Learn about the Standard Operating Procedures for the induction cap sealer machine, including their scope, responsibilities, precautions, procedures, and operation.
1.0 Scope: This SOP is applicable to setting and operating an induction cap sealer machine in the tablet department.
2.0 Responsibility: 2.1 Officer production is responsible for the implementation of this SOP
2.2 Head production is responsible for ensuring the overall compliance of this SOP.
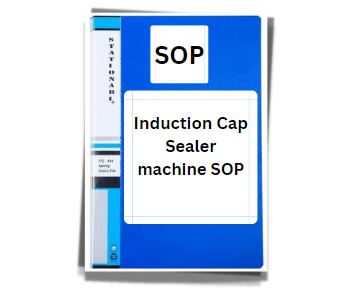
3.0 Precautions: 3.1 Ensure the cleaning of the area and equipment with their daily filled status label.
3.2 Ensure that no primary packing material, batch documents, or tablets of previous products and batches are lying in the cubicle.
3.3 Before starting the operation, obtain the necessary line clearance from IPQA.
3.4 Check their temperature, relative humidity, and pressure differential as per the requirement and record the relevant detail in the Environmental control monitoring format and batch packing record.
3.5 Ensure that there is only one recipe at a time saved in the machine.
3.6 Ensure that the conveyor should be stopped whenever air pressure goes below the limit of 3 kg/cm².
4.0 Procedure:
The setting of the induction cap sealer machine:
4.1 Adjust the sealing head, foil sensor, and jamming sensor (before and after the sealing head) of the induction cap sealer machine.
4.2 The sealing head, foil sensor, and jamming sensor (before and after the sealing head) of the Machines should be kept aligned with the center of the conveyor according to the arrow designed on the sealing head.
4.3 Set the guide track of the conveyor as per the size of the container to be used and according to the arrow design on the sealing head.
4.4 Adjust the height of the sealing head, foil sensor, and jamming sensor (before and after the sealing head) of the machine with respect to the container used for sealing.
4.5 Adjust the distance between the sealing head and cup of the bottle (preferably 5 mm) using the knob provided on the top by rotating it clockwise and anticlockwise.
4.6 Adjust the distance between the foil sensor and the cap of the container in such a way that it can sense the presence of foil properly.
4.7 Connect the air supply provided for rejection on the machine. Set the pressure as per requirement.
4.8 Connect the power supply of the induction head and conveyor.
4.9 Switch on the main of the induction head.
4.10 Switch the control on and set the speed of the conveyor belt with knob provided at the panel by rotating clockwise and anticlockwise.
4.11 Adjust the position of the jamming Sensor (before and after the sealing head in such a way that it can sense the presence of the container properly.
4.12 Press <menu> button and <basic system set up> will appear.
4.13 Press <sub menu> button and <recall Recipe> will appear.
4.14 Press <sub menu> button <Save Recipe > will appear
4.15 Press <sub menu> button and <Reset Counter> will appear.
4.16 Reset the container by pressing <INC> or <DEC> keys.
4 17 Press <sub menu> button and <power percentage> will appear. set <power percentage> using <INC> and <DEC> keys as per batch packing record.
4.18 Press <Sub menu> button and <mode> will appear.
4.19 To set the machine for a new product, select manual mode, and to run the machine select auto mode.
4.20 Press 3 times <Menu> button home screen will appear.
4.21 Pass the container through the induction head and check the sealing of the container, if found ok then process to the next step, if not then do fine setting by adjusting the speed of the conveyor to adjust the height of the induction head or by changing the power percentage following the step 4.12 to 4.19.
4.22 Press <menu> button two times and <timer fault setup> will appear.
4.23 Press <sub menu> and <jam timer> will appear. set the timer using <INC> and <DEC> keys (preferably 1 to 20 sec.) this time allows the jamming Sensor (before and after the Sealing Head) to measure the presence of the container for a set time. If the container remains in front of the Sensor after the jam times expire during operation, then the machine will stop automatically, and the fault will appear (press reset to reset the machine).
4.24 Press <sub menu> and <axcess fault> will appear. set the value using <INC> and <DEC> keys. if the rejection value during operation exceeds the set value, then the machine will stop automatically, and the fault will appear (press <reset> to reset the machine).
4.25 Press <sub menu> and <constructive faults> will appear. set the value using <INC> and <DEC> keys (preferably 1 to 20 sec). if the consecutive rejection value during operation exceeds the set value, then the machine will stop automatically, and the fault will appear (press <reset> to reset the machine).
4.26 Press <menu> and <power save set> will appear.
4.27 Place the container at the beginning of the conveyor and set the time jumping Sensor (after the induction head and before the induction head) using <INC> and <DEC> Keys. This time allows the machine to stop automatically if no container will pass and jumping sensation in between the set time.
4.28 Press three times <menu> button home screen will appear.
4.29 Press <menu> three time and <fault reset setup> will appear.
4.30 Press <sub menu> and <rejection time for s no foil cap> will appear.
4.31 Place the container at the beginning of the conveyor and set the time of the bottle to reach the center of the rejection system time using the <INC> and <DEC> keys. Ensure that the bottle is rejected properly by the rejection system.
4.32 Press <sub menu> key and <how long piston should extend> will appear.
4.33 Place the uncapped container at the beginning of the conveyor and set the time using <INC> and <DEC> keys in such a way that the rejection system rejects the bottle properly.
Operation of induction cap sealer machine:
4.34 Switch off the control of conveyor and press start button on induction machine.
4.35 After pressing the START button, the heating of the sealing head is automatically ON, and the power percentage will be displayed on the LCD screen.
4.36 Start the machine and perform the challenge test as per as batch packing record.
4.37 Carry out leak test to check the integrity of container sealing as per SOP of ” leak test”.
4.38 Carry out an in-process quality check as per the frequency mentioned in the batch packing record.
4.39 Record the operation activity in the equipment logbook as per SOP “uses and maintaining of logbooks for equipment.”
4.40 After completion of the operation activity, press the stop button of the induction machine.
4.41 Switch off the mains of the induction head and disconnect the power supply of the induction machine and conveyor belt.
4.42 Affix the “To be cleaned” label on the machine.
ABBREVIATIONS:
SOP- Standard Operating Procedure
No -Number
TB- Tablet
QA- Quality assurance

Naresh Bhakar is the Founder and Author at Pharmaguddu.com, bringing his extensive expertise in the field of pharmaceuticals to readers worldwide. He has experience in Pharma manufacturing and has worked with top Pharmaceuticals. He has rich knowledge and provides valuable insights and data through his articles and content on Pharmaguddu.com. For further inquiries or collaborations, please don’t hesitate to reach out via email at [email protected].