Design Qualification Protocol Vertical Laminar Reverse Flow Powder Containment Station has the following Table of content:
- Objective
- Scope
- Responsibility
- Review of URS (User Requirement Specification)
- Purchase Order Details
- Machine Description
- Technical specification
- Technical specifications of the sub-components/bought-out items, and their make, model & quantity, and backup records/brochures
- Details of utilities
- Identification of components for calibration
- Material of construction of all components
- Drawings
- P & ID Diagram for reference & approval
- Equipment orientation with room layout
- Brief process description
- Safety features
- FAT/SAT procedure
- Change control procedure
- Design Qualification Protocol Report Approval
- Appendix
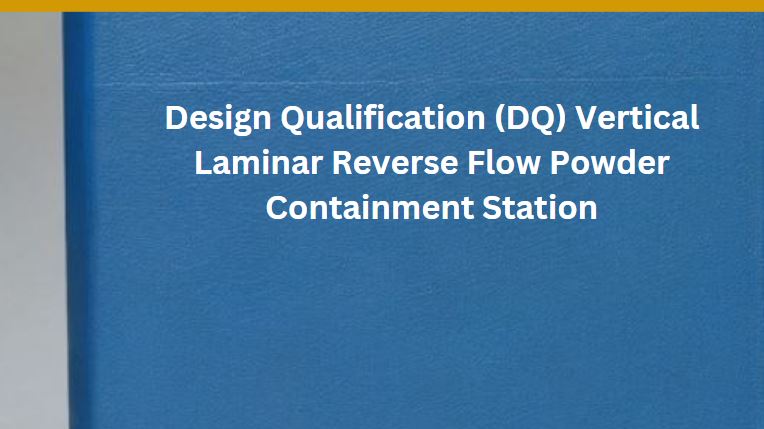
1.0 OBJECTIVE of Design Qualification Protocol:
To design, engineer, and supply the Vertical Laminar Reverse Flow Powder Containment Station, Model: (Modal Name) to assure that the machine is manufactured as per the URS and complies with the Scope of Supply.
To prove that each operation proceeds as per the design specification and the tolerances prescribed in the document. The validation procedure is set for the complete satisfaction of the customer & building the confidence of the user about the machine.
2.0 SCOPE:
The scope of this qualification document is limited to the Design Qualification of the Vertical Laminar Reverse Flow Powder Containment Station, Model: XYZ for Company name Pharmaceuticals. This qualification document is part of a validation activity for the Vertical Laminar Reverse Flow Powder Containment Station, Model: XYZ.
Every “Supplier Name” Laminar Air Flow System is capable of maintaining a Class-100 work area.
3.0 RESPONSIBILITIES:
CLIENT:
- To provide the URS for the equipment.
- To perform the Factory Acceptance Test (FAT).
MANUFACTURER:
- To design, engineer, and provide the complete technical details of the equipment about its design qualification protocol viz.
- (Machine overview,
- Specifications of the sub-components/bought-out items, and their make, model & quantity.
- Identification of components for calibration
- Material of construction of equipment.
- Brief process description
- Safety features.
- Installation requirements
- To facilitate the client for the Factory acceptance test of the machine at their works/ site.
- To confirm the safe delivery of the equipment to the user site.
- To ensure that no unauthorized and/or unrecorded design modifications shall take place. If at any point in time, any change is desired in the mutually agreed design, the Change control procedure shall be followed and documented in the Design Change Control Format.
- To ensure the proper installation and commissioning of the equipment.
