Learn about the Design Qualification protocol of Purified Water Generation System as per USP Standards along with a PDF sample.
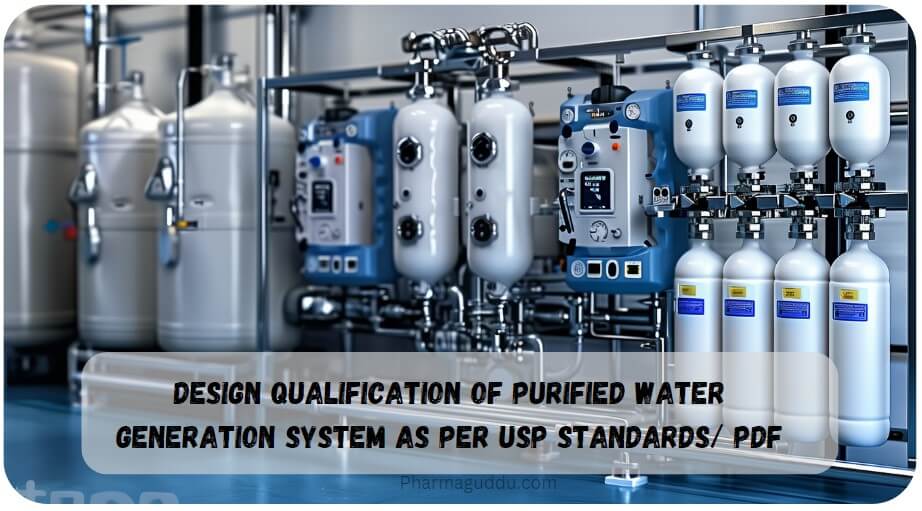
Design Qualification of Purified Water Generation System as per USP Standards Protocol:
NAME OF THE UTILITY / EQUIPMENT / SYSTEM / AREA | PURIFIED WATER GENERATION SYSTEM for XYZ Pharmaceutical Ltd. |
ID. NO. OF THE UTILITY / EQUIPMENT / SYSTEM / AREA | — |
VENDOR’S NAME & ADDRESS | XYZ Vendors along with their Address. |
DOCUMENT NUMBER | — |
Table of Contents:
SR. NO. | STAGE |
1 | OBJECTIVE & SCOPE |
2 | ACCEPTANCE CRITERIA |
3 | RESPONSIBILITY |
4 | SYSTEM DESCRIPTION (SYSTEM AND SUB-SYSTEM) |
5 | BASIS OF DESIGN AND ASSUMPTION |
6 | TECHNICAL SPECIFICATION |
7 | DRAWINGS REQUIRED |
8 | CALIBRATION OF INSTRUMENTS |
9 | SUPPORTING UTILITIES |
10 | PRE-QUALIFICATION CHECKLIST |
11 | REPORT APPROVAL DOCUMENTS REQUIRED |
12 | DESIGN QUALIFICATION |
13 | ABBREVIATIONS |
1. OBJECTIVE AND SCOPE:
1.1 OBJECTIVE
A) To prepare detailed specifications for all major components of equipment/instruments to ensure that user requirement Specifications and functional requirement specifications are achieved.
B) To design the equipment/instrument in conjunction with the design data in order to provide a basis for vendor, manufacturer & / or design engineer to design the system when the project begins.
1.2 SCOPE
Application to any equipment, system, facility, process & software programs.
a) When subjected to new installation
b) When the existing system is replaced with the new system.
c) When the existing system is subjected to up-gradation & / or modification.
All URS and FRS shall be defined by the user department in consultation with the engineering department, which should be finalized and mutually discussed with the system supplier, vendor & or manufacturer.
The design qualification is an essential part of the qualification mechanism and will serve as a basic document for the Validation Activity.
2. ACCEPTANCE CRITERIA:
2. A) PURIFIED WATER GENERATION SYSTEM
A.1 Equipment / Utility system shall conform to specifications which are as per the user requirements.
A.2 The Equipment / Utility/system shall conform to the predetermined requirements and a certificate is issued by the projects / Engineering Department.
