1.0 Purpose: To lay down a procedure for the preparation and approval of Bill of material (BOM).
2.0 Applicable: This SOP is applicable for the preparation and approval of Bill of Material of different products manufactured at Pharmaceuticals.
3.0 Responsibility:
3.1 Designated person of Production shall be responsible for the preparation of bill of material for different products as per the approved Master Formula.
3.2 The authorized person from QA /R&D shall be responsible for the review of the BOM with respect to the approved Master Formula.
3.3 Head, Warehouse, Production, and QC shall be responsible for the approval of Bill of Material.
3.4 Head/Designee of QA shall be responsible for the final authorization and implementation of the Bill of Material.
4.0 Procedure:
4.1 Preparation of BOM (Bill of material)
Flow chart:
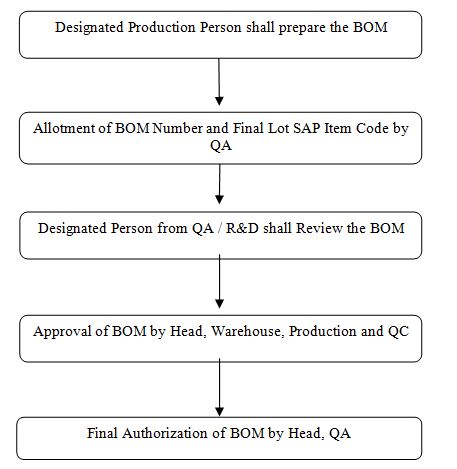
41.1 The Designated person from Production shall prepare the bill of material of all products as per the approved Master Formula or Technology Transfer Dossier documents in the format prescribed in Annexure-1.
4.1.2 The BOM shall contain the description of the Label claim of the product along with the overages (if applicable) to be added in the final formulation.
4.1.3 The BOM shall clearly specify the quantities of active raw materials, inactive raw materials, primary packing materials, and secondary packing materials to be used for the complete batch along with their unit of measurement.
4.1.4 The final quantity shall include any overages (if applicable) to be added in the formulation and the loss during the process e.g. filtration loss, evaporation loss, filling/packing rejection loss, rounding off a loss, etc.
4.1.5 Each ingredient of the product mentioned in the BOM shall be provided with the respective item codes, SAP/alternate UOM, source of ARM/RM, and the QC specification numbers.
4.2 BOM Numbering system
4.2.1 Each BOM shall be assigned a unique BOM Number which shall be product specific as follows: BOM/PC/NNN
4.2.2 Where BOM represents the ‘Bill of Material’, PC represents the product code, and ‘NNN’ represents the serial number of the BOM.
4.2.3 When there is a revision in the BOM due to its editorial or minor changes e.g. item code, specification number, etc. the revision in the existing BOM shall be made with the same BOM number and new revision number.
e.g. The first BOM number of a product Polprotec shall be as follows: BOM/06/001 with revision number “00”. After revision in the same BOM (viz. item code, specification number, etc), the new BOM Number shall be as: BOM/06/001 with revision number “01” and with the revised effective date.
4.2.4 New BOM number shall be allotted in case there is a major change in the BOM such as a change in batch size, ARM/RM source, and composition of units/dose.
4.3 Final Lot SAP Item Code Numbering System
4.3.1 The final lot item code shall be a specific number which shall remain as follows: FLPCR-NN for commercial batches and RLPCR-NN for R & D batches.
Where
‘FL’ represents the Final Lot.
RL’ represents the R & D Lot.
‘PC’ represents the product code.
‘R’ represents the presentation code, and ‘NN’ represents the version number of the final lot item code.
4.3.2 The revision in the BOM or the Final Lot SAP Item Code shall be done through the change control procedure as per the “Change control” SOP.
4.4 Review and Approval of BOM
4.4.1 The authorized person from QA/ R&D shall be responsible for reviewing of the BOM as per the approved Master Formula or Manufacturing Formula.
4.4.2 The reviewed BOM shall be forwarded to the Head Warehouse, Production, and Quality Control Departments for its approval.
4.4.3 The Head QA shall finally authorize the Bill of Material for its implementation. The master BOM shall be archived in QA, and a controlled copy shall be issued to the respective department for reference.
5.0 Annexure:
Bill of Materials
Log of Bill of Material
6.0 Distribution:
Master Copy Archived with Quality Assurance Department
Controlled Copy Production Department, Warehouse, Quality control,
Subsequent controlled copies Department (s) making the requisition
7.0 Abbreviations:
PR Production
BOM Bill of Material
SOP Standard Operating Procedure
WHO World Health Organization
QA Quality Assurance
GMP Good Manufacturing Practices.
QAR Quality Assurance Record.
