The BQS (Blister Quickly Through Servo) Machine is a part of pharmaceutical packaging, where it helps to aggregate unit doses into a blister form, also known as primary packaging. BQS uses continuous motion technology, enabled by flat sealing and flat forming, to achieve precision, power, speed, and position control.
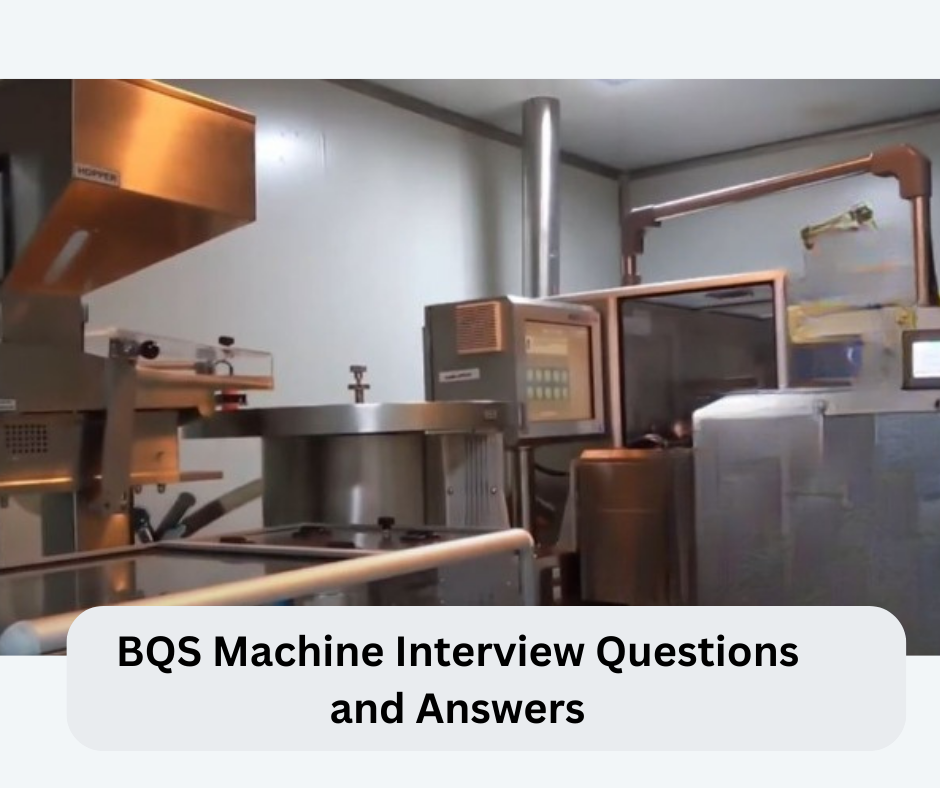
BQS machine Change Parts
- Hopper
- Bowl
- Feeding channel
- Guide track
- Heating plate
- Forming plate
- Sealing plate
- Perforation tools
- Embossing tools
- Indexing roller
- Printing units
- Gears units
- Punching and cutting units
Principle of BQS machine:
The principle of the BQS machine works on “Flat forming Flat sealing” with a continuous motion for high speed.
Types of servo motors in BQS
- Feeding servo
- Printing servo
- Punching servo
- Pulling servo
- Main cam servo
What is meant by servo?
A servo is an electromagnetic device that helps to cover electricity into a precisely controlled motion by the use of a negative feedback mechanism.
Importance of servo motor in Blister Quickly Through Servo machine
- It helps to increase productivity or output.
- It reduces the change over time and is easy to dismantle.
BQS Parameters and specifications:
Forming depth/ die depth– Depth up to 12mm in the case of PVC/PVDC thermoforming and up to 9mm in the case of cold forming.
Forming cycle: Forming cycle up to 40 cycles per minute for thermoforming and 35 cycles per minute for cold forming.
Punching cycle: Maximum 180 cycles per minute
No. of tracks: it may be single, double, triple, or four-track.
Plate Dimension: 265 x 368 mm
Forming Area: Maximum 240mm in width x 180 mm in advance. it may differ from make to make.
Servo Size: Standard size is 40 mm (length) x 38mm (height) x 20mm (width).
Pressure and chilled water used in the Machine:
- Cavity-forming station- 6 Bar
- Heating station, cooling station, and cooling plate- 4 Bar
- The capacity of the Cylinder – up to 10 Bar
- Pvc foil break cylinder – 2 to 3 Bar
- Punching station air blowing for cleaning – 3 Bar
- Alu- Alu flap cylinder – 3 Bar
- Blister Pickup wall – 1 to 1.5 Bar
- Chiller water used for cooling in BQS for thermoforming is 8 -10°C in the case of PVDC and 18 – 20°C in the case of Pvc.
Related Post: Pharma packing questions for the interview
BQS Parts and Their Roles:
Guide roller: It helps in moving the web upwards, additionally, the knob is provided to adjust it.
Spring assembly: These are pressure-based springs to provide pressure to get embossing quality.
Indexing roller: It consists of a web jam-checking sensor. indexing roller helps in pushes the web forwards in parallel motion.
Punching station: Punch the blister to get the edge to edge cutting.
Pick-up station: It lies just after Blister punching units where the Blister is picked up by the pickup assembly.
Pickup angle roles in the Blister machine: They drop the Rejected blisters at 45°, Good blister at 90°, and overflow blister at 180°.
Cylinder for forming: It is a pneumatically operated cylinder to develop forming force on foil. the minimum air pressure required is 6 Bar.
Overprinting unit: It is a servo drive unit to ensure precise control of printing quality.
Vacuum Required in blister packing Machine:
Blister Pick up -26 in mm Hg
Lidding foil splicing sensor -26 in mm Hg
Forming foil splicing sensor -26 in mm Hg

Naresh Bhakar is the Founder and Author at Pharmaguddu.com, bringing his extensive expertise in the field of pharmaceuticals to readers worldwide. He has experience in Pharma manufacturing and has worked with top Pharmaceuticals. He has rich knowledge and provides valuable insights and data through his articles and content on Pharmaguddu.com. For further inquiries or collaborations, please don’t hesitate to reach out via email at [email protected].
What is OEE in blister packing machine
OEE (overall equipment effectiveness) is only used to measurement of how efficiently a manufacturing operation is used.