol or included in the Operation qualification summary report. Verified that all amendments and discrepancies are documented, approved, and attached to this protocol.
The signature in the block below indicates that all items in this Auto Coater Operational Qualification report have been reviewed and found to be acceptable and that all variations or discrepancies have been satisfactorily resolved. After the successful operational qualification of the Auto coater, the equipment can be taken for performance qualification.
NAME | DESIGNATION | DEPARTMENT | SIGNATURE | DATE |
PROJECTS / ENGINEERING | ||||
PRODUCTION | ||||
QUALITY ASSURANCE |

Naresh Bhakar is the Founder and Author at Pharmaguddu.com, bringing his extensive expertise in the field of pharmaceuticals to readers worldwide. He has experience in Pharma manufacturing and has worked with top Pharmaceuticals. He has rich knowledge and provides valuable insights and data through his articles and content on Pharmaguddu.com. For further inquiries or collaborations, please don’t hesitate to reach out via email at [email protected].