QC Quality Control
UOM Unit of Measurement
ARM Active Raw Material
RM Raw Material
SAP System Application Program
R & D Research and Development
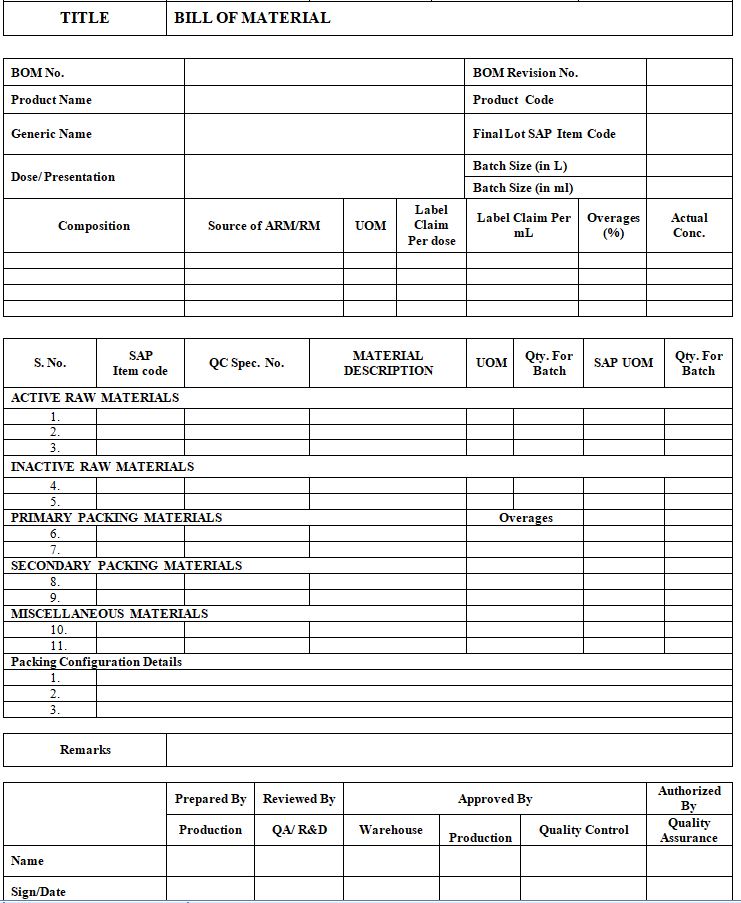
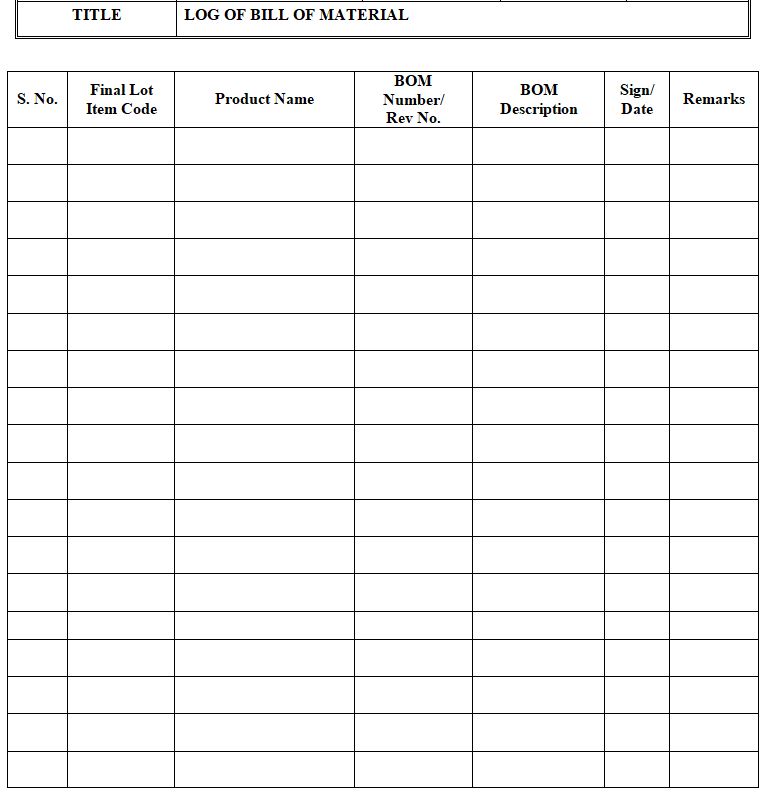

Naresh Bhakar is the Founder and Author at Pharmaguddu.com, bringing his extensive expertise in the field of pharmaceuticals to readers worldwide. He has experience in Pharma manufacturing and has worked with top Pharmaceuticals. He has rich knowledge and provides valuable insights and data through his articles and content on Pharmaguddu.com. For further inquiries or collaborations, please don’t hesitate to reach out via email at [email protected].