Sometimes issues happen during the manufacturing process of tablets, and we call them tablet manufacturing defects. Below is a Detailed discussion on Tablets Manufacturing Defects and Remedies that help to encounter these situations. So to provide and maintain the quality of products, tablets should be free from such visual defects.
A pharmaceutical company that manufactures medicines may have trouble with the quality of what they produce. Most of these problems come from various reasons, and fixing them requires a good understanding of how granulation processing works.
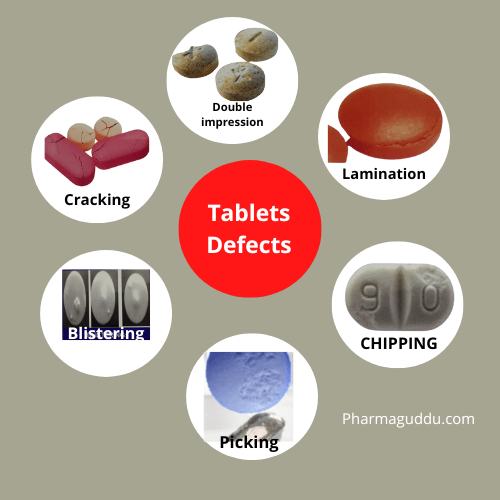
The entire article will cover the 9 types of Tablet manufacturing defects and their Solution.
Types of Tablets Manufacturing Defects and Definition
Tablet processing defects may be due to problems in the Granules or the setting of the compression Machine.
Common Defects Type | Definition |
---|---|
Capping | Capping is the partial and complete separation of the top or bottom of tablets due to air entrapment in granular materials. |
Lamination | Lamination is the separation of a tablet into two or more layers due to air-entrapment in granular material. |
Cracking | Cracking is due to the rapid expansion of tablets when deep concave punches are used. |
The Tablets Defects Related to Excipients:
Other tablet manufacturing defects and remedies due to excipients are given below:
Chipping: chipping is due to more dry granules.
Sticking: Sticking is the adherence of materials to the die wall.
Picking: Picking is removed from materials from the surface of the tablet and its adherence to the face of the punch.
Binding: problem likes sticking and picking due to more Amount of Binder in the granules or wet granules.
Compression Problems due to other factors:
Mottling: Mottling defects are due to the colored drugs, which contain a different color than the remaining granules (excipients related) or improper mixing of granular materials (process-related); dirt in granular materials or on punch face.
Tablets Defects Related to Compression Machine:
Double impression: Double impression is due to the free rotation of punches, which have some engraving on punch faces.
Types of Tablets Manufacturing Defects and Remedies
Below are the different kinds of Tablets Manufacturing Defects along with their Solution
1. CAPPING
Capping is the division of the upper and lower segments of the tablet that separates horizontally during ejection from the tablet press.
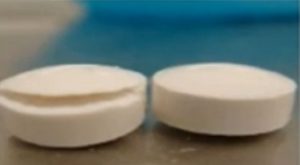
Reason: capping is because of air-entrapment during compression and subsequent expansion of the tablet on the ejection of a tablet from the die.
Causes of Capping in Tablets
- A large number of fines in granules
- Too dry and low moisture content (result is the loss of proper binding action.
- Not properly dried granules thoroughly
- Less Amount of binder or improper binder and lubricant.
Remedies of Tablet Capping
- Use 100 to 200 mesh screens to remove fines
- Moisten the granules, add hygroscopic substance, e.g., sorbitol,methyl-cellulose, or PEG-4000
- Dry granules properly
- Add more Amount binder and lubricant.
- Compress in inadequate environmental conditions.
Problems Related to Machines
- Poorly finished die.
- Deep concave punches.
- The lower punch remains below the face of the die during tablet ejection.
- Incorrect adjustment of the sweep of the blade.
- High turret speed.
