- PURPOSE: This Master Validation Plan will give general guidelines for which modifications, additions, and reconstruction will be made in such a way that validation of the facility will be possible. In addition to satisfying building, codes upgrades will have to satisfy Environmental Room requirements.
- SCOPE: Installation Qualifications and Operation Qualification will be conducted in the Environmental Room on upgraded elements.
- REFERENCES
3.1. None - GLOSSARY
4.1. Red-Line: The process of marking additions and changes on existing documents, drawings, and schematics with a red ink pen. The modifications will also be signed and initialed. Printed names, initials, signatures, and dates must be documented.
4.2. Tagging: The identification process where a physical item(s) is/are marked in such a way that a layperson can identify that item and track it to related documents.
4.3. Pests: Invading biological entity.
4.4. Short Circuit: Producing a power draw where the current needed exceeds the rating of the circuit, resulting in a blown fuse.
4.5. Dead Air pocket: An area where air remains stagnant.
4.6. Activity A situation where people and/or machines are moving within a room. - UPGRADE ELEMENTS
5.1. Electrical
5.2. Plumbing
5.3. Facility
5.3.1. Ceiling
5.3.2. Walls
5.3.3. Floors
5.4. HVAC / AC / Air Handlers
5.4.1. Ducts
5.4.2. Climate Control / Air Systems Units
5.5. Miscellaneous
5.5.1. Bug mitigation and elemental control
5.5.2. Pest extermination plan
5.5.3. Control systems, audible and displayed - REQUIREMENTS
6.1. Installation Qualification
6.1.1. Documentation
6.1.1.1. Modifications to existing schematics will be red-lined on all appropriate schematics, drawings, drafts, and any related documents.
6.1.1.2. The gage of electrical wiring is identified, documented, and tagged.
6.1.1.3. Contractors providing services will provide a copy of their certification and qualifications for the tasks involved.
6.1.1.3.1. The contractors will be approved by Quality Assurance before the start of work.
6.1.1.4. A maximum power rating will be displayed either on the outlet or in any visible manner.
6.1.1.5. Fuses will be identified (with the location specified on fuse box listing) and rated properly for the circuit.
6.1.2. Facility
6.1.2.1. For All Items being installed in the Environmental Room or distally but relating to the room, the following must be provided, as appropriate:
6.1.2.1.1. MSDS (where applicable), Purchase Orders, Purchase Requisitions, Drawings, Sketches, Schematics, Parts Lists, Packing Slips, Work Description or Plans, Manuals, Item Descriptions, Invoices, and any documentation that will identify items going into the upgrade process.
6.1.2.2. Walls
6.1.2.2.1. Paint used for walls will be identified and will be of a low or non-particulate emitting type and electro-static reducing.
6.1.2.3. Ceiling
6.1.2.3.1. Ceiling tiles will be sealed so that they will be low or non-particulate emitting.
6.1.2.4. Floors
6.1.2.4.1. Floors will be sealed with an appropriate sealant so that they will be low or non-particulate emitting.
6.1.2.4.2. Seems in the floor will be sealed so that no particles can be caught.
6.1.2.4.3. The floor will be easy to sanitize.
6.1.2.4.4. Floor will be resistant to corrosives (i.e. sodium hydroxide and hydrochloric acid) and common solvents (i.e. ethanol and acetone).
6.1.2.4.5. The floor will be inert and will not react with chemicals.
6.1.2.4.6. Tacky mat stations will be installed at all entrances to the environmental room.
6.1.2.5. Miscellaneous
6.1.2.5.1. Barriers will be in place to prevent water and pests from entering the facility, including the warehouse.
6.1.2.5.2. Bug electrocuting units will be placed within 6 feet of all entrances to the environmental room facility.
6.1.2.5.2.1. At least one unit will be placed at each entrance.
6.1.2.5.2.2. The entrance to the warehouse will have at least 2 units.
6.1.2.5.3. An annual pest extermination inspection will be established.
6.1.2.5.3.1. The exterminator will be approved by Quality Assurance before the start of work.
6.1.2.5.3.2. Materials used for extermination will be identified and MSDSs provided, where applicable.
6.1.2.5.3.3. A post extermination inspection and documentation will be required.
6.1.3. HVAC / AC / Air Systems
6.1.3.1. HVAC and/or Air Handler Systems will be identified and the following information will be provided:
6.1.3.1.1. Descriptive: Model Number, Serial Numbers, Preventive Maintenance Procedures / Manuals, User’s Procedures / Manuals, Voltage requirement, Current requirement, Power rating, Phase and Frequency requirement, Drawings, and Parts lists, and services providers.
