1.0 Purpose: To lay down the procedure to carry out the Fogging at the Production and Service floors.
2.0 Aim: This Standard Operating Procedure is applicable to carry out Fogging process on the Production Floor and the service floor of pharmaceuticals.
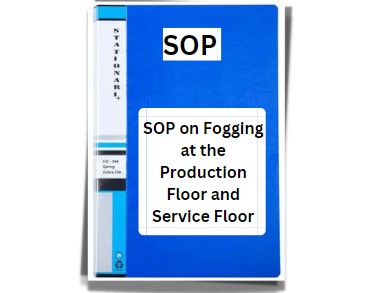
3.0 Responsibility:
3.1 Trained Line coordinators shall be responsible for carrying out the processes.
3.2 Sr. officer/officer shall be responsible for supervising the procedure.
3.3 Production manager shall be responsible for the implementation of SOP.
3.4 Head of Quality Assurance shall be responsible for ensuring compliance with the SOP.
4.0 Safety Considerations:
4.1 Ensure that all Raw materials, Intermediate products & Primary Packaging Materials in the fogging area are correctly closed.
4.2 Personnel must leave the area under Fogg as soon as possible after fogging.
4.3 Persons coming in contact with the disinfectant solution must thoroughly wash their hands and face with soap and water.
4.4 Wear safety equipment (goggles, gloves, and masks) while handling the disinfectants.
5.0 Types of equipment:
5.1 Fogger
5.2 Fogger
6.0 Materials and reagents:
6.1 Fogger
6.2 Fogging agent
7.0 Procedure:
7.1 Before Fogging, the area shall be cleaned as per “Cleaning and sanitization of area. “
7.2 Prepare the solution for fogging in the disinfectant preparation area as per SOP.
7.3 Filter the solution as per requirement and pour it into the fogger as per the required quantity.
7.4 Mop the fogger with 70 %IPA before transferring it to the core area.
7.5 Now, transfer the fogger into the area that is under Fogging.
7.6 Elevate the spraying mouth of the fogger at a 45° angle.
7.7 Switch on the fogger machine and leave the fogger for a few minutes (Approximately 5 minutes) based on the area volume.
7.8 Adjust the knob to set the concentration of disinfectant spray for fogging based on area volume.
7.9 Repeat the process in rooms starting from the inside to the exit and closing the door after completing the process.
7.10 After completion of fogging, keep the area closed for at least 15 minutes.
7.11 Record the details in the core area cleaning logbook.
8.0 Distribution:
Master Copy – Quality Assurance Department
Controlled Copy – Production Department
Subsequent controlled copies – Department (s) making the requisition
Related Post: Fumigation And Fogging In Pharmaceutical
9.0 Abbreviations:
SOP: Standard Operating Procedure
QA: Quality Assurance
PR: Production
IPA: Iso Propyl Alcohol
Eqp: Equipment
No. : Number

Naresh Bhakar is the Founder and Author at Pharmaguddu.com, bringing his extensive expertise in the field of pharmaceuticals to readers worldwide. He has experience in Pharma manufacturing and has worked with top Pharmaceuticals. He has rich knowledge and provides valuable insights and data through his articles and content on Pharmaguddu.com. For further inquiries or collaborations, please don’t hesitate to reach out via email at [email protected].