1.0 Objective: To lay down a procedure for indent, inspection, and maintenance of punches and dies.
2.0 Scope: This procedure is applicable to indent, inspection, and maintenance of punches and dies used in the production department.
3.0 Responsibility:
Operator, Officer, Executive – Production Department
Manager – Production Department
4.0 Procedure:
4.1 Indent of dies and punches:
4.1.1 For ordering a new set, raise a requisition to Purchase Department with the required specifications in the purchase indent book in duplicate.
4.1.2 Get the indent approved by the head of the unit and forward it to the purchasing department at the head office.
4.1.3 On receipt of the proper drawing from the supplier, the same is to be approved by QA Manager and the Production Manager.
4.1.4 Send the approved drawing to the supplier for manufacturing.
4.2 Inspection and maintenance of punches & dies:
4.2.1 On receipt of intimation from stores, collect the punch set from the packing material dedusting area.
4.2.2 Verify the quantity received against the Purchase Order.
4.2.3 Each punch and die shall be cleaned using a dry duster to remove any adhered grease, followed by a duster dipped in 70 % IPA (70 ml IPA + 30 ml water).
4.2.4 Each lower punch, upper punch, and die shall be checked for various parameters with a standard gauge.
4.2.5 After the complete inspection assign the set identification number and enter the same in the punch and die inventory record as per Annexure-I.
Each set will be having separate identification code abbreviated product name followed by the year of manufacturing and serial no.
For Example:-
i) PRCM 100/701
Where PRCM 100 is the abbreviation of the Paracetamol 100 product name, ‘7’ is the year of Manufacturing, and 01 is serial no.
ii) AMV 5/601
Where DOP 5 is an abbreviation of Domperidone 5, ‘6’ is the year of manufacturing, and 01 is serial no.
4.2.6 Apply a thin layer of food-grade lubricant on the surface of punches and dies. Place individual punches in the plastic cover.
4.2.7 Engrave the number of punches set with the identification number and the quantity.
4.2.8 Transfer the punch sets from the original container into a suitable Stainless steel cabinet or plastic container and label them with the product name, Identification No., punch dimension, shape, and quantity.
4.2.9 In case of rejection of dies or punches, inform the purchasing department and return the punches to stores for further action.
4.2.10 In case of product changeover (type-B cleaning), clean the punches with 70 % IPA (70 ml IPA + 30 ml water).
4.2.11 Ensure that the punches are cleaned.
4.2.12 Apply a thin layer of food-grade lubricant on the surface of punches & dies.
4.2.13 NOTE: Verify the quantity of each individual punch set and record the same in Annexure-I when the punches are received.
Related SOP: Inventory and Storage of Sieves, Screens
5.0 ABBREVIATION(S):
QA: Quality Assurance
SOP: Standard Operation Procedure
ml: Milliliter
IPA: Iso Propyl Alcohol
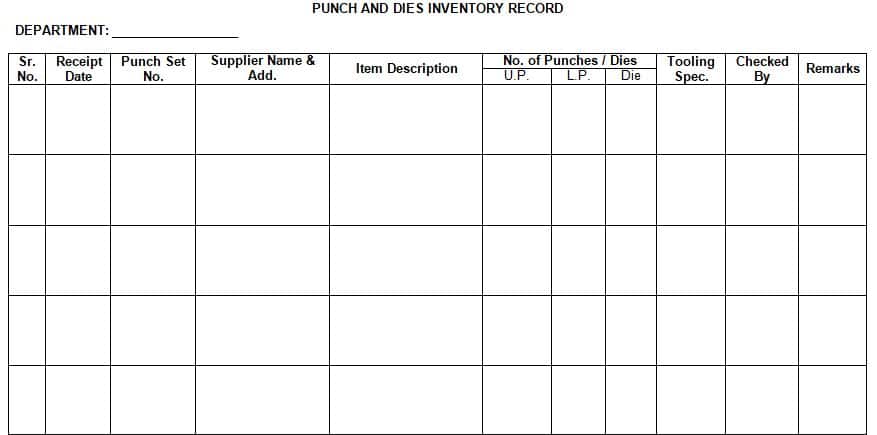

Naresh Bhakar is the Founder and Author at Pharmaguddu.com, bringing his extensive expertise in the field of pharmaceuticals to readers worldwide. He has experience in Pharma manufacturing and has worked with top Pharmaceuticals. He has rich knowledge and provides valuable insights and data through his articles and content on Pharmaguddu.com. For further inquiries or collaborations, please don’t hesitate to reach out via email at [email protected].