DESIGN BASIS:
RAW WATER ANALYSIS :
- Turbidity: less than 1.2 NTU
- Color: less than 1 Hazen / Clear
- Odor: Unobjectionable
- pH: 6.9
- Total Dissolved Solids: 282.2 ppm
- Total Hardness as Caco3: 237.7 ppm
- Total Alkainity as Caco3: 248.2 ppm
- Calcium as Ca: 74.3 ppm
- Chloride as Cl: 18.7 ppm
- Magnesium as Mg: 12.5 ppm
- Nitrate as NO3: 4.1 ppm
- Sulphate as SO4: 14.5 ppm
- Iron as Fe: 0.2 ppm
- Coliform Bacteria (MPN INDEX): Less than 2 / 100 ml
- Silica as SiO2: 10 ppm. ( assumed)
Note:-
- For design purposes, we have considered the above parameters 20% excess i.e., TDS considered for design is 120ppm.
- Feed Water is free from pathogens like E- Coli, Pseudonymous, Salmonella
PRETREATMENT:
FOR Pressure Quartz Filter :
- No. of Units: 1 nos.
- Maximum Flowrate: 32 m3/hr
- Specific Velocity of Filtration: 15 m/hr
For Softening Plant:
- No. of Unit: 2 no. (1W + 1S)
- Maximum Flowrate: 28 m3/hr
- Output Between successive
- Regeneration: 290 m3
- No. of Working Hours. : 10 hrs.
RO SYSTEM:
FOR Reverse Osmosis System (Pass I) :
- Feed Flowrate: 6.4 m3/hr
- Permeate Flowrate: 4.5 m3/hr ( 4500 ltrs/hr)
- Reject Flowrate: 1.4 m3/hr ( 1400 ltrs/hr)
- Reject Recycle Flowrate: 0.9 m3/hr ( 900 ltrs/hr)
- Overall recovery: 70- 75%
FOR Reverse Osmosis System (Pass II) :
- Feed Flowrate: 4.5 m3/hr
- Permeate Flowrate: 3.6 m3/hr ( 3600 ltrs/hr)
- Reject Flowrate: 0.9 m3/hr ( 900 ltrs/hr)
- Overall recovery: 80- 85 %
FOR EDI Unit:
- Feed Flowrate: 3.6 m3/hr ( 3600 ltrs/hr)
- Treated Water Flowrate: 3.3 m3/hr ( 3300 ltrs/hr)
POST-TREATMENT:
FOR Ultra Filtration System :
- Feed Flowrate: 3.3 m3/hr
- Final Permeate Flowrate: 3.0 m3/hr ( 3000 ltrs/hr)
- Reject Flowrate: 0.3 m3/hr ( 300 ltrs/hr)
- Overall recovery: 90- 95 %
TREATED WATER QUALITY:
Outlet of Softener :
- Treated Water Hardness: Less than 5 ppm
Outlet of Second pass RO Unit:
- Online Conductivity: Less than 20 S/cm
Outlet of EDI Unit : ( Purified Water as per USP Standards )
- On-Line Conductivity: Less than 0.5 us/cm2
- Total Organic Carbon: Less than 200 ppb.
- Total Bacterial Count: Less than 50 CFU/ml
( Note. : TOC analyzer will be provided by the client.)
Outlet of UF Unit : ( Purified Water as per USP Standards )
- On-Line Conductivity: Less than 0.5 us/cm2
- Total Organic Carbon: Less than 50 ppb.
- Total Bacterial Count: Less than 10 CFU/ml
( Note. : TOC analyzer will be provided by the client.)
(Note: With the change in the incoming water parameters, the treated water quantity & quality may be affected at different stages of the plant.)
3.0 RESPONSIBILITIES:
User Dept: For providing user requirements (Technical and cGMP)
Works Manager: To review the specifications from installation and Maintenance aspects.
QA: To review the specification from GMP Aspects
Vendor: To review and agree upon the requirements.
4. SYSTEM DESCRIPTION (SYSTEM AND SUB-SYSTEM):
The Fully Automated PLC-operated high-purity water Treatment Plant is designed to generate 200 Ltrs/ hr. of Purified Water as per USP Standards.
PRE TREATMENT :.
- Raw Water Pump. (Client scope)
- Pressure Quartz Filter. (32 m3/hr)
- Softener Unit. (28 m3/hr)
- Chlorination system.
- Soft Water Storage Tank. (Client Scope)
REVERSE OSMOSIS SYSTEM :
- RO Feed Pumps.
- SMBS Dosing System
- ORP Analyser along with auto dumping valve.
