1.0 Objective: To lay down a procedure for Inventory and storage of sieves, screens.
2.0 Scope: This procedure is applicable to Inventory management and storage of sieves, screens.
3.0 Responsibility: Operator, Officer, Executive – Production Department
Manager – Production Department
4.0 Procedure:
4.1 Inventory
4.1.1 On intimation of receipt from stores, collect all the sieves/screens from the packing material de-dusting area.
4.1.2 Check the integrity of individual sieves/screens and record the observations in annexure-I.
4.1.3 Remark ‘OK’ for pass sieves/screens and ‘Not OK’ for sieves/screens which fail the integrity test. Return backs the defective sieves/screens to stores.
4.1.4 Allot code no. as per Coding SOP to the pass sieves/screens and transfer the respective storage area.
4.1.5 Record the observations in annexure-I.
4.1.6 Clean the sieves/screens as per cleaning SOP.
4.2 Storage
4.2.1 Cover the clean and dry sieve/screen in a virgin polybag.
4.2.2 Ensure that the trolley is clean and dry before use.
4.2.3 Keep the covered sieves on the backside gap of the rectangular trolley.
4.2.4 Keep covered screens can be kept in the rack.
4.2.5 After completion of activity clean and place sieve/screen in virgin polybag, label, and store as per procedure mentioned in step no. 4.2.1 to 4.2.4.
5.0 Abbreviation(S):
SOP: Standard operating procedure
Annexure-1
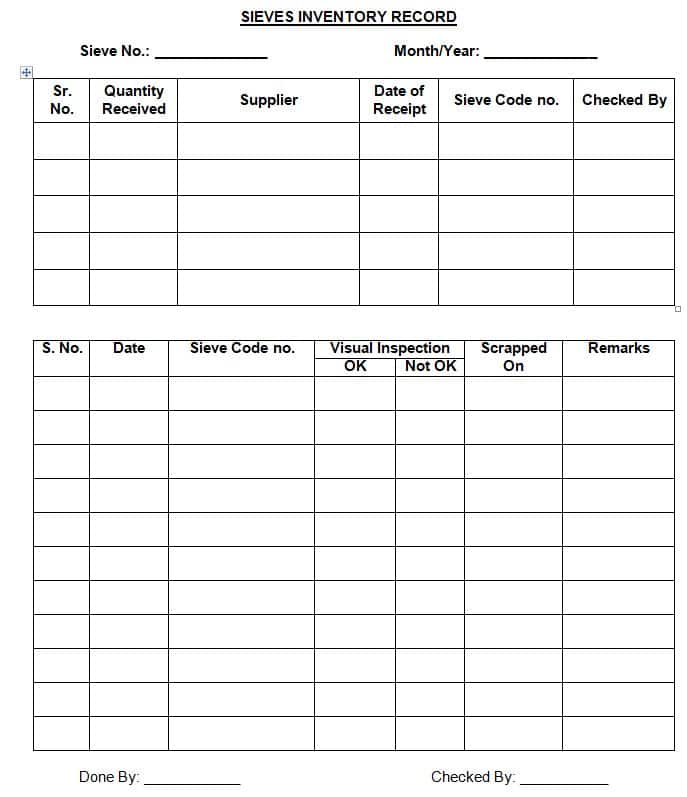

Naresh Bhakar is the Founder and Author at Pharmaguddu.com, bringing his extensive expertise in the field of pharmaceuticals to readers worldwide. He has experience in Pharma manufacturing and has worked with top Pharmaceuticals. He has rich knowledge and provides valuable insights and data through his articles and content on Pharmaguddu.com. For further inquiries or collaborations, please don’t hesitate to reach out via email at [email protected].