Double Cone Blender equipment is used in pharmaceuticals to mix Excipients, chemicals, and cosmetics to get a homogeneous mixture of dry powders and granules. The principle of the double cone blender is based on the mechanical mixing that occurs due to tumbling motion. The double-cone blender is constructed by welding two cone-shaped sections at their bases to a central cylindrical section. In this article, we will discuss in detail the principle, working, advantages, disadvantages, and applications of the double cone blender.
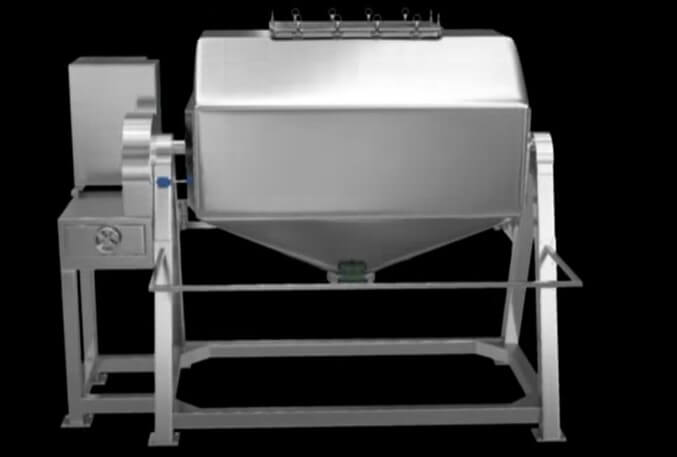
Principle of Double Cone Blender:
The principle of the double cone blender is based on mechanical mixing, which occurs due to tumbling motion.
Working Double Cone Blender:
The rotation axis of the double-cone blender is positioned perpendicular to the cone axis and runs through the central cylindrical section. This design allows for efficient and consistent mixing of the materials inside the blender.
To operate the blender, a driving motor is installed on one of the two lateral supports that hold the blender body. The motor provides the necessary rotational force to spin the blender and mix the contents inside.
The powder is filled up to 2 or 3rd of the volume of the blender to ensure proper mixing. The rate of rotation should be 30 to 100 RPM, and on rotation, mixing occurs due to the tumbling motion. Finally, mixed Material is discharged from the bottom of the equipment. the mixing tank can be slanted freely at an angle of 0° to 360° for material discharging and cleaning purposes.
Note: The rotation speed should be optimum, depending on the size and shape of the blenders and the nature of the materials to be mixed. The rotation speed of the blender is generally kept between 30 to 100 Revolutions per minute.
Construction of Double Cone Blender:
The double-cone blender is constructed by welding two cone-shaped sections at their bases to a central cylindrical section. The axis of the rotation is perpendicular to the cone axis and passes through the cylindrical section. The driving motor is located at one of the two lateral supports holding the blender body. All parts of the double cone blender, including the mixing tank and blends, are made of stainless steel 316L. The rate of rotation should be optimum, depending on the size and shape of the blenders and the nature of the materials to be mixed.
Related: Types of Blenders Used in Pharmaceuticals
Advantages:
Some of the advantages of the double cone blender are as follows:
- It is Easy to maintain and clean.
- No chance of clogging materials into corners.
- Large amounts of granules can be handled easily.
- No too much Tear and wear are required.
Disadvantages:
Along with advantages, the double-cone blender also has some limitations, which include:
- It is not suitable for fine particles.
- Not suitable for the particle with greater particle size because of less shear.
Pharmaceutical Applications:
- In the pharmaceutical industry, it is used for the homogeneous mixing of dry powder and granules for tablets and capsules.
- It is also used in the preparation of spices, flavors, cake mixes, and other solid ingredients.
- In the chemical industry, it is used for blending chemicals, creating dry powdered detergents, manufacturing glass or ceramic products, and producing fertilizer.
Conclusion:
In conclusion, the double cone blender is an important piece of equipment for industries that require high mixing and shearing.

Naresh Bhakar is the Founder and Author at Pharmaguddu.com, bringing his extensive expertise in the field of pharmaceuticals to readers worldwide. He has experience in Pharma manufacturing and has worked with top Pharmaceuticals. He has rich knowledge and provides valuable insights and data through his articles and content on Pharmaguddu.com. For further inquiries or collaborations, please don’t hesitate to reach out via email at [email protected].