A Non-Conformance Report is issued when anything deviates from the standard required parameters for a product or components during the inspection periods by the Quality department. On deviating from the process parameters, a Quality person issued a document known as a Non-Conformance Report.
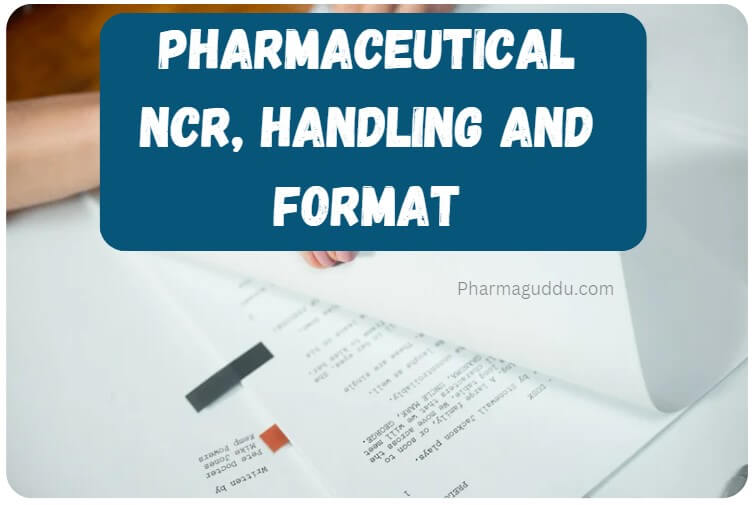
NCR Definition:
A Non-Conformance Report is a document that is used to report any non-conformity on inspection of any process and product.
Non-Conformance Report Process follows:
On issuance of the NC Report, the observation point is to be included along with justification, immediate action, and CAPA from the concerned department, and finally, it has been submitted to the Quality Person and Head of quality for review.
NCR Contents:
Non-Conformance Report Includes a header, Body, and Footer section. Let us understand one by one.
Header: The header section includes NCR No., Date, Department, Product/Equipment/Instrument, stage, and Batch/Equipment/ Instrument No.
Body Section: 1. Categories of Non-Conformance: Critical, Major, Minor along with tick mark box.
2. Observation: The QA person shall write a brief report on finding observation (See Example below).
3. Justification: The concerned department shall write a justification based on the observation in NCR.
4. Immediate Action: The concerned department shall write about what immediate action was taken to prevent damage.
5. Corrective action: By the concerned department.
6. Preventive action: By the concerned department.
7. Verification: By the QA Department.
8. Final Review: By QA Head/ Designee
Example of NCR in Pharmaceuticals:
Observation
Date: 2024-07-20
Location: Quality Control (QC) Laboratory
Description: During a routine inspection of the QC laboratory, it was observed that a batch of finished product (Batch No. XYZ123) did not meet the specified pH range. The pH value recorded was 6.8, whereas the acceptable range was 7.0 to 7.4.
Justification
Reason for NCR: The pH deviation shall impact the stability and efficacy of the product. So It is required that all product parameters shall be within the specified range.
Immediate Action
Taken by: QC Supervisor
Action Date: 2024-07-20
Details:
- The affected batch was immediately quarantined to prevent it from being released.
- A hold was placed on all subsequent batches of the same product until the issue was investigated and resolved.
Corrective Action
Taken by: Quality Assurance (QA) Team
Action Date: 2024-07-21
Details:
- An investigation was conducted to identify the root cause of the pH deviation. It was found that the incorrect buffer solution was used during the final testing phase.
- The incorrect buffer solution was replaced with the correct one, and the batch was retested. The new pH value fell within the acceptable range (7.2).
- The retrained batch was then subjected to additional stability tests to ensure there were no other deviations.
Preventive Action
Taken by: Production and QC Teams
Action Date: 2024-07-22
Details:
- Training sessions were conducted for all QC personnel to reinforce the importance of using the correct buffer solutions and to review the standard operating procedures (SOPs) for pH testing.
- Updated the SOP to include an additional verification step where a second QC analyst checks the buffer solution before use.
- Implemented a checklist for the preparation and use of buffer solutions to ensure compliance with SOPs.
- Scheduled regular audits to ensure adherence to the updated SOP and corrective measures.
Related Topic: Nonconformity During Audit and its types with Examples
NCR Format:
NCR Number: | NCR-2024-001 (Example) |
Date: | 2024-07-20 |
Reported By: | QC Supervisor |
Department: | Quality Control (QC) |
Stage: | — |
Product/ Equipment no.: | — |
Batch/Equipment No.: | — |
Category of NCR: | Critical, Major, Minor |
Observation: | . . . . . |
Justification: (To be filled by concerned department personnel) | . . |
Prompt/ Immediate Action: | . . . . |
Corrective Action: (To be filled by concerned department Head/Designee) | . . . |
Preventive Action: (To be filled by concerned department Head/Designee) | . . . |
Verification: (To be filled by QA Personnel) | . |
Final Review By Head QA/ Designee: Conclusion: NCR Closed/ Not Closed | . . . |
Prepared By: | Reviewed By: | Approved By: |
Signature | ||
Date |
FAQs:
Ans: Always follow the process and standard procedure along with providing instructions to the workers. Keep the documents and process parallel to the product to avoid loss.
Ans: An NCR is investigated by determining the root cause of the non-conformance, which includes analyzing processes, materials, and procedures to understand why the deviation happened.
Ans: NCRs are documented in a formal report that includes all relevant details and actions performed (As described above). They are monitored with a unique NCR number and examined on a regular basis to ensure that corrective and preventive actions are effective.

Naresh Bhakar is the Founder and Author at Pharmaguddu.com, bringing his extensive expertise in the field of pharmaceuticals to readers worldwide. He has experience in Pharma manufacturing and has worked with top Pharmaceuticals. He has rich knowledge and provides valuable insights and data through his articles and content on Pharmaguddu.com. For further inquiries or collaborations, please don’t hesitate to reach out via email at [email protected].