The sieving technique is used widely to separate fine powder from coarse powder by utilizing sieves of specific sizes. By passing the powdered material through a sieve, we can determine the level of separation. Sieves are numbered for easy distinction between them.
Working & Construction
Size separation of powder occurs as the powdered material passes through a series of sieves. These sieves are arranged in descending order, with the larger ones positioned at the top and the smallest at the bottom. The receiving opening port is attached to the bottom sieve. Initially, the material is loaded onto the upper sieve. Mechanical sieve shakers or electromagnetic devices are employed to agitate the sieves, facilitating the passage of particles through them. In Pharmaceuticals Sives are made of stainless steel, (Grade SS 316). Choosing a welding type is also important in pharmaceuticals because it can lead to contamination and the chances of adding traces in materials becomes high. So to avoid this Argon welding is preferred to attach joints in sieves.
In the pharmaceutical industry, generally, one sieve is used at a time to separate coarse powder. Sieves are selected based on their numbers to obtain the desired powder size.
What is Sieve Number?
The sieve Number/mesh size denotes the number of holes present per linear inch inside a sieve. for example, A sieve is called 12 Number, if 12 holes/ meshes are present per linear inch.
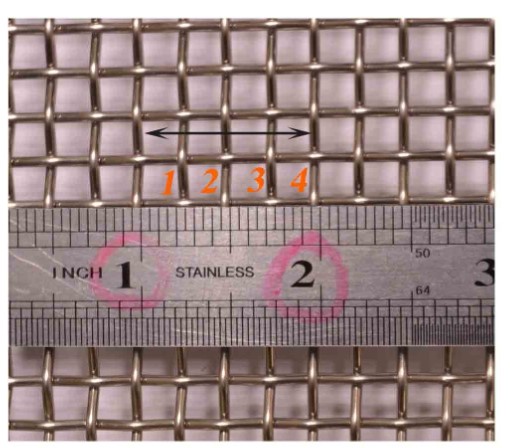
Learn: How to check Sieve mesh size?
Types of Sieving:
In Pharmaceuticals Generally, two types of sieve are used:
1. Safety Screening: These types of sieves are used to remove the contamination, or any foreign particle present in the powder, contamination may be from the worker wearing PPE equipment. It overall helps to get good quality products.
2. Grading: Grading is the system used to separate the powder as per its required size. These are used to separate only oversized and undersized powder particles.
Other Sieve commonly used in pharmaceutical, and other industries based on their MOC and processing are:
- Woven wire Sieves
- Bolting cloth Sieves
- Bar Screen
- Punched plates
1. Woven Wire Sieves: These are general purpose sieves and are widely used in pharmaceutical industries. It is of two types i) Plain weave and ii) Twilled weave.
2. Bolting cloth Sieves: These are made of silk, Nylon, and cotton cloth. Nylon cloths generally have micrometer openings used for the separation of fine powders.
3. Bar Screen: It is used in handling large and heavy materials. These bars are fixed in parallel positions and held by crossbars and spacers.
4. Punched Plates: These types of sieves is used for Coarse sizing, Screens are prepared by using sheet metal of various thickness with perforated holes. The hole may be round, oval, square, or rectangular.
Different Sieving Techniques/ Sieving Mechanism
Manual: Manual method is employed by using hands to get desired powder size.
Ultrasonic Deblinding System: While a standard sieve can quickly and accurately screen most powders, certain pharmaceutical powders may pose challenges due to stickiness or irregular-shaped particles. Such issues can lead to mesh-blinding problems. To solve this ultrasonic vibration of the stainless steel mesh wires in a powder screening machine is used. High-frequency, low-amplitude vibrations effectively remove the risk of apertures getting blocked.
As this technique helps to reduce the surface tension, Rendering the stainless steel wires friction-free. As a result, particles, whether slightly larger or smaller than the mesh, are prevented from causing blinding or obstruction.