Machine-related Remedies For Tablets
- Do proper polishing of the die
- Try to use flat punches
- Do the proper setting of lower punch during ejection
- Adjust proper sweep-of blade for ejection
- Decrease the speed of turret (increase dwell time)
2. LAMINATION
Lamination is the separation of Tablets into two or more parts horizontally (see below Image).
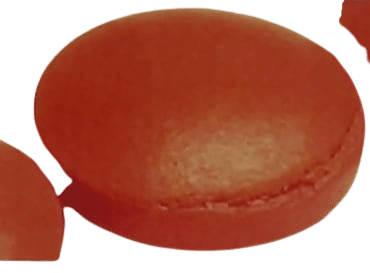
Reason for Lamination in Tablets
The Defect is due to Air-entrapment during compression and subsequent release on ejection, the condition triggered by the higher speed of the turret.
Causes of Lamination
- Oily or waxy materials in granules
- Too much hydrophobic lubricant
- Magnesium-stearate
Remedies of Lamination in tablets
- Add adsorbent or absorbent
- Less Amount of lubricant or change the type of lubricant
Causes of Lamination due to a machine:
- Rapid decompression
- During ejection, rapid relaxation of edge regions of tablets.
- Use tapered die (the upper part of the die bore has an outward taper of 3 to 5 degrees.
- Reduce compression and turret speed.
Related article: Tablets coating defects
3. CHIPPING
Chipping is mainly the breaking of tablet edges (see below Image).
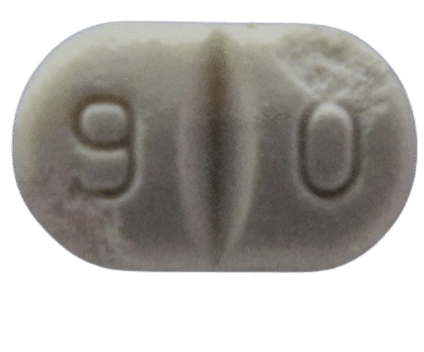
Causes of Chipping:
- Sticking on punches’ faces.
- Too dry granules.
- Too much binding causes are chipping at the bottom.
Remedies of Chipping:
- Increase lubrication.
- Dry the granules properly.
- Moisten the granules to plasticize. Add hygroscopic substances, or use a dry binder.
Chipping Problems related to compression machine:
- Barreled die(center of die wider than the end).
- It may be due to a punch face or maybe turned inside.
- The groove of the die is worn at the compression point.
Machine related Remedies
- Replace the die or polish to the open-end, and polish the die to make it cylindrical.
- Polish the punch edges.
- Use a flat punch.
4. CRACKING
Cracking is small and fine observed on the upper and lower portion of the tablet (see below Image). It is observed as a result of the rapid expansion of tablets. It causes a large size of granules.
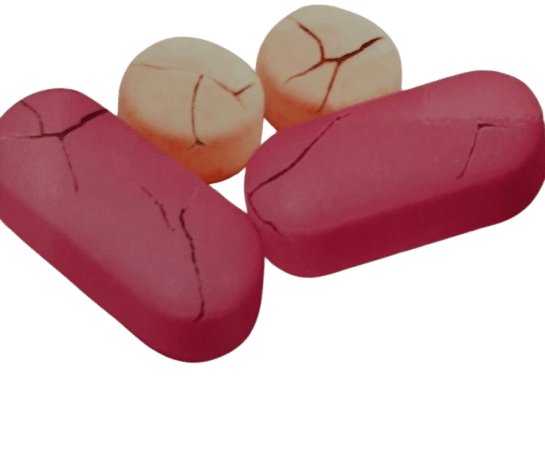
Reason for Cracking:
- Too dry granules.
- Tablets expand.
- Granulation is too cold.
Remedies for Cracking defects
- Add fines and reduce granule size.
- Moisten the granules properly and add the proper amount of binder(dry binder).
- Compress at room temperature.
Causes related to the compression machine:
- Tablets get to expand on ejection due to air entrapment.
- Deep concavities cause cracking during the removal of tablets.
