The objective of developing and executing the Blender Performance Qualification protocol is to document the verification of all aspects of the equipment that can affect product quality. To make an impact assessment of the critical components of the equipment on the material to establish, check, and document the performance of equipment in the established/predetermined operating ranges.
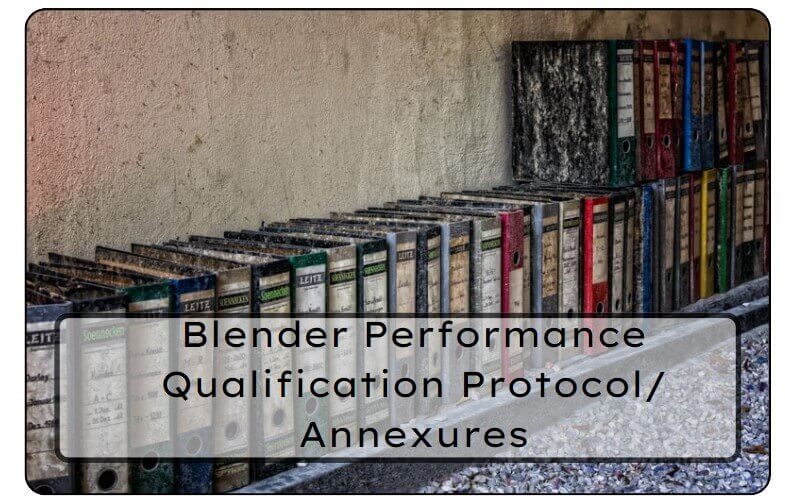
SERIAL NO. | ITEM DESCRIPTION |
1.0 | PROTOCOL APPROVAL |
2.0 | OVERVIEW: |
2.1 | Objective |
2.2 | Purpose |
2.3 | Scope |
2.4 | Responsibility |
2.5 | Execution Team |
3.0 | GENERAL CONSIDERATION/PREREQUISITE |
4.0 | REVALIDATION CRITERIA |
5.0 | PERFORMANCE QUALIFICATION PROCEDURE |
5.1 | Methodology |
6.0 | ACCEPTANCE CRITERIA |
7.0 | MATERIAL REQUIRED FOR BLENDING |
7.1 | Total batch size 80kg of working capacity (max.) |
7.2 | Total batch size 30kg of working capacity (min.) |
7.3 | Total batch size 40 kg of working capacity (max.) |
7.4 | Total batch size 15 kg of working capacity (min.) |
8.0 | DIAGRAM OF BLENDER BIN WITH SAMPLING POINTS |
9.0 | BLENDING |
9.1 | For a batch size of 80 Kg maximum. (Pre Lubrication Mixing) |
9.1.1 | Final Lubrication |
9.2 | For a batch size of 30 Kg minimum. (Pre Lubrication Mixing) |
9.2.1 | Final Lubrication |
9.3 | For a batch size of 40 Kg maximum. (Pre Lubrication Mixing) |
9.3.1 | Final Lubrication |
9.4 | For a batch size of 15 Kg minimum. (Pre Lubrication Mixing) |
9.4.1 | Final Lubrication |
10.0 | DEFICIENCY AND CORRECTIVE ACTIONS |
11.0 | Annexure (s) |
12.0 | PERFORMANCE QUALIFICATION FINAL REPORT |
12.1 | Summary |
12.2 | Conclusion |
12.3 | Final report approval |
1.0 | PROTOCOL APPROVAL: |
This performance qualification protocol of blender 200/100 Ltrs. has been reviewed and approved by the following persons:
FUNCTION | NAME | DEPARTMENT | SIGNATURE | DATE |
PREPARED BY | QUALITY ASSURANCE | |||
REVIEWED BY | PRODUCTION | |||
REVIEWED BY | QUALITY CONTROL | |||
APPROVED BY | QUALITY ASSURANCE |
2.0 | OVERVIEW: |
2.1 | OBJECTIVE: |
The objective of developing and executing this protocol is to document the verification of all aspects of the equipment that can affect product quality. To make an impact assessment of the critical components of the equipment on the material to establish, check, and document the performance of equipment in the established/predetermined operating ranges. | |
2.2 | PURPOSE: |
The purpose of the Blender Performance Qualification protocol is to verify that the equipment produces the desired output. Performance qualification of the equipment is planned after the successful completion of the installation and operational qualification. The performance of the equipment is verified by charging the material and analyzing the content of paracetamol in the blend. | |
2.3 | SCOPE: |
The protocol shall define the test procedures, documentation, references, and acceptance criteria to establish that the performance of the equipment shall meet the predetermined acceptance criteria. The Scope of this protocol is limited to the performance qualification of blender 200/100 Ltrs in XYZ Pharmaceutical. Once the performance qualification of blender 200/100 Ltrs has been completed successfully, the equipment shall be released for the production trial | |
2.4 | RESPONSIBILITY: |
