A Fluid bed processor is used in Pharmaceuticals for Granulation, coating on granules, drying, and palletization of granule particles. The FBE (Fluid Bed Equipment) technique introduces to improve the product quality, reduce the processing time, and reduce the cost of the manufacturing process.
A fluid bed processor is an advanced technique if talking about the past like FBD and RMG used to perform the same function which is involved the long time process, hence new technique is a very effective way to reduce the manufacturing time, workforce and cost.
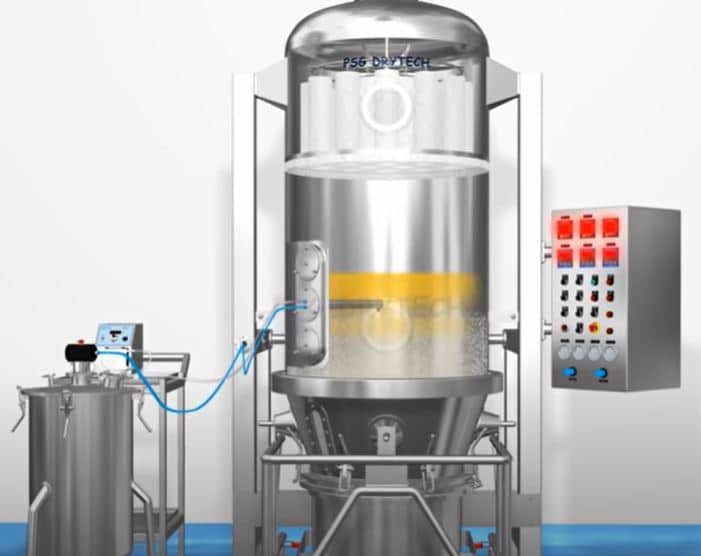
Principle of Fluid Bed Processor:
FBP involves getting the powder in a fluidized state after being pressurized with hot air and getting passed below the product bowl. Hot air continuously holds the particles in an air medium to get dry, this is also known as a fluidized state.
Components of FBP:
The granulation chamber consists of:
- Base part
- Movable product Equipment Parts like Top and Bottom spray, tangent spray)
- Expansion chamber
- filter chamber
- Exhaust Air Handling Unit Consists:
- Stainless Steel 304 Impulse Back Blow Dust Collection
- Temperature Sensor
- Differential pressure meter
- Exhaust Air Recycling
- The polyester cartridge filtration is anti-static. Blowing of the lines with compressed air or washing with water.
- Exhaust Air Recycling (option item)
- Air Handling Unit (AHU) of FBP
- The Inlet Air Handling Unit Consists:
- Pre-filter G4
- Intermediate Filter F8
- Wheel dehumidification
- Electric heating system
- Cold & Hot Air Valve
- Final Filter H13
- Temperature& Humidity Sensor
Working of Fluid Bed Processor:
A hot filtered Air is passed through the Bowl to get dry. the granule particle suspends in the air after being lifted from the bottom side of the bowl with the help of an air stream. at the same time coating solution spray is done on granules to coating them with the help of top, bottom, and tangential spray provided with the chamber unit.
Application/ Use:
- A fluid bed Processor is used to enhance product quality.
- it can be used to make sustainable release coating and enteric coating drugs.
- reduced the cost of manufacturing, and manpower and also reduced time.
- the product from atmospheric degradation.
Important FAQ:
180 mesh
bottom spray, Top spray, and tangential spray.

Naresh Bhakar is the Founder and Author at Pharmaguddu.com, bringing his extensive expertise in the field of pharmaceuticals to readers worldwide. He has experience in Pharma manufacturing and has worked with top Pharmaceuticals. He has rich knowledge and provides valuable insights and data through his articles and content on Pharmaguddu.com. For further inquiries or collaborations, please don’t hesitate to reach out via email at [email protected].
Good 👍 information