In pharmaceutical industries AHU and HVAC play an essential role in controlling microorganism-free environments by supplying fresh air. The quality of pharmaceutical products is dependent on hygiene within the industry. Preventing the spread of microorganisms through the air is highly significant. Whether it’s during laboratory development or manufacturing activities, maintaining a clean and suitable room atmosphere is essential in the pharmaceutical sector. Therefore, air-handling systems are installed for restricting or preventing airborne microorganisms.
AHU Construction and Components:
It consists of a rectangular box containing the following parts:
- Mixing box
- Prefilter
- Cooling coil
- Blower (to generate pressurized air)
- Fine filter
- Plenum HEPA (An enclosed, typically positive pressure section of an air supply system)
- RH control
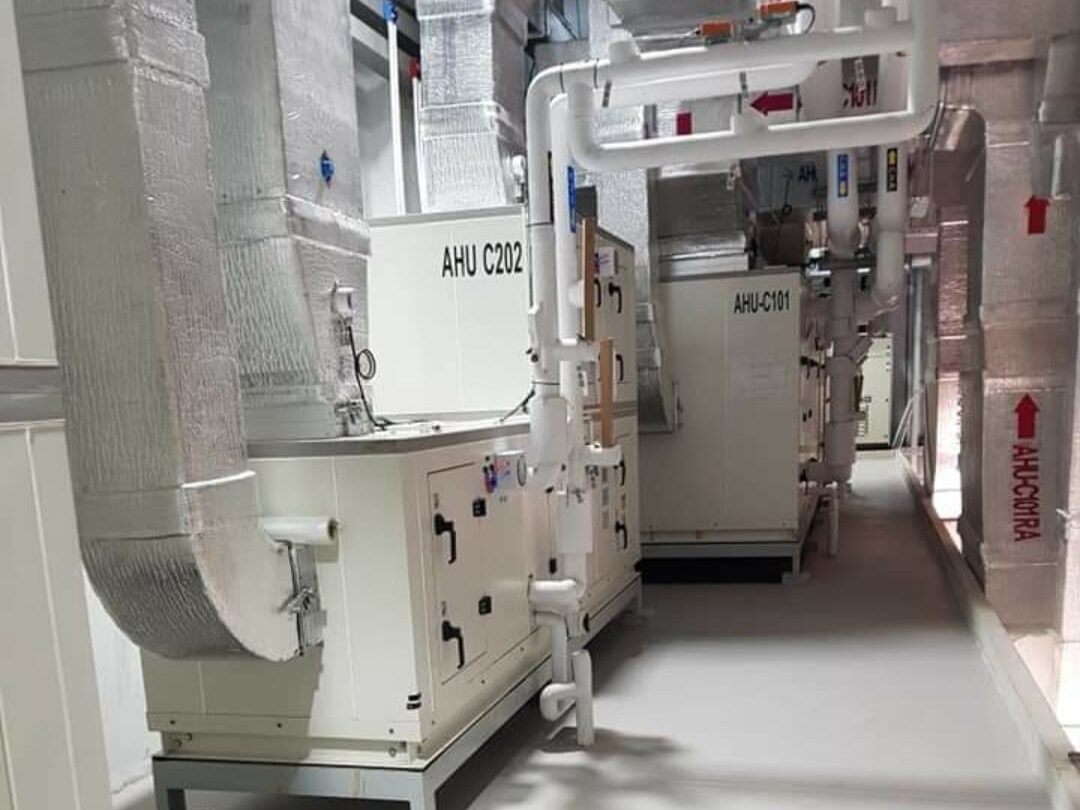
Related Topic: AHU Good Practices
HVAC System:
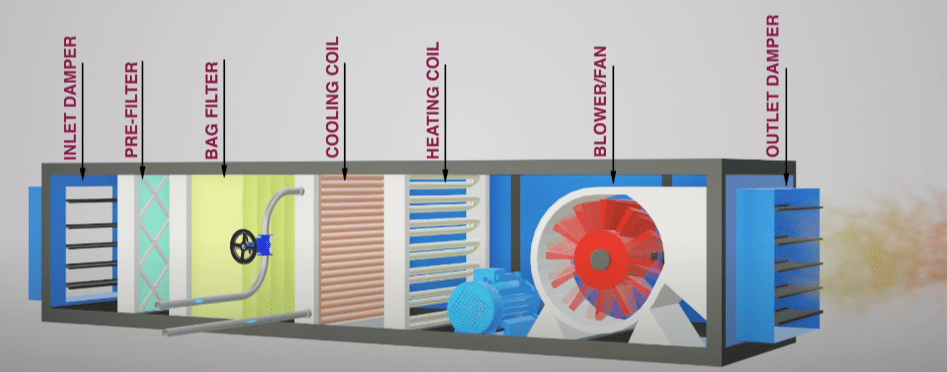
The complete set of AHU units includes air carriers (ducts), air distribution, and collection in the room (risers/grills and diffusers), a volume control system (dampers), terminal filters, along with cooling and heating coils for temperature and humidity control.