The following shall be responsible; Quality assurance officer/Executive – For Preparation of Protocol /Execution Production Head – For execution support Quality Control head – To analyse the blend sample Quality Assurance Head – For adequacy and final approval |
2.5 | EXECUTION TEAM: |
The execution team is responsible for the execution of performance qualification of blender 200/100 Ltrs. The execution team comprises of: |
DEPARTMENT | DESIGNATION | NAME | SIGNATURE | DATE |
PRODUCTION | ||||
QUALITY CONTROL | ||||
QUALITY ASSURANCE |
3.0 | GENERAL CONSIDERATION/ PREREQUISITE |
3.1 | Approved Standard operating procedure of the blender 200/100 Ltrs shall be available |
3.2 | The installation and operational qualification of the equipment shall be successfully completed before the execution of the performance qualification. |
3.3 | All the deficiencies and discrepancies related to the equipment that affect the product quality and corrective action taken shall be recorded in the appropriate section of the protocol. |
3.4 | The analytical test results and other reports related to the equipment shall be attached to the performance qualification of the equipment and finally verified. |
3.5 | After completion of PQ activities, equipment shall be cleaned as per respective cleaning SOPs and released for manufacturing. |
4.0 | REVALIDATION CRITERIA: |
The machine shall be revalidated if | |
1. There are any major changes, which affect the performance of the equipment. 2. After major changes in the components of the equipment. 3. Batch/lot size taken out of the range on which performance is done. 4. As per the revalidation date and schedule. |
5.0 | PERFORMANCE QUALIFICATION PROCEDURE |
5.1 | METHODOLOGY: |
The principle of the blender 200/100 Ltrs is to blend the material uniformly. The material is charged by opening the top lid and allowed to blend up to the desired time at a defined speed. A dual motor is provided to control the speed. The blending and lubrication operation is performed by rotating the blender up to a defined period of time at 12 RPM. The samples shall be collected after the Pre lubrication mixing stage at 10,15,20,25& 30-minute time intervals and after final Lubrication (3& 5 Minutes). Duplicate Samples shall be taken. Approximately 2 g of sample shall be taken from each location for analysis. The capacity of the blender is 200/100 Ltrs. as per the manufacturer’s recommendation. The performance of the equipment is challenged by taking the maximum capacity i.e. 70% and minimum i. e. 25% of the total working capacity. |
6.0 | ACCEPTANCE CRITERIA |
6.1 | The uniformity of content of paracetamol in the blend shall lie in the range of 90 to 110%. |
6.2 | The RSD of the blend shall not be more than 5%. |
7.0 MATERIAL REQUIRED FOR BLENDING
For a blender of 200 Ltrs volumetric capacity
Capacity of equipment in liter: 200 Ltrs.
Capacity of equipment in kg: 120 Kg
7.1 Total batch size: 80 kg (maximum capacity)
Sr. No. | Ingredients | Stage | Weight (in kg) |
1. | Sized Granules | Blending | 67.18 |
2. | Starch | Blending | 4.56 |
3. | Purified Talc | Blending | 5.50 |
4. | Magnesium Stearate | Blending | 2.76 |
7.2 Total batch size: 30 kg (minimum capacity)
Sr. No. | Ingredients | Stage | Weight (in kg) |
1. | Sized Granules | Blending | 25.19 |
2. | Starch | Blending | 1.70 |
3. | Purified Talc | Blending | 2.06 |
4. | Magnesium Stearate | Blending | 1.03 |
For a blender of 100 Ltrs volumetric capacity
Capacity of equipment in liter: 100 Ltrs.