Standards used for Sieve:
In Pharmaceuticals mainly two standards are used for example:
- U.S Standard
- Tyler Standard
U.S standard: it is based on the opening of 1mm. It means, Sieve mesh is called 20 mesh if per 1mm area total count hole present is 20.
In Indian Pharmaceuticals Tyler standard is used. Tyler standard is the ratio of width opening in a successive sieve is √2. The Tyler standard is based on the size of the opening in wire cloth having 80 openings per linear inch is called 80 mesh size.
Conversion Table from Mesh to Micron:
The conversion table for Mesh to Micron, inch is as Follows:
Mesh Size | Approximate Opening Size (inches) | Opening Size (microns) |
3 | 0.265 | 6730 |
4 | 0.187 | 4760 |
5 | 0.157 | 4000 |
6 | 0.132 | 3360 |
7 | 0.111 | 2830 |
8 | 0.0937 | 2380 |
10 | 0.0787 | 2000 |
12 | 0.0661 | 1680 |
14 | 0.0555 | 1410 |
16 | 0.0469 | 1190 |
18 | 0.0394 | 1000 |
20 | 0.0331 | 841 |
25 | 0.0278 | 707 |
30 | 0.0234 | 595 |
35 | 0.0197 | 500 |
40 | 0.0165 | 400 |
45 | 0.0138 | 354 |
50 | 0.0117 | 297 |
60 | 0.0098 | 250 |
70 | 0.0083 | 210 |
80 | 0.007 | 177 |
100 | 0.0059 | 149 |
120 | 0.0049 | 125 |
140 | 0.0041 | 105 |
170 | 0.0035 | 88 |
200 | 0.0029 | 74 |
230 | 0.0024 | 63 |
270 | 0.0021 | 53 |
325 | 0.0017 | 44 |
400 | 0.0015 | 37 |
Conversion Table for Mesh to opening in mm:
Mesh size | Opening size in (mm) |
3 | 6.730 |
4 | 4.750 |
5 | 4.000 |
6 | 3.350 |
7 | 2.830 |
8 | 2.360 |
10 | 2.000 |
12 | 1.700 |
14 | 1.400 |
16 | 1.180 |
18 | 1.000 |
20 | 0.850 |
25 | 0.710 |
30 | 0.600 |
35 | 0.500 |
40 | 0.425 |
45 | 0.355 |
50 | 0.300 |
60 | 0.250 |
70 | 0.212 |
80 | 0.180 |
100 | 0.150 |
120 | 0.125 |
140 | 0.106 |
170 | 0.090 |
200 | 0.075 |
230 | 0.063 |
270 | 0.053 |
325 | 0.045 |
400 | 0.038 |
Troubleshooting in Sieving Process:
In the granulation section of the pharmaceutical industry, During the sieving process Sometimes, powders create a static charge, probably while in vibration mode. This static charge can be dangerous because it can cause the powder to burn. The burning of the powder can be a serious problem as it can lead to fires or explosions. Therefore, it is important to take precautions and control static charge during the sieving process to ensure safety in the pharmaceutical industry.
Advantages:
- Cost-effective
- User-friendly
Disadvantages:
- Possibility of sieve clogging if the powder is inadequately dried
- Attrition may occur during the shaking process.
FAQs on Sieving
Sieving is the process of getting desired size powder by using a sieve.
Sieving is widely used in different industries such as pharmaceuticals, food production, construction, mining, and minerals.
Sieving is important in the pharmaceutical industry for quality control purposes. It helps ensure the uniformity of drug substances, checks for impurities, and contamination to ensures proper particle size distribution.

Naresh Bhakar is the Founder and Author at Pharmaguddu.com, bringing his extensive expertise in the field of pharmaceuticals to readers worldwide. He has experience in Pharma manufacturing and has worked with top Pharmaceuticals. He has rich knowledge and provides valuable insights and data through his articles and content on Pharmaguddu.com. For further inquiries or collaborations, please don’t hesitate to reach out via email at [email protected].