- Antiscalant Dosing System.
- Auto pH Correction System.
- 5-micron Cartridge Filter.
- First and Second pass RO High-Pressure Pump.
- First and Second pass Reverse Osmosis membranes along with High-Pressure housing. (Chemically Sanatizable)
- Conductivity meter with Alarm.
POST-TREATMENT:
- EDI Feed Pump.
- Electro – Deionisation Unit. (Hot Water Sanatizable)
- Conductivity meter.
ULTRA-FILTRATION SYSTEM:
- 500 ltrs. SS 316L UF Feed Water Tank complete with vent filter, level switch, and compound pressure gauge.
- UF Feed cum Fast Flush pump.
- Ultra-filtration membrane.
4.1 SYSTEM DESCRIPTION:
The raw water pump will feed raw water from the bore well to the pressure quartz filter @ 32.0 m3/hr.
Pressure Quartz Filter is a vertical down flow vessel containing pure graded silex quartz as a filtering media. The vessel is fabricated in MS epoxy-painted vessel. The water generated at the outlet of Pressure Quartz filter will have suspended solids of less than 5 ppm. A pressure Quartz filter is provided with a Manual Backwash & Rinse arrangement. (Note that the inlet suspended solid load should not be more than 20 ppm.).
The filtered water will be feed to a Softener Unit, which will remove the calcium and magnesium hardness present in the raw water. The hardness of soft water will be less than 5 ppm.
This softened water will be collected in a soft water storage tank. The soft water tank is provided with level switch which will automatically start and stop raw water feed pump depending upon the level in the tank. (Client Scope)
Water from Soft water tank is feed to RO – EDI system by means of RO feed pump.
Sodium Metabisulphate is then dosed in this chlorinated water to neutralize the free chlorine (excess chlorine) present in the filtered water.
ORP Analyser is provided so as to check the absence of chlorine in the feed water to the RO System. If free chlorine is sensed in the feed water it will give an indication on the panel & open the dumping valve and dump the high ORP water for 120 secs. & even if the ORP value is not below the set point it will trip the system.
The antiscalant dosage system is then dosed in filtered water to avoid scale formation on the RO membranes.
This water is further processed through a 5-micron Cartridge Filter to trap the suspended solids. This will avoid choking of RO membranes due to suspended solids.
This filtered water is then fed to the Reverse Osmosis Pass I System by means of a High-Pressure Vertical multistage pump I with SS304 wettable parts of M/s. Grundfos, Denmark. The Reverse Osmosis system will generate 4500 liters/hr water with an overall recovery of 70 – 75%. This water is then further fed to the Reverse Osmosis Pass II System by means of a High-Pressure Vertical multistage pump II with SS304 wettable parts of M/s. Grundfos, Denmark. The Reverse Osmosis system will generate 3600 liters/hr water with an overall recovery of 80 – 85%. The generated water will have total dissolved solids of less than 20 ppm. The semi-permeable reverse osmosis membrane has molecular weight cut off less than 150 M.W.C.O. The reverse osmosis membrane acts as a positive barrier to remove dissolved solids, organic compounds & bacteria.
The Reverse Osmosis System consists of a thin film composite type reverse osmosis membrane of hydraunautics, USA. The material of construction of the RO membrane is Polyamide. The RO membrane is housed in the High-Pressure SS 316 Housing having TC end connection.
The Permeate water from the RO system will be fed to the Electro deionization Unit (EDI) having a Feed flow rate of 3300 Liters. The EDI system has a recovery of 95%. The 5% reject water from EDI can be fed back to the feed of RO System & hence the overall recovery of the system is 100% (approx.).
The water generated from the outlet of EDI will be as per USP Standards for Purified Water. (Conductivity less than 1.25s/cm & TOC less than 500 ppb)
Post Ultra-Filtration system is provided after EDI unit to bring down TOC to less than 50 ppb & Bacterial count to less than 10 CFU/ml.
5. BASIS OF DESIGN AND ASSUMPTION:
5.1 FEED WATER SAMPLE:
The system design is based on the feed water analysis provided by the customer as per Annexure A.
5.2 PRODUCT WATER QUALITY:
(Purified Water as per USP Standards)
Treated Water Hardness: Nil
Conductivity: Less than 1.25 s/cm
Total Bacterial Count: Less than 50 CFU/ml.