Capacity of equipment in kg: 60 Kg
7.3 Total batch size: 40 kg (maximum capacity)
Sr. No. | Ingredients | Stage | Weight (in kg) |
1. | Sized Granules | Blending | 33.59 |
2. | Starch | Blending | 2.27 |
3. | Purified Talc | Blending | 2.75 |
4. | Magnesium Stearate | Blending | 1.38 |
7.4 Total batch size: 15 kg (minimum capacity)
Sr. No. | Ingredients | Stage | Weight (in kg) |
1. | Sized Granules | Blending | 12.60 |
2. | Starch | Blending | 0.85 |
3. | Purified Talc | Blending | 1.03 |
4. | Magnesium Stearate | Blending | 0.52 |
8.0 DIAGRAM OF BLENDER BIN 1200 L WITH SAMPLING POINTS:
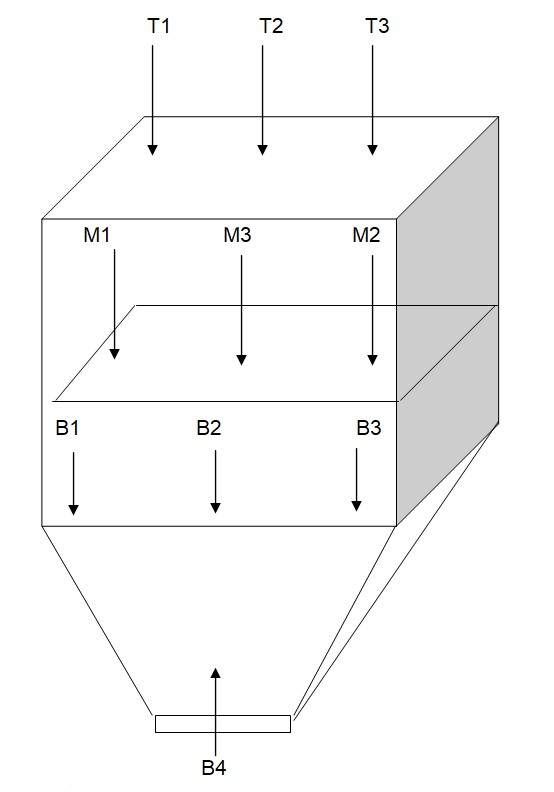
T1 = Top left
T2 = Top middle
T3 = Top right
M1 = Middle right
M2 = Middle
M3 = Middle left
B1= Bottom left
B2= Bottom middle
B3= Bottom right
B4= Discharge point
9.0 BLENDING
9.1 FOR BATCH SIZE OF 80 Kg Maximum. (Pre Lubrication Mixing)
Volumetric capacity of blender: 200 Liters
Capacity of equipment: 120 Kg
Pre-Lubrication Time: Speed of blender:
Location | Assay (in %) | |||||
BLEND UNIFORMITY | After 10 minutes | After 15 minutes | After 20 minutes | After 25 minutes | After 30 minutes | |
Active Ingredient | Paracetamol | Paracetamol | Paracetamol | Paracetamol | Paracetamol | |
T1 | ||||||
T2 | ||||||
T3 | ||||||
M1 | ||||||
M2 | ||||||
M3 | ||||||
B1 | ||||||
B2 | ||||||
B3 | ||||||
B4 | ||||||
Max. | ||||||
Min. | ||||||
Mean | ||||||
STD. DEV. (SD) | ||||||
RSD |
9.1.1 FOR BATCH SIZE OF 80 Kg Maximum. (Final Lubrication)
Final Lubrication Time:
Speed of blender:
BLEND UNIFORMITY (After 33 minutes) | ||||||||||
Location | T1 | T2 | T3 | M1 | M2 | M3 | B1 | B2 | B3 | B4 |
Paracetamol Assay (in %) | ||||||||||
Max. | ||||||||||
Min. | ||||||||||
Mean | ||||||||||
STD. DEV. | ||||||||||
RSD |
BLEND UNIFORMITY (After 35 minutes) | ||||||||||
Location | T1 | T2 | T3 | M1 | M2 | M3 | B1 | B2 | B3 | B4 |
Paracetamol Assay (in %) | ||||||||||
Max. | ||||||||||
Min. | ||||||||||
Mean | ||||||||||
STD. DEV. | ||||||||||
RSD |
INFERENCE:
————————————————————————————————————————–
————————————————————————————————————————–
Checked By:
Date:
9.2 FOR BATCH SIZE OF 30 Kg Minimum. (Pre Lubrication Mixing)
Volumetric capacity of blender: 200Liters
Capacity of equipment: 120 Kg
Pre-Lubrication Time: Speed of blender:
Location | Assay (in %) | |||||
BLEND UNIFORMITY | After 10 minutes | After 15 minutes | After 20 minutes | After 25 minutes | After 30 minutes | |
Active Ingredient | Paracetamol | Paracetamol | Paracetamol | Paracetamol | Paracetamol | |
T1 | ||||||
T2 | ||||||
T3 | ||||||
M1 | ||||||
M2 | ||||||
M3 | ||||||