4.0 REVIEW OF USER REQUIREMENTS SPECIFICATION (URS):
DESCRIPTION | SPECIFICATIONS |
Equipment | Vertical Laminar Reverse Flow Powder Containment Station |
Specification | Class 100 Vertical Laminar Reverse Flow Powder Containment Station In S.S. 304(16G) construction, comprising as; standard features; MINIPLEAT HEPA filters 0.3µ; Prefilter 5µ; Intermediate filters (0.3µ 50% DOP HEPA); suitable motor blower assembly; MINIPLEAT HEPA filter for exhaust; plenum for prefilter and air circulation; SS filter protective grilles; white light; Stainless steel double walled side panels (PUF filled); Stainless steel in-built covings (all inside corners) to avoid dust accumulation; feather touch ON/OFF switches for blower & light; extra electrical points with switches; 3-off Magnehelic gauges indicate filter loading on supply and return sides; separate control panel box in S.S. 304(16G) Construction accommodating electrical fittings like; MCBs and on/off switches to avoid dust accumulation. |
Overall Dimensions | 2050mmWx2260mmDx2535mmH |
Process | Vertical Laminar Reverse Flow Powder Containment system is capable of maintaining a Class 100 work area meeting all requirements as per Cgmp |
Material of construction | The body of Equipment is of S.S. 304 construction. HEPA filter [frame] construction Aluminium extrusion, food grade gasket on both sides. Pre Filter [frame] construction: S.S.304 Motor Blower construction MS powder coated |
Operation of Laminar Air Flow System | Switching of Laminar Air Flow by pressing the ‘ON’ switch. After getting the required differential pressure on the Magnehelic gauge, work can be carried out. |
Brief Process Description | These are Vertical Laminar Reverse Flow Cleanair Work Stations with HEPA-filtered air sweeping the area from top to bottom to protect the products from contamination as well as preventing the operators from inhaling potentially harmful active materials during sampling, weighing, and/or dispensing powders. The filtered air picks up aerosolized particles and forces them to travel in a predetermined flow pattern until trapped by the scavenging filters on the back panel of the unit. The airflow pattern is so maintained that the operators in the safe zone (approx 300 to 450mm into the open front of the cubicle) are not exposed to the dispersed particles. The return air passes through intermediate filters and enters the positive pressure plenum to be pushed downward through HEPA filters. 10% of the air is exhausted out of the zone through HEPA filters for maintaining a slight negative pressure inside to ensure that at no point in time, air movement can be outward. |
Calibration | All components that require calibration shall be identified and calibrated. Calibration certificates are to be provided at the time of Installation qualification. |
Qualifications/ Documentation | The manufacturer shall complete and provide the documents about Design, Installation, and Operation Qualification, equipment validation, and detailed functional specifications. Information of purchased/bought-out parts. Circuit’s details. |
Control system | The equipment shall be controlled through an Electrical Switches system. |
Related: Risk Assessment Protocol
5.0 Purchase Order Details :
P.O. No. XYZ Date: 28.11.23 is enclosed.
6.0 Machine Description :
Class 100 Vertical Laminar Reverse Flow Powder Containment Station In S.S. 304 construction, comprising as; standard features; MINIPLEAT HEPA filters 0.3µ; Prefilter 5µ; Intermediate filters 3µ; suitable motor blower assembly; MINIPLEAT HEPA filter for exhaust; plenum for prefilter and air circulation; SS filter protective grilles; white light; Stainless steel double walled side panels (PUF filled); Stainless steel in-built covings (all inside corners) to avoid dust accumulation; feather touch ON/OFF switches for blower & light; extra electrical points with switches; 3-off Magnehelic gauges t indicate filter loading on supply and return sides; table with fully perforated stainless steel top mounted on independent stainless steel stands (Size: 610mmWx610mmDx760mmH); separate control panel box in S.S. 304 Construction accommodating electrical fittings like; MCBs and on/off switches to avoid dust accumulation.
7.0 Technical Specifications:
Pre-filters:
a) Size/Dimensions of filter: 30”x24” x 3”, 03 Nos.
b) Filter makes: Supplier Name
c) MOC of filter media: Fibre Glass Media
d) Filter efficiency: 60-65% on ASHRAE STD 52-76 equivalent to 98% [5µ] on BS 2831 Test Dust II.
e) Gasket: Closed-cell neoprene gasket (Food Grade)
f) Testing Codes and practices: ASHRAE STD 52-76 / BS 2831 Test Dust II
g) Face velocity: 200 to 300 FPM
Intermediate Pre-filters:
h) Size/Dimensions of filter: 24”x18” x 6”, 03 Nos.
i) Filter make: Supplier Name
j) MOC of filter media: Fibre Glass Media
k) Filter efficiency: 70-75% on ASHRAE STD 52-76 equivalent to 99% [3µ] on BS 2831 Test Dust II.
l) Gasket: Closed-cell neoprene gasket (Food Grade)
m) Testing Codes and practices: ASHRAE STD 52-76 / BS 2831 Test Dust II
n) Face velocity: 200 to 300 FPM
HEPA Filters:
a) Size/Dimension/Qty of filter: 36”wx30”dx3”h – 4 Nos.
b) 24”wx6”dx3”h – 2 Nos.
c) Filter make: TSupplier Name
d) MOC of filter media: Micro Fibre Glass Media
e) Filter efficiency: 99.997% down to 0.3 micron
f) Gasket: Closed-cell neoprene gasket (Food Grade)
g) Testing Codes and practices: IES-RP-CC-001-86
h) Face velocity: 90 ± 20% FPM
Blower – Motor:
Motor Blower – 1/2 HP, Single Phase, 1440 RPM – 04 Nos.
Make: Supplier Name
Centrifugal fan with high capacity forward curved blower (in M.S. powder coated construction), direct drive, sized to provide required airflow volume over the anticipated life of the HEPA filter. Special bearings to ensure low noise levels. Fan: Statically and dynamically balanced. Fan [Airtek Make] size: 210x170mm – 04 No.
8.0 Technical specifications of the sub-components/bought-out items, and their make, model & quantity, and backup records/brochures.