Total Organic Contamination: Less Than 200 ppb
(Note: With the change in the incoming water parameters, the treated water quantity & quality may be affected at different stages of the plant.)
5.3 FACILITY OPERATION:
The plant operation will be for 8-10 hours/day.
5.4 SYSTEM PRESSURE & TEMPERATURE
The Purified Water systems will be designed to deliver the product water to various points of use at the following process parameters.
POINT OF USER PROCESS PARAMETERS for PW
Pressure-at POU’s | > 1 bar |
Temperature at POU’s | Ambient |
ANNEXURE – A
RAW WATER ANALYSIS :
- Turbidity: less than 1.2 NTU
- Color: less than 1 Hazen / Clear
- Odor: Unobjectionable
- pH: 6.9
- Total Dissolved Solids: 282.2 ppm
- Total Hardness as Caco3: 237.7 ppm
- Total Alkainity as Caco3: 248.2 ppm
- Calcium as Ca: 74.3 ppm
- Chloride as Cl: 18.7 ppm
- Magnesium as Mg: 12.5 ppm
- Nitrate as NO3 : 4.1 ppm
- Sulphate as SO4: 14.5 ppm
- Iron as Fe: 0.2 ppm
- Coliform Bacteria (MPN INDEX): Less than 2 / 100 ml
- Silica as SiO2: 10 ppm. ( assumed)
Note:-
- For design purposes, we have considered the above parameters 20 % excess i.e., TDS considered for design is 120ppm.
- Feed Water is free from pathogens like E- Coli, Pseudonymous, Salmonella
6. TECHNICAL SPECIFICATIONS:
6. A PRETREATMENT
6.A.1 RAW WATER PUMP (Client Scope)
- Quantity: One
- Type: Centrifugal Monobloc Pump
- Flow rate: 32 m3/hr
- Pressure: 2.5 kg / cm2
- Material of Construction: SS 304
- Make: Grundfos
6.A.2 PRESSURE QUARTZ FILTER
- No. of Unit: One
- Type: Vertical Downflow
- Normal Flowrate: 32 m3/hr
- Pressure Drop at Max. Flow: 0.5 kg/cm2
- Max. Work Pressure: 3.5 kg/cm2
- Test Pressure: 5.0 kg/cm2
- MOC of Vessel: IS 2062 Grade ‘A’
- Filter Media: Graded SILEX Pure Quartz. Time required for Backwash: 8 – 10 Minutes.
- Diameter: 1500 mm
- Height on straight: 1800 mm
- Pipe Size: 80 mm NB
- Valve type: CI Butterfly Valves
- Make of Valves: Audco
- Pressure Gauges: 100 mm dial
- Pressure Gauges Make: Waaree
- Material of Construction: MS Epoxy Coated
6.A.3 HYDROPURE SOFTENER
- No. of Unit: Two (1W + 1S)
- Type: Vertical Downflow
- Normal Flowrate: 28 m3/hr
- Output Betn. Successive Regn. : 290 m3
- Total hardness: 300 ppm
- Pressure Drop at Max. Flow: 0.5 kg/cm2
- Max. Work Pressure: 3.5 kg/cm2
- Max. Test Pressure: 5.0 kg/cm2
- Diameter: 1500 mm
- Height on straight: 1500 mm
- Resin quantity: 2050 ltrs.
- Regenerant : 340 kgs. 100% NaCl
- Type of Resin: Sodium Based Resin – (C – 20 Na)
- Make of Resin: Auchtel
- Reg. Tank Capacity: 1250 liters.
- Pipe Size: 80 mm
- Pressure Gauges: 100 mm dial
- Pressure Gauges Make: Waaree
- Material of Construction: MSR/L
- Make of Vessel: M/s. Hydropure
6.A.4 NaOCl DOSING SYSTEM
- Quantity: One
- Type: Positive Displacement Pump
- Flow Range: 0.5 to 5 LPH
- Max. Working Pressure: 5.0 kg / cm2
- MOC of Dosing Tank: HDPE
- Dosing Tank: 100 Ltrs. Provided
- Low-Level Switch: Provided
- Make: M/s Grundfos
6. B REVERSE OSMOSIS SYSTEM:
6.B.1 RO FEED PUMP
- Quantity: One
- Type: Centrifugal Monobloc Pump
- Flow rate: 5500 LPH
- Pressure: 2.5 kg / cm2
- Material of Construction: SS 304
- Make: Grundfos.