HVAC Utility:
The utility of the HVAC system in operational ranges depends on its surrounding system. This includes equipment like a DG set, boiler, chiller, air conditioning compressor, air compressor, cooling tower, vacuum, refrigerant gas, and outdoor heating.
Components of Pharmaceutical HVAC:
It consists of a rectangular box with single skin ( without insulation) and double skin (with PUF insulation of 25, 50, and 60 mm thickness or as per requirements).
Pharmaceutical AHU and HVAC— MOC:
Pharmaceutical AHU and HVAC rectangular boxes are made of GI, MS, and SS with AL, MS, and SS supporting frames.
A. Filters:
Filters are used for removing air contamination, so they help in the prevention of cross-contamination. filters types based on microns are:
1. Coarse filter:
A coarse filter made of a Mesh of 40 microns for insect and bird control.
2. Prefilters:
Prefilters are around 20, 10, and 5 microns in size. This can vary depending on the system and air quality needs. They are washable and can be cleaned. Materials such as HDPE (high-density polyethylene), nylon, and polymeric fibers are used. Construction involves using five-ply and three-ply.
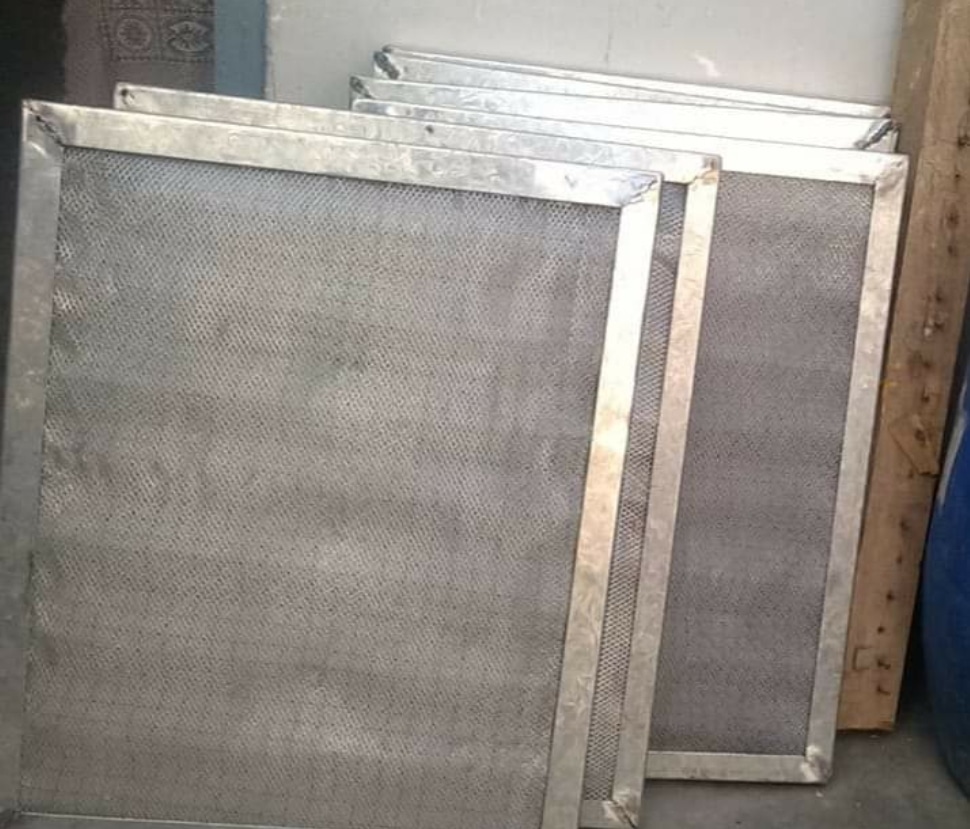
3. Intermediate filter:
The intermediate filter is approximately 5 to 3 microns in size. Sizes may vary depending on the system and required air quality. These filters are cleanable, made of non-woven material, and not washable. Materials such as HDPE (High-density polyethylene), nylon, or polymeric fibers (with a depth of fold ranging from 150 mm to 300 mm) are generally used. These filters are also known as micro V filters. If HEPA is not used following this, they are referred to as fine filters. Their dust arrestance capacity can be tested.
4. Fine filter:
Fine filters such as HEPA, ULPA, and SULPA are 0.3 microns in size. They are made of materials like glass fiber and PTFE (polytetrafluoroethylene). These filters are available in various sizes and capacities measured in CFM. Their efficiency can be tested through particle count and DOP penetration. They are non-washable and non-cleanable.