B1 | ||||||
B2 | ||||||
B3 | ||||||
B4 | ||||||
Max. | ||||||
Min. | ||||||
Mean | ||||||
STD. DEV. (SD) | ||||||
RSD |
9.2.1 FOR BATCH SIZE OF 30 Kg Maximum. (Final Lubrication)
Final Lubrication Time:
Speed of blender:
BLEND UNIFORMITY (After 33 minutes) | ||||||||||
Location | T1 | T2 | T3 | M1 | M2 | M3 | B1 | B2 | B3 | B4 |
Paracetamol Assay (in %) | ||||||||||
Max. | ||||||||||
Min. | ||||||||||
Mean | ||||||||||
STD. DEV. | ||||||||||
RSD |
BLEND UNIFORMITY (After 35 minutes) | ||||||||||
Location | T1 | T2 | T3 | M1 | M2 | M3 | B1 | B2 | B3 | B4 |
Paracetamol Assay (in %) | ||||||||||
Max. | ||||||||||
Min. | ||||||||||
Mean | ||||||||||
STD. DEV. | ||||||||||
RSD |
INFERENCE:
————————————————————————————————————————–
————————————————————————————————————————
Checked By:
Date:
9.3 FOR BATCH SIZE OF 40 Kg Maximum. (Pre Lubrication Mixing)
Volumetric capacity of blender: 100Liters
Capacity of equipment: 60 Kg
Pre-Lubrication Time: Speed of blender:
Location | Assay (in %) | |||||
BLEND UNIFORMITY | After 10 minutes | After 15 minutes | After 20 minutes | After 25 minutes | After 30 minutes | |
Active ingredient | Paracetamol | Paracetamol | Paracetamol | Paracetamol | Paracetamol | |
T1 | ||||||
T2 | ||||||
T3 | ||||||
M1 | ||||||
M2 | ||||||
M3 | ||||||
B1 | ||||||
B2 | ||||||
B3 | ||||||
B4 | ||||||
Max. | ||||||
Min. | ||||||
Mean | ||||||
STD. DEV. (SD) | ||||||
RSD |
9.3.1 FOR BATCH SIZE OF 40 Kg Maximum. (Final Lubrication)
Final Lubrication Time:
Speed of blender:
BLEND UNIFORMITY (After 33 minutes) | ||||||||||
Location | T1 | T2 | T3 | M1 | M2 | M3 | B1 | B2 | B3 | B4 |
Paracetamol Assay (in %) | ||||||||||
Max. | ||||||||||
Min. | ||||||||||
Mean | ||||||||||
STD. DEV. | ||||||||||
RSD |
BLEND UNIFORMITY (After 35 minutes) | ||||||||||
Location | T1 | T2 | T3 | M1 | M2 | M3 | B1 | B2 | B3 | B4 |
Paracetamol Assay (in %) | ||||||||||
Max. | ||||||||||
Min. | ||||||||||
Mean | ||||||||||
STD. DEV. | ||||||||||
RSD |
INFERENCE:
————————————————————————————————————————–
————————————————————————————————————————–
Checked By:
Date:
9.4 FOR BATCH SIZE OF 15 Kg Minimum. (Pre Lubrication Mixing)
Volumetric capacity of blender: 100Liters
Capacity of equipment: 60 Kg
Pre-Lubrication Time: Speed of blender:
Location | Assay (in %) | |||||
BLEND UNIFORMITY | After 10 minutes | After 15 minutes | After 20 minutes | After 25 minutes | After 30 minutes | |
Active Ingredient | Paracetamol | Paracetamol | Paracetamol | Paracetamol | Paracetamol | |
T1 | ||||||
T2 | ||||||
T3 | ||||||
M1 | ||||||
M2 | ||||||
M3 | ||||||
B1 | ||||||