6.B.2 SMBS DOSING SYSTEM
- Quantity: One
- Type: Positive Displacement Pump
- Flow Range: 0.5 to 5 LPH
- Max. Working Pressure: 5.0 kg / cm2
- MOC of Dosing Tank: SS 316
- Dosing Tank: 25 Ltrs. Provided
- Low-Level Switch: Provided
- Make: M/s Grundfos
6.B.3 ANTISCALANT DOSING SYSTEM
- Quantity: One
- Type: Positive Displacement Pump
- Flow Range: 0.5 to 5 LPH
- Max. Working Pressure: 5.0 kg / cm2
- MOC of Dosing Tank: SS 316
- Dosing Tank: 25 Ltrs. Provided
- Low-Level Switch: Provided
- Make: M/s Grundfos
6.B.4 5-MICRON CARTRIDGE FILTER
- No. of Unit: One
- Type of cartridge: Spun bounded type
- Rating: 5 micron
- Flowrate: 5500 LPH
- No. of Cartridge : 3 nos. 20” long
- MOC of Cartridge Housing: SS 316.
- MOC of Cartridge: PP Spun Bounded
6.B.5 REVERSE OSMOSIS HIGH-PRESSURE PUMP – I
- No. of Unit: One
- Type of Pump: Vertical Multistage Pump
- Maximum Flowrate: 6400 LPH
- Operating Pressure: 12 kg/cm2
- Material of Construction: SS 304 Wettable parts.
- Make: Grundfos
6.B.6 REVERSE OSMOSIS MEMBRANES Pass – I
- No. of Membrane: Five
- Size of Membrane: 8” Dia & 40” Long
- Type of Membrane: Thin Film Composite
- Material of Construction: Polyamide
- Make of Membrane: Hydraunautics USA
- Type of sanitization: Chemical
6.B.7 REVERSE OSMOSIS MEMBRANES HOUSING Pass – I
- No. of Housing: Two
- Maximum Flowrate: 4500 LPH
- Material of Construction: SS 316
6.B.8 REVERSE OSMOSIS HIGH-PRESSURE PUMP – II
- No. of Unit: One
- Type of Pump: Vertical Multistage Pump
- Maximum Flowrate: 4500 LPH
- Operating Pressure: 10 kg/cm2
- Material of Construction: SS 304 Wettable parts.
- Make: Grundfos
6.B.9 REVERSE OSMOSIS MEMBRANES Pass – II
- No. of Membrane: Three
- Size of Membrane: 8” Dia & 40” Long
- Type of Membrane: Thin Film Composite
- Material of Construction: Polyamide
- Make of Membrane: Hydraunautics USA
- Type of sanitization: Chemical
6.B.10 REVERSE OSMOSIS MEMBRANES HOUSING Pass – II
- No. of Housing: One
- Maximum Flowrate: 3600 LPH
- Material of Construction: SS 316
6. C POST-TREATMENT
6.C.1 EDI FEED PUMP
- No. of Unit: One
- Type of Pump: Horizontal Multistage Pump
- Maximum Flowrate: 3600 LPH
- Operating Pressure: 2.5 kg/cm2
- Material of Construction: SS 316
- Make: Grundfos
6.C.2 EDI-UNIT
- No. Of Unit: One
- Type of EDI: Hot Water Sanitizable
- Normal Flowrate: 3300 ltrs/hr
- End Connection: 1” TC
- Operating Voltage DC: 200-350 V DC
- Concentrate Flowrate (Reject): 250 – 300 ltrs/hr
- Pressure Drop across concentrate: 0.5 kg/cm2
- Max. Working Pressure: 2.5 kg/cm2
- Model No. : IP – LXM – 24HI – 3
- Make of EDI: M/s. Ionpure, USA
6.C.3 DIGITAL TYPE CONDUCTIVITY METER
No. of Units: Two
Type: Digital Display
Range : 0-100 s/cm & 0 – 10 s/cm
Location :
- Outlet of Reverse Osmosis System
- Outlet of EDI
- Make Megh Electronics.
