Blenders play a significant role in mixing ingredients in pharmaceuticals. Choosing the right types of blenders is crucial, so we select specific blenders among the different types available for use in pharmaceutical manufacturing according to our requirements.
Blenders are used in pharmaceuticals after the granules manufacturing in the production section. Granules are mixed with different ingredients that are to be mixed in a blender for further processing to get smooth properties of granules.
All types of blenders have the same role but different purposes. So the selection of blenders is also essential at that time.
Types of blenders used in manufacturing:
- Octagonal blenders
- V-type blender
- Double cone blender
- Vertical blender
- Mass blender
1. Octagonal blender:
As the name suggested, these are octagonal in shape. Its lower and upper parts are polygonal, which helps pass out materials. Baffles in blender provided to mix material quickly. They are beneficial in the mixing of power effectively.
Precaution: Fill it only up to 70% of its capacity.
Advantages: It’s easy to clean and wash, and easy to operate and handle. No wastage of powders or granules because of the attached clamp and clamp guard on their mouth. Low in noise level.
2. V-type blender:
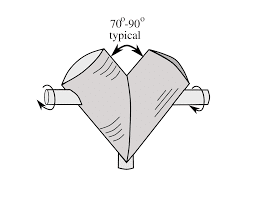
The ‘V’ shape blender help to mix the powder in good manners. It is best to use in pharmaceuticals to achieve uniform mixing of granules. Advantages include, It is easy to use and requires less space to install and operate. Easy to clean and rotated manually.
Read More: Our detailed Article on V Cone Blender
3. Double cone blender:
Its mixes and distribute the powder effectively with the help of inner blades. Fill granules up to two or 3rd portions of it to ensure the adequate mixing of ingredients. A double cone blender consists of a feeding and discharges port with a butterfly valve for smooth operation—an automatic timer is given on the panel for smooth working.
Read More: Our detailed Article on Double cone blender
4. Vertical blender:
Verticle blenders feature a slow-turning screw orbiting a vacuum-rated conical vessel. Because it turns the screw gently, lifts material upward and towards the middle of the batch. Similarly, a product from the highest cascades back to very cheap, whereas mixing with materials is affected upward by the orbiting screw. Vacuum drying is also an excellent technique for processing heat-sensitive formulations without worrying about thermal degradation. In addition, it also helps lower energy consumption.
5. Mass Blender:
Mass blender used for dry, wet, and lumpy mass. It designs with horizontal blades for easy cover of all granules to ensure adequate mixing.
Conclusion:
Blenders are most effective for mixing the granules with the other ingredients in pharmaceuticals among the different blenders. Double-cone blenders are used primarily on drugs. It is crucial to choose the blenders to get high-quality products as per good manufacturing practices.

Naresh Bhakar is the Founder and Author at Pharmaguddu.com, bringing his extensive expertise in the field of pharmaceuticals to readers worldwide. He has experience in Pharma manufacturing and has worked with top Pharmaceuticals. He has rich knowledge and provides valuable insights and data through his articles and content on Pharmaguddu.com. For further inquiries or collaborations, please don’t hesitate to reach out via email at [email protected].