Standard Operating Procedure for Operating and Validating a Biosafety Cabinet
1.0 Objective: The purpose of this procedure is to outline how to use and verify the functionality of a Biosafety Cabinet.
2.0 Scope: This procedure covers the usage and internal validation of a Biosafety Cabinet.
3.0 Responsibilities: Microbiologist: Responsible for using, validating, and maintaining the instrument according to the procedure. Maintain necessary records.
QA Officer/QA Manager: Review records and oversee the documentation.
4.0 Procedure:
4.1 Start by turning on the main power.
4.2 Switch on the Ultraviolet (UV) light for 30 minutes before beginning work.
4.3 Activate the HEPA filter for 15 minutes before starting work.
4.4 Ensure the UV light is off while working.
4.5 Confirm the inward airflow by holding a tissue at the middle of the edge of the viewing panel and checking if it gets pulled in.
4.6 Log the usage of the UV light in the provided UV light usage log book (Annexure-1).
4.7 Turn off the instrument once the work is completed.
4.8 Clean the interior surface of the Biosafety Cabinet with 70% Isopropyl Alcohol (IPA) before and after analysis.
5.0 Validation:
5.1 HEPA Filter Performance Check:
5.1.1 Perform the following tests by an external agency once a year:
- DOP Test.
- Particulate Count.
- Velocity Measurement.
5.2 Plate Count Method:
5.2.1 Place soya bean casein digest agar and Sabouraud chloramphenicol agar plates in the Biosafety Cabinet for 2 hours.
5.2.2 Incubate plates as follows:
- Soya bean casein digest agar at 35-37°C for 24 hours.
- Sabouraud chloramphenicol agar at 20-25°C for 72-96 hours.
- Count and record the number of colonies on the plates in the Biosafety Cabinet log book (Annexure-2).
5.3 Acceptance Criteria: The acceptable limit is not more than 1 colony-forming unit (cfu) per plate every 2 hours.
5.4 Frequency: Conduct the Plate Count Method validation once a month.
6.0 Maintenance:
6.1 Cleaning:
6.1.1 Use a dry cloth to clean the instrument and the Biosafety Cabinet bench. Clean the UV light tub with a dry cloth.
7.0 Documentation:
7.1 Records:
Annexure 1: Ultra Violet Usage Log Book.
Annexure 2: Biosafety Cabinet Validation Log Book.
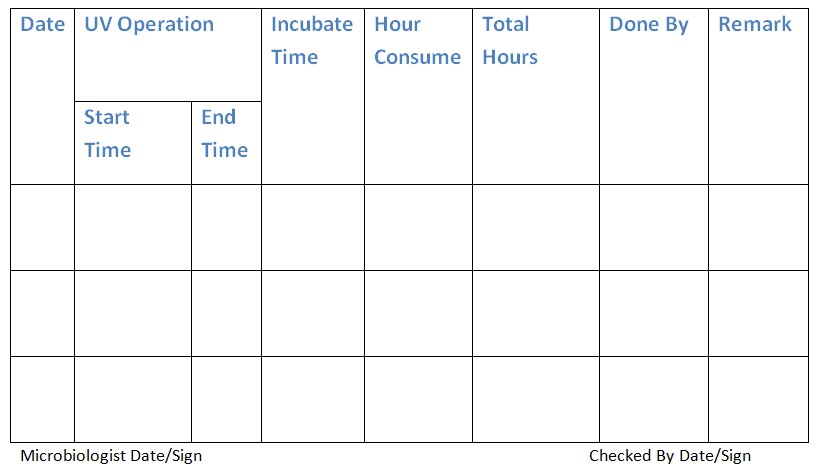
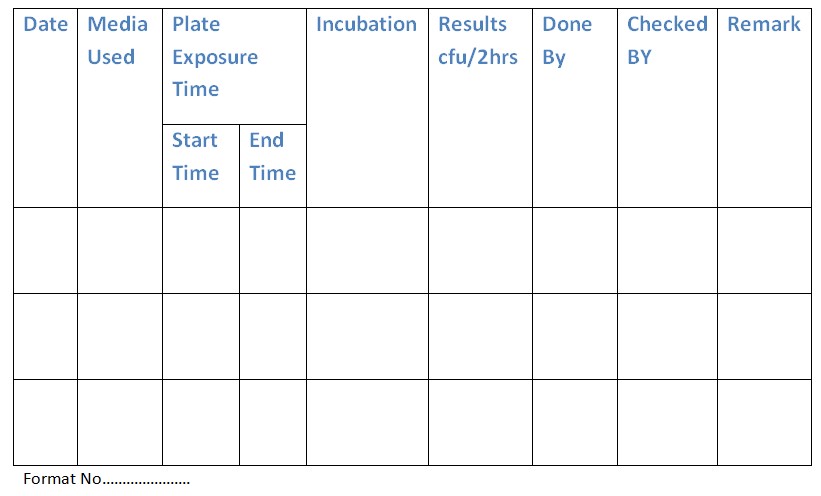