6.D. POST ULTRAFILTERATION
6.D.1 ULTRAFILTRATION FEED CUM FAST FLUSH PUMP
- No. of Unit: One
- Type of Pump: Horizontal Multi-stage Pump
- Normal Flowrate: 3.6 m3/hr
- Operating Pressure: 2.5 kg/cm2
- Material of Construction: SS 316
- Make: Grundfos
6.D.2 ULTRAFILTRATION SYSTEM
- No. of Unit: One
- Type of Membrane: Hollow fiber membrane
- Make of Membrane: Koch, Membrane
- Size of Membrane: 5” Dia. X 43” Height
- Nos. of Membrane : 3 no.
- Maximum Feed Flowrate: 3.3 m3/hr
- Overall recovery of the system. : 90 – 95%
- Maximum Permeate Flowrate: 3.0 m3/hr.
- Provision for Fast flush operation: Provided in Automode.
- Operating Pressure: 2.5 – 3.0 kg/cm2
- Type of Sanitization: Hot Water ( 85°C)
6.E.INSTRUMENTATION & OTHER ITEMS
6.E.1 PRESSURE GAUGES:
I) Specification: Pressure Gauge with Plastic Body & brass internals, glycerin filled.
Make: Make Name
Size of Gauge: 100 mm Dial
Range : 0-7 kg/cm2
Location:
1 Inlet of Pressure Quartz Filter.
2 Outlet of Pressure Quartz Filter.
II) Specification: SS Pressure Gauge with brass internals with glycerin filled.
Make: Make Name
Size of Gauge: 65 mm Dial
Range : 0-21kg/cm2
Location:
1. Outlet of High-Pressure Pump I & II
2. Reject of RO Pass I & II System
III) Specification: Pressure Gauge with Plastic Body & brass internals, glycerin filled.
Make: Make Name
Size of Gauge: 65 mm Dial
Range: 0-7 kg/cm2
Location: At Jacket safety assembly (PW tank)
IV) Specification: Pressure Gauge with SS & brass internals, glycerin filled.
Make: Make Name
Size of Gauge: 65 mm Dial
Range: 0-7 kg/cm2
Location:
1. Discharge of RO Feed Pump.
2. Inlet of 5 microns Cartridge Filter
3. Outlet of 5 microns Cartridge Filter
4. Discharge of EDI Feed Pump.
5. Discharge of Post UF Feed Pump.
6.E.2 ROTAMETER:
Specification: Acrylic Rotameter.
Make: Make Name
Range: Minimum 1.5 times the feed flow.
Location: 1. Discharge of Raw water Pump.
2. Inlet of EDI Concentrate.
6. E..3 ORP SENSOR, TRANSMITTER & CONTROLLER: (ORP)
Specification: ORP Sensor, Two Wire Transmitter & Controller.
Make: Make Name
Location: Inlet of first pass of the RO system.
6.E.4 CONDUCTIVITY METER:
Specification: Conductivity Sensor & Controller.
Make: Make Name
Location: 1. Outlet of RO Pass I & II System. (CI 1) – 0-200 s/cm( Megh)
2. Outlet of EDI Unit (CI2)- 0-20 s/cm (Megh)
6.E.5 PRESSURE SWITCH:
Specification: Seamless Bellow type Pressure switch.
Make: Make Name
Location: 1. Low-Pressure Switch at inlet of High-Pressure Pump I & II
2. High-Pressure Switch at outlet of High-Pressure pump I & II
3. Low Pressure Switch at inlet of EDI Unit.
6.E.6 LEVEL SWITCH:
Specification: Magnetic Type Level switch.
Make: Make Name
Location :
1. Anticsalent Dosing System.
2. Sodium Meta Bisulphate Dosing System.
3. NaOCl Dosing System.
6.E.7 FLOW METER:
Specification: Paddle – Wheel Type
Make: Make Name
Location :
