The Why-Why analysis is considered to be a problem-solving approach that is mainly incorporated within the pharmaceutical industry so as to get to the root of the problems. It is a basic technique in which the why is asked Frequently until the real problem is found. This applies to the why-why technique the root cause of the problem is sought instead of only solving the observable symptoms.
Why-Why Analysis Step-by-Step Process:
Identify the Problem: The first thing is to describe the problem very well. For Example, let’s say “black particles in tablets.” In the beginning, this is what you will say.
Ask ‘Why?’ After you have defined the problem well, then you pose a question which is the first “Why?” For Example “Why are there black particles in the tablets?
One of the possible answers could be that the particles were as a result of contamination during the manufacturing of tablets.
Continue Asking ‘Why?’ After you have provided the first answer, then you proceed to ask “why” once again:
A potential response could be that “there was wear and tear in the tablet compression machine”.
Repeat Until You Find the Root Cause: You keep on posing “why” for every answer you get back or any reasoning until you can establish a practical solution to the problem. In this case you might discover that the root cause of such poor repair is poor maintenance of the equipment so or that there are poor cleaning methods of the equipment.
Why-Why Analysis Procedure:
Let’s understand it with an Example of a Contaminated Product.
Problem Statement: Suppose, A product batch was found to be contaminated, leading to a recall.
So, First, let’s Focus on our 5-Why process.
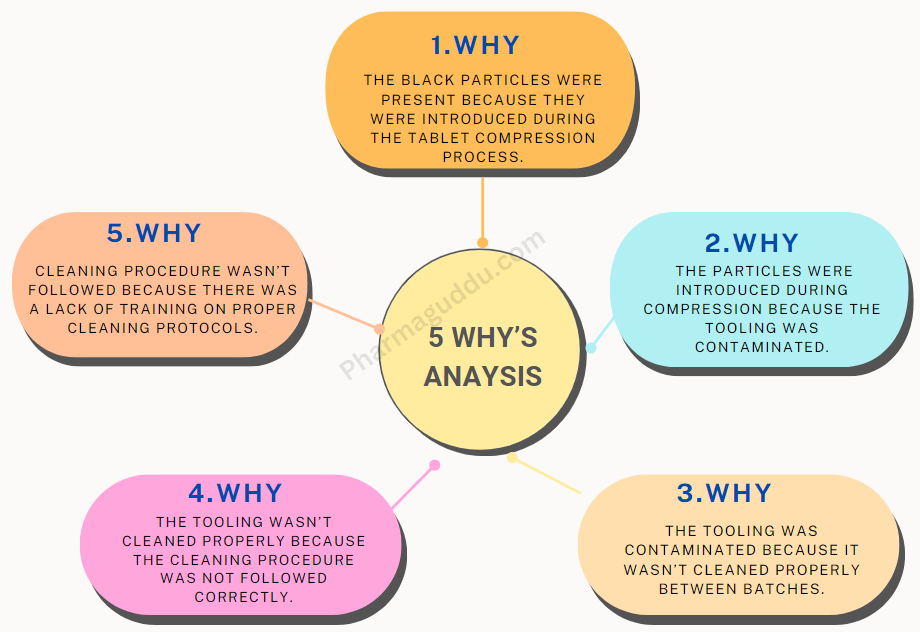
Why: The product was contaminated because foreign particles were found in a few tablets.
Why: The foreign particles were present because the mixing tank wasn’t properly cleaned.
Why: The tank was not cleaned because the cleaning procedure was not followed correctly.
Why: The cleaning procedure was not followed because the operator was unaware of the updated cleaning protocol.
Why: The operator was unaware of the updated protocol because the new guidelines were not communicated effectively.
As seen above we have found our 5-Ways answers, Now let’s move on next part.
Root Causes Analysis: Here, Our 5 Way answer is appropriate to decide the problem’s Root cause. As we saw above, contamination occurred because the updated cleaning protocol was not communicated effectively (which means, there were clear gaps in communication), leading to improper cleaning of the mixing tank.
Evidence/Data/Fact:
- Quality control reports indicate that there are foreign particles in one of the batches inside the tablets.
- The Training records indicate that the operator had not previously been trained on this revised Cleaning Protocol.
- The inspection was completed and it was found that there was leftover residue in the mixing tank that ought to have been eliminated during cleaning.
Solution Idea:
- All the operators will be trained on updated cleaning procedures.
- Enhance ways of communicating changes in procedures.
- All cleaning procedure documents should be clear, easily understood, and retrieved.
Corrective Action:
- Appropriate training sessions observing all the new cleaning procedures should be provided to all operators.
- There should be a process whereby staff members are updated on procedure changes.
- There should be regular assessment/audit of cleaning procedures to ascertain that cleaning procedures are carried out as per updated protocol.
Preventive Measures:
- A clear checklist focussing on the cleaning procedure should be written and distributed
- Perform regular internal audits for compliance with the cleaning procedure including issues arising is to be conducted.
- A review of communication processes and practices should also be done on a continuous basis if all such changes are aimed at making updated communication clearer and faster to the relevant staff members.
Why-Why Analysis: Let’s understand it with another Example: Black Particles in Tablets
Problem Statement: Black particles were found in tablets during quality control inspection.
Why: The black particles were present because they were introduced during the tablet compression process.
Why: The particles were introduced during compression because the tooling was contaminated.
Why: The tooling was contaminated because it wasn’t cleaned properly between batches.
Why: The tooling wasn’t cleaned properly because the cleaning procedure was not followed correctly.
Why: The cleaning procedure wasn’t followed because there was a lack of training on proper cleaning protocols.
Root Causes: Here, again Our 5 Way answer is appropriate to decide the problem’s Root cause. The black particles were introduced due to improper cleaning of the compression machine tooling, resulting from inadequate training on cleaning procedures.
Evidence/Data/Fact:
- Reports of the inspections state that black particles were found in the affected batch.
- On checking Cleaning logs. It indicates irregularities in the cleaning process for the compression machine tooling.
- Employee training records indicate that there are gaps in the training.
Solution Ideas:
- Create and implement an appropriate cleaning procedure for each equipment.
- A well-structured training program is required which shall focus on the importance of complying with cleaning protocols.
- Regular monitoring and evaluation of cleaning procedures should be done.
Corrective Action:
- Create and enforce a detailed cleaning protocol for all tooling and equipment.
- Conduct training sessions for all relevant staff on the importance of proper cleaning and following procedures.
- Set up regular inspections to ensure the cleaning process is adhered to, with documentation for each batch.
- Review and, if necessary, replace or repair any tooling that may contribute to contamination.
Preventive Measures:
- Maintain a detailed cleaning checklist that must be completed and signed off after each cleaning session.
- Perform regular audits to verify that cleaning protocols are being followed consistently.
- Evaluate and choose high-quality materials and equipment suppliers to reduce the risk of contamination.

Naresh Bhakar is the Founder and Author at Pharmaguddu.com, bringing his extensive expertise in the field of pharmaceuticals to readers worldwide. He has experience in Pharma manufacturing and has worked with top Pharmaceuticals. He has rich knowledge and provides valuable insights and data through his articles and content on Pharmaguddu.com. For further inquiries or collaborations, please don’t hesitate to reach out via email at [email protected].