S.N. | Name of Item | Specifications | Qty. | Make |
8.1 | Magnehelic Guage | Range 0-50mm Range 0-25mm Range 0-10mm | 01 No. 01 No. 01 No. | Make Name |
8.2 | Impellers in Aluminium | 210x170mm | 01 Set | Make Name |
8.3 | Motor | 0.5 HP 1440 RPM | 04 Set | Make Name |
8.4 | MCB | 4 Amps, Single Pole | 01 Set | Make Name |
8.5 | White Lights | 230 V | 01 set | Make Name |
8.6 | Feather touch On/off switches | 15 Amp | 01 Set | Make Name |
8.7 | The electrical point with switches | 15 Amp | 01 Sets. | Make Name |
9.0 DETAILS OF UTILITIES
Description | Specifications |
1 Electrical: | |
Phase | 1 Phase |
Voltage | 230V |
Frequency | 50Hz +/- 3% variations |
10.0 IDENTIFICATION OF COMPONENTS FOR CALIBRATION
In the Vertical Laminar Reverse Flow Powder Containment Station following are the components, which need calibration. They shall be calibrated during/before installation of the equipment at the site:
Sr. No. | Description |
1.0 | HEPA filter |
2.0 | Magnehelic Guage |
11.0 MATERIAL OF CONSTRUCTION
S.NO. | COMPONENT DESCRIPTION | MOC |
1. | Modules of Equipment | S.S.304 (18 G) |
2. | HEPA Filter [Frame] | Aluminium |
3. | Pre Filter [Frame] | S.S. |
4. | Table | S.S. |
5. | Side Panel | S.S. |
12.0 DRAWINGS
12.1 Layout drawing No. –
12.2 Equipment Drawing No: – EQ/RF/X.X/XXXX
12.3 Circuit Diagram No.
13.0 P & ID DIAGRAM FOR REFERENCE & APPROVAL
N.A.
14.0 EQUIPMENT ORIENTATION WITH ROOM LAYOUT:
Attached as annexure – DQ/ANX/XXXX
Approved status: APPROVED/NOT APPROVED
Any change in the approved orientation layout: Yes/No
If yes, the reason for change ……………………………………………………………. ……………………………………………………………………………………………
15.0 BRIEF PROCESS DESCRIPTION:
These are Vertical Laminar Reverse Flow Cleanair Work Stations with HEPA-filtered air sweeping the area from top to bottom to protect the products from contamination as well as preventing the operators from inhaling potentially harmful active materials during sampling, weighing, and/or dispensing powders. The filtered air picks up aerosolized particles and forces them to travel in a predetermined flow pattern until trapped by the scavenging filters on the back panel of the unit. The airflow pattern is so maintained that the operators in the safe zone (approx 300 to 450mm into the open front of the cubicle) are not exposed to the dispersed particles. The return air passes through intermediate filters and enters the positive pressure plenum to be pushed downward through HEPA filters. 10% of the air is exhausted out of the zone through HEPA filters for maintaining a slight negative pressure inside to ensure that at no point in time, air movement can be outward.
16.0 SAFETY FEATURES:
- Do keep the station clean and orderly.
- periodic maintenance is required for checking motor blowers,
Magnehelic Gauges. - The periodic validation of the HEPA filter
- Periodic Calibration of the Instrument
17.0 FAT/SAT PROCEDURE:
Factory Acceptance Test Procedure shall be as follows:
After the completion of the erection work of the machine, the client shall be informed to perform the factory acceptance test (FAT) at a workshop or Site Acceptance test at the site.
Client shall perform the FAT at the manufacturer site or SAT at the client site and record all the data in the prescribed FAT or SAT document as per the details given below:
- Design Verification
- Test Criteria
- Deficiency & Corrective Action Report
- Final report
18.0 CHANGE CONTROL PROCEDURE:
Change in the agreed design shall be addressed through the change control procedure.
19.0 DESIGN QUALIFICATION PROTOCOL REPORT APPROVAL
19.1 Summary:
Prepared by: Supplier Name Date: |
Checked by: Date: |
Approved by: Date: |
19.2 Certification:
Remark: Approved/Not Approved
Department | Name | Signature | Date |
Project | |||
Q.A. | |||
Engineering |
20.0 APPENDIX
20.1 LIST OF ABBREVIATIONS:
S.S.: Stainless steel
SAT: Site acceptance test
FAT: Factory acceptance test
DQ: Design Qualifications
20.2 REFERENCE DOCUMENTS:
1. Manufactures Brochure(s)/manual (s). (Title & Location).
To be supplied with the installation qualification documents
1. Calibration certificates
2. Material of construction certificates
3. Test certificates
4. As-built Drawings

Naresh Bhakar is the Founder and Author at Pharmaguddu.com, bringing his extensive expertise in the field of pharmaceuticals to readers worldwide. He has experience in Pharma manufacturing and has worked with top Pharmaceuticals. He has rich knowledge and provides valuable insights and data through his articles and content on Pharmaguddu.com. For further inquiries or collaborations, please don’t hesitate to reach out via email at [email protected].