1 Discharge of RO Feed Pump.
2 RO Pass I Reject.
3 RO Pass II Permeate.
4 Discharge of Post UF Feed Pump.
5 Permeate of Post UF.
7. DRAWINGS REQUIRED:
SR. NO | DESCRIPTION | DRAWING NO | REV |
1 | P&ID for Purified water generation System | RO | |
2. | Drawing for Panel | RO | |
3 | Drawing Pumps | RO | |
4. | Drawing for Dosing System | RO | |
5. | Drawing RO Housing | RO | |
6 | RO Storage Tank Fabrication Drawing | RO | |
7. | Skid Drawing | RO |
8. CALIBRATION OF INSTRUMENTS:
Sr. No | Components | Make | Qty | Size | Purpose | Model No./Serial No. |
1. | Conductivity Meter | — — | 2 1 | 0-200us/cm 2 Nos 0-20us/cm 1 Nos | To measure conductivity | |
2. | Rotameters | — | 2 | 0 – 4m3/hr 0 – 500 m3/hr | To measure Flow | |
3 | Pressure Gauges | — | 9 | 0 – 7 Kg/cm2 – 5 nos. 0– 21 kg/cm2 –4 nos | To measure pressure. | |
4 | Pressure switch | — | 5 | 0 – 3 kg/cm2, 3nos 4 – 17 kg/cm22nos | To give a signal at set pressure. | |
5. | ORP sensor and analyzer | — | 1 | -1200 to +1200mv | To sense free chlorine. | |
6. | Flow Meter | — | 5 | 0 – 8 m3/hr | To Measure Flow |
9. SUPPORTING UTILITIES:
SR. NO | Equipments / Instruments | Location | Utilities | Specification | Scope |
1 | Pre-treatment | Pretreatment Plant | Water | 32000 LPH | MPL |
2 | RO-EDI Plant | RO Plant Room | Power | 3 phase, 440V, 50 Hz | MPL |
3. | Control Panel | RO Plant Room | Compressed Filtered regulated Air | 3.5 Kg/cm2 | MPL |
4. | Pre-treatment | Pretreatment Plant | Power | 3 phase, 440V, 50Hz | MPL |
10. PRE-QUALIFICATION CHECKLIST:
10.1 HYDRAULIC PRESSURE TEST
10.2 DOCUMENTATION CHECK
10.3 INTERLOCK CHECKS
10.4 OPERATIONAL CHECKS
11. LIST OF DOCUMENTS REQUIRED FOR GENERATION SYSTEM:
CODE | DOCUMENTS REQUIRED |
A | Manufacturer’s Manuals – Preventive Maintenance (O.M.) |
B | MOC Certificate |
C | Leak Test Reports / Hydro Test Report |
D | Sanitization Reports |
E | Cleaning / Flushing Reports |
F | Pump Performance Curves |
J | Manufacturer’s Catalogue |
L | Test Certificate |
M | Guarantee / Warranty Certificate |
N | Basis of Design |
Q | Welding Protocol |
12. DESIGN QUALIFICATION REPORT APPROVAL:
Approved / not approved: – _________________________________________________________
NAME | DESIGNATION | SIGNATURE | DATE |
Works Manager | |||
QA Head | |||
Vendor |
13. ABBREVIATIONS:
ABBREVIATION | DESCRIPTION |
URS | User required specification |
FRS | Functional required specification |
GMP | Good manufacturing practice |
QA | Quality Assurance |
UV | Ultraviolet |
UF | Ultra Filtration |
USP | United States Pharmacopoeia |
WHO | World Health Organization |
RO | Reverse Osmosis |
SMBS | Sodium MetaBi Sulphite |
CIP | Clean in place |
PPM | Mg/ltrs OR Parts per Million |
P&ID | Process Flow & Instrumentation Diagram |
Ltrs/hr | Liters per Hour |
CFU/ML | Colifrom plate count per ml |
T/C | Tri Clover |
MPL | Macleods Pharma Limited. |
ADS | Antiscalant Dosing System |
NaOCl | Sodium Hypo Chloride |
PQF | Pressure quartz filter |
Don’t Miss This…
- Design Qualification Of FBD in Pharmaceuticals
- Installation Qualification Protocol for Automatic four head Vial Sealing Machine
- Operational Qualification of Automatic High-Speed Linear Vial Washing Machine
- IQ of High-Speed Linear Vial Washing Machine
- Operation Qualification of Sterilizing and Depyrogenation Tunnel
- Installation Qualification of Sterilizing and Depyrogenation Tunnel (Protocol)

Naresh Bhakar is the Founder and Author at Pharmaguddu.com, bringing his extensive expertise in the field of pharmaceuticals to readers worldwide. He has experience in Pharma manufacturing and has worked with top Pharmaceuticals. He has rich knowledge and provides valuable insights and data through his articles and content on Pharmaguddu.com. For further inquiries or collaborations, please don’t hesitate to reach out via email at [email protected].