Today’s Countless tablets and pills are being produced worldwide by using different methods. Choosing an appropriate method for formulation depends on the types of materials that are going to add while making granules, For example for some heat-sensitive materials, Generally, Direct compression method is used. Below is a detailed discussion on Different types of tablets manufacturing processes, their usage, properties, advantages, and disadvantages.
Three most common Tablets manufacturing processes
- Direct compression
- Wet granulation
- Roller compaction also called dry granulation
Direct Compression
Direct compression is the easiest and most cost-efficient tablet manufacturing process. In this process, the Active Pharmaceutical Ingredient (API) and excipients, such as filler, binder, or lubricant, are mixed. The pre-mixed powder is then compressed directly using a tablet press.
The advantages of direct compression are its low production costs, fast and efficient process, and ability to work with water and heat-sensitive APIs. however, it may be difficult for low dosage due to weak content uniformity, pre-mixed powders require good flowability to ensure a perfect fill of the cavities. Good flow behavior can speed up the process by preventing different types of tablet manufacturing defects.
The powder flow properties are measured by the angle of repose. A small angle indicates good flowability if the pre-mixed powder has a higher angle of repose. In this case, granulation produces larger and rougher particles. thus dry manufacturing process is used to increase the flow properties by decreasing the particle surface and reducing the amount of dust granulation.
Wet Granulation
In wet Granulation, suitable granulating fluid like water, binder solution, or organic solvent is added along with API. Further to create a wet mass, these are granulated with a low or high-shear mixing tool known as RMG. Afterward, the wet granules are milled dried in an FBD (Fluid bed dryer), and sifted to the final particle size. Excipients such as lubricants or disintegrates are added later to mix them with dried granules by using a blender.
Pros: Wet granulation ensure good distribution of the API due to good content uniformity and are suitable for many excipients
Cons: Wet Granulation is not suitable for water or heat-sensitive API’s and is very costly due to the long Process.
Dry Granulation by Roller Compaction
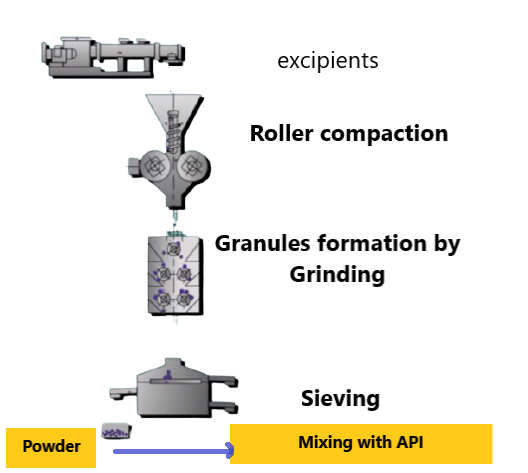
Roller compaction is another tablet manufacturing process, sometimes known as dry granulation, used to increase flowability. It has a few good features that make it unique for the tablet manufacturing process. One option is to only mix the excipient and not the API.
In roller compaction, the premix of excipient can be compressed with slugs or by roller compaction. After that, it is ground into granules without the use of fluids because the API is only added at this point. This process is perfectly suitable for sensitive APIs. Additionally, the consistency of the material ensures that the API is distributed well. However, the additional process steps in roller compaction make it quite costly.
All these three tablet manufacturing processes ultimately involve compression to produce powders or granules into tablets.
Conclusion
All three methods used in the tablet manufacturing process are safe and reliable. However, each above-described method has its advantages and disadvantages that should be considered.

Naresh Bhakar is the Founder and Author at Pharmaguddu.com, bringing his extensive expertise in the field of pharmaceuticals to readers worldwide. He has experience in Pharma manufacturing and has worked with top Pharmaceuticals. He has rich knowledge and provides valuable insights and data through his articles and content on Pharmaguddu.com. For further inquiries or collaborations, please don’t hesitate to reach out via email at [email protected].