Autoclave validation is required to get effective Sterilization to ensure good product quality and also sterility of glassware and media used for analysis is very important for product manufacturing. Ineffective autoclave validation may cause deviation in sterility and it may lead to a false result.
So data loggers play a very important role in recording the temperature at a different validation stage with the help of Probes. The number of Probes used depends on the size of the autoclave being validated.
Related Post: Bowie dick test for autoclave validation
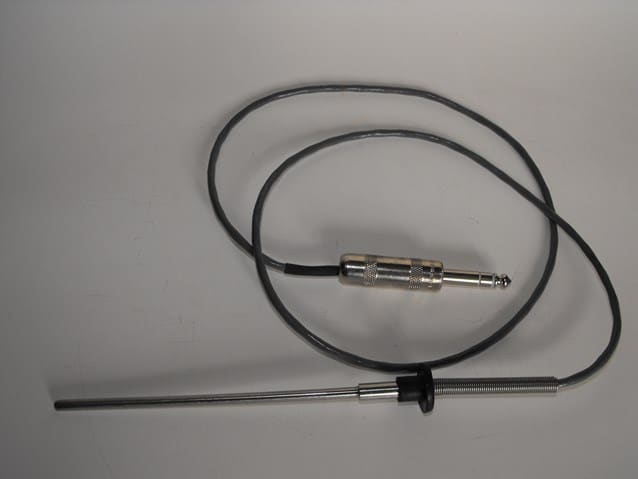
The Number of Probes used for Autoclave validation
There are lots of regulatory guidelines on autoclave validation, but among them, most don’t specify the number of probes to be used.
Biological indicators are not mandatory during the Slow to Heat study. It’s important to load only one batch at a time in an autoclave and use more than 12 temperature probes in the load to ensure proper validation.
This is because if the load items are more or, the autoclave chamber size is more than 1000 L, then we should place > than 12 probes.
This should include covering all corners, the bottom and upper central parts, as well as the mid-central part of the autoclave. The selection should be based on the load items and include representative items of a load.
Autoclave validation process
- To validate the autoclave effectively, place the temperature probes. During this, operate the Validator (Datalogger) simultaneously to apply a programmed cycle to the load. Calculate the F0 value using the formula F0 = 10^((Measured temperature – 121.1°C)/10) multiplied by the time interval of dwell time to meet all requirements.
- First, list the number of loads to be validated in the autoclave and categorize them into porous, non-porous, and mixed loads. Categorization is based on the nature of load items like rubber bung, silicon tube, cartridge filter, and HDPE bottle. Note that heat penetration is challenging in a porous load. After categorizing the loads, develop the heat penetration cycle known as the slow-to-heat cycle or hardest-to-heat cycle, or cold spot identification cycle in the load.
- Use the same cycle parameters for slow-to-heat and final runs for all non-liquid loads. Depending on the load type, items, post-pulse rate, and a number of post-pulses can vary, but the post parameter won’t impact heat penetration or Sterile Assurance Level (SAL).
- Conduct all slow-to-heat runs for different loads in the cool chamber. After the Slow-to-Heat study, validate all loads for three consecutive successful runs to demonstrate consistency, reliability, and SAL in the biological indicators at 10 cold spots.
- For the worst-case scenario in minimum load validation/Sterile Assurance Level/Variable position validation, consider one load as the worst case out of the four. Perform a half-cycle hold time, for example, if the full cycle time is 30 minutes, a 15-minute hold time will be half the cycle. Also, adopt the heat penetration study with biological indicators on the worst-case load to prove the 12-log reduction or Sterility Assurance Level (SAL) in full-cycle hold time.
Related: MACO and NOEL Calculation for Cleaning Validation
Things to avoid while autoclave validation
- Avoid touching of Thermocouple with the wall of the autoclave because on walls have a higher temperature as compared to the chamber.
- The Thermocouple must be kept in the right position.
- The Thermocouple should follow BS4937 standard part 4 (Nickel-chromium /Nickel-Aluminium) or part 5 (Copper-constantan).
- The width of the Thermocouple wire should not be more than 0.7 mm.
- The temperature between the Thermocouple must be controlled. It should not exceed 3⁰C. For instance, it should be maintained between 121⁰C to 124⁰C. The pressure must stay within 15 to 18 lbs for a 15-minute cycle.
FAQs
Ans: The 4 parameters of the autoclave process are pressure, steam, temperature, and time.
Ans: “F0 ” is defined as the number of equivalent minutes of steam sterilization at 250°F (121°C) delivered to a load
Ans: Minimum 12 and if the load items are more or, the autoclave chamber size is more than 1000L, then we should place > than 12 probes.
Ans: Because at 121°C the lethality rate & saturated steam point is optimum.
Ans: A cold spot is defined as any point where the temperature indicator is situated that does not achieve the minimum sterilization temperature of 121°C throughout the sterilization temperature hold time.
Ans: The time between the first sensor reaching the specified temperature and the end sensor reaching the set temperature is referred to as the lag time.

Naresh Bhakar is the Founder and Author at Pharmaguddu.com, bringing his extensive expertise in the field of pharmaceuticals to readers worldwide. He has experience in Pharma manufacturing and has worked with top Pharmaceuticals. He has rich knowledge and provides valuable insights and data through his articles and content on Pharmaguddu.com. For further inquiries or collaborations, please don’t hesitate to reach out via email at [email protected].