Another type of HEPA is mini pleat HEPA: In the same box, the maximum surface is provided with the pleat; hence, CFM is higher, and pressure drop is also less in the case of mini pleat (15 mmwg compared to HEPA [25 mmwg]). Mini pleat HEPA may offer about 25 to 40% more accuracy when compared to general HEPA.
B. Heating coil:
Pharmaceutical AHU and HVAC are also provided to heat the air to raise the dew point for humidity control. These are electric heaters or steam coils based on heating requirements and Air volume, two-row deep and four-row deep. The coil shall be fitted in AHU.
C. Blower:
- DIDW (Double inlets Double width): This air section is from the horizontal side and air delivery is from the upper side.
- SISW (Single inlet Single width): This air section is from only one horizontal side, and air delivery is from the side.
D. Fans ( Blade type):
- BDA-backward angle( for high static above 100- 125 mmwg)
- FDA-forward angle( for low static below 100 to 125 mmwg)
- Efficiency: for this use, the performance curve between; CFM Vs. static pressure, CFM Vs. Efficiency.
E. Cooling:
Based on the room temperature requirements, we use chilled water (with 7 °C inlets) or a DX coil in the AHU. If there’s a heating coil, we provide a cooling system after the blower. If there’s no heating coil, the cooling coil is placed before the blower. We add an aluminum fin to the coil to increase the dwell time.
For cooling non-production units, we sometimes use split air conditioners. These consist of the compressor, condenser, and FCU. The FCU (fan coil unit) is placed in the room, while the compressor is located outside. The cold air from the compressor is supplied to the FCU, and the FCU distributes the cold air in the room.
F. VCD ( Volume control dumper):
VCDs are helpful for balancing pressure. The construction materials are aluminum and GI. The capacity is measured in CFM
G. Gasket and RTV:
The gasket is a rubber gasket used between the joints of the duct and VCD to avoid air leakage.
RTV is a sealant (Room temperature vulcanized) used to seal the joints in the air path of the duct.
H. Duct:
The duct (rectangular or round-shaped) is used for the carriage of air. The material of construction (MOC) can be GI or SS (22, 24, 26, and 22 gauges are thick, and 26 gauge is a thin sheet). Generally, Smackna is used as the standard size based on the volume and velocity of air to be carried by the duct.
Sq.ft area of duct= CFM of air/ FPM of air in the duct.
I. Insulation of Pharmaceutical AHU and HVAC:
To avoid temperature drop, Ducts are insulated by suitable insulation material. Types of insulation are as follows;
- SCP ( Send cement plaster): EPS( Extruded polystyrene or thermocouple) of 25 mm, 50 mm thickness is pasted on the duct with the help of melted tar. Then affix a fine mesh before applying a final layer of sand cement plaster.
- Aluminum: Aluminum is used instead of mesh and SCP, aluminum tin cladding 10-micron thick aluminum foil is covered on the EPS insulated duct.
- Nitrile rubber: Attach nitrile rubber foam, either with or without an outer aluminum foil coating, to the duct surface using a chemical-based rubber adhesive.
J. Distribution System:
Distribution System are parts through which air through the duct is distributed in the room. The Air distribution system comprises:
- Terminal HEPA with filter screen: The HEPA box is fitted at the terminal side in the ceiling with a cover plate screen, through which air is supplied in the room.
- Diffusers: These are square-shaped, partitioned units with or without a volume control facility. MOC is GI powder-coated, aluminum, stainless steel grade 304. Capacity is calculated in CFM.
- Grills: Grills a rectangular, GI, MS, or SS-made frames with or without an air guide or volume control facility.Capacity in CFM.
K. Return air Risers:
Return air raisers are small boxes with filters and mesh covers. These boxes are installed in the wall at the bottom of the room to gather air from the room. They are connected to the return air duct.
MOC is aluminum, stainless steel, and GI powder coated. Capacity in CFM.
Monitoring equipment used are:
- Thermometer: to monitor the temperature.
- Hygrometer: to monitor RH.
- Pressure Gauge: (Magnehelic gauge)- to indicate room pressure and filter pressure drop.
- Inclined Manometer: A manometer filled with red ink is installed. Now it is not recommended.

Naresh Bhakar is the Founder and Author at Pharmaguddu.com, bringing his extensive expertise in the field of pharmaceuticals to readers worldwide. He has experience in Pharma manufacturing and has worked with top Pharmaceuticals. He has rich knowledge and provides valuable insights and data through his articles and content on Pharmaguddu.com. For further inquiries or collaborations, please don’t hesitate to reach out via email at [email protected].
informative Article, Thank you for providing depth knowledge.
Very imported information,
Thank you for providing depth knowledge
VERY INFORMATIVE ARTICLE