Remedies related to the compression machine:
- Use tapered die.
- Use special take-off.
5. STICKING
Sticking is adhering tablet materials to the die of the wall (see below Image). It starts with filming to form excess due to more Amount of moisture in granules.
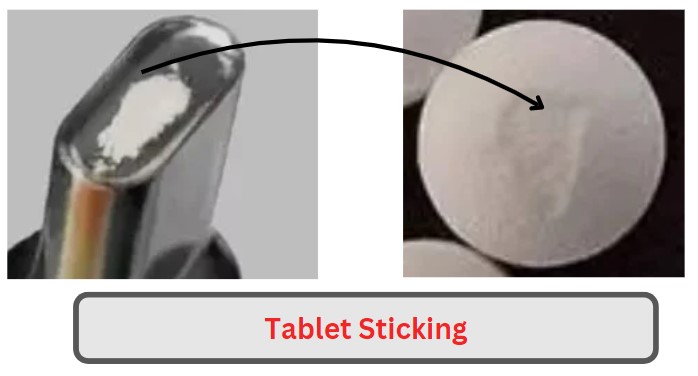
Cause of Sticking:
- Less dry granules.
- Improper lubrication.
- Too much binder.
- Hygroscopic granular materials.
- Oily or waxy materials.
- Week granules or too soft.
Remedies for Sticking in Tablets
- Dry the granules properly and do a moisture analysis to determine limits.
- Add more Amount lubricant to the formulation.
- Compress under controlled humidity.
- Modify the mixing process and add an absorbent.
- Optimize the Amount of binder and granulation technique.
Causes defects due to the machine:
- Too low pressure.
- Too fast compression.
- Concavity is too deep for granulation.
Remedies for Sticking due to compression machine
- Increase pressure.
- Reduced speed.
- Reduce concavity to the optimum.
6. PICKING
Picking is the small amount of materials removed from the tablet’s surface and sticks to the punch surface mainly more on the upper punch (see below Image).
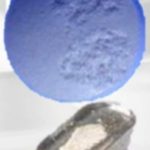
Reason for Picking in Tablets:
It comes when the punch face has engraving or embossing letters, as well as when granules are improperly dried.
Causes of Picking
- Excessive moisture in granules.
- Not well lubricated.
- The low melting substance may soften from the heat of compression and lead to picking.
- A high concentration of low melting point medicament.
- During compression, granules are not too warm.
- Too much Amount of a binder.
Remedies for Picking
- Dry granules properly and determine optimum limits
- Use colloidal silica(lubrication agent) as a polishing agent to prevent materials from adhering to punch skin.
- Use high materials-point materials.
- Keep granules at optimum temperature and compress them at room temperature.
- Reduce the Amount of binder. Use a dry binder.
Cause-related to Machine
- Rough or scratched punch faces.
- Bevels or dividing lines are too deep.
- The pressure applied is not enough; too soft tablets.
Remedies for Machine
- Polish face to a high luster.
- Design lettering as large as possible.
- Punch plating is required on the face of the punch with chromium to produce a smooth and non-adherent.
- Reduce depths and sharpness.
- Increase pressure to the optimum.
7. MOTTLING
Mottling is an unequal distribution of color on a tablet with light and dark spots on the surface of the tablet.
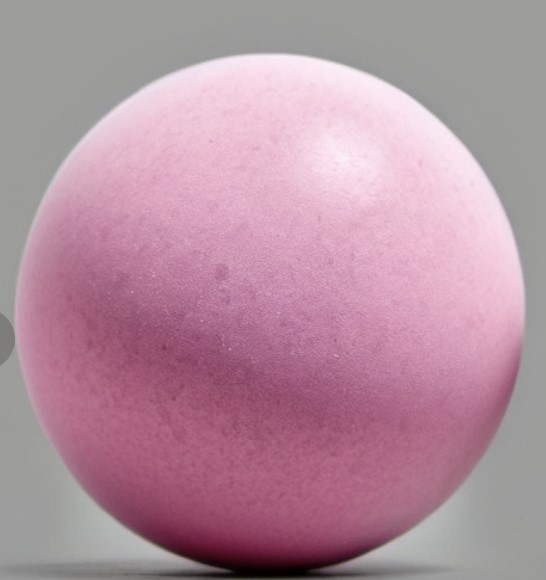
Reason: mottling defects are due to the difference in the color of drugs from the color of excipients that are used for the granulation of tablets.
