1.0 Objective: To lay down a procedure for the operation of the strip pack machine.
2.0 Scope: This standard operating procedure is applicable to the operation of the strip pack machine used in the production department.
3.0 Responsibility: Officer and Executive – for implementation of this procedure.
Manager Production is responsible for overall compliance with this procedure.
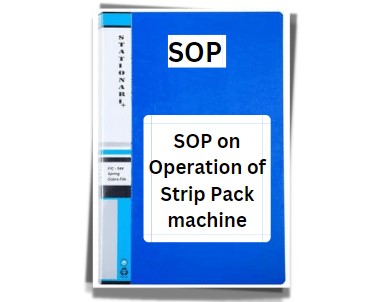
4.0 Procedure:
4.1 Machine Setting:
Ensure that the main switch is in the “OFF “position.
4.1.1 Mounting of sealing roller:
4.1.1.1 Mount the sealing roller on the shaft, then tighten the grub screw.
4.1.1.2 Ensure that the centerline of the rollers is exactly above the centerline of a draw of brushes.
4.1.1.3 Regulate the right sealing roller by means of studs and nuts to align the parallel position of the right sealing roller.
4.1.2 Adjustment of sealing pressure:
4.1.2.1 Check the cavity alignment of the sealing rollers.
4.1.2.2 Tighten the pressure-setting stud for the sealing pressure until the passing of packing material is knurled.
4.1.2.3 Tighten the stud for equalization of pressure gradually until the packing leaves the sealing roller in a correct position all over the web.
Related: Cleaning of Strip Pack Machine
4.1.3 Adjustment of cutting device:
4.1.3.1 Ensure that both the cam for the cutting device is functioning properly.
4.1.3.2 Push the cutter assembly downward to impart scissors action to the moving blade of the cutter assembly.
4.1.3.3 Adjust the point of cutting assembly by losing the screws and turning the handwheel.
4.1.3.4 Change the cutting length by means of changing gears and adjusting the screws on the cam disc.
4.1.4 Adjustment of dropping of tablets:
4.1.4.1 Adjust the dropping of tablets by losing the socket head cap screw and adjusting the pin ring on the left-hand roller shaft.
4.1.4.2 If the dropping of a tablet is early, rotate the back gear with the pin ring in a clockwise direction slowly so that the correct achieved. If the dropping is late, do the reverse.
4.2 Operation
4.2.1 After line clearance from Q.A., put the’’ UNDER PROCESS’’ label on the machine.
4.2.2 Enter the operation time of the batch in the equipment usage log sheet as per the “making entry in equipment logbook” SOP.
4.2.3 Switch “ON “the main switch from the electrical panel.
4.2.4 Take out the strips with tablets from the machine and check for the following:
- Knurling is proper to ensure smooth pressure.
- Dropping of the tablets is in the center of the pockets to avoid pocket cutting.
- Cutting the strips to the required size in the knurling portion to avoid cut pockets.
- See the overprinting details as per the BPR. Also, check for no smudging of ink.
- Ensure leak test as mentioned in the BPR.
4.2.5 Set the temperature of the sealing heater as per BPR manually.
4.2.6 Check the temperature and the same record in BPR.
4.2.7 Enter the completion time of the batch in the equipment usage log sheet.
4.2.8 Switch “OFF” the main switch from the electrical panel.
4.2.9 Affix the “TO BE CLEANED” label on the machine at the end of the batch.
4.3 Precautions
4.3.1 Never run the machine empty.
4.3.2 Clean the rollers by means of a soft brass wire brush.
Related: SOP for Camera vision system and pinhole detector
5.0 Abbreviation:
BPR: Batch Packing Record.
Q.A.: Quality Assurance.
SOP: Standard Operating Procedure

Naresh Bhakar is the Founder and Author at Pharmaguddu.com, bringing his extensive expertise in the field of pharmaceuticals to readers worldwide. He has experience in Pharma manufacturing and has worked with top Pharmaceuticals. He has rich knowledge and provides valuable insights and data through his articles and content on Pharmaguddu.com. For further inquiries or collaborations, please don’t hesitate to reach out via email at [email protected].