B2 | ||||||
B3 | ||||||
B4 | ||||||
Max. | ||||||
Min. | ||||||
Mean | ||||||
STD. DEV. (SD) | ||||||
RSD |
9.4.1 FOR BATCH SIZE OF 250 Kg Minimum. (Final Lubrication)
Final Lubrication Time:
Speed of blender:
BLEND UNIFORMITY (After 33 minutes) | ||||||||||
Location | T1 | T2 | T3 | M1 | M2 | M3 | B1 | B2 | B3 | B4 |
Paracetamol Assay (in %) | ||||||||||
Max. | ||||||||||
Min. | ||||||||||
Mean | ||||||||||
STD. DEV. | ||||||||||
RSD |
BLEND UNIFORMITY (After 35 minutes) | ||||||||||
Location | T1 | T2 | T3 | M1 | M2 | M3 | B1 | B2 | B3 | B4 |
Paracetamol Assay (in %) | ||||||||||
Max. | ||||||||||
Min. | ||||||||||
Mean | ||||||||||
STD. DEV. | ||||||||||
RSD |
INFERENCE:
————————————————————————————————————————–
————————————————————————————————————————–
Checked By:
Date:
10.0 | DEFICIENCY AND CORRECTIVE ACTIONS |
The following deficiency was verified and corrective actions were taken in consultation with the validation team. |
Description of deficiency: |
Corrective action(s) taken: |
Reviewed By:
Date:
11.0 Annexure (s):
Sr.No. | Annexure No. | Title of Annexure |
12.0 | BLENDER PERFORMANCE QUALIFICATION PROTOCOL FINAL REPORT: |
12.1 | SUMMARY: |
12.2 | CONCLUSION: |
12.3 FINAL REPORT APPROVAL
It has been verified that all tests required by this Blender Performance Qualification report are completed, reconciled, and attached to the Blender Performance Qualification protocol or included in the qualification summary report. Verified that all modifications and dissimilarities are documented, approved, and attached to this protocol.
The signature in the block below indicates that all items in this qualification report of Bin Blender have been reviewed and found to be acceptable and that all variations or discrepancies have been satisfactorily resolved. The equipment can be taken for production trial.
NAME | DESIGNATION | DEPARTMENT | SIGNATURE | DATE |
PRODUCTION | ||||
QUALITY CONTROL | ||||
QUALITY ASSURANCE |
Related Topics:
Auto Coater Operational Qualification Protocol/ Annexures
Design Qualification of Electric Stacker
Design Qualification Protocol for Vertical Laminar Reverse Flow

Naresh Bhakar is the Founder and Author at Pharmaguddu.com, bringing his extensive expertise in the field of pharmaceuticals to readers worldwide. He has experience in Pharma manufacturing and has worked with top Pharmaceuticals. He has rich knowledge and provides valuable insights and data through his articles and content on Pharmaguddu.com. For further inquiries or collaborations, please don’t hesitate to reach out via email at [email protected].