6.1.3.1.2. Services and replacement parts will be identified.
6.1.3.1.3. A preventive maintenance plan will be identified and documented.
6.1.3.1.4. All air ducts will be identified from the air handler.
6.1.3.1.5. Average, Maximum, and Minimum air changes will be documented.
6.1.3.1.6. Filter suppliers will be identified.
6.1.3.1.7. A filter maintenance schedule will be developed.
6.1.3.2. Alarm systems will be installed for monitoring of positive air pressure, set to trigger at 0.05-in. water.
6.1.3.3. There will be dampers that will not allow negative pressure to exist within the environmental room.
6.2. Operation Qualification
6.2.1. Electrical
6.2.1.1. The voltage fluctuation on any circuit is +5 / -10 % of the total at any time with the electrical circuit being fully loaded.
6.2.1.2. The current drop on any circuit is ≤ 2% of the total at any time with the electrical circuit being fully loaded.
6.2.1.3. There will be no occurrence of a short circuit, with the circuit being loaded below the maximum threshold.
6.2.1.4. There will be a short circuit, with the circuit being loaded above the maximum threshold.
6.2.1.5. All electrical conduits will be sealed.
6.2.2. Ambient Air
6.2.2.1. Positive Pressure is ≥ 0.05 in. water.
6.2.2.1.1. The negative air created at the fume hood in the Quality Assurance (QA) room will not cause the QA or manufacturing room ambient air to fall below 0.05 in. of water.
6.2.2.1.2. The positive pressure will be monitored for a minimum of 72 hours.
6.2.2.1.3. The positive pressure alarm will be activated by forcing the room air to fall below 0.05 in. of water.
6.2.2.2. Temperature Control is controllable and will be maintained at 15 – 30°C.
6.2.2.2.1. The temperature will be monitored for a minimum of 72 hours.
6.2.2.3. Air changes are as determined by the minimum load possible of all the air handlers.
6.2.2.4. Air currents will be identified and documented using smoke studies.
6.2.2.4.1. No dead air pockets will exist.
6.2.2.5. The Particulate Matter (PM) reading will not exceed 91,000 pp cf/minute (parts per cubic foot per minute) at 0.5 microns and will not exceed 700 pp cf/minute at 5.0 micron.
6.2.2.5.1. During activity, PM readings will take place at 4 random positions each time within each room at 0 (zero) hour and hour 2, two (2) times daily, for three (3) days.
6.2.2.6. The negative air pressure created at the fume hood in the Quality Assurance (QA) room will not cause the QA or manufacturing room ambient air to fall below 0.05 in. of water.
6.3. Performance Qualification
6.3.1. PQ is NOT required since no input variables are associated that could affect the outcome of the finished product.
6.4. Post Validation Monitoring
6.4.1. A plan will be developed for routine monitoring of ambient particulate matter.
6.4.1.1. The interval of monitoring will be established based on preliminary results.
6.4.2. A per biennium smoke study will be performed to verify the absence of dead air pockets.
6.4.3. Positive air pressure alarm will be tested quarterly.
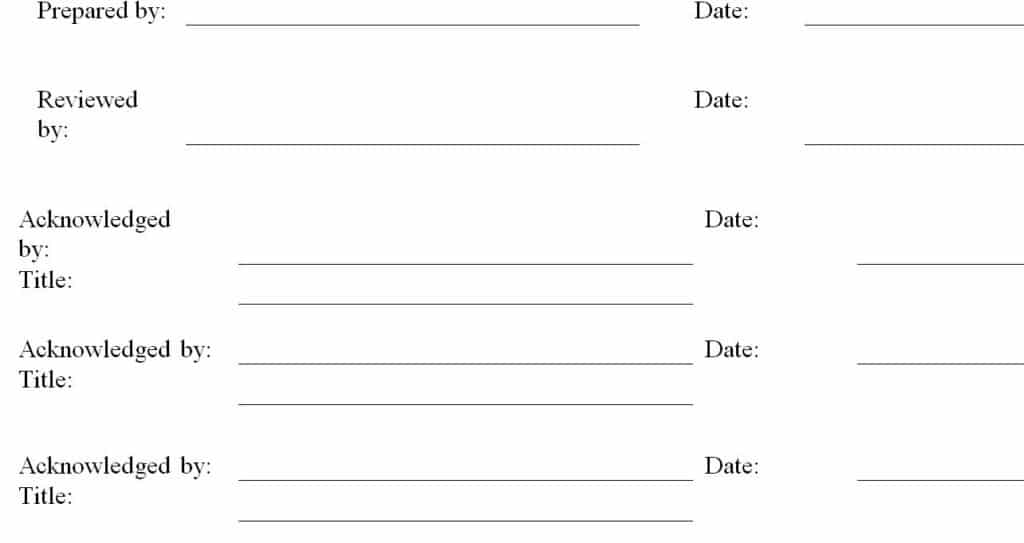

Naresh Bhakar is the Founder and Author at Pharmaguddu.com, bringing his extensive expertise in the field of pharmaceuticals to readers worldwide. He has experience in Pharma manufacturing and has worked with top Pharmaceuticals. He has rich knowledge and provides valuable insights and data through his articles and content on Pharmaguddu.com. For further inquiries or collaborations, please don’t hesitate to reach out via email at [email protected].