Causes of Mottling in Pharmaceutical Tablets:
- A colored drug is used along with colorless or white-colored materials.
- This is due to the migration of color to the surface of granules during the drying process.
- Not proper mixing of dye, especially during direct compression.
- Improper mixing of a colored binder solution.
Remedies for Mottling
- Reduces drying temperature, and changes the binder and solvent.
- Prevent segregation by mixing properly and reducing the size if it is large.
- During the powder blending step, add dry color additives, then finally add powdered adhesives such as acacia and tragacanth.
8. DOUBLE IMPRESSION
It involves only those punches that have engraving or monograms on them (see below Image).

Reason: At the time of compression tablet receives the imprint from the punch. Sometimes punch may drop and start to rotate freely. During this punch, travels become uncontrolled for a short distance before the ejection of tablets from the cam. During free travel of punch, they rotate at these points. The punch may make a new impression.
Causes of Double impression:
- Free rotation of upper or lower punch during the ejection of tablets.
Remedies for Double Impression
- Inset a key alongside the punch to prevent free rotation.
- Never press anti-turning devices, which prevent punch rotation.
9. TABLET WEIGHT VARIATION:
Tablet weight variation is a common type of tablet manufacturing defect. The following remedies are given below:
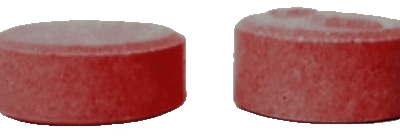
This type of problem is due to variations in power density and distribution of particle size (see above Image). Punch working length should be taken into consideration. The working length is an important factor to determine, How punches affect tablet weight. Powder flow and feed flow also affect the weight variation.
Conclusion:
Tablets manufacturing defects and remedies in Pharmaceutical are very challenging to the drug manufacturer, the overall quality of products depends on the appearance of Tablets. The quality of such products can be minimized with a given solution of tablet defects.
FAQs:
Ans: Tablet defects are changes in color, shape, size, and weight along with some other common defects that may cause a reduction in the quality of products.
Ans: Examples include Capping, Lamination, Cracking, Chipping, Sticking, Picking, Mottling, and Double Impression.
Ans: Issues like chipping and sticking may arise due to dry granules or excessive binder.
Ans: Remedies include using screens to remove fines, adding hygroscopic substances, and adjusting environmental conditions like temperature and RH.
Ans: Lamination is caused by air entrapment during compression, triggered by high turret speed.
Ans: Solutions involve proper drying of granules, adjusting lubrication, and optimizing binder and granulation techniques.
Ans: Picking is the removal of materials from tablet surfaces. Remedies include proper drying, lubrication, and adjusting machine parameters.
Ans: Mottling results from differences in the color of drugs and excipients. Remedies include adjusting drying temperature and proper mixing.
Ans: Double impression happens due to the free rotation of punches during ejection. Remedies include preventing free rotation with keys.
Ans: Tablet weight variation is due to variations in powder density and particle size distribution. Punch working length and powder flow also play a role.

Naresh Bhakar is the Founder and Author at Pharmaguddu.com, bringing his extensive expertise in the field of pharmaceuticals to readers worldwide. He has experience in Pharma manufacturing and has worked with top Pharmaceuticals. He has rich knowledge and provides valuable insights and data through his articles and content on Pharmaguddu.com. For further inquiries or collaborations, please don’t hesitate to reach out via email at [email protected].